Introduction: Yet Another 3D Printed Robot Arm
This is my first 3d printed robot arm. If you find any typo's please let me know I am just banging this out right now I will be adding more files and information.
I am trying to locate where I left all of my cads for this and my drawings I think I did this one in Fusion 360 so I will have to reinstall the software and pull the files.
This robot arm will be 6 axes. I have designed not only the arm but the gear reduction and mounting. All part except motors is to be 3d printed. Fortunately I have access to an SLS printer by Stratasys. It does a great job.
Attachments
bearings.pdf
PAC User Guide Rev B.pdf
price motor.pdf
Shopping Cart.pdf
Your AliExpress shopping cart - Buy directly from China.pdf
Your AliExpress shopping cart - Buy directly from China2.pdf
16009-010108B.ipt
16009-010109A.ipt
base plateA.ipt
base plateB.ipt
bearing base cover.ipt
bearing lock gear pack.ipt
cover A.ipt
cover.ipt
cycloid2.ipt
hub.ipt
nema 17 motor mount A.ipt
nema 17 motor mount.ipt
nema17 pivot.ipt
outer cycloid.ipt
Small bearing ring.ipt
16009-010089A.ipt
16009-010092A.ipt
16009-010092C.ipt
16009-010094A.ipt
16009-010094C.ipt
16009-010104A.ipt
16009-010108A.ipt
Supplies
You'll need the following.
5 NEMA 23 stepper motors
1 NEMA 17 stepper motor.
1 24 volt power supply 5 amp.
1 Mach-3 interface for controlling the stepper motor drive
30 feet 18-23 gauge insulated wire.
10 feet wire protector black ribbed.
6 motor controllers for stepper motors
1 tablet computer or micro pc with keyboard and mouse
1 monitor if no tablet
1 enclosure for electronics to mount
all 3d printed parts
1 bearing for each of the axis gear box's
1 bearing for 6 axis gearbox.
x8 Mounting screws
x6 mounting bolts flush mount 10/28 for each gearbox.
x4 10/28 flush mount .75 long bolts for a motor mount. for each gearbox.
Mach-3 software.
1x pendant for manual movement of each or all axis or running program.
x6 offset gear lug
x6 needle bearing for offset gear drive axel lug.
x1 10-28 tap
x1 1/4-20 tap
1 tap handle
1 drill
1 .201 drill bit for 1/4-20 tapped hole
1.96 drill bit for 10/28 tapped hole
wire cutters
soldering iron
solder acid core silver solder
wire strippers
heat shrink tubing
zip ties small and medium
Step 1: First Things First
I needed to come up with a workable and strong gear reduction. What I ended up with is a Hypocycloyed gear reducer.
My first attempt had duel disk reduction. I ended up with 1400 to 1 reduction. This was a way to low. So I removed one disk and remade the outer housing. You can see in the middle pic the duel gear. On the rite, the duel gear resing inside the hub mount.
Once I redesigned the gearbox. I also added an outer ring to hold the large bearing that holds all of the gearboxes together.
Step 2: Too Arms, Too Arms.
Next, I designed the Base. The base is seen in picture 1 in black. This base used bearings mounted to the main hub and arms shoulder axis arranged perpendicular to the rotary axis of the base these bearings road on the surface of the base floor like a lazy susan (see pic 2-3).
In the last picture, you can see one of the arm segments. I had to tape all the holes on both sides of the mounting areas for the motor and gear reduction. Picture 4 shows the arm segment.
Picture 5 shows the tapping of the holes for the gear mounting. These are tapped to 1/4-20. .75 deep. This was an arduous task I could not use a drill for this because the friction would melt the plastic and ruin the print. So all of these damn holes were tapped by and.
Pictures 6 and 7 show tapping of the hubs that mount to each of the pivot points.
Step 3: DA Basics
Here you can see the bearings for the base and the motor mounted into the base Hypercyloyed gear reduction.
There is a tight fit to get all the bearings to find while holding the mounting flang/ring than getting the reduction bolts for fit into the base was time-consuming. It came out well. So far all parts are fitting very well.
Step 4: Use the Force
Motors fit in the middle of the axis with one gear reducer on each side. this gives balance to the forces and uniform torque to the arm.
In this picture you can how the part fit together, However, this is an early version of the gear box. In the subsequent version, I added some more space between the gear faces and the motor so. In doing so I had to add more spacers to each bolt with a threaded pipe cut to the exact length much like a long stand off. You can see the stand offs in picture 4.
You can see the motor mounted and the screws being put into the arm for the main gear which also holds the motor on both sides of the robot for each axis.
Step 5:
As you can see in the first picture that there are a lot of wires associated with six motors and we have to attach all of them to each of the motor controllers. You can see in pic 2 that a test of 3 motors is attached for testing. Pic 3 and for also show the motors and controllers attached. Finally you see the stack of motor controllers and the first 4 axises all installed and wired to the motor controllers.
Step 6: Circuits
Once we added the motor controllers I then added the interface. The center picture is the interface board used with Mach-3 control software and can operate up to 6 axes at a time. Note the pinouts in the second picture. I also added the control setting in the third pic for the motor controller.
Step 7: Control
I added a wireless robot remote control to drive and program the axis through the Mach-3 software.
I also added the micro or pico PC for control running windows XP.
Step 8:
Another look at how each axis goes together. notice the cutout for the wires on the first picture. You can see the third axis going together.
The next major axis is number 4. You can see just at the end of picture 4 the axis is installed.
Step 9: 5 and 6 Pick Up Sticks
Here you can see the last two-axis being built and tested. This one-part finishes off the robot. Pic 1-3 shows the belt and pulleys that drive axis 5. Pic 3 -5 show axis 6. The mounting holes in the face are for whatever end effector you want Pic 7 shows you the bearing that I used.
Finally the video for the testing of the axis.
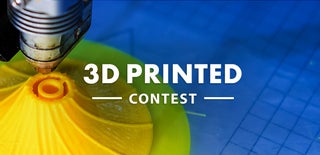
Participated in the
3D Printed Contest