Introduction: 3D Printable Nerf-Style Gauntlet: Falconer MK II
This is my second generation nerf gauntlet. Inspired by Yang's Ember Celica's from the anime RWBY they're designed to hold 22 Nerf darts and can fire single shot or automatic. They are also completely 3D printable and the STL files can be found on my Thingiverse here along with the first generation.
DISCLAIMER: I don't have access to a 3D printer nor the money to order prints (part of the reason I want to win a printer with this contest) so this is mostly a theoretical build. I've had feedback on my MK I from some who printed and have used this to improve and modify the design. I would greatly appreciate feedback and suggestions to refine the design further. Due to its modularity there is minimal wastage when reprinting modified parts, something I see as a positive.
Step 1: Electronics
All of the electronics are run through an Arduino Nano.
The VIN can be used for the input power as the Nano can handle the 7.4V given by the LiPo battery. Both the image above and the code section should be used to ensure proper wiring, unfortunately the circuit diagram drawing tools I used didn't have a Nano so the wiring there is representative only and so should be wired with reference to the code, which has better notes.
The flywheels are driven by 2 drone BLDCs (a misnomer, they're more akin to high-speed ACs). It's designed with these motors in mind. (RCX Z R 1804 2400K Micro)
The flywheel motors are driven by these ESCs. (SimonK 30A ESC)
The ramrod motor is a geared torque motor from here. (DC 370 JSX-370)
The battery is a 7.4V LiPo available here. (7.4V 1300mAh 35C LiPo)
Other micro electronics are as follows:
Lever microswitch
TIP120 transistor
1N4004 diode
1K resistor
2 simple push buttons
Step 2: Printing
Parts available here.
All of the parts have been designed to be printed with minimal if any support material and there's no requirement for ABS or PLA in particular. The model has also been broken down into smaller parts to reduce waste, increase fixability and also allow smaller printers to print easily. The parts are all up on thingiverse at the link given in the description. They are assembled with M3 screws which bite into the plastic. 15mm M3's are suitable for most parts.
Cleanup will most likely be necessary. Clearance has been designed in where possible however depending on your printer settings some parts may need sanding or trimming. Ensure you check and test each moving part to make sure it runs smoothly.
Step 3: Code
This code is designed for the Arduino Nano but any small board would probably manage it just fine. The only limitation is the available space. I used a Nano because they're small and I had one on hand for testing.
The code is editable and if anyone with more experience wants to improve it for me I would be very grateful. The code is also derived from two sources, one for each of the circuits. The ESC link will help in calibrating your ESCs if necessary.
Attachments
Step 4: Assembly
The assembly should be decently straightforward, refer to the videos and just let me know if you need any help.
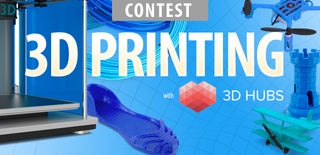
Runner Up in the
3D Printing Contest 2016
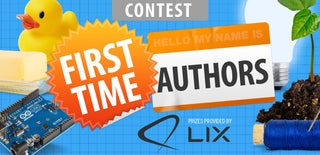
Participated in the
First Time Author Contest 2016