Introduction: 3D Printed Planetary Rover
So you are sitting in your geopod waiting for the methane storm to pass. You have done as much video rerun bingeing you can bear, Possibly suffering from a bad case of ‘pod fever”. Well cot potato you better throw that PLA popcorn bowl in the “Extrude-A-Spool 3000” and get ready to go outside without going outside. Were going to make a:
3D Printed FPV Planetary Rover.
In general rovers are complex machines containing thousands of parts, and your engineer is having a conversation with the potato plants and that chat won’t be over anytime soon. We are going to make it simple with as little parts as possible’ *warning if your planet or moon is above 170C do not attempt (melting may occur)
I am using a very cheap but capable printer. Nowadays you can now get them for the same price as a microwave oven so if you don’t have one..get one.
First things first. Here is a list of Items you will need
Materials:
4 Geared Motors
1 servo
1 R/C transmitter
1 R/C Receiver
2 R/C Car Speed Controller
1 Small Video Camera with wifi or FPV capabilities
1 Smart device or FPV Monitor
1 Bunch of screws and zip ties
lipo batteries to power rover
Equipment/Software
3D rendering software, I used Tinkercad(it's free)
3D printerMine is Anet A8
Digital Caliper
Screw driver
Soldering Iron
Scissors or nippers
Step 1: Step 1: Choosing the Motors
There is really no right or wrong with choosing a set of motors for your rover. Any geared motor should do the trick. The thing you should keep in mind is how big you want your rover to be, bigger motors means bigger rover and bigger batteries. Smaller motors means smaller rover and smaller batteries(cheaper). Larger rovers are good for tackling rough terrain whereas small rovers are inconspicuous. The motors I decided to use are small 16mm surplus 12v brushed gear motors because they are cheap tough and small and easier to use in a skid steer system.
Step 2: Step 2: Suspension/Chassis
I designed my suspension/chassis on Tinkercad.com I have no Cad training so I can tell you it is pretty straight forward and easy to learn. Firstly, I got out my digital caliper and took measurements of the motors so that I could design the motor carriers. Since the motor housing was a squared of circle and the gear housing was a circular shape. I designed the motor carrier to friction fit over the motor since it could be restricted from rotation by the nature of its shape. A cool and extremely useful tool in tinkered is the ability to turn any shape you make into a hole shape. I made the motors shape and then converted it to a hole and saved it so that anytime I wanted to make a motor carrier I just have to use the motor shape hole and group it with any solid shape I desire. I designed the suspension/chassis arms to be “C’ shaped with a motor on each end and a fulcrum point in the middle so they could pivot. I added 2 separate leaf arms on each so you can firm the suspension or loosen it by adding fasteners to them.
Step 3: Step 3: Body
I concocted several different body types for this rover, all of them will fit and are interchangeable. I designed a narrow body a light weight body and a Bucket/box body.
The one I chose to use for this instructable is the light body. I made a rectangular prism in the software then made a smaller version of the prism in hole form and added attachment points for the suspension chassis then cut away pieces until it looked good.
Step 4: Step 4 Camera/Servo/Roof
I made the camera carrier by tinkercadding a servo bracket from a customized saved part I made for a previous project. I then took this bracket and placed it on a the rover body in tinker cad and converted the body to a hole then grouped the parts so the servo bracket would naturally just clip on to the body.
I drilled some holes in the roof so I could attach my electronics(Speed controllers and radio receiver) with zip ties.
Step 5: Step 5 Wheels
I designed the wheels by making a square on the 3d rendering software, copying it and rotating it on itself several times. I then I copied the whole knurled cylinder shrunk it down and used it as a hole to hollow the wheel. I used some 12mm brass hex adapters to attach the wheels to the motor shaft but you could friction fit the wheels to the motor shafts or use a bolt to clamp it from the side like a grub nut.
Step 6: Step 6: Wiring
This step is pretty straight forward . I soldered the left side positive motor wires to a bullet connector and soldered the left side negative motor wires to another bullet connector to connect to the left speed controller out wires. I repeated this with the right side but make sure you reverse polarity to the motor out wires in order to keep the motors going in the same direction.
The speed controllers were soldered to a single power in Deans connector which is plugged into a 7.4v lipo battery and the speed controller then in turn powers the radio with it's servo wire.
The camera has its own lipo battery, which is zip tied to the top of the camera.
Step 7: Now We Are Ready to Rove
I dialed in my Liliput 5.8ghz monitor screen to my 5.8ghz fpv camera. flicked on all the switches and yes everything works. There are many ways to get First person view. You can attach a phone and Skype with separate Skype accounts between your rover and home base computer. You can put a WiFi action cam linked with a smart device. Or as I have done use a radio linked camera for FPV specifically.
Here is the design on Tinkercad
Time to open the airlocks and Rove the great unknown. Thanks for reading my Instructable Please vote for me I Rove you all. :)
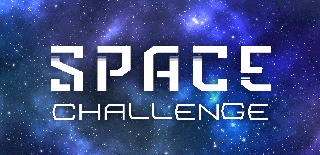
Participated in the
Space Challenge