Introduction: Time Turner Necklace
I have always wanted to make a time turner necklace, like in Harry Potter and the Prisoner of Azkaban, but this was something I held for impossible. This was until I started designing in 3D :) In last year's youth design contest, I won a free 3D print. I wanted to design something really special this time, something worth that print. I designed some things, but really nothing was special. But then I thought, why don't I try to make a time turner! The sizes I used are based on the dimensions visible in the movie, though made slightly bigger because otherwise some parts would get really small.
I couldn't wait to get the pieces and finally see if my calculations were correct and the time turner could actually turn! But, time went by and it turned out it was somehow not printed yet, but thanks to some awesome people, including Nicole, I finally received the package I was waiting for. When I opened it, it immediately became clear something was wrong. It was a lot bigger than I expected, about 2,5 times as big. When it was printed, the machine was accidentally set on inches, instead of cm. Luckily, the print was run again, this time in cm. So, I could finally make my pendant :)
But, despite the fact that it took about three months longer than expected (four months total) I was actually happy they made this mistake. This gave me the opportunity to look at the model at a much bigger scale and use it as a prototype.
I hope you like it!
Step 1: Materials
To make a pendant like this, you will need:
- the 3 D printed parts, see step 3 on where to get them
- glue, I ended up using Polycaprolactone (it's moldable plastic, but after a bit of trying it turns out it works perfectly as glue in this case) since my glue gun wasn't an option anymore (see step 4)
- paint
- brushes
- an SMD rework station, I used this for this type of glue, if you are using an other kind of glue this is not necessary
- chain
- aluminium foil
- plastic foil
- a bit of wire
Step 2: Designing the Time Turner
I don't have screen shots of the designing itself, so I'm just going to do a lot of explaining without images.
The hourglass:
The hourglass was created by making two spheres, joining them with a cylinder and adding small spheres on top. To make place for the stick, I added a void stick with a diameter of 0,2 cm. The total size of the hourglass is 1,6x0,8x0,8 cm.
The smallest circle:
The smallest circle has a diameter of 2,5 cm and a height of 0,5 cm. To create the place for the hourglass to fit in, I added two cylinder voids, placed a cube in the middle and added voids of smaller cylinders in the middle. To make sure the hourglass would fit in, I placed it inside the shape in 123D design, to see that it fitted indeed. Eventually I added two holes to the circle, in the middle, across each other, with a diameter of 0,2 cm.
The middle circle:
This was definitely the easiest piece to design. I took a cylinder with a diameter of 3,75 cm and added a void cylinder with a diameter of 3,15 cm to the middle of it, leaving 0,325 cm between the two circles. I added four holes to this circle, all four with a diameter of 0,2 cm, evenly spread over the circle.
The biggest circle:
This circle was quite similar to the middle circle. It was made with a cylinder with a diameter of 5 cm and a height of 0,5 cm. The cylinder I added to the middle of it, had a diameter of 4,4 cm. To add the ears to it, I took the smart torus and removed the bottom part by adding a cube void to it. I then turned the piece so it would be positioned the way I wanted it to be. I repeated this on the other side, but then with the piece turned mirrored.
The small knobs:
For these, I took two cones, that I then joined. To make the stick, I also added a cylinder to it, which has a diameter of 0,18 cm, so it fits in the 0,2 cm holes. For the length of the stick, I took the thickness of the biggest circle: 0,3 cm; and the space between the middle and the outside circle: 0,325 cm. I then added 0,1 cm to make it go in the hole and ended up with a total length of 0,725 cm, making the total heigh of the knobs 1,033 cm.
The small beads:
The small beads are basically just spheres of 0,4 cm, with a hole of 0,19 cm trough the middle, so they fit exactly over the sticks.
The stick:
This is a cylinder with a length of 3,5 cm and a diameter of 0,18 cm, making it possible for it to turn around in the holes of 0,2 cm.
Attachments
Step 3: Getting the Printed Parts
Of course, this is easiest when you have a 3 D printer yourself. But, don't worry about not having one, you can also order this print by going to the model here: Design Time turner and clicking the edit/download: order a 3d print button. I checked it using this link, the total cost of the parts is around 11 dollar.
Step 4: The Prototype
When I had received the (failed) print, one of the first things I did was assembling it. To do so, I used my glue gun. I first assembled the middle part, followed by the little knobs. After this I painted the complete thing, for as far as possible of course ( all visible parts from how it was turned.) The next day, when the paint was completely dry, I started trying it out a bit. First it went perfectly, but after just a few turns, one of the knobs came off. The glue hadn't really connected to the surface of the 3 D print that well. Because I still wanted to put the prototype together, I decided to glue it on again. This is also when I decided I would not be using my glue gun in the final pendant: thanks to the heat of the glue gun, the paint started getting off the print and on the tip of the glue gun..
After a while, the other knob came off as well, so I decided to leave them off until I would have a new method to try out, that would hopefully work. It wasn't until last week that I found the solution. My dad and I were on a Maker Faire, and he bought a few samples of this: protoplast. Like I said in the materials list, it's called Polycaprolactone. When you heat it, it becomes clear and sticky and you can shape it the way you want.
It turned out to work perfectly for the 3D print!! After finally having the prototype working correctly, it was time to move on to the actual pendant, which is also where I switch from describing what I did to giving instructions :)
Step 5: Assembly
Before starting to glue, it's really, really helpful to know how you can put this model together.
Start by taking the hourglass and the circle that fits around it. To connect these two to the circle that goes around this part, you will also need the small stick and two of the round beads. First, put the stick trough one of the beads. Then, add it to the smallest circle, followed by the hourglass. Let the stick go through completely and once it is out on the other side, add a bead to that end as well. You can now push the stick a bit further to one side and add it to one of the four holes in the circle. By pushing the stick back again and positioning it back in the middle, you can add it to the hole across this one as well, which will secure it in place.
To add the small knobs and connect the middle part with the biggest circle, you need to put the knobs through the two holes on the biggest circle. Do not put them through completely, but far enough to add the two remaining beads. You can now place the middle part in the biggest circle and push the knobs a bit further, so the last part will be inside the two remaining holes.
Step 6: Preparing for Glueing and Painting
Since you don't want your hourglass to be gold (or maybe you do, I don't know you, in that case pretend this step doesn't exist), you should wrap it in plastic foil before glueing the pieces together. The foil can be removed later, but adding it after the glueing would get really, really tricky. After wrapping the hourglass, you can join the middle parts (so everything except the outer circle) the way shown in last step.
Step 7: Glueing Basics
*note* these instructions are meant for when you are using Polycaprolactone or something similar.
Start by taking a piece of aluminum foil. Shape it into a small bowllike shape. Place a piece of the plastic into the bowl and turn on the SMD, at about 110 degrees Celsius. Since the plastic won't stick to metal that well, you can easily get it off the foil. When the plastic has melted, you will see it has turned clear and you will be able to shape it. Depending on where exactly you need to use it, you can put it on a metal wire or shape it with your hands.
Step 8: The First Two Connections
If you hadn't already, assemble the model to the part shown in the first image. Melt a bit of the plastic as described in last step. Put it on a piece of wire. Chances are it has already cooled off too much to work with now, if that's the case you can just heat it again. Add it to the holes where the ends of the stick are in as well. Remove any excess plastic by reheating and spinning it around the wire. I used the excess of the first hole to fill up the second one.
Once it's cooled down, and if everything went the way it should, your middle piece is now connected to the circle and won't just come off. Be honest in deciding if the connection is good or not, if you have any doubts, just reheat it and do it again, until you are satisfied with the result and your parts won't just come loose.
Step 9: The Other Two Connections
To connect the biggest circle to the rest of the time turner, start by filling up the two remaining holes in the middle sized circle. You can do this by melting a piece, shaping it a bit with your hands and adding it as shown. When the holes have been filled, remove the excess just as in last step.
Now take the biggest circle. Add the knobs as shown in the picture, not completely through yet. Melt the filled up hole and push the last part of the knob through. Repeat this on the other side. Melt it again on the inside and remove the excess plastic.
Step 10: Painting
For the painting I used gold coloured enamel paint. You might want to experiment with the paint a bit first, I decided to go with one a bit thicker layer to create the look I wanted, but if you want a really flawless painted print, you could better carefully paint multiple thin layers.
For some reason, I decided to paint the entire thing at once :) So, while holding my already painted model, I realised I also needed to let it dry somewhere :P Luckily, I still had the wire and cutting pliers laying on the table, so I made a loop of wire and added it to one of the ears of the pendant, which gave me the opportunity to paint the places where I had been holding it.
Step 11: Letting It Dry
To let the pendant dry, I bent an other loop and added it to the first one. I then hang it over a knob, giving it all the space and time needed to dry.
Step 12: Removing the Foil
When the paint has dried, you can take away the foil. By carefully pulling the end of it, it will unwrap almost automatically. Removing the foil is absolutely great to do, like remove those blue coloured protection plastics new devices come with, to unravel that final look.
Step 13: Adding a Chain
I wanted to just add two of the jump rings to the ears, but the jump rings were slightly too small, so I made two extra rings, silver coloured, and used them to make this connection. After this all that was left to do was add the chain to the rings :)
Step 14: Enjoy :D
So there you have it, your very own time turner! I am so so happy with how this pendant turned out, I hope you like it as well, if you did I would love to know!
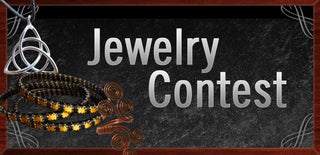
Second Prize in the
Jewelry Contest
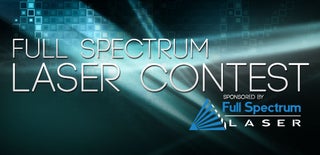
Participated in the
Full Spectrum Laser Contest
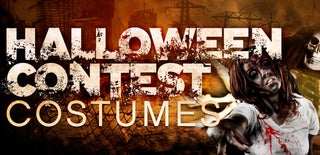
Participated in the
Halloween Costume Contest
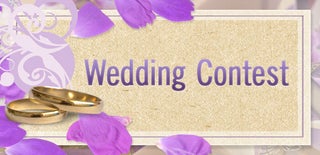
Participated in the
Wedding Contest