Introduction: Wooden "Hobbit" Tankard
As a fan of many medieval-era shows and Norse themes, I've taken an interest in the design of old fashioned tankards.
This tutorial is heavily inspired by bricobart's tutorial, but I felt I'd contribute my own findings and experience with an additional instructable, and making use of additional tools to speed up the process.
Materials used:
- ~12m diameter Beech log
- ~2.5cm Hazel Branch
- 450g of beeswax bars
- 10m of waxed cotton cord
- Wood glue
Tools used:
- Chainsaw
- Small axe
- Metal mallet
- Power drill
- Jigsaw
- Files
- Sandpaper
- Rotary cutting tool / engraver
Step 1: Choosing the Logs
The type of log is just as important as the size. Choosing a section of the trunk or branch with as few protruding branches or knurls as possible will yield a more straightforward cutting process. Try to cut sections at least the branch's own thickness away from any major splits/forks to avoid an uneven cross section.
Draw guidelines across the top end of the log using a pen and ruler, passing straight through the centre of the log, irrespective of where the "core" is. The trick is to ensure the outside of the segments are all the same width. A higher number of segments will make it less stable when you re-join them all, but fewer will mean less material is hollowed out due to cutting across a larger angle. You can compromise between stability and mug capacity by cutting closer to the outside of the log when hollowing out, but avoid making the walls less than 10% the thickness of the whole log.
You should also take into account the desired mug capacity. I intended the make mugs that could hold around 2 pints, so I cut a pair of 23cm logs with a chainsaw (the angle is more predictable than when using a standard saw) which varied between 11 and 13cm thick once de-barked. Allowing 1.5cm for wall thickness would give an average internal diameter of 9cm. With a base 3cm from the bottom of the mug, it could be filled with 18cm of liquid before being "full" (2cm from the top), making the mug's capacity around 1150ml (Although this will decrease due to incomplete hollowed segments and the sealing process).
To decrease the chance of the mug warping before re-attaching the parts, ideally allow the cut log section to dry out for at least a week before splitting it into segments.
Step 2: Hollowing the Log Segments
The logs I chose were from a Beech tree, and despite being careful to avoid imperfections, there were several knurls. This added to the uniqueness of each mug, although it presents a problem when hollowing them.
The easiest and most accurate way to split the logs is with an axe and a heavy mallet. When making the first split, make several lighter blows with the axe/hammer along the line without causing it to split very far so that by the time it splits, it does not deviate from the pre-drawn line. All further cuts should be possible without having to re-locate the axe head. There will be some variation to the segment width at the bottom of the mug, but they will be roughly the same as the top.
The major obstacle when hollowing the log out is that the axe has a tendency to curve as it moves down, usually away from the thicker section, so if you made your first cut 1.5cm in from the outside, it would be likely to make the wall thinner toward the bottom. You can avoid this by cutting progressively closer to the outer edge. If you've cut from the desired place at the top, but the bottom edge is still to thick, you can flip it over and cut from the bottom instead, and it should only cut away the excess, rather than going all the way back up to the top.
Occasionally you may find a knot in the middle of the wall, and the axe may veer sharply to one side of it. If it begins to go to the outer edge, stop immediately, and instead hack away at the excess using the axe alone, aiming at the knot (See image 4). You can repair the unwanted crack with wood glue, since it'll be sealed later.
Step 3: Making the Handle
For the handle, I chose a Hazel branch about an inch thick, with an interior angle of about 50°. While there were similar branches available from the Beech tree, they were very smooth once stripped of their bark, and didn't match the rest of the mug. The Hazel branch's natural ridges looked like a deer antler once lightly sanded.
From the "elbow" of the branch, make sure it is at least 20-30% longer than the height of the mug since you can cut it shorter later. Decide which of the segments will host the handle, and line the branch up next to it. Draw a line on the top part of the branch in line with the segment's inner wall, and another on the bottom part in line with the base of the segment and cut the branch there.
Hold the newly cut handle against the outer wall and draw around it in pencil. a simple round hole will suffice for the top (Drill out then file to widen it out), but in order to fit both ends in, you'll need to use a different method for the bottom half. I used a keyhole design which allowed the handle to be slotted in from the underneath at a slight angle, then the top pushed into place.
To secure the top part, I drilled a 4mm hole in from the top, about 40mm deep, and hammered in a wooden dowel.
Step 4: Joining the Segments
After stripping away the bark by hand (Or with the assistance of the axe), remove any loose splinters that may prevent the walls fitting together properly.
For ease of handling, and to add strength to the mug, I used wood glue to join the segments together. I initially tried joining them in pairs, then joining two of those pairs together to form a half of the tankard, but this resulted in too much of an angle offset. A better option is to arrange the segments around a cylinder (A concentrated juice bottle worked well for this size) and glue all but two of the gaps (Leave the separation between segments 1>8, and 4>5 unglued), then tighten them all together with a strap.
Once dried, and the fit of the two halves has been checked after removing the strap, you can drizzle more glue into the cracks to further improve the strength (There are likely to be air gaps due to imperfections between the segments).
Step 5: Shaping the Base
I opted for a slightly raised base, and the irregular nature of the inner walls meant that getting the right shape was difficult. I traced the outline of each half onto a piece of card to get the rough outline, then checked its fit when raised by about 2cm. Some walls were further from the card, and others were closer, but a couple of template iterations later and I had the right shape.
I transferred the two halves of the template to a thin slice of the same Beech tree log I'd cut out earlier with the chainsaw, and cut around it with a jigsaw at a slight angle, so the base effectively protruded several mm further than the template.
I used a rotary cutting disk to create a "V" shaped groove on the inner walls near the base, which would match the edges of the mug's base. The fit wasn't perfect, but after filing some corners down, the two halves could be fitted around the base and glued in place.
Once dried, I began to seal some of the major holes by running small amounts of wood glue into the gaps.
Step 6: Binding the Halves Together
Cut a shallow recess about 3-4cm from the top and the bottom of the tankard. It should be wide enough to accommodate several times the width of the cord you are using (6-8mm). You can create additional grooves for the handle or the centre of the tankard.
Drill a small hole about 1cm deep for the start of the cord to go in. I used a general purpose fast drying glue to secure the cord and also glued the first few cm in place. Once dry enough to apply tension to, add a thin layer of glue across the recess and wrap the cord around as tightly as you can around it, clamping it in place when you've gone all the way around multiple times. The glue will stop the tension being released when you finally un-clamp it.
To deal with the other end of the cord, push it into any nearby gaps, such as the gap around the handle, or between the segments where it will be out of sight.
Rather than go around the bottom half of the handle, I drilled a slot that I could pass the cord through (Which made the perfect place to leave the end of it).
Step 7: Engraving Details
This step is optional, but I chose to carve in some Norse runes, which I felt complimented the design pretty well. Drawing them out in pencil first made engraving them much easier.
I used a high-speed rotary tool with an inverse conical attachment in order to get sharp V shaped grooves.
Step 8: Wax Seal
There are several ways to melt wax, but bear in mind you want to avoid exposing it directly to the heat source so it won't be as likely to burn. I chose to melt the wax blocks in an empty steel can surrounded by a small amount of boiling water on a medium heat within a small pan.
Two of the 40g blocks were more than enough for a tankard of this size.
The most effective way to get a complete seal was to drizzle the wax around the inside of the base, then re-melt it with a paint gun or hair dryer. The surface tension of the wax was sufficient enough for it to cool in a ring, and not fully adhere to the 90° join of the base and the walls, which was why it needed re-melting. The same applies for the inside: Use a small paint brush (10-15mm width) to "paint" the melted wax onto the inside walls of the tankard, then re-heat it to smooth it out. You'll get a large quantity of molten wax pooling at the bottom of the tankard, so there's no point in coating this with wax in addition to the inner walls. Try to slosh it around to cover all the wood evenly. Grooves and recesses will accumulate more wax than flat areas, but only a thin layer is actually necessary.
Sealing the underneath should prevent leakage from the underneath, but there may still be gaps where the handle joins, so be wary of where it might leak onto to prevent damage to skin or clothes. I allowed the last of the molten wax to cool in the lower part of the handle joint to provide a strong seal.
In order to reduce the likelihood of wax running down the outside of the tankard, I stuck masking tape to the outside of the rim.
Step 9: You're Done!
The tankard should be fully sealed and ready to drink from after they've cooled!
Bear in mind that you should only drink cold drinks from it to avoid melting the wax.
If you have leftover wax in the melting pot, there are many tutorials for making wood polish with beeswax and nut-based oils (Walnut oil is recommended). This could be idea to polish the wood with in order to give it a lustrous shine and added protection from water.
Enjoy your new tankard with a well-deserved pint or two of old fashioned ale!
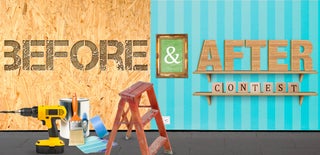
Second Prize in the
Before and After Contest
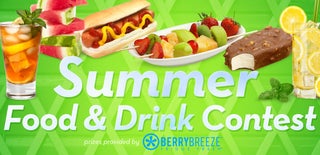
Runner Up in the
Summer Food and Drink Contest
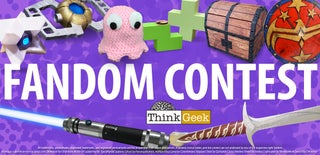
Participated in the
Fandom Contest
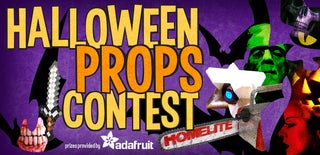
Participated in the
Halloween Props Contest 2015