Introduction: Turning a Corian Container
In this instructable I plan to show how to use a wood lathe to make a lidded container about 4.5 inches tall and 3.5 inches wide. I made this container out of Corian. You can use the same method to make it out of wood as well. Corian is used to make counter tops. It is much harder and much more brittle then wood, but you can use any of your woodworking tools to work on it.
I am disabled and on a fixed income so I can't afford a high end Lathe, but I have learned to use the one I have to accomplish nearly any project up to 8 inches in diameter and 12 inches long.
I used a table saw to cut the larger chunks of material into 4" squares then used a band-saw to cut them into disks. When cutting Corian, be sure to wear a full face shield. It tends to send off small shards of material that are razor sharp and could penetrate an eye in less then a heartbeat.
In addition when turning the initial block of material to make it round, I put masking tape on the side of my hand to protect it. Once you have all the edges rounded, it will come off in long soft ribbons.
To glue the Corian together, I sanded each disc on both sides with 220 grit sandpaper that was taped to a sheet of Corian so that it would be dead flat. For this project I used a two part Epoxy, and clamped them all together at one time.
Wrong way to do it.
When you see the first photos of the block you will see why. When you try to clamp the discs together, they tend to slide all over the place. Resulting in a block that is extremely irregular.
For my next project I used CA glue and only glued and clamped two disks at a time then clamped each of the sections together until I got to the thickness I wanted. It worked much better.
Step 1: Initial Measurment
My lathe has a 3/4 x 16 threaded face plate connector. I don't like using screws to attach things to the face plate, so in the next section I will describe how I build my own.
I went to the local Nut and Bolt distributor and bought a box of 20 nuts for less then $10.00.
When I measured the nuts, I discovered that they were quite a bit too narrow so to accommodate the discrepancy I placed two washers on the shaft first.
Step 2: Making the Face Plate.
To begin with I had several pieces of scrap oak that I cut into disks. then using a 1 1/8 inch Fostner bit I drilled a hole in each disc the depth of the nut. I then used masking tape to cover both sides of the nuts and placed one in each of the wooden disks.
Step 3: Gluing Things Together.
I use a two part epoxy. I did some price matching and found the package of 2 four ounce bottles were much less expensive then the syringe kind. I just put a dollop of each on a piece of corian and mix it up with a Popsicle stick then dab a bit on the edge of each nut. I then break the stick lengthwise and dab it in each edge to be sure the glue is all the way down inside.
It says it only takes 5 minutes to harden, but I leave it overnight to cure to be sure it is secure.
After the glue has cured, I put it on the lathe and true up the edge and the face of each disk.
I have yet to get things assembled so they were square and true.
Step 4: Attaching the Blank.
As you can see, the blank is quite irregular and also weighs considerably more than a chunk of wood the same size. When using wood, I just hot glue the blank to the faceplate, but because it is so heavy, I epoxied it.
Be sure the blank is securely fastened to the drive.
Step 5:
I forced the live center up next to the blank to find the center, then drilled a small hole in the blank and then tightened the tailstock.
As you can see the blank is extremely irregular. If the tailstock were not in place it would spin itself into space.
I tried using regular woodturning tools, and didn't have much luck. I then got out a carbide tipped tool and was able to smooth things out.
Again, you have to watch the chunks that are torn off. They are very sharp and after awhile, they even get very hot.
Step 6: Oops
I then made a small cut on one end the thickness of the lid. Then I put the tool rest on the end to form the lid and found that by the time I got the blank round, it had rattled the faceplate so much that the end wobbled so much that I could do nothing with it.
Step 7: Repairing the Faceplate.
It had wobbled so much that I was easily able to remove the plate from the nut.
Then using a small chisel I removed the glue and then re-glued the nut in place.
Step 8: Reattaching the Plate.
After I reattached the plate, I flattened the face of the plate again.
As you can see, it was way off.
After checking to be sure it was flat, I scraped the glue off of the blank and re-glued everything together.
Step 9: Making Sure It Turns Correctly.
After drilling another hole in the end of the blank, I was then able to turn the blank completely round. I was then able to remove the tailstock and start cutting the bottom portion of the lid.
Step 10: Inside the Lid.
After deciding how thick I wanted the edge of the lid, I turned it to that dimension then hollowed it out.
I then used wet dry sandpaper and a spray bottle and water, I sanded the inside of the lid through the grits from 220 to 1200. Using water does away with a lot of dust and makes things so smooth you hardly have to polish it.
Be sure to wear your face shield and I put paper towel over the lathe to keep it from getting wet.
Step 11: Parting Off the Lid.
I am still pretty new at turning, So instead of a parting tool, I used a hole saw and was able to turn the lid off with very little effort.
Step 12: Turning the Outside of the Lid.
After I removed the lid, I was able to turn a groove in the blank and was able to force the lid on so I could turn the outside.
I was careful to be sure the lid fit very tightly. I didn't want it to come off while turning the outside.
I have been known to use a couple drops of hot glue on occasion to help hold things together.
After finishing the lid, I sanded it using the same method as before.
Step 13: Drilling Out the Center.
I don't have a drill chuck, so I was able to jam a 2 1/8 inch Forstner bit into the tailstock then using a pair of vice-grip pliers I was able to drill a hole in the blank.
Be sure to drill Corian very slowly and clean the shavings out of the bit regularly. As you can see on one of the photos, The shavings are pretty much melted into the bit.
While drilling a hole in a piece of Corian to be used for a pen blank, I was able to melt the bit in so tightly that I had to break the Corian to get the bit out. Another reminder that the stuff gets Hot.
Step 14: The Inside.
After measuring to make sure I was deep enough I removed the tale stock so I was able to get into the inside to turn the opening to the desired size.
I then sanded everything. Inside and out to 1200 grit and then I used headlight polish to put a nice shine on it.
Step 15: Getting Ready to Finish the Bottom.
After polishing I again used the hole saw and parted the container from the face plate.
At this time I turned another groove in the face plate.
Step 16: Almost Done.
To be sure the container didn't fall off the face plate, I used a chunk of Popsicle stick to protect the bottom from the live center. I was then able to turn the rest of the container to the size I wanted.
I then removed the live center and finished hollowing out the bottom.
Step 17: Finishing the Outside and Bottom.
I again used a spray bottle and water and wet dry sandpaper and sanded through all the grits from 220 to 1200.
Step 18:
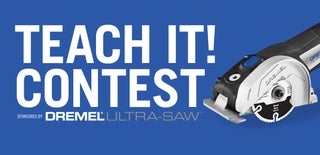
Participated in the
Teach It! Contest Sponsored by Dremel