Introduction: Techniques for 3D Printing in Nylon
3D printing in Nylon for makers has come a long way since Taulman first introduced it back in 2012. The material has improved, the methods have improved, and now color is an option. I have been printing quite a bit in Taulman's nylon and I wanted to share a few tips and tricks I have come across for successful 3D printing in nylon. This list is by no means comprehensive and I'm pretty sure other people have figured this stuff out before, so I take no credit for being the first, but I compile my experiences here as a resource for those of you looking to add nylon as a material in your 3D printing repertoire.
For the obligatory safety speech: Although this is a relatively benign procedure all around, you will need to use a hot plate to heat up vinegar or a similar acid, so be smart about it. Vinegar in your eye sucks, hot vinegar with dye in it is an actual problem. So pay attention to your workspace and if you are prone to accidents or things finding their way into your eye, wear goggles.
Step 1: Why Nylon?
Since nylon obviously has a few caveats that require special attention and extra work, you might ask, why use nylon? There are several properties that nylon has which more than make up for the extra consideration that goes into printing with it.
Strength: Nylon is by far the toughest material that hobbyist level printers can currently use. This means it can be used in functional models by an end user. The prosthetic hand pictured here is one I printed as part of the volunteer group e-NABLE. The nylon is extremely robust and will not crack or break the way ABS or PLA might after some wear and tear. It also will hold up against heat much better, as anyone who has ever left a PLA print in a hot car can appreciate.
Flexibility: Nylon offers an incredible degree of flexibility without breaking in thin-walled prints or very low z height prints that allows for flexible constructions like straps or buckles that require bending portions to lock in place.
Photo/chemical resistance: Nylon is UV resistant and much more resistant to chemical attack than PLA or ABS.
Low coefficient of friction: Nylon is slippery and will work well when mated parts need to glide along one another or at a hinged joint.
Artistic Possibilities: While this may be seem like a stretch, I argue that nylon gives you some nice advantages for artistic expression in terms of coloration. You can easily dye nylon with safe and inexpensive fabric dye, which means you only have to buy one roll of filament to have dozens of different colored prints from the same roll. The nylon filament is a kind of blank canvas in a sense. You can also save and reuse the dye. More on this later.
With these things in mind, I will give you the tips and tricks I have found to be most useful while printing in nylon.
Step 2: Materials Overview
Nylon filament:
All the nylon I have printed with so far comes from taulman3d.com. I have printed using the 618, 645, and Bridge.
3D printer:
Although I can only speak to the the use of two types of 3D printers on a personal level (solidoodle 2 and a home-built MendelMax), and most of my nylon printing has been done on the Mendel. I have heard (and seen) many reports that you can use most FDM printers with nylon filament, provided you can get the hotend safely up to 240C.
Drybox:
As it turns out, one of the features of nylon is its tendency to absorb moisture from the air. This presents a problem when printing/storing the filament. I found a simple drybox took care of both of these problems rather well, and was not difficult to make or use.
Color:
I used RIT fabric dye, the liquid variety, for the dyeing you will see in this instructable. All the nylon filaments I've used come in the same "natural" color. A kind of milky white that can be semi-translucent when printed very thin. However, if you want to jazz it up a little with some color, there are a couple of ways to go about it. First, I'd like to point out that a great deal of work in this area has already been laid down by RichRap. Rich's method was mostly about dyeing the nylon filament prior to printing, which can have some really cool outcomes. I've struggled with getting the filament dry enough afterward to print with and have had greater success with post-print dyeing. Also, taulman3d.com has recently added a page on coloring the nylon, both prior to and after the print. They suggest to dye the nylon after the print for best results, which is what I will be covering in this instructable.
Step 3: Printer and Settings
- My printer is a MendelMax running Repetier firmware and controlled with Repetier Host: both are free from repetier.com
- It is also important to turn up your retraction with nylon as it tends to be a little stringy sometimes. Using at least 4mm of retraction or sometimes more, can help a lot. Also, if stringiness is excessive, turning off 'random start points' will help prevent this at the cost of having an unsightly "seam" on one side of the print.
I print nylon with an extrusion temp of 240C and a bed temp of 80C.
- I have found that the best results come from printing on glass that I have applied an even coat from an elmer's gluestick, aka Polyvinyl acetate (PVA). Some have advocated printing on blue painters tape, but my experience with this has been underwhelming. While the print sticks furiously to the tape, there is some shrinkage of the nylon, particularly the earlier varieties like 618, and they will eventually pull the painters tape up from your build platform, resulting in curled edges. I've not had this problem with the PVA glue. Others have been singing the praises of using garolite, which is a celluslose based material that can be purchased in nice flat sheets to which nylon readily sticks without much problem. I never got around to trying garolite because I found the PVA on glass solution fixed all of my problems.
Step 4: Dry Box
Excessive moisture in the nylon filament will boil off as the filament goes through the hot end. This causes steam to push its way out along with the extruded line which will result in bubbles and poor layer to layer adhesion. Besides making the print unsightly, it will also make it more prone to delamination. Moisture control is definitely something to consider when printing in nylon and can also effect ABS and PLA when the humidity is extreme. In the summer months, I use the dry box for all my filaments and store those not in use in a giant seal-able bin.
Materials for Drybox:
- Air-tight tupperware-like box that is an appropriate shape for the spool (Mine was a rubbermade that I believe was made to accommodate cereal).
- 608 bearings X2
- body of a ball-point pen or dowel rod
- 1/4 in tubing push connector
- 1/4 in tubing ~ 1 meter
- 3D printed bearing holder
- foam rubber
- silica desiccant beads ( I purchased some of mine from protoparadigm.com)
The design for this is extremely simple and although I listed specific components, they certainly can be replaced with anything that will function in a similar fashion. The two most important considerations are that the box can be sealed, more or less airtight, and that the filament can be spooled out of the box with as little friction as possible.This second point is absolutely key.
- Print the bearing holders that will go over your bearings and provide a surface on to which you can glue your rubber grippers. I will attache the STL's for the holders I used for my 608 bearings, but if you have different bearings, its is literally one of the simplest shapes to generate in sketchup. Its just an extruded square with a circle pushed down into it.
- Place the bearings inside the bearing holders and glue the foam rubber grips to the flat side.
- Cut a length of tubing or dowel that will both fit inside the bearings inner ring snugly and be just long enough to press against the sides of container when the bearings are attached to each end. I used the body of a ball point pen.
- Drill a hole in the lid for the push connector and screw in push connector.
- Push in length of tubing* (I should note here that I ended up threading another bit of PTFE tubing, of the type that I had used for my bowden extruder, inside the regular PVC tubing in an effort to reduce the friction and it helped quite a bit. I didn't have the push connector that fit the PTFE tubing I already had, so that's why I went with the 1/4in. This isn't necessary if you have the correct connectors and could just go straight to your bowden tubing. Ultimately, you want a very slippery tubing that is only slightly larger than your filament so as to reduce the amount of air that can pass through the tube and into the drybox while not causing too much friction that the filament cannot feed properly).
- Add silica beads to the drybox to help absorb the moisture and keep the humidity in the box low. If you live in a moist climate or are frequently changing the spool, you may want to occasionally dry out your beads using a microwave or oven. They aren't toxic, but I would advocate using a container that would keep them from spilling into an area where your food might be prepared.
That's it, now you have a mobile drybox storage container and filament spool holder. This drastically improved the quality of my prints, especially with 618 and 645 nylon. Bridge seems to be a little more resistant to moisture absorption, but I still use a drybox with it.
Step 5: Now in Color!
Materials:
- Hot plate
- Rit Dye (liquid)
- vinegar or other weak acid
- glass dish
- tongs
- rubber gloves (not a necessity, but it can get messy and it does kinda dye your finger nails...)
- something to blot the model dry like a shop rag or paper towel
Procedure:
To add a little color, I used RIT liquid fabric dye. Start by pouring the dye into a glass dish. Then add your weak acid, (I used vinegar because that's what I had lying around). Make sure to stir the mixture thoroughly and continue to stir the dye periodically, even when the part is in the dye bath, as the dye can tend to settle. The main aspects that allow you to get good color from this method appear to be temperature and pH. If the dye isn't taking to the nylon, add a little vinegar and turn up the heat a little. You'll know when it starts to take because when you pull out the part you will see a sudden and drastic change in color as you hit that correct temperature/pH range. If its not within that range, it will look as though all the dye is just running off the part and it will appear mostly white when you pull it out.
Color considerations:
The time it takes to dye the piece will depend on how dark you want the color. For reference, the green prosthetic hand took about 5-7 min submerged to achieve that color, but its worth noting that I waited until it was heated up to 65C before putting it in.
Another interesting feature of dyeing nylon this way is that the color appearance is a function of the surface area to volume ratio. That is, if there are holes through the model or multiple ridges, that portion will have a larger surface area exposed to the dye at one time and thus be darker relative to a portion of the model with a smooth even surface, for a given amount of dyeing time. This is something to keep in mind if you are dyeing something with a lot of irregular features to it. The other attributes that control the color outcome are concentration of dye to diluent (water + vinegar) and time spent in the dye bath.
A word on the actual color outcome vs what the packages claim, apparently dyeing 3D printed nylon doesn't translate exactly in the color world the way using the same dye on fabric would. They just don't match what they say they will be on the bottle. "Denim blue" was very black at the strong concentration, and gray a lower concentrations. "Cherry red" varied from pinkish to maroon depending on the time spent in the dye. In a way, using this dye is a little like mixing paint for color, its not always intuitive and often requires a few tests to get it right. That said, if you have printed a large complicated part that took a lot of effort to produce, I would suggest using a smaller print to do a test dye before dunking your hard work into the dye. You cannot undo the dye, so make sure you are satisfied with the color outcome before putting that 26-hour print in there. The nice thing about this dye is that, once you have found a concentration that gives you the color you like, you can store the dye at that concentration and reuse it. Granted I haven't reused a dye that was stored for more than a few weeks thus far, but it seems to keep at least for a little while.
Finishing:
Lastly, the print still needs to be dried after dyeing, otherwise you can have residual dye that can rub off onto other things. I have had success with my drybox over night, or if you are in a hurry, you could put it under a heat lamp or in an oven on low (~70-80C) . Although I'm not positive about the food safety of drying dyed nylon in an oven that you cook your food in, so I wouldn't suggest this if you don't have a non-food oven. If you used vinegar to lower the pH, as I did, you will notice a vinegar smell on the print when you first take it out and blot it dry, but don't worry, this will go away and after a day or so you won't be able to detect it at all.
Step 6: Acknowledgements
I appreciate the great effort contributed by makers before me and from whom I have learned so much. I want to make sure to give credit where it is due.
All respect to:
Taulman of Taulman3d.com for pioneering nylon printing for the hobbyist.
Richrap for his myriad contributions in pushing the boundaries of 3D printing. Thanks for always documenting so well, Rich.
The folks of e-NABLE for the great work you do, and for the development of the prosthetic hand featured here.
Models shown here were:
http://www.thingiverse.com/thing:261462
http://www.thingiverse.com/thing:262723
http://www.thingiverse.com/thing:18672
http://www.thingiverse.com/thing:270130
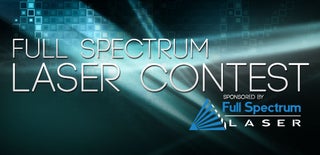
Participated in the
Full Spectrum Laser Contest