Introduction: 30 KVA Induction Heater
Introduction
Induction heaters are used to heat conductive materials in a non-contact process. Commercially, they are used for heat treating, brazing, soldering, etc., as well as to melt and forge iron, steel, and aluminum.
This Instructable will walk you through the construction of a high-power (30kVA) heater, suitable for melting aluminum and steel. Note that to take full advantage of this design, you will need a 220V outlet, at least a 50A single-phase one and preferably a 50A or 60A 3-phase outlet.
About the author:
Bayley Wang (me) is a EE student at MIT. I'm responsible for a variety of nefarious power electronics projects which you can find on my blog; perhaps most interestingly is oneTesla, which has since gained a life of its own as a startup creating DRSSTC kits.
WARNINGS
- This project uses mains voltage. While well-behaved, 110/220 mains can seriously injure, maim, and/or kill you if used improperly.
- The voltage across the tank capacitor can potentially ring up to hundreds of volts. Don't let the 20:1 step-down ratio fool you!
- When scoping the circuit, beware of ground loops.
- The work piece, naturally, can get very hot. DO NOT TOUCH! Less obviously, do not rapidly quench the work piece with water, as this can lead to dangerous sputtering.
- This project uses power electronics. Under fault conditions, semiconductor devices used in this project may rapidly heat, vent, and/or release rapidly moving shrapnel. Shield appropriately.
WIth that said and done, let us move on.
Step 1: Bill of Materials
- 2 IGBT half-bridge modules. I used Powerex CM400DU-12F 400A 600V Dual IGBTs; anything of similar power handling and switching speed should work. These can be purchased as cheap surplus from Ebay.
- 4 MOSFETs or IGBTs for the gate drive. I used HGTG30N60B3D's, which are way overkill for the application. They need to be able to dissipate about 30W without burning up.
- 2 gate drive IC's, of at least 9A peak current capability. I use the UCC37322 from TI.
- 2 ferrite toroids. These are your gate drive transformers, and should be able to pass a reasonably clean square wave at 50 kHz. Magnetics, Inc. and TSC Ferrite International are good manufacturers, or you can salvage them from old CRTs or switching power supplies. The powered iron cores from ATX supplies rarely work.
- Large ferrite toroids for the toroidial coupling transfromer.
- 1 TL494 PWM IC.
- 1 at least 20 uF, at least 20V film or ceramic capacitor.
- Assorted resistors, capacitors, and potentiometers for the driver.
- 10' of 1/4" soft copper refrigeration tubing.
- A water block capable of accommodating the two IGBTs. A large heatsink may also work, but I haven't tried.
- 2 aluminum or copper bars, ~3/4"x8"
- 2 1/4" compression unions
- A 4-position rotary contactor, good for several tens of amps.
- A screw-terminal electrolytic capacitor of reasonable quality. I recommend at least a few hundred uF for 3-phase operation.
- A high-quality, low inductance snubber capacitor for the bridge. Ebay has cute brick-mount 20 uF blocks for $5.
- One or more high-quality polypropylene capacitors for the tank capacitor. More on this part later.
- An analog current meter good for several tens of amps.
- A 3-phase bridge rectifier (or single-phase if you are willing to settle for single-phase operation only).
- A suitable project case and associated hardware (3-phase breaker, cord, plug, etc).
- A water pump capable of a couple GPM
- Tubing appropriate for hooking up the water-cooling.
- A Variac for testing.
Step 2: Words of Wisdom
The IGBTs: or "bricks", as we like to call them. They should be good for 600V (not a concern, I've never seen a brick rated under that before), at least 200A (I use 400A modules to be, safe), and more importantly, need to be fast. This is where you need to check the datasheet - IGBTs have an inherently long turn-off delay. For 65 kHz operation, rise time + turn-on delay + turn-off delay + fall time should be under 2 uS.
Bricks come in several types: single-transistor, dual transistor, 6-pack, and some rarer types such as chopper modules. Single-transistor modules are prevalent for 1200V and larger IGBTs, and have the highest thermal ratings and are the most difficult to mount. Duals (half-bridge modules) are the much easier to mount and can dissipate less. They are most common for 600V modules. 6-packs are used for 3-phase inverters, require no external power connections, and have the lowest thermal ratings.
Use what you see fit; this tutorial uses half-bridge modules.
The tank capacitor: is very very important. It handles tremendous amounts of reactive power at very high frequencies. It is absolutely essential that this part be selected appropriately. It must be a high-quality polypropylene or mica capacitor. I use giant snubber capacitors made by Eurofarad; alternatively, a series/parallel array of smaller capacitors (such as the Tesla coiler's beloved CDE942 series) should work. The ultimate capacitor, of course, is a water or conduction-cooled unit made by Celem, but such caps will run you about $150 for a 2 uF unit. You want enough capacitance to resonate with your work coil at no more than 70 kHz.
Step 3: Principle of Operation
Induction heaters function by surrounding the work piece with a coil carrying a high-frequency (kHz to low MHz) alternating current. This induces eddy currents in the work piece, which acts as a shorted 1-turn transformer secondary. The currents can be tremendous, on the order of several thousands of amps. This causes high I^2R losses in the work piece, heating it.
Schematic Description
Note: Ignore the transistor model numbers; I just used what Eagle had built in.
IC1 is a TL494 acting as an oscillator with adjustable dead time and frequency. The output is fed into the input of two UCC37322 9A gate drive ICs, which "beef up" the signal into something capable of driving high-capacitance transistor gates. The output signal is passed through C5 to insure only the AC component reaches GDT1, a gate drive transformer. This transformer provides the electrical isolation necessary to drive Q1 through Q4, which form a full-bridge. This intermediate bridge is necessary to provide the high average power necessary to drive Q5 through Q8, a full-bridge of large IGBT modules.
This bridge forms the main inverter. The output of this inverter is stepped down through a 20:1 torodial transformer TR_MATCH, which provides impedance matching as well as isolation for L_WORK, the work coil inductor. The capacitor C_TANK forms a resonant LC circuit with L_WORK; when driven at resonance, this circuit displays zero reactive impedance to the inverter, allowing for higher powers and minimizing switching losses in the inverter.
Step 4: Construction: Controller
Construct the logic circuit as you wish, either by using the attached images to make boards or using perfboard or a breadboard.
The gate drive transformers must be able to pass a high-quality square wave at your operating frequency. To check this, wind 10+10 turns on the toroid, connect one set of windings to a signal generator, and scope across the other. The output should look like a reasonable square wave.
The GDT should be wound with 5 twisted wires to minimize leakage inductance. Many people have had luck with using CAT5 cable, which comes pre-twisted.
Step 5: The Inverter
The inverter should be very well-cooled, either with a large heatsink or a waterblock. I used a waterblock for compactness and robustness; but a big (think 12"x12"x3" with several hundred CFM of forced-air cooling) should work too. The pump should be relatively large to handle the pressure drop through the work coil (mine was rated for 2GPM).
The main filtering capacitors should be placed close to the bridge itself, preferably bolted across the busbars. You should also use a snubber capacitor (the black box in the picture) placed directly across the transistors to reduce voltage spikes caused by excitation of the parasitic inductances in the inverter layout.
Using half-bridge or six-pack modules is the easiest way to buld the inverter; a bridge of single transistors will require access to a machine shop to do right.
Step 6: Work Coil/Tank Circuit
The coupling transformer should be toroidal. Wind ~20t around some large ferrite cores (I was using a stack of 4 ~4"x1" cores).
The tank capacitor willget warm. It should have significant terminal area to conduct both heat and thousands of amps. If you are using a MMC of small capacitors, solder them individually to large copper plates. If you are using a Celem or a giant snubber, bolt large copper plates to the terminals. Then in either case, solder the terminals to the copper tubing that forms the rest of the tank circuit.
Attach the work coil to the tank circuit using compression fittings; this allows you to change work coils to accommodate different loads.
Make the work coil out of at least 1/4" copper tubing. Thicker tubing is less lossy, but harder to handle; trade-off between the two as you see fit. When winding the work coil, it helps to fill it with sand to prevent the tubing from collapsing. As a rule of thumb, the resistance of 1' diameter copper tubing at 65 KHz is 0.8 mΩ/m; that is, to compute the resistance of your secondary, multiply 0.8 mΩ by its length and divide by its diameter in inches.
Step 7: Testing and Usage
Assemble everything according to the schematic. Use a current transformer on the primary side (100t burdened with a couple ohms around a ferrite toroid will do) to monitor the waveforms.
Using a current-limited bench supply (preferably 30V, 10A), slowly ramp up the voltage until enough current is drawn to give a clear reading on the 'scope. Adjust the frequency pot until the waveform is a clean sinewave, and current draw is maximized (you may have to search a little to avoid harmonics). If you don't have a scope, just tune until current is maximized (mine drew something like 40A at 200VDC on the bus, unloaded).
With ~30V on the bus, load the work coil with a bolt. At a few hundred watts in, it should get hot within a couple minutes. If it draws power, but the workpiece doesn't get hot, check the transistors for heating. If they get excessively hot, your bridge is shooting through.
If all is well at low powers, you are ready for a high-power test. Use your favorite DC source (single phase, three-phase, smoothed, unsmoothed, etc - it doesn't really matter) to power the bridge. Preferably, use a Variac, in case it draws too much current (you can predict current draw from the low-power tests by noting that the heater is a fairly linear load). Don't forget water cooling!
At a few kilowatts, without a crucible, you can melt aluminum and copper and make steel orange-hot. 10 KW+ (50A dryer/stove line or 3-phase) is necessary to melt steel in open air. A crucible helps a lot.
You can control power by very slightly detuning the inverter, or by changing the bus voltage, or by tapping the matching transformer. The latter is a recommended feature, and steel and copper have very different effective "resistances".
Good luck, and have fun!
Step 8: Sources for Components
By popular demand, I've added this page.
For the power components, one word - EBAY.
EBAY EBAY EBAY. There is no way this project could have been remotely affordable without it. For the IGBT's, the most reliable source is CTR Surplus, who goes by the usernames ctr_surplus, deals_ctrsurplus, and lisa_ctrsurplus. CTR Surplus also has a constant supply of large electrolytic capacitors, snubbers, and heatsinks used in this project.
The capacitors are also from CTR Surplus - a search for "Eurofarad" works wonders.
Copper tubing is best purchased from Home Depot (assuming you live in the US). They have prices that beat most Internet sources.
The toroids can be from Magnetics, Inc or TSC Ferrite International.
Miscellaneous small components can be purchased from Digi-key.
Arrow has very good prices on transistors, far lower than most other suppliers.
Submitted by MITERS for the Instructables Sponsorship Program
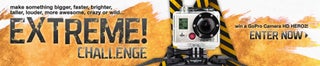
Finalist in the
EXTREME! Challenge