Introduction: 3D Printed Record
In order to explore the current limits of 3D printing technology, I've created a technique for converting digital audio files into 3D-printable, 33rpm records and printed a few functional prototypes that play on ordinary record players. Though the audio quality is low -the records have a sampling rate of 11kHz (a quarter of typical mp3 audio) and 5-6 bit resolution (less than one thousandth of typical 16 bit resolution)- the songs are still easily recognizable, watch the video above to see the process and hear what the records sound like. Also check out my laser cut records, made on wood, paper, and acrylic.
This past year I've been posting a lot of audio projects, specifically, I've been experimenting with using relatively simple tools and techniques and very little memory to approximate and recreate digital audio signals. A great example is my Arduino Vocal Effects Box, where I used an Arduino to perform realtime pitch-bending on an incoming audio signal. Through these projects, I've learned that audio is a very resilient medium, it can take a fair amount of abuse (in the form of distortion and compression) while still maintaining most of the integrity of the original sound. The key is as long as you loosely approximate the overall shape of an audio signal, the output will sound reasonably recognizable. We have evolution to thank for this: as we hear audio, some complicated processing goes on in our brains that makes us very good at ignoring noise and focusing on the important pieces of information coming through. We can work off of relatively few cues (sometimes these even include contextual or visual cues) to piece together mangled or noisy audio and make sense of it; this is how we are able to focus on one voice in crowded room or decipher a message sent over a cheap walkie talkie.
This project was my first experiment extending this idea beyond electronics. I printed these records on a UV-cured resin printer called the Objet Connex500. Like most 3D printers, the Objet creates an object by depositing material layer by layer until the final form is achieved. This printer has incredibly high resolution: 600dpi in the x and y axes and 16 microns in the z axis, some of the highest resolution possible with 3D printing at the moment. Despite all its precision, the Objet is still at least an order of magnitude or two away from the resolution of a real vinyl record. When I first started this project, I wasn't sure that the resolution of the Objet would be enough to reproduce audio, but I hoped that I might produce something recognizable by approximating the groove shape as accurately as possible with the tools I had.
In this Instructable, I'll demonstrate how I developed a workflow that can convert any audio file, of virtually any format, into a 3D model of a record, and how I optimized these records for playback on a real turntable. The 3D modeling in this project was far too complex for traditional drafting-style CAD techniques, so I wrote an program to do this conversion automatically. It works by importing raw audio data, performing some calculations to generate the geometry of a record, and eventually exporting this geometry straight to a 3D printable file format. Most of the heavy lifting is done by Processing, an open source programming environment that's often used for 2D and 3D graphics and modeling applications. Here's a basic overview of my Processing algorithm:
use raw audio data to set the groove depth- parse through the raw audio data, this is the set of numbers that defines the shape of the audio waveform, and use this information to set the height of the bottom of a spiral groove. This way, when a turntable stylus moves along the groove it will move vertically in the same path as the original waveform and recreate the original audio signal.
draw record and groove geometry- A 3D model is essentially a list of triangles arranged in 3D space to create a continuous mesh, use the data from the last step and some general record parameters (record diameter, thickness, groove width, etc) to generate the list of triangular faces that describes the record's shape and the detailed spiral groove inscribed on its surface.
export model in STL format- the STL file format is understood by all 3D printers, export the geometry calculated in the last step as an STL file. To get Processing to export straight to STL, I used the ModelBuilder Library written by Marius Watz (if you are into Arduino/Processing and 3D printing I highly recommend checking this out, it works great).
I've uploaded some of my complete record models to the 123D gallery as well as the Pirate Bay. Check Step 6 for a complete listing of what's there and what I plan on posting. Alternatively, you can go to Step 7 to download my code and learn how to make printable record models from your own audio.
Special thanks to Randy Sarafan, Steve Delaire, Arthur Harsuvanakit, Phil Seaton, and Audrey Love for their help with this project.
Here's another video that gives a great overview of the printing process and shows the printers at work:
Step 1: How Does a Record Work?
The basic mechanism of a record player is very simple. The record moves at a constant rotational speed (usually 33.3 or 45 rpm) and a needle (also called a stylus) moves along a long spiral groove cut into the record's surface. As the record spins, the needle hits tiny bumps in the groove and vibrates to produce audio signals. I won't get into the specifics of how the needle extracts data from the record, but it is really interesting and there's a great demo of it here.
The record player and record cutter were invented by Edison in 1877. Due to a lack of precise machinery and technique at the time, the grooves on the first records were much larger than those on modern microgroove records and, subsequently, the audio signals were much noisier. This is a similar situation that I found myself in when starting this project: despite the high precision of the Objet machines, the resolution is nowhere near modern vinyl quality. Here and here are two examples of Edison's first phonograph tests. You can hear that the quality of recording of these tests is pretty close to what I've been able to 3d print; although I can't find the exact specs on these records, I'd imagine that the scale of the grooves was similar to what I was working with.
To give you an idea of the resolution of a modern record, check out the images above. Figs 1-3 are from Chris Supranowitz, a researcher at The Institute of Optics at the University of Rochester. These are close up images of a vinyl record, taken with an electron microscope. The dark objects in figs 1 and 2 are tiny particles of dust. Fig 3 is a bird's eye view of the record grooves, the darker regions are the top (uncut) surface of the record.
Fig 4 was made by branku62 at vinylengine.com, it shows the profile dimensions of a standard microgrove mono groove, this is what you would find on a modern mono 33 or 45 (stereo grooves are actually cut a bit smaller). In the diagram 1 mil = 1/1000", which is about 25um. Microgroove records require a stylus with a 0.7 to 1.0 mil radius tip, the tip makes contact with the groove at E in fig 1, a width of about 1.4 mil. The total depth of the groove is around 1.1 mil. These dimensions match up nicely with the dimensions of the electron microscope images.
Fig 5 is from Ron Geesin and Mark Berresford's website, it shows the groove depths of the older 78's. These records were much more coarse than microgroove records, both the needle and grooves were about 3x as large in every dimension. Fig 2 shows the groove depth for 78's was somewhere between 2.2 and 3.6 mil. The stylus radius was around 2.7 mil.
Step 2: Printer Specs
Here at Instructables HQ, we have access to Autodesk's fleet of Objet Connex 500 printers. These printers use UV light to cure resin layer by layer until a complete model is produced. They are very different from the fused deposition printers you may have seen or used before (MakerBot, RepRap, Up!, etc), not only can they print out of many types of materials (ranging from flexible rubbery material to hard polymer), but they are also extremely precise. In the x and y axes they have 600dpi resolution (that's about 42microns), and in the z axis they have a resolution of 16microns.
Before I started printing anything, I used these numbers to calculate the resolution I'd be able to achieve- so I could decide if this project was even worth pursuing any further. First I wanted to make sure that I would be able to get a good sampling rate on my audio. Sampling rate is the amount of samples per second in a song. Usually the sampling rate is 44.1kHz (or 44,100 samples a second). When the sampling rate drops below about 40kHz the higher frequencies of a song start losing their detail, but depending on the song you can go down to 10kHz sampling rate without too much of a problem.
To calculate the sampling rate of the 3D printed record I used the following relationship:
sampling frequency = (resolution per inch)*(inches per revolution)*(revolutions per second)
in order to maximize the sampling frequency, I want all of these numbers (res/inch, inch/rev, rev/sec) to be as high as possible
First I'll start with revolutions per second. Record players typically play at two different speeds: 33.3 and 45rpm. (Some record players also have a 78rpm speed, but this is less common and only used for very old records). I wanted to use the lower 33.3RPM speed in order to make this more like a real 12" record (45 RPM is only used for 7" records, and 33RPM for the full sized 12") and so that I could fit more audio onto each side of the disc.
revolutions per second = (revolutions per minute)/(seconds per minute)
revolutions per second at 33 rpm = 33.3/60 = 0.55
Next is inches per revolution, this number depends on the circumference of the disk where the needle is hitting it. The largest sized records are 12" in diameter (30cm). According to the RIAA standards, the outermost groove of a 12" record falls at a radius of 5.75" and the innermost groove falls at about 2.25". I'll use these numbers to determine the range of sampling rates I can achieve at 33RPM. The circumference (the distance in inches traveled by the needle during one revolution of the record) is calculated as follows:
inches per revolution = 2*pi*(radius of needle)
max inches per revolution = 2*pi*5.75 =~ 36
min inches per revolution = 2*pi*2.35 =~ 15
I already know that the resolution per inch of the 3D printer is 600 (600 dpi in the x and y axes). So combining this all I get:
sampling frequency = (resolution per inch)*(inches per revolution)*(revolutions per second)
max sampling frequency at 33 rpm = 600*36*0.55 =~ 12000 = 12kHz
min sampling frequency at 33 rpm = 600*15*0.55 =~ 4900 = 4.9kHz
This is a pretty good starting point. If I scale this to 45rpm instead of 33 the sampling rate becomes:
max sampling frequency at 45 rpm = 600*36*0.75 =~ 16000 = 16kHz
min sampling frequency at 45 rpm = 600*15*0.75 =~ 6700 = 6.7kHz
I'll keep this option in mind in case sampling rate becomes an issue. The other piece of information that I needed was the bit depth I'd be able to achieve with the Objet printer. Bit depth is the resolution of the audio data. Most audio these days in 16 bit, meaning each sample can have one of 65536 (2^16) possible values. 8 bit audio has only 256 (2^8) steps of resolution and still sounds pretty close to the original. Even going down to 3 and 4 bit sounds recognizable. (I should note here that the music commonly referred to as "8-bit" like the music in early Nintendo games is actually 1 bit resolution, it's called 8 bit because it was first made with 8 bit computers, not with 8 bit resolution).
Since the z axis is the most precise axis on the Objet printer, I wanted to print my record so that the needle vibrates vertically in the groove to trace out the audio wave to maximize my bit depth. The following equation calculates the vertical distance that the needle will move as it traces the a wave of a given bit depth:
vertical displacement of needle = (2^bit depth)*(precision of z axis)
where the precision of the z axis is 16micron. I used this to calculate the following table:
bit depth vertical displacement steps of resolution
2 64um 4
3 128um 8
4 256um 16
5 512um 32
6 1.024mm 64
7 2.048mm 128
8 4.096mm 256
The bolded rows in the table are the numbers that I wanted to shoot for with this project. A vertical amplitude of 64-512um is an order of magnitude (~10x) larger than the amplitude of a vinyl record groove, but I felt like I'd probably be able to get away with it and still maintain a reasonable bit depth.
Step 3: First Tests
First I prepared some test files to print to get an idea of what is possible with the printer and optimize the dimensions of the grooves. These record files have circular grooves on them containing sine waves of various frequencies, amplitudes, groove depths, groove widths, and beveled groove edges. (When I say that the groove "contained" a sine wave, I mean the bottom of the groves moves up and down in a sinusoidal pattern around the record). I generated all of these files in Processing using the ModelBuilder library to export straight to STL.
TEST ONE:
My first test record had 72 grooves on it, screen shots of the model are shown in figs 2 through 6 I tested two frequencies of sine waves:
1000 cycles per revolution = 555Hz at 33RPM
500 cycles per revolution = 277Hz at 33RPM
I tested a few different amplitudes, depths, and groove widths for these frequencies and gave each groove a constant bevel size of 2px on each side (you can see in fig 5 how the edges of the groove flare outward). I printed the record in Objet's Vero Clear material, this material is a fairly hard, clear resin. I printed the file with the "smooth" setting to prevent any support material from being deposited in the grooves. Unfortunately, when I was ready to make this print we were having some problems with power in our shop, so I had to use another Objet machine that was not set up for high resolution printing; the best I could do was 300DPI X/Y resolution with 30um Z steps. This is half the resolution that each of these axes is capable of, meaning the print came out at (1/2)3, or 1/8th resolution overall. The results are shown in the video below (the grooves were not deep enough to keep the needle inside, so I had to hold in it place with my hand). The record was also a little big for my record player, I decreased the diameter of my STL file to 11.8" in later versions.
In this video you can hear a periodic frequency sweep on top of the steady sine wave (best heard w headphones). This sweeping sound is caused by the needle moving over the thousands of tiny parallel bumps in the print caused by adjacent print-heads on the Objet machine. This noise is unavoidable, but increasing the strength of the signal will help to make it less noticeable.
The Processing sketch that generated this record is given below:
<pre>//sine tests //by Amanda Ghassaei //Dec 2012 //https://www.instructables.com/id/3D-Printed-Record/ /* * This program is free software; you can redistribute it and/or modify * it under the terms of the GNU General Public License as published by * the Free Software Foundation; either version 3 of the License, or * (at your option) any later version. */ import processing.opengl.*; import unlekker.util.*; import unlekker.modelbuilder.*; import ec.util.*; UVertexList recordPerimeterUpper,recordPerimeterLower,recordHoleUpper,recordHoleLower;//storage for perimeter and center hole of record UVertexList lastEdge;//storage for conecting one groove to the next UGeometry geo;//storage for stl geometry //variables float theta;//angle variable float thetaIter = 10000;//how many values of theta per cycle float radius;//variable to calculate radius of grooves int diameter = 12;//diameter of record in inches float innerHole = 0.286;//diameter of center hole in inches float innerRad = 2.35;//radius of innermost groove in inches float outerRad = 5.75;//radius of outermost groove in inches float grooveSpacing = 20;//pixel spacing of grooves float bevel = 2;//pixel width of groove bevel //record parameters float recordHeight = 0.08;//height of record in inches int recordBottom = 0;//height of bottom of record //parameters to test float amplitude[] = {2,4,8};//in units of 16 micron steps (remember this is the amplitude of the sine wave, the total vert displacement will be twice this) int frequency[] = {1000,500,0};//cycles per rotation float depth[] = {0.5,1,0};//how many 16 microns steps below the surface of the record to print the uppermost point of the groove float grooveWidth[] = {1,2,3};//in 600dpi pixels float incrNum = TWO_PI/thetaIter;//calculcate inrementation amount int grooveNum = 0;//variable for keeping track of how long this will take void setup() {//everything that executes in this sketch is contained in the setup() geo = new UGeometry();//place to store geometery of verticies setUpVariables();//convert units, initialize etc setUpRecordShape();//draw basic shape of record drawGrooves();//draw in grooves geo.writeSTL(this, "test.stl");//write stl file from geomtery } void setUpVariables(){ //convert everything to inches float micronsPerInch = 25400;//scalingfactor float dpi = 600; byte micronsPerLayer = 16;//microns per vertical print layer grooveSpacing /= dpi; bevel /= dpi; for(byte i=0;i<3;i++){ amplitude[i] = amplitude[i]*micronsPerLayer/micronsPerInch; depth[i] = depth[i]*micronsPerLayer/micronsPerInch; grooveWidth[i] /= dpi; } } void setUpRecordShape(){ //set up storage recordPerimeterUpper = new UVertexList(); recordPerimeterLower = new UVertexList(); recordHoleUpper = new UVertexList(); recordHoleLower = new UVertexList(); //get verticies for(theta=0;theta<TWO_PI;theta+=incrNum){ //outer edge of record float perimeterX = diameter/2+diameter/2*cos(theta); float perimeterY = diameter/2+diameter/2*sin(theta); recordPerimeterUpper.add(perimeterX,perimeterY,recordHeight); recordPerimeterLower.add(perimeterX,perimeterY,recordBottom); //center hole float centerHoleX = diameter/2+innerHole/2*cos(theta); float centerHoleY = diameter/2+innerHole/2*sin(theta); recordHoleUpper.add(centerHoleX,centerHoleY,recordHeight); recordHoleLower.add(centerHoleX,centerHoleY,recordBottom); } //close vertex lists (closed loops) recordPerimeterUpper.close(); recordPerimeterLower.close(); recordHoleUpper.close(); recordHoleLower.close(); //connect verticies geo.quadStrip(recordHoleUpper,recordHoleLower); geo.quadStrip(recordHoleLower,recordPerimeterLower); geo.quadStrip(recordPerimeterLower,recordPerimeterUpper); //to start, outer edge of record is the last egde we need to connect to with the outmost groove lastEdge = new UVertexList(); lastEdge.add(recordPerimeterUpper); println("record drawn, starting grooves"); grooveNum = 0;//variable for keeping track of how much longer this will take } void drawGrooves(){ UVertexList grooveOuterUpper,grooveOuterLower,grooveInnerUpper,grooveInnerLower;//groove verticies //set up storage grooveOuterUpper = new UVertexList(); grooveOuterLower = new UVertexList(); grooveInnerUpper = new UVertexList(); grooveInnerLower = new UVertexList(); //DRAW GROOVES radius = outerRad;//outermost radius (at 5.75") to start for(byte frequencyIndex=0;frequencyIndex<2;frequencyIndex++){ for(byte amplitudeIndex=0;amplitudeIndex<3;amplitudeIndex++){ for(byte grooveDepthIndex=0;grooveDepthIndex<2;grooveDepthIndex++){ for(byte grooveWidthIndex=0;grooveWidthIndex<3;grooveWidthIndex++){ for(byte copies=0;copies<2;copies++){ //clear lists grooveOuterUpper.reset(); grooveOuterLower.reset(); grooveInnerUpper.reset(); grooveInnerLower.reset(); for(theta=0;theta<TWO_PI;theta+=incrNum){//for theta between 0 and 2pi float sineTheta = sin(theta); float cosineTheta = cos(theta); //calculate height of groove float grooveHeight = recordHeight-depth[grooveDepthIndex]-amplitude[amplitudeIndex]+amplitude[amplitudeIndex]*sin(theta*frequency[frequencyIndex]); grooveOuterUpper.add((diameter/2+(radius+bevel)*cosineTheta),(diameter/2+(radius+bevel)*sineTheta),recordHeight); grooveOuterLower.add((diameter/2+radius*cosineTheta),(diameter/2+radius*sineTheta),grooveHeight); grooveInnerLower.add((diameter/2+(radius-grooveWidth[grooveWidthIndex])*cosineTheta),(diameter/2+(radius-grooveWidth[grooveWidthIndex])*sineTheta),grooveHeight); grooveInnerUpper.add((diameter/2+(radius-grooveWidth[grooveWidthIndex]-bevel)*cosineTheta),(diameter/2+(radius-grooveWidth[grooveWidthIndex]-bevel)*sineTheta),recordHeight); } //close vertex lists (closed loops) grooveOuterUpper.close(); grooveOuterLower.close(); grooveInnerUpper.close(); grooveInnerLower.close(); //connect verticies geo.quadStrip(lastEdge,grooveOuterUpper); geo.quadStrip(grooveOuterUpper,grooveOuterLower); geo.quadStrip(grooveOuterLower,grooveInnerLower); geo.quadStrip(grooveInnerLower,grooveInnerUpper); //set new last edge lastEdge.reset();//clear old data lastEdge.add(grooveInnerUpper); radius -= grooveSpacing+grooveWidth[grooveWidthIndex];//set next radius //tell me how much longer grooveNum++; print(grooveNum); println(" of 72 grooves drawn"); } radius -= 2*grooveSpacing;//extra spacing } radius -= 2*grooveSpacing;//extra spacing } radius -= 2*grooveSpacing;//extra spacing } radius -= 2*grooveSpacing;//extra spacing } geo.quadStrip(lastEdge,recordHoleUpper);//close remaining space between last groove and center hole }
TEST TWO:
In my next test I made a record with 108 grooves, still sine waves, but this time I made the grooves deeper, increase the bevel of each groove to equal half the amplitude of the sine wave, and tried out three different frequencies: 555hz, 277hz, and 139hz (1000, 500, and 250 cycles per revolution at 33.3rpm). I also tested different amplitudes (4, 8 and 16 steps), groove depths (2, and 3 steps below the top of the record), and groove widths (1, 2 and 3 pixels). Since our shop came back online, I switched printers and started printing with Objet's Vero White material, which is similar to Vero Clear in texture, but (as you might image) is a translucent white color. This time I was finally able to print with the full 16 micron and 600 dpi resolution of the printer. Here is a video of the results:
TEST THREE:
In my third test I increased the resolution of my stl file to test out some higher frequency sine waves. I used 22000 points per revolution to draw out the sine waves (as opposed to 10000 in my previous tests), this puts me at about the max resolution I can get with 600dpi (calculated in the last step). I tested three frequencies: 1110hz, 832hz, and 694hz (2000, 1500, and 1250 cycles per revolution at 33.3rpm). I also tested different amplitudes (12 and 16 steps) and groove widths (2 and 3 px). Here is the video:
RESULTS:
At the end of all these tests I learned a few things about 3d printing records with the Objet:
Groove Depth min of 48um below top of record - I found that grooves that kept the waveform at a minimum of 48um (or 3 16 micron steps) below the top of the record kept the needle in place while being played. This was true for all the frequencies I tested.
Groove Width 2px - At lower frequencies I found that the 2px grooves were much less noisy than the 1px, but I didn't hear too much of a difference between 2 and 3px. However, when I tested again with the higher frequencies (2000 cycles/rev) I could hear much more noise on the 3px groove than the 2px.
Frequency Range - at 22000 points per revolution, I easily achieved the upper limit of the human vocal range (about 1.1kHz). Theoretically I should be able to reproduce frequencies equal to half my sampling rate. With a sampling rate of 12kHz (calculated in the last step), the highest frequency I can theoretically achieve is 6kHz. I suspect that the movement of the liquid resin during the curing process will prevent me from actually achieving these frequencies, but if I can just get into the 2kHz range it will still sound reasonably good. Based on the tests I've run so far, I think this is possible.
Dimensions - Although it seems like a 12" record should measure 12" in diameter, I found that printing at 12" made the record slightly too large for my record player. I decreased the diameter down to 11.8" and it worked great.
Max file size of ~300MB - Although Processing is capable of producing much larger files, the Objet Software that runs the printers seems to only handle about 300MB of data at a time. It's possible that increased RAM might bring this up to 500mb, but this still does not give me a lot of room to work with. Although this is plenty for normal CAD purposes, I found out that I would have to be very efficient with the way I packed data onto the STL for the final version of my Processing sketch. One problem with my current sketch is that is has a constant angular sampling rate, this means that the same amount of data is used to describe a groove on the outer edge of the record and a groove near the center of the record. Since the groove at the center of the record is much smaller it would a higher resolution than the outer groove, unfortunately, this extra precision goes to waste because the printer has constant DPI across the entire surface of the record. Eventually, I hope to decrease the angular sampling rate of the inner grooves to save storage space and pack as much audio into the STL file as possible.
Attachments
Step 4: Extracting Audio Data With Python
<pre>#Wav to Txt #by Amanda Ghassaei #https://www.instructables.com/member/amandaghassaei/ ## * This program is free software; you can redistribute it and/or modify ## * it under the terms of the GNU General Public License as published by ## * the Free Software Foundation; either version 3 of the License, or ## * (at your option) any later version. #this code unpacks and repacks data from: #16 bit stereo wav file at 44100hz sampling rate #and saves it as a txt file import wave import math import struct bitDepth = 8#target bitDepth frate = 44100#target frame rate fileName = "audio.wav"#file to be imported (change this) #read file and get data w = wave.open(fileName, 'r') numframes = w.getnframes() frame = w.readframes(numframes)#w.getnframes() frameInt = map(ord, list(frame))#turn into array #separate left and right channels and merge bytes frameOneChannel = [0]*numframes#initialize list of one channel of wave for i in range(numframes): frameOneChannel[i] = frameInt[4*i+1]*2**8+frameInt[4*i]#separate channels and store one channel in new list if frameOneChannel[i] > 2**15: frameOneChannel[i] = (frameOneChannel[i]-2**16) elif frameOneChannel[i] == 2**15: frameOneChannel[i] = 0 else: frameOneChannel[i] = frameOneChannel[i] #convert to string audioStr = '' for i in range(numframes): audioStr += str(frameOneChannel[i]) audioStr += ","#separate elements with comma fileName = fileName[:-3]#remove .wav extension text_file = open(fileName+"txt", "w") text_file.write("%s"%audioStr) text_file.close()
Once I create a text file, I can import the data into Processing and convert it into an STL. I would like to streamline my code so that audio files (wav/mp3) can be loaded directly into Processing, but I have not found a solution yet, any suggestions would be appreciated!
Step 5: Initial Audio Tests (featuring the Pixies)
In the first test I used the same parameters that I'd had luck with in the sine wave tests:
amplitude: 16 x 16 micron z axis steps
groove width: 2px
groove depth: 3 x 16 micron z axis steps
sampling rate: 11,025hz (one quarter of normal mp3 sampling rate)
groove spacing: 20 pixels (at 600 dpi)
My processing code is below. The code is heavily commented, but here's the overall gist:
An audio file is basically a list of numbers that plot a waveform over time. The data that I pulled from Python in the last step is just that, the list of data points in the audio file. Essentially what I did in this Processing sketch was use this data to set the depth of a long, spiral groove on the record's surface. Later when the needle passes over this groove, its tip will follow this path and actually trace out the original waveform stored in the audio data.
<pre>//txt to stl conversion - 3d printable record //by Amanda Ghassaei //Dec 2012 //https://www.instructables.com/id/3D-Printed-Record/ /* * This program is free software; you can redistribute it and/or modify * it under the terms of the GNU General Public License as published by * the Free Software Foundation; either version 3 of the License, or * (at your option) any later version. */ import processing.opengl.*; import unlekker.util.*; import unlekker.modelbuilder.*; import ec.util.*; String filename = "debaser.txt"; UVertexList recordPerimeterUpper,recordPerimeterLower,recordHoleUpper,recordHoleLower;//storage for perimeter and center hole of record UVertexList lastEdge;//storage for conecting one groove to the next UGeometry geo;//storage for stl geometry //parameters float samplingRate = 44100;//(44.1hz audio) float rpm = 33.3;//rev per min float secPerMin = 60;//seconds per minute float rateDivisor = 4;//how much we are downsampling by float theta;//angle variable float thetaIter = (samplingRate*secPerMin)/(rateDivisor*rpm);//how many values of theta per cycle float radius;//variable to calculate radius of grooves float diameter = 11.8;//diameter of record in inches float innerHole = 0.286;//diameter of center hole in inches float innerRad = 2.35;//radius of innermost groove in inches float outerRad = 5.75;//radius of outermost groove in inches float grooveSpacing = 20;//pixel spacing of grooves //record parameters float recordHeight = 0.04;//height of record in inches int recordBottom = 0;//height of bottom of record //variable parameters float amplitude = 24;//amplitude of signal (in 16 micron steps) float bevel = 0.5;//bevelled groove edge float grooveWidth = 3;//in 600dpi pixels float depth = 6;//measured in 16 microns steps, depth of tops of wave in groove from uppermost surface of record float incrNum = TWO_PI/thetaIter;//calculcate angular incrementation amount int grooveNum = 0;//variable for keeping track of how long this will take int totalSampleNum; void setup(){ geo = new UGeometry();//place to store geometery of verticies setUpVariables();//convert units, initialize etc setUpRecordShape();//draw basic shape of record drawGrooves(processAudioData());//draw in grooves geo.writeSTL(this, filename + ".stl");//write stl file from geomtery exit(); } float[] processAudioData(){ //get data out of txt file String rawData[] = loadStrings(filename); String rawDataString = rawData[0]; float audioData[] = float(split(rawDataString,','));//separated by commas //normalize audio data to given bitdepth //first find max val float maxval = 0; for(int i=0;i<audioData.length;i++){ if (abs(audioData[i])>maxval){ maxval = abs(audioData[i]); } } //normalize amplitude to max val for(int i=0;i<audioData.length;i++){ audioData[i]*=amplitude/maxval; } return audioData; } void setUpVariables(){ //convert everything to inches float micronsPerInch = 25400;//scalingfactor float dpi = 600; byte micronsPerLayer = 16;//microns per vertical print layer grooveSpacing /= dpi; amplitude = amplitude*micronsPerLayer/micronsPerInch; depth = depth*micronsPerLayer/micronsPerInch; grooveWidth /= dpi; } void setUpRecordShape(){ //set up storage recordPerimeterUpper = new UVertexList(); recordPerimeterLower = new UVertexList(); recordHoleUpper = new UVertexList(); recordHoleLower = new UVertexList(); //get verticies for(theta=0;theta<TWO_PI;theta+=incrNum){ //outer edge of record float perimeterX = diameter/2+diameter/2*cos(theta); float perimeterY = diameter/2+diameter/2*sin(theta); recordPerimeterUpper.add(perimeterX,perimeterY,recordHeight); recordPerimeterLower.add(perimeterX,perimeterY,recordBottom); //center hole float centerHoleX = diameter/2+innerHole/2*cos(theta); float centerHoleY = diameter/2+innerHole/2*sin(theta); recordHoleUpper.add(centerHoleX,centerHoleY,recordHeight); recordHoleLower.add(centerHoleX,centerHoleY,recordBottom); } //close vertex lists (closed loops) recordPerimeterUpper.close(); recordPerimeterLower.close(); recordHoleUpper.close(); recordHoleLower.close(); //connect verticies geo.quadStrip(recordHoleUpper,recordHoleLower); geo.quadStrip(recordHoleLower,recordPerimeterLower); geo.quadStrip(recordPerimeterLower,recordPerimeterUpper); //to start, outer edge of record is the last egde we need to connect to with the outmost groove lastEdge = new UVertexList(); lastEdge.add(recordPerimeterUpper); println("record drawn, starting grooves"); grooveNum = 0;//variable for keeping track of how much longer this will take } void drawGrooves(float[] audioData){ UVertexList grooveOuterUpper,grooveOuterLower,grooveInnerUpper,grooveInnerLower;//groove verticies UVertexList stop1,stop2;//storage for very beginning and end of sprial groove //set up storage grooveOuterUpper = new UVertexList(); grooveOuterLower = new UVertexList(); grooveInnerUpper = new UVertexList(); grooveInnerLower = new UVertexList(); stop1 = new UVertexList(); stop2 = new UVertexList(); //DRAW GROOVES radius = outerRad;//outermost radius (at 5.75") to start float radIncr = (grooveSpacing+grooveWidth)/thetaIter;//calculate radial incrementtion amount int samplenum = 0; int totalgroovenum = int(audioData.length/(rateDivisor*thetaIter)); //first draw starting cap theta = 0; float sineTheta = sin(theta); float cosineTheta = cos(theta); //calculate height of groove float grooveHeight = recordHeight-depth-amplitude+audioData[int(rateDivisor*samplenum)]; stop1.add((diameter/2+(radius+amplitude*bevel)*cosineTheta),(diameter/2+(radius+amplitude*bevel)*sineTheta),recordHeight);//outerupper stop2.add((diameter/2+radius*cosineTheta),(diameter/2+radius*sineTheta),grooveHeight);//outerlower stop2.add((diameter/2+(radius-grooveWidth)*cosineTheta),(diameter/2+(radius-grooveWidth)*sineTheta),grooveHeight);//innerlower stop1.add((diameter/2+(radius-grooveWidth-amplitude*bevel)*cosineTheta),(diameter/2+(radius-grooveWidth-amplitude*bevel)*sineTheta),recordHeight);//innerupper //draw triangles geo.quadStrip(stop1,stop2); //then spiral groove while (radius>innerRad && rateDivisor*samplenum<(audioData.length-rateDivisor*thetaIter+1)){//while we still have audio to write and we have not reached the innermost groove //clear lists grooveOuterUpper.reset(); grooveOuterLower.reset(); grooveInnerUpper.reset(); grooveInnerLower.reset(); for(theta=0;theta<TWO_PI;theta+=incrNum){//for theta between 0 and 2pi sineTheta = sin(theta); cosineTheta = cos(theta); //calculate height of groove grooveHeight = recordHeight-depth-amplitude+audioData[int(rateDivisor*samplenum)]; samplenum++;//increment sample num grooveOuterUpper.add((diameter/2+(radius+amplitude*bevel)*cosineTheta),(diameter/2+(radius+amplitude*bevel)*sineTheta),recordHeight); grooveOuterLower.add((diameter/2+radius*cosineTheta),(diameter/2+radius*sineTheta),grooveHeight); grooveInnerLower.add((diameter/2+(radius-grooveWidth)*cosineTheta),(diameter/2+(radius-grooveWidth)*sineTheta),grooveHeight); grooveInnerUpper.add((diameter/2+(radius-grooveWidth-amplitude*bevel)*cosineTheta),(diameter/2+(radius-grooveWidth-amplitude*bevel)*sineTheta),recordHeight); radius -= radIncr; } //add last value to grooves to complete one full rev theta = 0; sineTheta = sin(theta); cosineTheta = cos(theta); //calculate height of groove grooveHeight = recordHeight-depth-amplitude+audioData[int(rateDivisor*samplenum)]; grooveOuterUpper.add((diameter/2+(radius+amplitude*bevel)*cosineTheta),(diameter/2+(radius+amplitude*bevel)*sineTheta),recordHeight); grooveOuterLower.add((diameter/2+radius*cosineTheta),(diameter/2+radius*sineTheta),grooveHeight); grooveInnerLower.add((diameter/2+(radius-grooveWidth)*cosineTheta),(diameter/2+(radius-grooveWidth)*sineTheta),grooveHeight); grooveInnerUpper.add((diameter/2+(radius-grooveWidth-amplitude*bevel)*cosineTheta),(diameter/2+(radius-grooveWidth-amplitude*bevel)*sineTheta),recordHeight); //connect verticies geo.quadStrip(lastEdge,grooveOuterUpper); geo.quadStrip(grooveOuterUpper,grooveOuterLower); geo.quadStrip(grooveOuterLower,grooveInnerLower); geo.quadStrip(grooveInnerLower,grooveInnerUpper); //set new last edge lastEdge.reset();//clear old data lastEdge.add(grooveInnerUpper); //complete beginning cap if necessary if (grooveNum==1){ //clear stop2 stop2.reset(); stop2.add(diameter/2+diameter/2*cosineTheta,diameter/2+diameter/2*sineTheta,recordHeight);//outer perimeter[0] stop2.add((diameter/2+(radius+amplitude*bevel)*cosineTheta),(diameter/2+(radius+amplitude*bevel)*sineTheta),recordHeight);//outer groove edge [2pi] //draw triangles geo.quadStrip(stop1,stop2); } //tell me how much longer grooveNum++; print(grooveNum); print(" of "); print(totalgroovenum); println(" grooves drawn"); } //draw end cap of spiral groove stop1.reset(); stop2.reset(); stop1.add((diameter/2+(radius+amplitude*bevel)*cosineTheta),(diameter/2+(radius+amplitude*bevel)*sineTheta),recordHeight);//outeruppter stop2.add((diameter/2+radius*cosineTheta),(diameter/2+radius*sineTheta),grooveHeight);//outerlower stop2.add((diameter/2+(radius-grooveWidth)*cosineTheta),(diameter/2+(radius-grooveWidth)*sineTheta),grooveHeight);//innerlower stop1.add((diameter/2+(radius-grooveWidth-amplitude*bevel)*cosineTheta),(diameter/2+(radius-grooveWidth-amplitude*bevel)*sineTheta),recordHeight);//innerupper //draw triangles geo.quadStrip(stop1,stop2); stop2.reset(); stop2.add(grooveInnerUpper.first());//innerupper[0] stop2.add(diameter/2+innerHole/2*cosineTheta,diameter/2+innerHole/2*sineTheta,recordHeight);//innerhole[0] //draw triangles geo.quadStrip(stop1,stop2); geo.quadStrip(lastEdge,recordHoleUpper);//close remaining space between last groove and center hole }
and here is the result:
Success! You can clearly hear The Pixies coming through, but the signal to noise ratio is not great. In my next test I amplified the original audio signal a little bit before sending it to my Processing sketch. This way some of the louder drum sections would get slightly clipped and allow the overall amplitude of the normalized signal to get a little larger. Here's what that sounds like:
Signal to noise is getting better, I added a little more audio to this file so that you can start to hear Frank Black's vocals coming in. Next I increased the amplitude of the signal to see if I could get a better signal out. In my sine tests I thought that an amplitude of 16 was plenty loud, but not so large that it caused excessive distortion in the signal. Since the Pixies signal is not always spanning the full amplitude allowed by my program I increased the amplitude of the algorithm (most of the time the waveform is hovering around half of its peak amplitude, only the drums are able to kick the signal up to full amplitude). This may cause some extra distortion on the drum beats, but since drums are already pretty noisy I was ok with that. Here's the result of amplitude 32:
Signal to noise is better, but there is quite a bit of distortion. I decreased the amplitude to 24 next:
This sounds a lot better. Good signal to noise without too much distortion. Next I made a slight edit to my code to minimize the amount of data packed into the stl file. In the previous examples I created some space between grooves, basically a flat surface parallel to the top of the record. In the code below I removed this space and used the last upper edge of the previous groove as the upper edge of the next groove. The difference in the model is shown in fig 2.
<pre>//txt to stl conversion - 3d printable record //by Amanda Ghassaei //Dec 2012 //https://www.instructables.com/id/3D-Printed-Record/ /* * This program is free software; you can redistribute it and/or modify * it under the terms of the GNU General Public License as published by * the Free Software Foundation; either version 3 of the License, or * (at your option) any later version. */ import processing.opengl.*; import unlekker.util.*; import unlekker.modelbuilder.*; import ec.util.*; String filename = "bluemonday.txt"; UVertexList recordPerimeterUpper,recordPerimeterLower,recordHoleUpper,recordHoleLower;//storage for perimeter and center hole of record UVertexList lastEdge;//storage for conecting one groove to the next UGeometry geo;//storage for stl geometry //parameters float samplingRate = 44100;//(44.1khz audio) float rpm = 33.3;//rev per min float secPerMin = 60;//seconds per minute float rateDivisor = 4;//how much we are downsampling by float theta;//angle variable float thetaIter = (samplingRate*secPerMin)/(rateDivisor*rpm);//how many values of theta per cycle float radius;//variable to calculate radius of grooves float diameter = 11.8;//diameter of record in inches float innerHole = 0.286;//diameter of center hole in inches float innerRad = 2.35;//radius of innermost groove in inches float outerRad = 5.75;//radius of outermost groove in inches //record parameters float recordHeight = 0.04;//height of record in inches int recordBottom = 0;//height of bottom of record //variable parameters float amplitude = 24;//amplitude of signal (in 16 micron steps) float bevel = 0.5;//bevelled groove edge float grooveWidth = 2;//in 600dpi pixels float depth = 6;//measured in 16 microns steps, depth of tops of wave in groove from uppermost surface of record float incrNum = TWO_PI/thetaIter;//calculcate angular incrementation amount int grooveNum = 0;//variable for keeping track of how long this will take int totalSampleNum; void setup(){ geo = new UGeometry();//place to store geometery of verticies setUpVariables();//convert units, initialize etc setUpRecordShape();//draw basic shape of record drawGrooves(processAudioData());//draw in grooves geo.writeSTL(this, filename + ".stl");//write stl file from geomtery exit(); } float[] processAudioData(){ //get data out of txt file String rawData[] = loadStrings(filename); String rawDataString = rawData[0]; float audioData[] = float(split(rawDataString,','));//separated by commas //normalize audio data to given bitdepth //first find max val float maxval = 0; for(int i=0;i<audioData.length;i++){ if (abs(audioData[i])>maxval){ maxval = abs(audioData[i]); } } //normalize amplitude to max val for(int i=0;i<audioData.length;i++){ audioData[i]*=amplitude/maxval; } return audioData; } void setUpVariables(){ //convert everything to inches float micronsPerInch = 25400;//scalingfactor float dpi = 600; byte micronsPerLayer = 16;//microns per vertical print layer amplitude = amplitude*micronsPerLayer/micronsPerInch; depth = depth*micronsPerLayer/micronsPerInch; grooveWidth /= dpi; } void setUpRecordShape(){ //set up storage recordPerimeterUpper = new UVertexList(); recordPerimeterLower = new UVertexList(); recordHoleUpper = new UVertexList(); recordHoleLower = new UVertexList(); //get verticies for(theta=0;theta<TWO_PI;theta+=incrNum){ //outer edge of record float perimeterX = diameter/2+diameter/2*cos(theta); float perimeterY = diameter/2+diameter/2*sin(theta); recordPerimeterUpper.add(perimeterX,perimeterY,recordHeight); recordPerimeterLower.add(perimeterX,perimeterY,recordBottom); //center hole float centerHoleX = diameter/2+innerHole/2*cos(theta); float centerHoleY = diameter/2+innerHole/2*sin(theta); recordHoleUpper.add(centerHoleX,centerHoleY,recordHeight); recordHoleLower.add(centerHoleX,centerHoleY,recordBottom); } //close vertex lists (closed loops) recordPerimeterUpper.close(); recordPerimeterLower.close(); recordHoleUpper.close(); recordHoleLower.close(); //connect verticies geo.quadStrip(recordHoleUpper,recordHoleLower); geo.quadStrip(recordHoleLower,recordPerimeterLower); geo.quadStrip(recordPerimeterLower,recordPerimeterUpper); //to start, outer edge of record is the last egde we need to connect to with the outmost groove lastEdge = new UVertexList(); lastEdge.add(recordPerimeterUpper); println("record drawn, starting grooves"); grooveNum = 0;//variable for keeping track of how much longer this will take } void drawGrooves(float[] audioData){ UVertexList grooveOuterUpper,grooveOuterLower,grooveInnerUpper,grooveInnerLower;//groove verticies UVertexList stop1,stop2;//storage for very beginning and end of sprial groove //set up storage grooveOuterUpper = new UVertexList(); grooveOuterLower = new UVertexList(); grooveInnerUpper = new UVertexList(); grooveInnerLower = new UVertexList(); stop1 = new UVertexList(); stop2 = new UVertexList(); //DRAW GROOVES radius = outerRad;//outermost radius (at 5.75") to start float radIncr = (grooveWidth+2*bevel*amplitude)/thetaIter;//calculate radial incrementation amount int samplenum = 0; int totalgroovenum = int(audioData.length/(rateDivisor*thetaIter)); //first draw starting cap theta = 0; float sineTheta = sin(theta); float cosineTheta = cos(theta); //calculate height of groove float grooveHeight = recordHeight-depth-amplitude+audioData[int(rateDivisor*samplenum)]; stop1.add((diameter/2+(radius+amplitude*bevel)*cosineTheta),(diameter/2+(radius+amplitude*bevel)*sineTheta),recordHeight);//outerupper stop2.add((diameter/2+radius*cosineTheta),(diameter/2+radius*sineTheta),grooveHeight);//outerlower stop2.add((diameter/2+(radius-grooveWidth)*cosineTheta),(diameter/2+(radius-grooveWidth)*sineTheta),grooveHeight);//innerlower stop1.add((diameter/2+(radius-grooveWidth-amplitude*bevel)*cosineTheta),(diameter/2+(radius-grooveWidth-amplitude*bevel)*sineTheta),recordHeight);//innerupper //draw triangles geo.quadStrip(stop1,stop2); //then spiral groove while (radius>innerRad && rateDivisor*samplenum<(audioData.length-rateDivisor*thetaIter+1)){//while we still have audio to write and we have not reached the innermost groove //clear lists grooveOuterUpper.reset(); grooveOuterLower.reset(); grooveInnerUpper.reset(); grooveInnerLower.reset(); for(theta=0;theta<TWO_PI;theta+=incrNum){//for theta between 0 and 2pi sineTheta = sin(theta); cosineTheta = cos(theta); //calculate height of groove grooveHeight = recordHeight-depth-amplitude+audioData[int(rateDivisor*samplenum)]; samplenum++;//increment sample num if (grooveNum==0){ grooveOuterUpper.add((diameter/2+(radius+amplitude*bevel)*cosineTheta),(diameter/2+(radius+amplitude*bevel)*sineTheta),recordHeight); } grooveOuterLower.add((diameter/2+radius*cosineTheta),(diameter/2+radius*sineTheta),grooveHeight); grooveInnerLower.add((diameter/2+(radius-grooveWidth)*cosineTheta),(diameter/2+(radius-grooveWidth)*sineTheta),grooveHeight); grooveInnerUpper.add((diameter/2+(radius-grooveWidth-amplitude*bevel)*cosineTheta),(diameter/2+(radius-grooveWidth-amplitude*bevel)*sineTheta),recordHeight); radius -= radIncr; } //add last value to grooves to complete one full rev theta = 0; sineTheta = sin(theta); cosineTheta = cos(theta); //calculate height of groove grooveHeight = recordHeight-depth-amplitude+audioData[int(rateDivisor*samplenum)]; if (grooveNum==0){ grooveOuterUpper.add(grooveInnerUpper.first());//grooveOuterUpper.add((diameter/2+(radius+amplitude*bevel)*cosineTheta),(diameter/2+(radius+amplitude*bevel)*sineTheta),recordHeight); } grooveOuterLower.add((diameter/2+radius*cosineTheta),(diameter/2+radius*sineTheta),grooveHeight); grooveInnerLower.add((diameter/2+(radius-grooveWidth)*cosineTheta),(diameter/2+(radius-grooveWidth)*sineTheta),grooveHeight); grooveInnerUpper.add((diameter/2+(radius-grooveWidth-amplitude*bevel)*cosineTheta),(diameter/2+(radius-grooveWidth-amplitude*bevel)*sineTheta),recordHeight); //connect verticies if (grooveNum==0){//if joining a roove to the edge of the record geo.quadStrip(lastEdge,grooveOuterUpper); geo.quadStrip(grooveOuterUpper,grooveOuterLower); } else{//if joining a groove to another groove geo.quadStrip(lastEdge,grooveOuterLower); } geo.quadStrip(grooveOuterLower,grooveInnerLower); geo.quadStrip(grooveInnerLower,grooveInnerUpper); //set new last edge lastEdge.reset();//clear old data lastEdge.add(grooveInnerUpper); //complete beginning cap if necessary if (grooveNum==0){ //clear stop2 stop2.reset(); stop2.add(diameter/2+diameter/2*cosineTheta,diameter/2+diameter/2*sineTheta,recordHeight);//outer perimeter[0] stop2.add((diameter/2+(radius+amplitude*bevel)*cosineTheta),(diameter/2+(radius+amplitude*bevel)*sineTheta),recordHeight);//outer groove edge [2pi] //draw triangles geo.quadStrip(stop1,stop2); } //tell me how much longer grooveNum++; print(grooveNum); print(" of "); print(totalgroovenum); println(" grooves drawn"); } //draw end cap of spiral groove stop1.reset(); stop2.reset(); stop1.add((diameter/2+(radius+amplitude*bevel)*cosineTheta),(diameter/2+(radius+amplitude*bevel)*sineTheta),recordHeight);//outeruppter stop2.add((diameter/2+radius*cosineTheta),(diameter/2+radius*sineTheta),grooveHeight);//outerlower stop2.add((diameter/2+(radius-grooveWidth)*cosineTheta),(diameter/2+(radius-grooveWidth)*sineTheta),grooveHeight);//innerlower stop1.add((diameter/2+(radius-grooveWidth-amplitude*bevel)*cosineTheta),(diameter/2+(radius-grooveWidth-amplitude*bevel)*sineTheta),recordHeight);//innerupper //draw triangles geo.quadStrip(stop1,stop2); stop2.reset(); stop2.add(lastEdge.last());//innerupper[0] stop2.add(diameter/2+innerHole/2*cosineTheta,diameter/2+innerHole/2*sineTheta,recordHeight);//innerhole[0] //draw triangles geo.quadStrip(stop1,stop2); geo.quadStrip(lastEdge,recordHoleUpper);//close remaining space between last groove and center hole }
And here's what it sounds like:
I was really happy with the way this came out, this is the code I used moving forward.
Step 6: Records
After nearly a week of printing, frantically running around downtown SF, and generally fighting with technology, I've got some reasonably good sounding audio to share with you:
You'll notice that all of these prints are only about a minute long- this was due to some issues I was having with file size and RAM. I'm currently working on troubleshooting these problems, but at the moment the largest file I can print out is about 250MB, or a little over a minute of audio. Each size has the potential to fit about 6 minutes of audio, this amounts to a file containing about 1.5GB of data.
Some of these files are up on The Pirate Bay and the 123D gallery for anyone to download. (Pirate Bay recently introduced new section on their site for sharing 3d designs called Physibles, many of the models are ready for 3D printing or other forms of digital fabrication). Unfortunately, some of my files were so large that I had to down-sample even farther, to 9kHz, to get them to export before my computer crashed. I'm still not done generating all the files I would like to make, it takes a bit of time to process and handle such large amounts of data, so things are moving along relatively slowly. Check back for updates, and if you download any of these, please seed them!
Pink Floyd - Dark Side of the Moon (4 discs, 7 sides) Supposedly, there is a factory in germany that does nothing but press copies of dark side of the moon, maybe one day 3d printers will put that factory out of business, but for now I've had to split the album up onto seven sides of four discs to even get it to fit...
New Order - Blue Monday Single(1 disc, 2 sides)The top selling 12" single of all time. Side a is Blue Monday in its nearly 8 minute entirety, I had to cheat a little and extend the grooves into the space where the label should go to pull this off, but it's not too bad, and side b is a remix of Blue Monday called The Beach, just like the original release.
White Stripes - Fell in Love with a Girl(1 disc, 1 side) This is song is not even 2 min long, so I exported it at slightly higher res- 45rpm with a 16kHz sampling rate. Now that our 3D printing facility has an upgraded computer, I'd like to print out a bunch of short songs like this at 45rpm.
I made all these files at half the thickness of a regular record. That way, if you ever find a way to print them, you can glue two of them together to make a double sided record.
Step 7: Make Your Own Records
You can convert your own audio files into 3D STL models in ten easy steps:
1. Download Processing.
2. Download the ModelBuilder library for Processing. I used version 0007a03.
3. Unzip the Modelbuilder library .zip and copy the folder inside called "modelbuilder". Unzip the processing .zip and go to Processing>modes>java>libraries and paste the "modelbuilder" folder in the "libraries" folder.
4. Download Python 2.5.4.
5. Download Audacity.
6. Download the code from GitHub (you can download the files as a zip by clicking on the cloud button). Open the folder called Processing3DPrintedRecord.
7. Open an audio file of your choice with Audacity. Use Effect>Amplify to amplify the signal as much as you can without noticeable effects of clipping (you will be able to get away with some clipping, and remember this is not crystal clear audio anyway). Make sure there is 2 sec of blank audio at the end of the track so that nothing gets clipped. Keep the audio under 6 min. File>Export this file and save it in the "Processing3DPrintedRecord" folder as a wav file.
8. Open the Python file called "wavtotxt". Copy the file name of the file you just saved in the line:
fileName = "your_file_name_here.wav"
Hit Run>RunModule, after a minute or two you will have a .txt file saved in the Processing3DPrintedRecord folder.
9. Open the Processing Sketch. In File>Preferences check the box that says "increase the maximum available memory to" and write in the amount of available ram on your computer. I've found that my laptop with 4GB RAM can handle audio files up to 1.5 min long. For longer files you will need to use a computer with 12-16GB of RAM. If Processing starts and then gets stuck or crashes, it is a RAM issue and you will need to move to a machine with more RAM.
10. Change the name of the import file in the Processing sketch to your txt file name:
String filename = "your_file_name_here.txt";
Close all other programs running on your computer and run the Processing sketch Sketch>Run. After a few seconds you will see "record drawn, starting grooves" appear at the bottom of the Processing window. After some more time you will get updates on the status of the sketch: "3 of 85 grooves drawn". Eventually Processing will tell you that it is writing your STL file and when it is done it will say "Closing 'name_of_your_file.stl' and tell you haw many faces are in the file. You can find the finished file in the Processing3DPrintedRecord folder.
Once you've made them, post them! I've been posting mine on the 123D gallery and the Pirate Bay. Enjoy, and let me know if you have questions or need help getting this to work. I've tested this process in both Windows (64 bit) and Mac OS, though I'd imagine it will work for Linux as well.
Attachments
Step 8: Future Work
We're currently trying to upgrade our computer setup so that we will be able to print out files larger than 250MB. Eventually I'd like to actually print physical copies of some of the files that I posted in the last step. I'm also interested in hearing how the resolution difference between the outer and inner grooves of the record (explained in step 2) manifest themselves in the audio output.
Soon I'd also like to experiment with some more creative applications of this technology. For example, printing out a record with many adjacent closed loops of ~2second looping samples. This way you could set your needle down in one groove and listen to a loop repeat over and over, then tap the needle to the side to switch to another loop. Assuming all the the loops have a similar time signature, you could turn this record into a cool, interactive sample mixer.
I'm currently working on another project that takes audio data and outputs a vector cutting path in the shape of a record (pictured above). I'm planning on cutting this record with a laser cutter on acrylic. Unfortunately, we've been having some trouble with our lasers recently, but I hope to get the project up in the first few weeks of January, as I have most of the code done. I'm excited about this project because it has the potential to be a lot more useful to ordinary(ish) people. The vector files are much easier and faster to generate, and the whole process uses cheaper materials and tools that a decent amount of people have access to these days. I still haven't done enough testing to say how it will compare to my 3D printed record, but I'm fairly confident it will work.
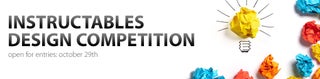
Participated in the
Instructables Design Competition