Introduction: 1000W Portable Induction Heater
Hey guys, this is my portable induction heater that can be powered either with batteries or connected to a power supply. You can use this to heat metals well above 1500 degrees Fahrenheit. I have made different attachments for cooking, releasing seized bolts, a solder pot attachment, and more. Take it camping or just use it around the shop to heat up different materials.
Step 1: What You'll Need
1. ZVS Driver
2. 6"x6"x4" Electrical Junction Box
4. Heavy Duty 6 AWG Wire for output
6. Binder Clip
8. Thick walled heat shrink tubing
Step 2: Cut Four Blocks of Plastic.
Step 3: Press in Threaded Brass Inserts With a Soldering Iron.
Step 4: Attach Standoffs From the Opposite Side of the Blocks.
Step 5: Attach the Standoff Blocks to the ZVS Driver.
Step 6: Glue the ZVS Driver Into the Base of the Enclosure.
Step 7: Drill Holes for the Cable Glands, the Switch, and the Binder Clips.
Step 8: Bend Out the Binder Clips and Drill a Hole in the Center.
Step 9: Final Assembly
After feeding the cables into the cable glands, tighten them to the enclosure. Use screws and nuts to attach the binder clips and velcro to attach the batteries. Use a few layers of heat shrink tubing to your output cable to make the area for gripping more rigid. Use the terminal strip block to attach your coil to the hand wand.
Step 10: Taking It a Step Further.
After you have finished assembling the battery powered version, there are a few thing you can do to upgrade your unit. You can make an adapter that will allow you to use a high power 24VDC-48VDC power supply.
If you choose to go the power supply route, you must use two different switches to improve the reliability. One switch to turn on the power supply and another switch to apply power to the induction heater. The power supply should be turned on first and then you can turn on the power to the induction heater. The reason is that most cheap switching power supply don't reach their rated voltage quick enough to kickstart the oscillation of the circuit. This causes both of the MOSFETs to latch up and catch fire. The same will happen if your supply or batteries drop below 12V under full load.
Do not turn the unit on with something in the coil as this can also damage the unit.
You can also design different attachments for different uses. I've salvaged a coil from an induction cooktop as well as made my own cooktop coil. In addition to that, I've made an induction solder pot.
Step 11:
That's it guys! Let me know if you have any questions or comment.
Please vote for me if you liked this instructable or found it useful!
Until next time,
Anthony(Proto G)
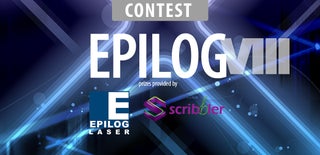
Runner Up in the
Epilog Contest 8