Introduction: Tool Pouch Rebuild and Pattern Development
I am not really good at preplanning alot of the things I build. I don't generally create diagrams before hand and during the builds I tend to adjust course as necessary for whatever mistakes I made because of my poor planning. This has cost me time and energy in the past when I want to try and recreate something I've previously made. For example I made some custom capstones for a block wall and at some point a year or two later I had to make some more. I had already gotten rid of the form I built for casting the stones so I had to reverse engineer the form from an existing stone. The result was close but not 100% identical, and its something subtle that I notice everytime I look at the wall. I've had to turn to some of my previous Instructables to remember things like the concrete mixtures I've used in the past.
So when I decided to recreate a tool pouch that I like I committed to making a pattern so that I could remake it again and again as needed. Here is the process I used and some of the hiccups I encountered along the way.
Supplies
- 5/6 oz leather
- Leather dye
- Rivets
- Snaps
- Needles
- Waxed Thread
- Leather punch
- Leather stitching punch
- Belt clip
- Mallet
- Dye daubers
- Buffing cloth
- Pattern Material
- Markers
- Razor blade
- Ruler
Step 1: The Old Model
I don't carry very many tools on me at work, maybe only 10 or 12 small hand tools like a 12-in-1 screwdriver, a specific allen key, a few wrenches and a calculator. These are just the bare essentials I usually need while in an attic or on a ladder. My tool pouches don't need to be very big or have tons of pockets. I get bored with them every couple of years and decide to make myself replacements to change things up. I made this one about three or four years ago at the start of a large project and it turned out to be my favorite variations so far. Although it could have easily lasted 10 more years of use, it was starting to get a little worn out and had a few issues that I wasn't totally happy with. So I decided to build a new pouch based on this design with a few modifications to address the problem areas.
In hindsight I should have taken some detailed measurements before I started removing stitches but I got excited and just started at it. It looks dirty and gross but the leather is still in decent shape with no holes or tears. I'm considering cleaning it up and stitching it back together like new as a backup for the new one. After taking it completely apart I began taking measurements. What I got was the chicken scratch notes you see in the picture. It may not look like it but I have actually taken drafting classes in college years ago. My lettering was much better back then.
Step 2: Layout and More Measurements
After I made all my notes I began making the new pieces. I used the measurements gathered from the old pieces and noticed a few discrepancies. One of the main body pieces was about 3/16" shorter than it needed to be to fit with another piece. What I discovered is that one of the pieces shrunk about that much which was not what I had expected. All of the other pieces had actually stretched a little which I accounted for when taking my notes. I believe the piece that shrunk did so because it was on the inside of another piece and was being compressed over the years. I duplicated all of the stitching lines from the previous model that were alike but there were a few modifications. I compared all of the pieces in common to make sure they were a close match.
One of the main problems I had with the previous version was the side pocket where my screwdriver goes. Because of the construction of the bottom of the pocket there was a small unstitched gap in the corner that over time allowed the tip of the screwdriver to create a space in that corner where the tip would poke out. It wasn't a hole in the leather but a hole in the overlapping layers. This caused me to lose a coupe tips out of my screwdriver which annoyed me, so I revised the overlap and stitching to correct this problem.
Another issue I had with the previous version is the lack of a good place to keep a marker. So instead of just a flat space on the front where the laser burned logo is I added two thin, tall pouches. One for a marker and one for a laser pointer.
Step 3: The Pattern
The part that was going to make this build unique for me is the pattern construction. I had never made a pattern of my leatherwork so I was eager to see how it would turn out. I had seen some other people make patterns out of cardboard and others use clear plastic. I first tried 1/8" acrylic sheet because I liked that it was completely transparent but I found that it was way too difficult to make small cuts in. It was like trying to cut fine details in a pane of glass and I kept cracking it. I then found this stuff sold by Weaver leather that was specifically for making patterns. Its a roll of translucent plastic sheet that cost about $15.00 for 6 sq.ft. Its a bit difficult to write on with anything other than a sharpie but I made due with a good ball point pen for most of it. A pencil did not work at all. Using my notes I first cut out all of the rectangles needed. You can cut this stuff really easily using a straight-edge and a razor knife. After the rectangles were cut I laid out the designs exactly the same way I did on the leather. All of the red lines are the stitching lines. I punched small holes at the ends of the lines to i could just scribe a line between those ends and not have to layout the stitch lines again by hand. Any place that gets a rivet hole has a small hole so I can mark the location of the hole to be punched. I compared the pattern to the pieces I had cut out for the new pouch.
Step 4: Coloring and Assembly
On a complete whim I decided to go bold with the coloring. So, I'm kind of a dweeb. I fully admit that. I had it in my mind that I would create several of these pouches in an Avengers theme. A Captain America, Hulk, Ironman, Black Widow etc...scheme. So this first one is not so much a 'Murica!' choice as it is a Captain America choice.
After staining all of the leather I buffed them with a scrap piece of denim. This helps get rid of the excess dye and gives it a glossy look. I did not use any kind of top coat sealer because its not really going to do any good. This bag will get abused so scuffs and scrapes and spills are going to destroy any kind of protection I put on it anyway. I also didn't bother with any fancy edging or burnishing for the same reason.
After the dye dried I started stitching. I used White waxed thread. All of the stitching holes were punched during layout. I use two needles and do a saddle stitch. I find that this method works well for me and have never had a stitch break. Because of the way the pouches are connected to the main body I had to stitch half of the pouches then stitch them to the body and then complete the other half of the pouch. It was a process I had to work out while doing the stitching. All in all it took me about 6 hours of hand sewing which I usually do on the couch while watching TV with my kids.
The final product looked less Captain America and more like a despondent Optimus Prime.
One small modification I made to the pattern post build was to shorten the marker pouch. the pouch was too deep and I couldn't reach the marker once I put it in there. For this version I just wadded up some denim at the bottom of the pouch to keep the marker up where I can reach it with my fingers. I shortened the pattern 1/2" for the next version.
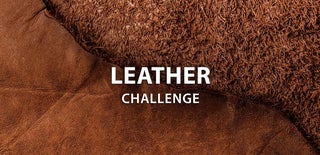
Runner Up in the
Leather Challenge