Introduction: 3D Print a Vector File Using Tinkercad
My pal Diego and I wanted to make something cool for our artist collective called "OUR HOUSE". He came up with this super sweet logo for our project, and I wanted to 3D print it as an ornament. I think it could be made in to jewelry too, and I hope to make a mold from this model. (Next Instructable!)
He sent me his Adobe Illustrator logo file, so I started hacking away at it to create some models that we could print :D
Step 1: Export Your Vector.
Step 2: Tinkercad
My user experience in Tinkercad was awesome. I felt like I was a 3D modelling pro (this is far from the truth). I was able to make something I really like very quickly.
Setting up an account was a breeze, and I was able to start mushing models together quickly.
Step 3: THINGIVERSE!
I knew I wanted to incorporate additional models of homes in to my existing vector-based model, and looked to Thingiverse to find many adorable and awesome models to load into Tinkercad
Thingiverse is a place for you to share your digital designs with others, and appropriate others designs into your own under the Attribution rules of Creative Commons.
http://www.thingiverse.com/thing:86415
http://www.thingiverse.com/thing:29468
http://www.thingiverse.com/thing:18960
http://www.thingiverse.com/thing:26244
http://www.thingiverse.com/thing:88464
http://www.thingiverse.com/thing:11673
http://www.thingiverse.com/thing:24379
http://www.thingiverse.com/thing:6539
Step 4: Arrange Models in Tinkercad
I was able to import both .svg files, as well as the .stl files from Thingiverse to my Tinkercad workspace. From there, I started smooshing them together, adjusting the z-depth and dimensions of my figures until I was happy about how the model looked. My last step was to group all the models together, to create one continuous model.
I did this by dragging the marquee over the entire workspace, then hitting the "Group" button in the upper right hand corner of the Tinkercad browser.
Step 5: Export Model
I downloaded my model file as an .stl from Tinkercad so I could print it out with a 3D printer. From the Tinkercad browser window select: Design>Download for 3D Printing>.stl
I know that the printer I was going to use prefers .stl files, but it may vary case to case.
Step 6: Printing the Model.
Here at Instructables HQ, we have access to Autodesk's fleet of Objet Connex 500 printers. These printers use UV light to cure resin layer by layer until a complete model is produced. They are very different from the fused deposition printers you may have seen or used before (MakerBot, RepRap, Up!, etc), not only can they print out of many types of materials (ranging from flexible rubbery material to hard polymer), but they are also extremely precise. In the x and y axes they have 600dpi resolution (that's about 42microns), and in the z axis they have a resolution of 16microns.
When the prints come out of the printer, they are coated in a support material that needs to be scraped off, and in some instances, power washed off.
This print needed minimal cleaning, and I can't wait to install it at our space, or make a mold out of it so we can easily cast other models like it. :D
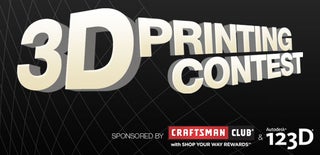
Participated in the
3D Printing Contest