Introduction: Super Strong 3D Component Carbon Fiber Parts
Welcome to my instructable, this time I was inspired by carbon fiber reinforced parts from RichMAc with the difference that I wanted to make my parts as light as possible. Conventional methods use plates of carbon done by vacuum forming or such, but plates are blocking air coming through but in many cases walls are not really needed. Then comes the idea to secure only 3D printed parts needed to avoid with other parts in space and connect it together by carbon fiber. The part is done by single long real carbon fiber tow, which made it super strong and its connected only in places where is needed. Next layers of carbon fiber pull all air bubbles out so there is no need for vacuum machine or such. Additional carbon fiber profiles are used to do bridges and mounting points in parts, detailed description can be found in this tutorial. I call this as "3D component carbon fiber" because part is done only from few 3D printed components connected by long carbon fiber. Other name that comes to my mind was "carbon skeleton", but it is not representing 3D printed parts which are critical to do this kind of project.
BOM
- filament: ColorFabb - XT-CF20 because its carbon to carbon :)
- carbon fiber: AMOCO (CYTEC) THORNEL T-300 3K continuous filament carbon fiber tow from ebay. 3K is maximum for me for such small parts, more K means more thick tow is. Tow means wire made from 3000 fibers in this case. Use smaller K and make more layers to have your part stronger.
- glue: Just some medium or soft super glue.
- epoxy: I used EPOXY L285 200+80g hardener 5MA40052, this is something i was able to buy locally.
- carbon profiles: 1,2mm carbon rod and 1x3mm carbon profile
Step 1: Make 3D Component Carbon Fiber Part
3D files needed for this project can be downloaded from my thingiverse site.
Please follow pictures to go step by step:
- Build your fixing platform, fixing platform should hold parts really strong. Measure vertical distances of both pieces to have them on same height.
- Glue in carbon rods, leave it longer than needed. It is good to have long mounting points during winding of carbon fiber. Excess can be easily sanded at the end.
- Glue in 1x3mm carbon profiles, fix it in fixing platform and leave super glue to cure. Its necessary to to wait for super glue to harden, because it can react with epoxy resin causing smoke and destroying bonds.
- Wire end of carbon fiber tow to fixing structure. This will be strong start point to start wire fiber around the part.
- Mix epoxy resin according to manual, mine was 2:1. This step is important because epoxy can harden for many days if you put less hardener part to the mix.
- Put a bit of epoxy to the part before start. Tightly wind carbon fiber around part in the structures you think are the best to distribute forces in the part. I made X structures from the sides and top of the part in continuous circles. Put epoxy to all newly winded parts every 2-4 circles. It takes few turns and you will find your style easily. Stop when you think is enough, cut the tow and tighten it again to fixing structure to prevent unwinding. Re-epoxy all structure again.
- Let epoxy to cure, it will take 24hours if mixed well.
- Sand and grind excess stuff. Carbon produce a lot of miniature dust, its good to use mask or do it under the water.
- Dry the part and you are ready to go.
I used around 7m of 3K carbon tow for this part. Its hard to estimate exact length, I just stopped when space between supporting rods was full and my hand starts to hurt because of fiber cutting my skin. So I recommend to use gloves, also epoxy resin is hard to clean from the hands when its finished.
In the next step I will show you my tests around this part, how well it stands between others.
Step 2: Test It
Usually if you do carbon you are looking for something light and rigid, so I went for straight forward testing. I put five test pieces in test, these are more less copy of same thingiverse reinforced arm part for hoversip MHQ quadcopter :
- ABS 30% infill
- ABS 30% infill with 2x 1,2 mm rod
- ABS 100% infill
- ColorFabb - XT-CF20 100% infill
- My 3D component carbon prototype
First observation I made is that not all ABS plastics are the same, it really depends from manufacturer how flexible ABS is. Usually many manufacturers go for more soft ABS mixture because its easier to 3D print. ABS 30% infill with 2x 1,2 mm rod is my first attempt how to carbon reinforce 3D printed parts, model can be found also on thingiverse,
Pictures show the test results, 1kg weight was used because this number that can be attacked by quad copter motors with 5inch propeller (3blade bullnose).
Weight test:
- ABS 30% infill = 7gram
- My 3D component carbon prototype = 8gram
- ABS 30% infill with 2x 1,2 mm rod = 8gram
- ABS 100% infill = 10gram
- ColorFabb - XT-CF20 100% infill = 12gram
Bend test:
- My 3D component carbon prototype = really strong
- ColorFabb - XT-CF20 100% infill = really strong
- ABS 100% infill = in the middle OK for use
- ABS 30% infill with 2x 1,2 mm rod = soft but flies quite OK
- ABS 30% infill = total soft
Just subjectively rated twist test done by hand
- ColorFabb - XT-CF20 100% infill = really hard to twist
- My 3D component carbon prototype = hard to twist
- ABS 100% infill = hard to twist
- ABS 30% infill with 2x 1,2 mm rod = soft but flies quite OK
- ABS 30% infill = total soft
These tests are showing great weight/strong ratio as carbon fiber stuff should have.
In the next step I will show you how to prepare your own part to do it in 3D component carbon fiber style.
Step 3: Design Your Own 3D Component Carbon Fiber Part
In this step we will try to remake OpenRC rear wishbone into 3D component carbon fiber style. Pictures added to this step are exactly step by step guide. First we have to identify mounting points on our part, in this case its one side that will be attached to car body, two tips to hold C-hub and three holes to put shocks in. I put whole part as one group in google sketch up and used transparent texture. Then I recreate this mounting points by newly created objects, these objects are textured as red. Then we have to expand it by mounting points and grooves for carbon fiber tow. Holes are 1,4mm big for 1,2mm carbon rod to be glued in and 3x1mm for 3x1mm carbon profiles. Then we have to make fixing structure. The white textured part was made to help fix all components, its basically platform, like projection to x axis of all components connected together.
In this stage you can use your 3D printer to print these parts, I made fixing structure 2x to be able to fix it from both sides.
Bolts were used to fix all components to their place. Please note that all components have to be strongly fixed between each other, applying carbon tow will pull them together. I made mistake as can be seen on the last picture. I had to put something between during the process to prevent C-hub holders to pull together. It will be much better to have screw there as red line is showing with nuts from the beginning.
From this point the procedure is identical as on second page of this tutorial we did for quad copter arms.
3D model made in this step can be downloaded from my thingiverse page.
Step 4: Use Your Part
As you can see the winding strategy was completely chaotic this time. Next time I will prepare some winding paths before start because it gets me in several troubles. Trust me its quite hard to solve troubles with one hand from epoxy and second holding carbon fiber tow tighten. The part itself is quite rigid, much stronger than original one. Problems came because two holders for C-hub were not secured between each other by fixing structure, so carbon winding move them close to each other, I put spring between in hurry but final part needs quite a lot of sanding at the end to fit C-hub in. Then I made some bridges in the wrong places colliding with C-hub and shock, also clearance under shock was filled by carbon so shock collides with it. So next time measure twice and do carbon once. From weight perspective carbon was a bit more heavy than my abs wishbones but I must say ABS one are quite crappy (sorry for forgotten bolt).
I hope that my tutorial helps you mainly to see 3D printing in the new ways and possibilities to create new stuff. Thanks.
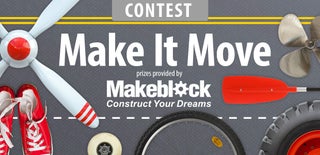
Participated in the
Make it Move Contest 2016
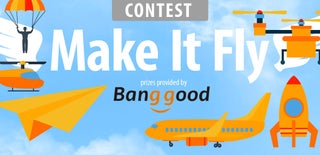
Participated in the
Make It Fly Contest 2016
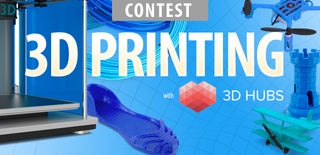
Participated in the
3D Printing Contest 2016