Introduction: Turn a Chandelier Into Wutang Rings
so i love wutang.. i also just bought some equipment to make jewelry.
i need some practice before i start using the real stuff. I tried silver already but didnt go to well and honestly dont want to waste money in messed up castings
so i was reading about people casting brass, bronze and copper etc. these metals are a lot cheaper than silver and gold.
I originally wanted to cast these wutang rings in gold but gold being 1700 dollar per oz that was out of the question
i decided to go with brass because it looks like gold and it can be plated.
you can typically go to the jewelry supply store or order some brass grain online. i decided to go a different route and decided to make my own casting grain
Supplies
broken Chandelier or brass pieces
furnace
burnout oven
bucket with water and ice
casting investment
vaccum casting table or centrifugal casting equipment
Step 1: Picking Up Your Chandelier
i went to a couple thrift stores and most of them didnt have much. this one very crappy looking one that almost looked like a hoarder store more than a thrift store had a lot of stuff. i guess a lot of stores probably just junk this stuff or recycle it
i was lucky and i found this broken chandelier.
picking brass is a bit tricky. some of it its shinny, some of it is more dull and some of it its more brown. it all depends on the alloys that are used to make it. more copper or more zinc will change it's attributes and strenght.
so you have to put that stuff into consideretion.
the way i picked my stuff is scratch it and making sure it's brass all over not just the outside. also i used a magnet. if it's magnetic it's not brass
you can find more about it here
anyways i bought this chandelier for like 10 bucks. he wanted 20 but i say no buddy.
anyways once you have a chandelier you have to break it apart. i took out all the cables and and broke it into smaller pieces that would fit into my furnace. the stuff that didnt fit i would either bend, step on it, cut it with a grinder etc.
also make sure that you pay attention as some pieces might not be brass, some of it were aluminum around the lightbulbs but were painted gold.
after breaking it apart i heated up my furnace to the melting temperature of brass which is about 950 to 1050
https://www.siamcasting.com/casting_temperature_gu...
i filled up a water bucket and put some ice on it. i also put a metal bowl at the bottom .
heated up the metal and poured the molten metal into the bucket. just poured it and the water and ice makes it into smaller castable pebbles.
melting it also cleans out the dirt and paint that was on it. you dont want to get that into your jewelry so its important you do this process. also doing it all at once gets it out of the way.
i put this in a glass bottle and saved it for when im ready for casting
Step 2: Wax Molds
you can either make your own wax molds by hand carving wax. carving wax and carving tools can be bought online. however i seen people melt candles and carve with an exacto knife. not sure how effective that is but you can go that way if you like
i already had rings in 3d that i designed years ago when i said i was going to buy equipment and started making jewelry.
so i busted out my dusty formlabs form 1+ and started printing some stuff. then i realized that my printing trays were cracked or scratched. see the plastic trays that formlabs sells for like 150 dollars crack really easy. specially the older they are. i cracked 2 out of my 3 trays and thankfully i was able to print some rings.
see those lines between my rings? thats what happens when you have a cracked tray. it's like a sword cut right between my rings
Formalbs stopped supporting my form 1+ years ago and they dont make trays, sell resin, or support their software for this printer anymore. DO NOT BUY ANY FORMLABS PRINTERS. THEY ARE A HORRIBLE COMPANY AND THEY WILL SCREW YOU
anyways i ended up buying some makerjuice castable resin that is compatible with the formlabs 1+. had tons of failed prints because of the printer and because of the resin wouldnt stick to the darn printing bed.
dozens of hours later i managed to print some stuff enough to make a castable tree.
making a tree is a different monster. you suppose to make it in angles and put branching trees and little vents to pour the metal and avoid bubbles.
its easier to make one with some kind of sodering tool. i did my 1st couple of them with a lighter / torch and it was not fun. again you can buy professional carving equipment but i just ended up using this sodering tool i bought to fix 3d prints on kickstarter
you suppose to weight the tree and calculate the metal weight using some kind of formula etc etc.
i just eyeballed it as i have lots of metal it doesnt matter. i did this with some silver pieces and it didnt go well as my rings are very large and i under estimated the amount of silver needed so i got some messed up rings
you live and you learn i guess
Step 3: Casting Investment
here is another thing i learned. if you do very detailed and small stuff using 3d printed parts you should definetly invest in a good casting investment.
i originally bought some regular R & R investment for like 50 bucks at a local jewelry supply store for like 50 bucks. saved me 50 bucks in shipping from R&R yay!!
well no yay at all. 3d printed wax or resin expands during burn off and when this happens small details break off. this creates holes and deformities when casting.
so i ended up going back to R&R and ordered some plasticast investment. its about 50 bucks but the damrn shipping is another 50 bucks argh!!!
https://www.riogrande.com/product/RansomRandolphPlasticastInvestment44lbs/702349?gclid=CjwKCAjwhOyJBhA4EiwAEcJdcYgRlXlUZaeAcvYAE80KCn2b6HYnaJmw0X0ti9Tm7vMczAzBsS72pRoCvKEQAvD_BwE&gclsrc=aw.ds
anyways
you live and you learn.
i have two different types of flasks. perforated and non perforated flasks. both need some kind of funnel like material. i used some plastic covers i was using to make faceshields for healthcare workers.. you can use painters tape or folders or thin cardboard boxes.
i made my own vaccumm casting table which i will make an instructable soon. pretty much mimics a 700 dollar casting table using like 250 dollars worth of parts
so make your tree, fill your flask, vaccumm the investment and let it dry for a day or two.
Step 4: Burn Out, Melting, Vacuuming and Casting
so this is where it gets tricky.
if you went with hand carving wax your burn out process is a few hours.
however if you did 3d printed molds. well it takes like 12 hours. 18 hours for the formlabs super overpriced resin.
so you have to plan out your day.
i did formlabs resin and i ended up casting at 3 am and stayed up till 5am. anyways plan your day. set up your burn out schedule and pray everything goes well.
like i said before i made my own vacumm table. i originally wanted to make it into a perforated flask table which i had working but it lost suction a couple of times. so i put that on hold until i get some welding equipment
the one on the video was a combination of a pipe and my vaccumm table.
so for some reason some youtubers said to heat up your flask to almost the same temperature as the melting temperature of your metal.. WRONG!!!!
the melting temperature and the flask temperature are very important. getting it wrong will overheat your metals while casting which releases some gases and therefore messes up your casting.
as you can see some of my 1st castings had holes.. these were actually gas build ups because my flasks were too hot.
so use this table for your metals and flasks. as you can see my castings got much better after i used the correct temperatures
https://www.siamcasting.com/casting_temperature_gu...
hope you guys likes my instructable. if you did please vote for me. if you have any questions post them below and ill answer
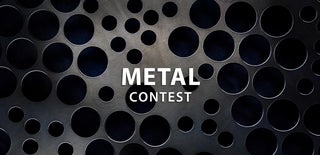
Participated in the
Metal Contest