Introduction: TankTop Hybrid Arcade Machine!
As a tribute to my high school electronics and engineering classes, I decided to leave them a gift that would attract new students and be entertaining. What better to do so than an AWESOME Arcade Machine!
Design Choice:
For this arcade machine I wanted the feel of a full sized cabinet, but with the portability of a bartop cabinet. There were no real options or previously done hybrid cabinets that I could find, so I decided to draft my own design and build a cabinet from scratch!
If you noticed, the arcade was built from plywood and not MDF. Personally, I would have chosen MDF as it is much, much easier to work with, but my electronics teacher insisted to have the archaic feel of a table top cabinet (stained wood). As a compromise, we decided to have the sides digitalized and the middle portion stained.
Step 1: AutoCad Files and Drafts
These are the files I have in regards to the dimensions. Unfortunately I do not have the original CAD files, but in the pictures displayed there is the side profile design for:
Sharp corners
Rounded edges
The choice of width is up to you and the TV/LCD you choose. If you are using 3/4 MDF, use this formula to calculate the total exterior width:
1.5" MDF (if measuring from outside edge) + 2" Wiggle Room + TV/LCD Width = Total Width
Step 2: Bill of Materials
Depending on how you customize the arcade machine, your list may differ slightly from mine. That is absolutely fine, personally I encourage adding twists to preset designs!
Wood:
(2) 3/4" High Grade Plywood 4' x 8' - 80-100$
or
(2) 3/4" MDF Board 4' x 8' - 70$
(3) 2' x 2' 96' lumber - 12$
(1) Wood Filler (non latex) - 10$
Screws:
(1) 1 5/8 Wood/Drywall Screws 100 pack- 10$
or
(1) 1 5/8 Finishing Screws (better option) - 15$
(1) Small Black Screws 1/2 to 1 inch - 4-10$
Acrylic & Black Plastic Sheets:
(1) Clear Acrylic Sheet - 13$
(2) Black Tinted Acrylic Sheet - 12$
Hinges:
(1) 8 Pack Locking Hinges - 9$
(1) Standard 1" Hinge - 5$
T-molding:
Side Art:
(2) 33" x 39" Poster Board - 80$
Velcro:
(2) Black Velcro 3/4" x 3 1/2" - 7$
Glue and Adhesives:
(1) Super Glue - 5$
(2) 90 Second Epoxy - 5$
(1) Clear Wood Glue - 10$
(1) Rubber Cement - 5$
(1) Contact Cement - 10$
(1) Masking Tape - 6$
(1) Electrical Tape - 3$
Electronics:
(1) LED String Lights Blue - 8$
(1) 3.5mm to RCA Adapter - 4$
(1) S-Video to RCA Adapter - 5$
(1) X-Arcade Tank Stick - 199$
(1) Old Laptop - Priceless
(1) CRT 32 inch TV - 10$
Mesh
(1) Speaker Mesh - 13$
Tools:
Dremel
Table Saw
Miter Saw
Orbital Sander
Jigsaw
Router
Drill
Drill Bits
Assortment of Screw Drivers and Allen Wrenches
35 inch InkJet Printer
Death Star...
Step 3: Frame Cuts
To cut the frame out of the 4 by 8 plywood sheets I used 2 methods:
Square Cuts:
Use a table saw for the square pieces (side, top, bottom, etc.). Be sure to keep the pieces aligned with the guard as you pass the plywood through the saw, and keep the exterior face (the face you want on the outside of the arcade) UP as most table saws cut in a clockwise direction.
Arcade Side Cuts:
For the sides of the Tank Top Arcade, I used the schools "D sized plotter" Hp T1100 (44 in max width, it's really just a HUGE inkjet printer) to print out the outline of the sides. I then taped the outline onto the plywood using green masking tape. To keep the plywood upright on my luxurious table, I used an old computer to hold the wood in place.
Jigsawing wood is always fun! but there are several pointers i learned while cutting the sides that I wished I knew beforehand.
The jigsaw tends to rip the veneer off the top of the wood if you cut against the grain (perpendicular to the general wood direction). To offset this, use a fine tooth bit (15-20+ teeth per inch) to cut, and keep the face you want on the exterior of the arcade facing down. Also, setting the cut speed to the highest setting helps counter veneer splitting.
For alignment I used a square metal ruler taped to the board. Although I didn't really think that method would work, it turned out just fine.
Step 4: Frame Mockup
To get a feel for how the arcade will look, I decided to mock up the frame using my "ultra strong" green masking tape.
Mock ups are important for planning and structural analysis (knowing where to place studs to screw to). Remember, green masking tape is not a permanent bonding agent. I remembered that I taped up the arcade then decided to leave it in its mocked up position overnight. The next day when I came back to check up on my mock up I was greeted with the arcade pieces all over the floor. Just something to remember :)
Step 5: Frame Assembly
Frame Shell:
For the interior, I lined the cabinet with 2" by 2" wooden studs. Starting with the base, I attached the cabinet sides to the 2 by 2's using 1 5/8" wood screws.
On the exterior of the sides (not shown) I marked every 5 inches to place a screw (roughly 6 on the bottom edge, 5 on the back edge).
To keep the screws from obtruding through the plywood on the exterior, I used a countersink bit to create a depression in the wood before putting in the screw.
If i were to redo the project, I would use finishing screws instead of wood screws as they are much easier to cover than the huge countersunk holes.
TV Support:
The support is the angled piece of plywood that stretches across the cabinet. For this piece you want to have the top face of the plywood flush with the outer edge of the side pieces (where the TV is viewed from). The plywood is lifted 5 inches from the base of the arcade machine, and the two supports were cut at 45* and simply pushed in until the TV was at the correct angle.
Back and Top Assembly:
The back edge of the arcade machine is a tad bit tricky since it has to be cut at 2 angles (The drafts I provide removes this complication).
Here's a little carpenters trick I learned on different woods project: If you have some funky angle like 26.7, Just cut at a larger angle (30*). Or if you have many different weird angles that have to be butted together, just cut all of them at 45*. The reason is that the gap from the larger angle wont be visible (on the inside), so as long as the length of the piece is the same it will work just fine.
Step 6: Frame Assembly (Part 2)
Top Box:
The top box ( the place where the blue LED's are stored) was constructed separately then attached to the arcade cabinet.The base of the top box is 24.5" x 12", with an 18" x 10" square cutout of the center of the base. The 2" x 2" bottom studs were attached to the base, then the back piece of the box was attached to the 2" x 2" bottom stud. Finally the bottom studs were screwed into the actual frame from the exterior ( counter sink screws) and permanently attached to the frame.
The back piece had a 1.5" hole later on drilled into it to allow the LED power cable to attach to the rear power strip. If I were to redo the back piece, I would either have it completely removed, or only make it half the size it currently is (trim the top off) to allow wires to be easily strung into the top box.
TV Placement:
Once the actual frame is assembled, the CRT can be placed for another mockup! Since the arcade machine is 26 inches wide, the TV base has to be 26 inches across too. Most 32-34 inch diagonal TV will fit, so long as it is 26 inches wide it is a go.
Just a side funny story, do you see that broken TV in the background? That was the original CRT that was to be put into the arcade, and it was slick too! It featured a full flat face, only weighed 2 tons...
Anyway I was transporting the arcade machine across the parking lot (don't ask) and one of the wheels on the rack the arcade sat on snagged on a crack in the pavement. According to newton's laws, all of them, the arcade machine went airborne and fell 5 feet to the pavement. luckily my bare toes, I was wearing sandles, were there to catch the fall of the 200 lb cabinet. Nothing happened to the arcade machine, but the TV got DESTROYED (he's dead Jim.). What was even more destroyed were my toes, or what was left of them. Never wore sandles since.
Plexiglass Shims:
Placing flat pieces of wood were the perfect option to mount the plexiglass and the bezel to. Since the plexiglass and the bezel were both 1/8", the shims had to be mounted 1/4" from the edge of the arcade machine. Using a ruler and a pencil I made two1/4" marks and then traced a line between the two marks. then I used 5/8" screws to mount the shims to the inner side of the arcade machine.
Step 7: Wood Filling and Sanding
Before I begin this section, let me warn you before hand: DO NOT USE CHEAP LATEX FILLER!
The reason being that latex is usually unstainable, leaving mismatched wood stain on the final product. I made that mistake on the back of the arcade machine, and now I have 3 lovely white marks where I filled in the wood.
Wood Filling:
Using a spatula or a putty knife, scoop some of the filler onto the tip of the putty knife. Apply a liberal amount to the hole intended to cover, then slide the knife over the surface of the wood. you may have to repeat this step several times to achieve a smooth surface, and even if the surface isn't smooth, don't worry about it since you're going to sand down the surface anyway.
For complex surfaces (such as corners or edges) that need to be filled, use masking tape to make a barrier so that the filler doesn't drip.
Wood Sanding:
Before you can stain the arcade machine, it is imperative that you sand the cabinet down first! To do so, I used an orbital sander. Sand down the surface of the wood using 120-150 grit sand paper first, then go over the first sanded layer with another 220 grit pass. When sanding use long, slow sweeps (don't "scrub" the plywood) and NEVER sand against the grain of the plywood. If you do sand perpendicular to the grain you will see the sanding marks when you stain the plywood.
Step 8: Staining, Poly, and Waxing the Arcade Machine
Staining:
After the cabinet has been sanded down, it's now time for the staining process!
For this step you need any sort of rag preferably cotton or some sort of material that doesn't flake (don't use bounty paper or toilet paper), and the staining color of your choice. Paint brushes work phenomenally well too.
Staining is fairly straight forward: make sure to shake the can, then open the can and dip the rag (I used an old cotton t shirt) into the stain. Apply the stain onto the plywood in a sweeping motion, making sure to stay with the grain. The longer the stain is on the wood, the darker and more saturated the wood is(usually I wait 8-10 minutes) then wipe the stain off using a clean t shirt.
Stain 2 coats, then wait overnight for the stain to dry for the next step.
Polyurethane:
After waiting overnight (or 4 hours depending on the specs of the stain) it's now time to polyurethane the arcade machine. Polyurethane protects the wood from water damage and adds a low shine to the exterior. To apply the polyurethane, pour some of it onto a rag and wipe over the stained wood (same procedure as staining). Wait a couple of hours, then SAND the exterior with steel wool and apply another coat of polyurethane.
After applying your 3rd coat this step is finished!
Wax:
Also known as minwax, wax leaves your cabinet looking SUPER shiny! This step is not necessary, but I highly recommend waxing the exterior of stained wood.
Wax has the texture of butter, to apply it simply scoop some of it out of the can (using a strip of t shirt or cotton) and rub it onto the cabinet in a circular fashion (like you're washing a car). Between every coat, use the steel wool to lightly sand down the surface. Apply 3 coats (don't sand down on the third coat) and you're cabinet should be like a mirror!
Step 9: Attaching the Front Lip, Rear Cover, and Plexiglass Mounts
Front Lip:
The front lip of the arcade machine (6" x 26) is what allows easy access to the laptop and internal of the arcade machine. I wanted to have it on a hinge, that way I could simply flip the front lip out instead of lifting the X arcade controller.
To place the hinges, I had to cut a 1" by 5" chunk out of the cabinet using my teeth. Just kidding, I used a dremel tool which worked out fine.
Rear Cover:
If you noticed in the computer model of the arcade machine, there was no existing hole for the CRT. But after measuring the dimensions of the TV I figured out fast that an extension was needed, plus having the back openable allows an easier management of power cables and wires.
Originally the rear box was made out of 3/4 inch plywood, and it was held on with one large hinge. That box was a bit too heavy, so I switched it out with 1/2 inch plywood, and made the rear cover out of black plastic. The end result turned out pretty nice, plus I installed locking hinges which eliminated the need for a separate locking system.
Step 10: Speaker Box!
Well, turns out I really didn't need speakers in the upper portion of the arcade machine because the TV speakers were loud enough. So I have a bunch of empty space in which I can fill with whatever I wish (nutella, skittiles, etc.). I ended up putting blue flashing LED's which complimented the overall design.
Speaker Mesh Frame:
Having a hollow area at the top of the arcade isn't very professional, so to keep the interior of the upper box hidden I decided to line the top of the cabinet with speaker mesh. I asked the Industrial Tech teacher (also the Wood Shop teacher) what the best method to mount the mesh and he recommended a frame to staple the mesh to.
I planned on using 2 layers of speaker mesh. The upper rectangular slot is 18" x 10", 2 layers of mesh roughly equal 1/8 of an inch, so the frame had to be 17 3/4 x 9 3/4.
The frame was pocket jointed and glued together, then i attached 3 blocks of wood to keep the frame in place (they don't have to be blocks, screws would work, so long as the frame doesn't fall).
A quick cover of black spray paint and the mesh was ready to be stapled on!
Speaker Mesh Installation:
Fold the mesh in half to get two layers of thickness. Starting from one of the corners, staple the edge of the mesh to the edge of the frame. Work your way around the box, folding the mesh over the top and stapling to the inside edge of the frame. To bypass the blocks, make V cuts around the edges of the blocks. On corners, cut along the diagonal, fold over the top of the frame, and staple in place.
By the time you reach all the way around the frame, the middle should be taught. If not, pull a little harder on the mesh and add more staples.
Step 11: Side Art Installation
The idea behind the side art was to have it define in the best way possible the electronics class. Instead of painting the side art, we used a premade poster-board as the design.
Image Selection:
Choosing an image for the TankTop Arcade Machine was a bit daunting, but after two days of google searching, we finally found nice image designs for the cabinet. Be sure that the pictures you choose are not copyright, and that the images are free to use.
Image Re-size:
To scale the image to the 33" x 39" size we needed, I used a Photoshop plugin called "fractals" to keep the sharpness of the image while scaling.
Poster Board Printing:
I really wanted to print the images on the huge printer we have, but it didn't really workout (too much ink needed, not enough space, etc.).
We ended up sending the images to http://www.posterbrain.com/, and chose a custom size (33" x 39") for the poster board. Just a note, we chose to have the lamination done to the poster for protection and shine. After about 2 weeks the posters arrived in a large cardboard tube!
Poster Layout and Cuts:
To get an accurate cutout for the sides of the arcade, simply place the arcade machine on the poster board, then trace the outline of the side with a purple sharpie. Same procedure happenes for the other poster, and after both sides are outlined, the posters can be prepared for cutting.
Using a T square, align the edge of the ruler to the purple line that was previously made. Slowly cut the outline using a box cutter, being careful not to curve the blade. After several cuts, the side art should be ready!
Side Art Pasting
This step is a tad bit tricky and it has two parts. The first part is applying rubber cement, which is a temporary bond, to both the back of the side art and to the arcade side face. Let the rubber cement dry, then stick the side art to the arcade machine. Position the side art till it is completely aligned with the side of the arcade machine, then use contact cement to permanently adhere the side art to the arcade machine. Spray contact cement onto the arcade face then onto a piece of the side art, wait 1 minute, then firmly press the two faces together.
Step 12: T Molding
Installing the T-molding ranks on my top 10 list of most frustrating tasks I've ever attempted (one rank easier than fixing a laptop keyboard). However, given the experience I have now, this task should not be that difficult.
Routing:
Before T-molding can be inserted into the arcade machine, a slot has to be routed out in the center of the plywood. For those of you who are not familiar with T-molding, it is the plastic that lines the edges of tables and cabinetry.
I bought a 25 ft roll of plain black T-molding from:
http://www.t-molding.com/store/product.php?productid=50
If you notice, the T lip is 3/32 of an inch large, so the slot cutting bit that you order should be 1/16 of an inch.
The router bit was ordered from:
http://www.mlcswoodworking.com/orderstatus/html/smarthtml/pages/bt_slot.html
Slot Cutter Complete Assmbly #7641, 1/16" - 1/2" shank (The name of the product.)
I would recommend looking at some video tutorials of routing if you have never routed before:
Two pointers to remember when routing: Do not install the bit backwards (you will know because the wood will smoke and burn), and try not to tilt or twist the router while cutting out the wood. NEVER try to rout the cabinet vertically, have it on its side to minimize twisting and torquing. Also, test to make sure the cut is centered on a scrap piece of wood before routing on your cabinet.
T-Molding Installation:
This step surprisingly was a pain due to my previous mishaps with the routing, but no worries, I managed to nicely finish the trim.
Simply press the molding into the routed slot, starting from the bottom edge of the arcade and working your way up. Around light edges, cut every 1/2" to relieve the pressure off the T-molding. Around sharp edges, cut out a V shape approximately 3/4 inch across from the T-molding lip to compensate the bend.
If you screwed up like I did and had sections where the routing cut was 1/4" across rather than 1/16", then have some 90 second epoxy ready. Squeeze the epoxy into the cavity and press the molding in place. After 2 minutes the T-molding should be held solid with no issues.
Step 13: Marquee
Marquee Printing:
Since the marquee is only 26" x 7", I decided to have that printed out on the school's HUGE HP T1100 Inkjet printer. A couple of pointers that I figured out AFTER I printed out the marquee:
Although photo paper is nice and shiny and looks phenomenal to print on, don't print on photo paper. The reason being that photo paper absorbs light fairly effectively, making it very difficult to shine LED's through it. Also it's very expensive, so don't print "first drafts" on it because it'll probably be wasted.
For marquees, print on any sort of light, thin paper material and avoid thick textured papers.
Marquee Encasing and Attachment:
Another pointer that I learned very quickly is that if water gets onto the inkjet-printed-marquee, you can kiss that marquee bye bye. To protect the marquee from damage and to give it a more aesthetic look, cut out a sheet of acrylic that is the same size of the marquee.
Carefully cut the marquee out of the paper, then use masking tape to attach the edges of the marquee to the acrylic. I used an electric tape overlay to cover the masking tape, and the results were alright but not exactly to my "high" standards.
To simplify the attachment process, I simply bought some Velcro and Velcroed the marquee to the arcade frame. I made the mistake of choosing white Velcro instead of black (d'oh!), but it wasn't too noticeable so it wasn't an issue.
If I were to go back and redo the marquee (and I just might) I wouldn't use a solid acrylic sheet, they make clear liquid epoxy/acrylic which can be poured over the paper, then overnight the marquee would solidify into one solid piece. Masking tape wouldn't be needed and the end result would be much cleaner.
Step 14: Front Plexiglass and Bezel
Plastic Cuts
The acrylic and black plastic were cut from a 28" x 30" sized sheet to a 24 1/2" x 20" sheet size. These dimensions allow for the screen to cover the front of the TV and all edges around the face of the arcade. However, I would strongly recommend cutting the sheet to 22" height instead of 20", because 20" just barely fit (was almost too short) and it will save you an extra step later on down the road.
The black plastic was cut again to be the bezel. I used a table saw for the cuts; cutting the interior only is a bit advanced, I would recommend a dremel tool for those who haven't used a table saw before. Set the guard rail to the measurement from the left that you need (24 1/2-5=xxx), then slowly drop the middle of plastic onto the saw (use pliers to keep your fingers safe). There should be a cut in the center of the plastic now. Slowly slide the plastic forward until your preset mark, then recede back to your other mark (careful not to over cut a line). Repeat for all 4 sides and you should have a nice square center cutout!
Black Plastic TV Cover
If you noticed, there is a 24 1/2" x 20 1/2 piece on the bottom edge of the inner cutout. This piece is there to cover the Toshiba logo of CRT and all of the control buttons (on/off, vol + -, channel + -). I simply lined up the piece to the edge and super glued then hot glued the piece into place.
Assembly
To install the bezel and plexiglass, I lined up where I wanted the plexiglass to be. Then I marked a point 1/2" from the top and 1/2" from both sides for the two upper screws, and 5" from the bottom and 1/2" from both sides for the two lower screws.
Using a drill, I lined up both pieces (plexiglass and bezel) then drilled through each mark. To keep the plastic from moving, I screwed in a screw after every hole drilled. I then realigned the plexiglass and bezel to the cabinet, and used a screwdriver to drive the screws into the wooden shims.
Step 15: Software and Electronics!
Electronics:
The secret is out! now everyone knows what powers the neutron core of the TankTop Arcade Cabinet! Yep, its an old AMD XP laptop. but for our purposes, it works just fine.
The next component is the viewing apparatus, also known as a CRT TV. The display could also be a flat screen LCD monitor (depend on your budget and preferences). From the front of the CRT comes out 3 wires, a WHITE, RED, and YELLOW wire. The WHITE and RED wires are your audio, and they are attached to a RCA to 3.5mm adapter which is plugged into the laptop. The yellow wire is your video and it's attached to a S-Video adapter which is also connected to the laptop.
The arcade panel is the Tank Stick X-Arcade controller ( If you haven't figured it out yet TankTop is derived from TankStick and BarTop. Surprise!).
The beauty of the X-Arcade Tank Stick is that it really needs no additional drivers or software as it shows up as an external keyboard and mouse.
To save space on the limited USB ports, I plugged the keyboard (arcade buttons) through the USB and the mouse (arcade trackball) through the PS/2 port.
Software:
Oh the joys of software......when it functions! Nah, the software wasn't that difficult to implement, and I'll try to cover all aspects of setting up an arcade machine on windows.
Cloning PC screen to TV:
This section really depends on what combination of outlets you have on your laptop and TV.
For older laptops, you can either use VGA or S-Video. S-Video is featured on older laptops and is probably the easiest way to connect to a CRT. A VGA connection requires a special adapter box to be able to connect to RCA (the video out on the TV).
For newer laptops (Windows Vista & 7) you can use VGA or HDMI. Both scenarios require a special box to convert to RCA, but they are relatively cheap (15-40$).
Here's a short overview over the different types of connections that are possible with a TV/Laptop pair.
Once the cables are connected, now its time to tell Windows that you have a second monitor connected. On laptops there usually is a monitor button ( 2 lines with a box in the middle), pressing this button should pull up a window that you can choose to add a monitor. Click on the clone button. Otherwise:
Windows XP: http://support.microsoft.com/kb/307873
Windows Vista & 7: http://h10025.www1.hp.com/ewfrf/wc/document?cc=us&lc=en&dlc=en&docname=c02013758
Windows 8: downgrade to Windows 7 and try again.
Emulators:
Here's where the fun begins, If you have no clue what an emulator is I suggest you familiarize yourself with the terms:
http://www.emulator-zone.com/doc.php/help/commondefs.html#whatisemulator
To play classic arcade games, download MAME (Multiple Arcade Machine Emulator) for windows.
http://www.mamedev.org/release.html
scroll to the pictures and I have a step by step tutorial on what to do (a picture is worth 1000 words).
Games:
You either have to find free licensed games or buy the roms. Here is a site for free LEGAL roms:
The other method is to buy Arcade Rom CD's from an online retailer:
http://www.amazon.com/Atari-Arcade-Hits-Jewel-Case-Pc/dp/B00004VXAN
MAME:
Run the mame0148b.exe file you downloaded earlier, and choose a location for it to extract.
Then, once you have downloaded your roms, place them in the rom folder located in the MAME directory. Double click on the MAME32.exe icon and MAME should open.
Step 16: Bon Appetite!
Your TankTop Hybrid Arcade Machine should now be completed. Rejoice, sit back, and enjoy hours upon hours of fun!
The core of this project was to attract students into the STEM (Science, Technology, Engineering, Mathematics) field of courses. Here in Southeast Missouri not a whole bunch of students are eagerly waiting to sign up for an engineering class, and perhaps by showing them the range of projects available to them in the STEM field they might peak some interest towards the classes.
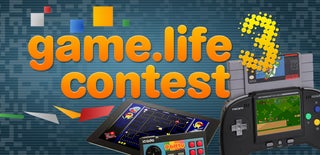
Runner Up in the
Game.Life 3 Contest
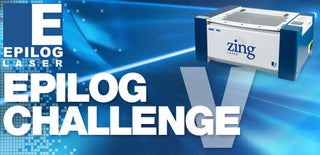
Participated in the
Epilog Challenge V
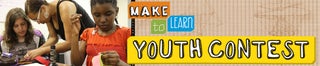
Participated in the
Make-to-Learn Youth Contest