Introduction: The Stowaway Simulator
When I was a kid, I dreamed and desired a racing simulator with a full size seat and adjustable pedals more than just about anything that I could remember. But as a kid, I didn't have the funds or the permission to purchase such a thing.....so I made due with pillows propped up around a coffee table. Now with a home of my own I finally thought I could make this dream happen, but I was faced with a new problem....where would I put it? A game room is off the table, for now at least, and my roommate (wife) doesn't think this would be the living room feature we need, and I am obliged to agree.
I of course considered buying a simulator, maybe even one that folds, and just storing it in a closet or basement or something. But I knew that personally, if I had to go and drag it out and set it up, I would hardly use it which kind of defeats the purpose a bit. Thus this instructable!
To solve this problem, I designed and fabricated the "Stowaway Simulator", a cabinet that is attractive enough to be in the living room in plain sight, but unfolds and opens into an adjustable racing simulator cockpit!
Supplies
As with any project, there is never one way to solve any problem and I think this project is a perfect example of this. To develop the Stowaway Simulator, i used a lot of scrap materials that I had laying around, below is an overview of these items.
- Choice of wheel setup, I used a Logitech G29 for my Playstation 4
- I used my LulzBot TAZ 6 3D printer with a 1.2mm MoarStruder toolhead to 3D print assorted brackets and parts
- PLA 3D printer filament
- I used my Universal Laser Engraver to cut plywood for some intricate components
- Basic power tools including a jig saw, cordless drill, drill press, router, and brad nail gun
- Approximately 4' x 6' x 1/2" plywood sheet stock
- Approximately 4' x 4' x 1/4" plywood sheet stock
- 1.5" x 1" x 30' pine lumber for trim
- 1" x 1" x 8' pine for framing
- 2" x 4"x 8' lumber for framing
- Assorted 1.5" MDF scrap board for different trim and framing pieces
- 3/4" wooden dowels
- 1" PVC pipe
- Assorted nuts, bolts, screws, and brackets
- Wood Glue and clamps for assembly
- Kreg Jig and pocket screws
- 2 of These cabinet hinges that are sturdy and snap between 90 and 180 degrees
- Velcro
- Choice of stain and paint
- Folding chair (optional)
In total, this project cost under $70 to build (not including the racing wheel), but that's largely because I used a lot of scrap material that I had from previous projects.
Step 1: Measurements and Design
It was important for me that despite this being a custom simulator, it was still adjustable. I didn't want it to only fit me, but instead be able to adjust the pedals and steering angle for someone of a different build. I chose to use myself as a middle ground, then design room to lengthen or shorten the setup through the various hinges and pivots.
I found taking measurements of my seating position to be difficult. To assist, I took a photo of me in a driving position and used ImageJ which is a pretty simple program that lets you take measurements off of photographs. I was holding a tape measure set to be 12" in the photo which allowed me to set an accurate scale in the program and record difficult measurements.
Originally, the idea was that this simulator would unfold and slide up and under a couch which would serve as the seat. In the end, we ended up moving and getting a new couch with a pull-out footrest which prevented this idea, so I redesigned to incorporate a folding chair which actually added some more adjustability to the seating position.
Step 2: Wheel Rest
The first major component is the wheel rest, an adjustable table that would need to support both the wheel and shifter while also being able to fold away into the cabinet during storage. I started by clamping the wheel and shifter plate onto a piece of plywood, then traced and cut out the panel using a jig saw. I created a plate for the shifter rather than putting the shift right on the board so it too would be adjustable, or you could move it completely out of the way if you weren't using it. The shifter mounted to a 3D printed plate (attached), which then connected to another 3D printed plate (mounted to this board) using a PVC pipe.
After cutting this board, it then attached and pivoted around the main 2x4 beam in the center of the simulator using 3D printed brackets and a 1/2" bolt. I used Onshape to design these parts and a 1.2mm nozzle to fabricate all of the 3D printed brackets so they were extremely durable for these high stress points.
The lower end of the main beam needed to be highly adjustable, both for seating position and user height, but also to fold the wheel away into the cabinet for storage. Again using Onshape, I designed a simple half-circle with 3/8" holes every 15 degrees that I then laser cut 6 times out of 1/4" plywood which were glued onto a mounting block made out of MDF. I chose to cut these out of separate sheets and glue them together mainly based on materials I had, but also to add some extra strength for a crucial component.
The main beam only needs two holes, one for the primary pivot point, and one for a pin which would lock into the 15 degree holes at the desired position. I marked and drilled these after the first half-circles were installed into the supporting block to ensure proper and easy alignment.
Step 3: Pedal Rest
To support the pedals, a simple table was created that is on a pivot to allow for some adjustability, but also a sturdy platform to push against. I again used my 3D printer to create pivot brackets, as well as hook-like brackets that would snap to a dowel to hold position. The pedal platform was made using 1/2" plywood with three pivot brackets at one end and the hook brackets a long the back. I used 3/8" dowels for prototyping and 3/8" bolts with washers to secure the pivot points together during assembly.
The supporting hook arm is a 3/4" wooden dowel that spans between two pine beams mounted to two 2x4 blocks. I was inspired by an adjustable lawn / lounge chair backrest for this design. When lifted, the dowel releases from the hook brackets. Under pressure (as if you are pressing onto the pedal during simulation) the dowel is forced into the hook bracket and it is locked into position. This provides three angle positions for an adjustable pedal platform.
I later added velcro to the bottom of the pedal assembly and the pedal rest to allow for the pedals to be secured to this table, but also to add another adjustment point for a custom driving position.
Step 4: Cabinet
After creating the main structure, including the center beam with wheel rest and the pedal platform, I moved into creating the cabinet around these components. Using my measurements I took of my seating position, I placed the pedal rest and center beam on a sheet of plywood to determine the minimum size I could create the cabinet. The cabinet is made from two sheets of plywood that are 16" x 72" for the front panel (bottom when unfolded) and 17.5" x 72" for the side.
During attachment, I reinforced the pivot system for the main beam and wheel rest using some small L brackets while also gluing and screwing it to the cabinet panel. The pedal rest was attached using its pivot points at one end, and 2x4 blocks with Kreg screws at the other. At the bottom of the cabinet (when in storage mode), I used 1"x1" pine to create a frame that would support the cabinet when it was upright. This frame is assembled using wood glue and pocket screws creating using a Kreg jig.
For aesthetics, I cut and created an barn / country X shaped pattern on the face of the cabinet which was I attached using a nail gun. The two halves of the cabinet are held together using snap hinges which lock it into the two positions when upright in storage, or down flat for simulation. For proper installation, I mounted the hinges to one side of the cabinet, then clamped the cabinet together before attaching the hinges to the second side.
Step 5: Finishing and Assembly
To continue with aesthetics, I applied a Minwax English Chestnut stain and polyurethane to the exterior of the cabinet, and a matte black coat of paint to all of the components on the interior. Because of all the pivot points and adjustable parts, I was able to detach many of the interior components and paint them separately.
For assembly, I reattached all of the components that were mock as assembled during the construction stages using various nuts and bolts. I also applied the velcro to the pedal rest and bottom of my pedal assembly which holds the pedals to the board, but allows them to be removed for position adjustment on the already adjustable plate.
Originally, I create a top to the cabinet that was stained and on hinges so it would cover the wheel from the top during storage, then fold away when opened for simulation. After building this cabinet, I realized this was a bit redundant so I removed the panel all together.
Step 6: Cable Management
To add to both functionality and aesthetics, I created a few different methods for cable management across the simulator, primarily through custom 3D printed parts. I created cable ties that were thin and flexible which could be screwed at either end with a bundle of wires passing through it. These were used to guide wires out of the way of obstruction. I also created a boat-like cleat to wrap up cables that needed to be used frequently, like the power cord or USB connection cable. These two methods were used in combination with zip ties to secure wires together for a clean appearance.
While I wanted clean and seamless cable control, it was important to leave some wiggle room as the whole system pivots and adjusts its position.
Step 7: Seating
Originally I had planned for this cabinet to unfold and slide under our couch which would then act as your seat. But as I was building this we moved and purchased a new couch that didn't allow for this as it had a pull-out footrest underneath it......so I needed to redesign.
So I purchased a folding chair that fit in the cabinet and added some brackets to hold it in place during upright storage using a velcro strap. I also created simple blocks that attached to the edge of the cabinet which the legs of the chair could rest against during use. This makes marking your optimal position easy while also keeping the chair from sliding off the platform during use.
Initially, I was disappointed as I thought the cabinet-to-couch model was a bit more inventive then just packing a chair in the box, but it turned out to improve and enhance the simulator in the end. With the chair, you can more easily adjust the seating position than you could on a couch. Additionally, it is easier to find and add a chair, whether it be folded or from your kitchen, then it is to change your couch.
Step 8: Conclusion
This has been one of my favorite personal builds over the past few years for a few reasons. Partially because it was a creative solution to a problem and want that I've had since I was a kid, but also because it combined a range of production and design techniques for the end result. Its taken me a long time to finally collect and document this project so could share it in an instructable and video, I hope you enjoyed it!
Thanks for reading and happy making!
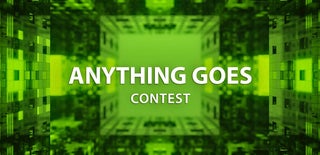
Runner Up in the
Anything Goes Contest