Introduction: 30lb Fighting Robot-Nyx
I recently built a new 30lb fighting robot for the NERC Sportsman class and Dragon*Con Robot Battles events. This instructable will follow the build process and will include links to parts suppliers, machining resources and .dxf drawings of the custom components used to make the robot.
If you are serious about building your own version of this robot, contact me and I'll be happy to help where I can.
Step 1: A Pile of Parts and the First Day of the Build
The pile of flat stock was waterjet cut by Westar Mfg. out of 6061 aluminum and 4130 steel.
Drawings for this collection of parts along with materials, thicknesses and quantities can be found here.
The top armor and two supplimental weapons were not included in that collection to allow modifications to be made for weight purposes. Those files are located here.
These drawings were done with the intent that most would be made on a waterjet, and as such did not require dimensioning. Each of the drawings that was meant for waterjet cutting has a 1" reference square on the sheet.
With the great deal of interlocking components, the order of assembly is important. The first components to be assembled are the weapon hub, support hubs and weapon sprocket. Doing this first also showed the first issue in the build. The sprocket model on McMaster.com did not have the correct hole spacing which meant only 3 of the 6 planned bolts would fit. These holes are all meant for a #10 bolt, and without a clearance hole bit on hand, one had to be ordered.
The other main piece of the day was countersinking the holes on the inner rails to ensure there would be no contact between the moving roller chain and the bolt heads. The front threaded spacers also needed to be added and loctited as the bolt heads will be covered by the D shaped bearing blocks during assembly. A product called Nutstrip is used to connect the panels together, allowing for quick assembly.
Step 2: Day 2, Padding and Keyway Modification
At this point the build was stuck since it would be another day before the 0.201" drill bit would arrive from McMaster-Carr, so I tackled two of the smaller projects.
The first was adding padding to the area the flipping attachment would contact the front panel. I used some 3/16" thick rubber cut into a hollow square shape and glued to the aluminum plate. The small pocketed area was added to allow the use of the optional low rpm dual grinding disks, as the main weapon hub would brush against the aluminum plate when spinning continuously.
The weapon sprocket needed to sit closer on the weapon motor shaft than the existing keyway allows and without a broach available, I chose to use a mini-mill with a 1/8" endmill to expand the keyway area. The shaft was clamped to the table with the existing keyway sitting roughly level. The endmill was then brought into the keyway slot and aligned with the vertical walls of the keyway. Using low spindle speeds and some cutting fluid it was easy to expand the keyway. I've also included a picture of the modified shaft next to a stock shaft for comparison.
Before calling it a day, I used some Goop adhesive to glue the bearings into the bearing blocks and the weapon hubs to keep them from sliding around while I was assembling the weapon rack.
Step 3: Day 3, Weapon Rack Completion and Initial Chassis Assembly
The first task of the day was drilling the new mount holes in the weapon sprocket. I used the steel weapon hub as a guide for the drill bit and quickly added three new holes to the steel sprocket.
The weapon hub was bolted together and the 3/4" tubular steel shaft (1/8" wall, 9.875" long) was slid through the assembly. Two shaft collars were added to each side and the two bearing blocks were slid on the ends of the shaft. These bearing blocks were bolted to the front armor panel locking the assembly together. The weapon hub was centered on the shaft and the shaft collars were locked down at the hub and bearing blocks to prevent it from moving side to side.
The two inner side rails were slid onto the rear armor panel and the weapon rack was slid into the front. These four sections were then bolted together.
The last part of the day was the addition of the remaining hex standoffs and the baseplate. For the initial build the holes were mistakenly drawn to 0.250" diameter when they should have been 1/4" clearance holes. (0.266" diameter) This has been fixed for the posted drawings.
Step 4: Day 4, Drive System Install
First, the dewalt powerdrive kits were bolted to the baseplate. I'm using the optional motor retainer kit with the stock steel threaded rod replaced with aluminum for a 3.6oz weight savings. After that, the outer side rails were bolted to the frame. 1/2" shoulder bolts were added with the threaded end on the outside of the outer wheel guards. Once they were added, measurements were taking to figure out how many washers needed to be added. The outer wheel guards were removed, allowing for the addition of washers, wheels and the drive shaft, which itself had washers, shaft collars and keyed sprockets on it. Once all of this was added the outer panel was reattached. The weapon motor shaft goes into an aluminum pillowblock made from scrap, the exact design will be up to you if you replicate it, the only important part is the bushing or bearing used in it must be 1" above the baseplate.
The next step was measuring and cutting the chain. First I aligned all of the sprockets with the wheels and weapon, then I took the length of roller chain I had and wrapped it around the section to determine where I needed to break it. Once the chain was broken at the proper length, I wrapped it back around and added the master links. At this point, the mechanical assembly is complete.
Step 5: Day 5, Wiring and the First Test Drive
The electrical system consists of the following components:
1 Hobbyking R610 receiver
1 Team Whyachi MS-1 switch (discontinued, MS-05 should be adequate)
1 Turnigy Nano-tech 6s1p 2650mah Lipoly pack
1 Digimix V-tail mixer
3 Holmes Hobbies BR-XL motor controllers
A small pile of deans connectors, wire and bullet plugs
The three BR-XL controllers are velcroed to the baseplate between the three dewalt powerdrive kits. The motor side of the controllers each connects to 1 motor, the positive lead on the battery side runs to the MS-1 switch, which has the positive battery lead connected to the other terminal. The negative lead for each controller connects directly to the negative battery lead. The drive PWM cables connect to the V-tail mixer, which then connects to the Ail/Ele ports on the rx. The weapon controllers PWM cable goes directly to the rudder port on the rx. A power light built using a high output LED and a resistor is connected in the same fashion as the power leads for the motor controllers.
The foam padding that the battery is resting in is to minimize the risk of shock damage in combat.
Once all of the systems were hooked up and calibrated (full calibration instructions come with the BR-XL controllers, only calibrate one at a time to avoid issues) the robot was ready for its first test drive.
Step 6: Final Touches
After doing some testing, it appears that the weapon drive will need a torque limiter for the flipper attachment. For now, the dual disks are working very well:
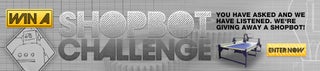
Participated in the
ShopBot Challenge
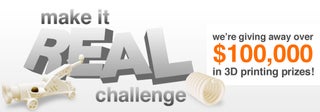
Participated in the
Make It Real Challenge