Introduction: Ultra Low Profile Mill Vise
I built myself a mini CNC mill a while back and while it has helped me out tremendously with my projects there are a few significant limitations with the machine. One of the main problems that I have to work around is my limited Z-axis travel. I did give myself some room to work with when I originally designed the mill but I made a few modifications since then and my current setup has much less space.
I really wanted to have a vise for fixturing work pieces but all of the low profile vises I have seen for sale are still too tall for my machine. So I decided to build my own.
Let's get started!
Step 1: Materials and Tools
Materials:
- Aluminum Flat Bar - 1.125" x 13" x 0.625"
- Aluminum Flat Bar - 0.875" x 1.875" x 0.375"
- Drill Rod - Ø0.250" (Assorted lengths)
- 10-24 UNC Socket Cap Screw (Assorted lengths)
- 8-32 UNC x 1" Pan Head Screw Qty. 2
Note: All of the stock dimensions are rough cut sizes. Please refer to the detailed part drawings in the next step for final dimensions
Tools:
- Manual Milling Machine
- Bandsaw
- Drill Bits - 0.136", 0.150", 0.166", 0.201", 0.235", 0.257"
- Reamer - 0.2510"
- Spot Drill or Center Drill
- End Mills, Two Flute - 3/8", 3/4"
- Facing Mill
- Caliper
- File
- Deburring Tool
- Taps - 8-32 UNC, 10-24 UNC
Step 2: Vise Design
My goal for this vise is simply to have it as low profile as possible. Since my CNC is fairly light duty, I could afford to sacrifice some rigidity to achieve a shorter vise as the machine wouldn't be able to take advantage of a super rigid setup anyway. I also wanted to be able to mount my vise directly to my CNC pallet table which has an array of 1/4"-20 UNC tapped holes on a 1" grid. Different machines would likely require different mounting solutions, so the necessary modifications should be made to the design of the vise.
The final design has the top of the vise resting only 1/2" above the pallet table surface, plus the thickness of the 1/4"-20 bolt heads used for mounting. The vise also features a pair of 4" jaws and an "infinite" opening distance provided the guide rods and leadscrew are long enough.
I used Autodesk Inventor to make a solid model of the vise. All of the detailed part drawings of my design are attached to this step, so feel free to copy or modify them in any way you like.
Attachments
Step 3: Prepare the Stock Material
In order to start machining the parts, I first had to cut all of the stock material to size. I used a vertical rollaway bandsaw to make my life easier, but a hacksaw and a bench vise would work just as well.
The stock material that is shown in the pictures don't quite match the dimensions that I provided in the first step because I used whatever scrap material I had lying around, but the general idea here remains the same. Just follow the part drawings and leave a bit of extra material so the part can be machined to size later on.
Step 4: Machining the Stock Material to Size
Once all of the raw stock has been cut down, I began to machine the parts to their final dimensions. To increase efficiency, I machined all of the parts to their overall dimensions before working on the individual features of each part.
I used the 3/4" end mill to clean up one of the saw cut sides of the stock and then flipped the part around to machine it to its final size. A facing mill was then used to machine all of the parts down to their final widths and thicknesses.
Step 5: Machining the Fixed Jaw
I started by machining the fixed jaw of the vise. This is arguably the most important part of the entire vise so I took my time and tried my best to machine this part as accurately as I could.
All of the hole locations were spotted with a spot drill or center drill and drilled to their respective sizes. The guide rod holes were then reamed to ensure a snug fit with the guide rods.
I decided to save machining the step for holding the workpiece until later so I could machine both of the jaws with the same setup, increasing the overall accuracy of the vise.
Step 6: Machining the Movable Jaw
The machining operations for the movable jaw are very similar to those performed on the fixed jaw. Again the hole locations were spotted and then drilled to size with the guide rod holes reamed. The main differences are that the movable jaw has three threaded holes in the center for the leadscrew that have to be tapped to 10-24 UNC and the guide rod holes are fully reamed through holes.
Step 7: Machining the Jaw Steps
With both jaws drilled and deburred, it is time to machine the vise jaw steps. This step allows for the workpiece to be supported by the vise jaws instead of the guide rods.
I set up the mill to machine the step with the 3/8" end mill and locked the machine down to make sure nothing would move. Once everything was in place I machined the jaws in succession to keep the step profile as consistent as possible.
Step 8: Machining the Backer Block
The backer block supports the free ends of the guide rods and provides additional rigidity to the vise. It can be positioned anywhere along the guide rods so that it can be secured near the movable jaw for extra rigidity.
The machining process for the backer block is very similar to the vise jaws: spot the hole locations and then drill and ream to size.
Step 9: Machining the Extender Block
The extender block allows the vise jaws to open farther than the length a single leadscrew by essentially coupling two sets of leadscrews together. A very important design feature of this part to consider is that it is machined slightly thinner than the height of the steps on the vise jaws so it would have clearance between the pallet table and the bottom of the workpiece. This ensures that the workpiece would be supported by the vise jaws and not by the extender block which would cause height and leveling issues.
As with the all of the previous parts, the hole locations were spotted and drilled out to their respective sizes. The center hole was tapped to 10-24 UNC to accept the leadscrew.
Step 10: Machining the Guide Rods
The guide rods keep all of the parts of the vise aligned. As the guide rods need to have a tight tolerance with the vise jaws and backer block to achieve a smooth sliding fit I made sure to keep the surface finish intact and undamaged.
The rods were loaded into a lathe chuck, faced to their desired lengths and one end was then spotted, drilled and tapped to 8-32 UNC. A light polish ensured that there were no surface imperfections to interfere with and/or damage the bearing surfaces in the vise jaws and backer block.
Step 11: Vise Assembly
Now that all of the parts are complete, it is finally time to assemble the vise!
I started by cleaning off all of the parts to make sure there weren't any chips or burrs left. Once I was satisfied that everything was clean, I slid the guide rods into the fixed vise jaw and secured them with the 8-32 screws. The movable vise jaw then goes onto the guide rods with the stepped side facing the fixed jaw. A 10-24 screw was passed through the fixed jaw and threaded into the movable jaw to act as the vise leadscrew. Once all this was complete I slid the backer block onto the guide rods and the vise is now ready to be used.
To use the vise with the extender block simply remove the 10-24 leadscrew from the moving jaw and thread it into the threaded center hole on the extender block. Two other 10-24 screws can then be passed through the two clearance holes on either side of the extender block and threaded into the matching threaded holes in the movable jaw.
The assembly drawings in step 2 describes the full vise assembly configuration.
Step 12: Mounting the Vise
Having this new vise opens up countless new opportunities for my CNC machining adventures and I am so glad that I took the time to build it. The mounting holes line up perfectly with my pallet thread array and once the vise is indicated it works like a charm. Best of all it doesn't take up nearly as much space as some of the other "low profile" mill vises that I could buy, and it wasn't as expensive either.
Thanks for reading my Instructable and please feel free to post any questions or comments down below!
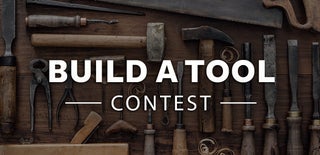
Participated in the
Build a Tool Contest