Introduction: 10 Easy Steps to Make Your Own Cello!
*Updated 12/13/15 I apologize for any trauma or
bodily harm inflicted by my 9th grade grammar
My friend and I attempted to build a cello for my 9th grade Science Olympiad Sounds of Music competition--these are the results.
Wood:
-Body: plywood (not the most traditional material I can readily admit)
-Fingerboard: unknown, scrap railing found at Home Depot
Metal
-Strings: Stock cello strings bought from local music store.
-Tuners: An L-bracket, a washer, and a screw.
-Metal Bar: I used a metal bar for the area where the fingerboard met the peg box.
Range
C2 to F6, the range of a normal cello
Sound quality
Relatively muffled but plays well for a homemade instrument
Video: https://www.youtube.com/watch?v=MN-EsLC4eeY
A quick timeline
1. Construction began with finding dimensions. Plans and measurements are readily accessible on the internet
2. Once plans were obtained, I mapped out a blank of the faceplates.
3. Using these blanks, I copied them onto two sheets of plywood.
4. Taking the leftover wood (save the planet!) I cut out the bouts (sides) of the cello.
5. I soaked the plywood in water overnight, this unorthodox method surprisingly worked! You will notice that the veneer of the plywood peels off.
6. I cut out two f-holes onto the faceplate using a power drill and handheld jig saw.
7. Creating the bridge was a bit more involved, I had to borrow a table saw and a belt sander from my school’s woodshop.
8. The scrolls and peg box were simplified for ease of construction. Note that the pegs are lubricated with graphite and/or bow rosin to control its coefficient of friction.
9. The Fingerboard was created (see above)
10. All the pieces were glued together using wood glue, with hot glue where needed, or with deck screws.
This cello was constructed for a retired Science Olympiad event called Sounds of Music. We had to created two different instruments of different registers, take a sound physics test, play Canon in D by Pachelbel, compose an original piece of music, and play both pieces. We placed second at states.
Step 1: Tools
What you'll really need for this project varies
with how nice you want your cello to be. I was under a deadline (the competition) but depending on your skill and time limits you can obviously take this above and beyond!
-Handheld Jigsaw: this gives you so much freedom when it comes to cutting the plywood, just be sure to use the proper safety procedures
-Power drill: this will help, especially when it comes to creating the peg holes and the f holes
-Hot Glue Gun: self-explanatory
-Ruler, pencil, calculator
-Sandpaper/ belt sander: this is imperative! It saved me so much time by cleaning up rough edges and sanding down the wood where I wanted slopes and curvatures, especially on the bouts.
-Access to a woodshop: this will help but is not necessary.
-A reliable recycling bin: I used a trusty recycling bin in lieu of an actual table.
-Creativity & Innovation: to have as much fun as you possibly can!
Step 2: Marking Out the Measurements
After doing some preliminary research online, I
found some blueprints. I translated them to a canvas- yes a painter’s canvas- as a basic guide. It’s probably faster and more accurate to trace the outline from a cello, but at the time I only had a ¾ size cello at home and was aiming to create a full size cello.
Measurements: http://woodsoundstudio.com/setup.htm
Step 3: Cutting Out the Faceplates
Here I used the guide created in the last step to cut out a wooden blank. This blank will be used later to help set bouts.
Step 4: Bending the Bouts
Unfortunately it didn't occur to me to take many pictures of this process, but it is relatively simple to recreate. I poured hot water into a garbage bag lined wagon and set the cut bout pieces overnight. In the morning the plywood gave more slack, just enough to bend without worry. It is important to note that I peeled off the veneer. Using the blank, I bent the pieces and fit them on the sides of the blank using dumbbells to hold them in place. Then I glued them together and to the back face plate and set it overnight.
Step 5: Putting Everything Together
Here you can see the process by which the bouts were glued down. The face plates were then subsequently placed on top, followed by drilling the f-holes.
Step 6: The Endpin
The end pin was somewhat of a pain to create. I used a small block of wood to reinforce the bout and used a scrap rod that can easily be scavenged from a blinds to go.
Step 7: The Bridge, Peg Box and Tail Piece
Okay here's where things get complicated. To build the bridge I drew the outline of a bridge onto a flat piece of wood and SLOWLY cut it out with the jigsaw. Slow and steady wins the race. Then I used a belt sander to taper the bridge form top to bottom. To make the heart I drilled three holes and slowly carved them out, same for the kidneys.
The peg box, as you can imagine, is a box fashioned out of 3 pieces of wood. For the pegs, I used 4 1 inch wooden dowels with fashioned pegs attached with wood glue. To make sure the pegs sticks to the peg box I used pencil graphite to make them easier to tune, then crushed rosin stop them from sliding.
The tuners are created using an L-bracket, a screw and a washer to control the tension.
Step 8: Finding the Right Fingerboard
This is probably the most important step- the fingerboard. If your fingerboard is too flimsy, the neck will snap. If it's too thick you won't be able to play it- find the right balance.
For this cello I used a l-brace, glue, and a screw to attach the board to the body. I MUST STRESS THIS PART, AS IT IS PROBABLY THE WEAKEST PART OF YOUR CELLO!! In fact I dropped a cello once and this is the exact area where it broke.
Step 9: Putting Everything Together
Now you should have
-your body finished
-tail piece finished
-bridge, pegs and pegbox
-fingerboard *note the fingerboard in this picture is not the actual final product*
-endpin
Now all you have to do is put them together!
Step 10: The Bow!
The bow is simply made from fishing line under high tension. I used sandpaper to barb the fishing line to give it more drag on the strings of the cello. The tension on the bow is achieved the same way the tuners on the cello operate.
Step 11: Time to Play!
That's IT!
Test your cello and make any modifications if necessary. Feel free to contact me with any questions, comments, or concerns.
-troubleshooting-
Strings are too high
- i personally had this problem- i didn't map out the angles, lower the bridge, your bridge is too high
No sound??
-First check that there is nothing there to muffle the string, for example the string is too close to the fingerboard to vibrate, then check that your bow is working properly. A good rule of thumb would be to use a real bow- then use your homemade one.
I can't tune it!/ The pegs won't stick!
-by this point you really want to use a lot of rosin powder on the pegs, but DON'T OVER DO IT. Make sure to hear a bit of creaking, but if you hear A LOT of creaking that's not good your, pegs will break! Use some pencil graphite to counter the rosin.
That's it! Hope you had as much fun as I did and enjoy your new cello :).
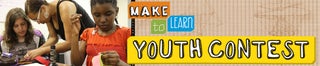
Fourth Prize in the
Make-to-Learn Youth Contest