Introduction: 3D Printed Van De Graaff Generator
This is an update of a project I did about 10 years ago, before I had a 3D printer. The original project is detailed here. It used rollers made from PVC pipe that turned on skate wheel bearings, and was driven by an AC motor. This new design uses a 3D printed base and rollers, spinning on bearings harvested from hard disk drives, and is driven by a small DC motor. Though the motor turns at about the same speed, it runs quieter and charges faster because it uses a wider belt. The new design makes belt replacement easier.
It uses a pair of steel, Blanda salad bowls from Ikea for the top electrode. Their 11" (280 mm) diameter means the generator can charge up to 400 kV under good conditions (low humidity air), and throw thick, blue, painful sparks about 300 mm long every few seconds.
Here it is in operation, on a damp, rainy evening, in slo-mo:
And not so slo-mo:
When you are handling the parts and assembling them, be sure your hands are clean or wear gloves. Clean the pipe inside and out with warm water and dish detergent and rinse thoroughly and dry it. A little contamination in the wrong place can reduce the output of your generator.
How does it work?
VDGs operate on the principle of triboelectricity. When objects made of dissimilar materials are brought into contact, a weak chemical bond is formed through sharing of electrons. When the objects are separated, one of them ends up with more electrons than the other and the two objects are said to be charged. In this machine, the rubber belt picks up electrons from the aluminum and transports them to the metal sphere at the top of the machine. At the other end, the Teflon pulls electrons from the belt and sends it back down the column, positively charged, to the brush at the bottom of the machine.
Moving electrons, whether they are moving in a wire or being physically transported on a rubber belt, constitute an electrical current. The sphere at the top of the column forms a capacitor with the Earth. The moving charge accumulates on the sphere, charging that capacitor (opposite charges are moving in the ground at the same time they are moving in the machine). As the charge on the sphere accumulates, the voltage (by definition, the physical separation of charges) rises. The faster the belt moves, the higher the current. The wider the belt is, the more room is has to carry charge, so the higher the current.
Air can support a limited electric field before it ionizes and becomes an electrical conductor. That electric field limit depends on the temperature and humidity of the air. More humid air breaks down at lower electric field strength. Dry air can withstand higher fields/voltage before the air ionizes.
The diameter of the sphere and the charge it accumulates determines the voltage on and electric field intensity around the sphere. As charge accumulates on the sphere, it spreads out over its surface. The electric field will be most intense at sharp points (such as the sharp edge where we cut a hole in the bowl, hence the plastic tubing to insulate that sharp edge), so the air will tend to ionize at a point at a lower voltage than it will at a large smooth surface. The larger and smoother the surface, the lower the electric field intensity, so it is ultimately the diameter of the sphere that determines how high the voltage can get on the sphere before the surrounding air ionizes and leaks away the charge. At some voltage, the charge leaking off into the air will equal the charge coming up the column and the voltage between the sphere and ground will stabilize... until you get near it and provide a path for a rapid discharge of the capacitor.
Note: you may see some minor differences between the parts in the CAD file and the photos. After the photos were made I made some minor changes to the design to make assembly easier and to improve operation.
Let's get started...
Step 1: Shopping
You will need:
1) 0.7 - 1m of 4" schedule 40 PVC pipe, ends cut square (use a miter saw or a table saw)
2) Mabuchi RZ-46BWA-2642 car seat adjuster motor available for about $10 via ebay or ali-express
3) Metal tape (any metal) or aluminum foil and glue
4) 3x bearings of the type in the photo, above, harvested from old HDDs
5) 1x exercise band, about 1-1.5 m long, at least 75 mm wide
6) a handful of #6 plastic thread rolling screws (wood screws will work, too)
7) 3-4 m of wire for brushes and ground
8) 2x 11" Blanda salad bowls from Ikea.
10) 400 mm of plastic aquarium air tubing or other flexible plastic or rubber hose.
11) 1x 6-12V DC power supply (a wall wart will usually be fine).
12) 500 g of your favorite 3D printer filament
Step 2: Cut One Bowl
You're going to be cutting a hole in one bowl so it fits over the pipe, with a piece of plastic tubing installed on its edge. Mark the bottom of one bowl with a circle, using the pipe as a stencil. Put on your safety glasses and using the circle as a guide, use a fiber reinforced cut-off wheel on a rotary tool to cut a slightly over-sized hole. Smooth the sharp edge with a grindstone on the rotary tool.
Slit a piece of plastic tubing lengthwise and fit it over edge of the hole you just cut and make sure it fits tightly over the pipe. The bowl should not fall down. If it does, don't worry, you can just glue a couple plastic stops to the pipe that the bowl can rest on.
The purpose of the plastic tube is to limit corona discharge from the sharp edge of the hole.
Step 3: Prepare the Belt
You need to turn the exercise band into a loop. The loop should be about 10% shorter than the PVC pipe. It's almost impossible to get glue to stick these things together, especially when it is stretched as part of its normal operation, so the easiest and most reliable way to join the ends of the belt is to stitch it with sewing thread.
If you stitch it straight across, every time the joint passes over a roller it will make a thump sound. If you stitch it at an angle, the whole joint doesn't hit the roller at once so the sound is much quieter. The easiest way to get the angle is to fold the belt and clamp it in the folded position as shown in the photo. Then you just do a continuous suture along the folded edge and tie it off. You may be able to do a neater job with a sewing machine.
The final step is to cut off the triangular flaps on the top and bottom side of belt.
Step 4: Print the Parts
The bearing fit part is used to make sure the holes in the rollers will be the right size to fit the bearings you have. The bearing should fit tightly into the hole and the flange should come out flush with the surface of the print. If it doesn't, tweak the hole size slightly and try again. Once you have found the size that works for your printer and filament, tweak the hole size in the rollers the same way.
Print the rollers, one of each type. Use random seam position and turn on support material generation in the slicer. I used 15% infill, 3 perimeters, 3 top and bottom layers. You'll have to rotate them when you bring them into the slicer. Note: the rollers are "crowned" which means they bulge a little at the center. That is intentional and keeps the belt centered on them when the generator is operating.
Now print the pipe fit test part. It should fit easily over the pipe, but not excessively easily. When you have the right sizes for the inner and outer diameters, apply the same tweaks, if any, to the base and top roller holders.
Print the base using the same settings as the rollers, but increase infill to about 20-25%.
Print 3 of the legs, with support material turned on, 100% infill, and use internal and external brims about 3-4 mm wide. You're going to have to rotate them when you bring them into the slicer.
Step 5: Prepare the Top Roller
Fit the bearings into the ends of the roller- they should fit very tightly. Press them into the holes by setting the stud end of the bearing into a hole in a block of wood, then place the pulley onto the end of the bearing and push down until it stops.
You can use the top roller without a layer of teflon tape, but output will be greatly reduced. I recommend you wrap one or two layers of teflon tape over the surface of the roller. It will make a big difference! You can have all sorts of fun experimenting with other materials...
Step 6: Prepare the Bottom Roller
The motor I ordered came with a brass worm gear on the shaft. After a couple failed attempts to press it off the shaft, I resorted to cutting it off using the cut off wheel on the rotary tool.
Check the fit of the motor shaft in the hole in the end of the bottom roller. If it's too tight, open it up a little with a drill- either 4 mm or 5/32". If it fits loosely, insert two #6 thread rolling screws into the holes and turn them to where they almost lock the shaft in place.
Insert the end bearing. Now fit the assembly into the base and adjust the position of the roller on the motor's shaft so that everything fits together properly and tighten the screws in the roller to lock it in position on the shaft. Take it back out of the base and cover the roller with one layer of metal tape. You can go right over the screw holes.
Step 7: Prepare the Top Brush
Place the bottom bowl with the hole over one end of the pipe. Now put the top roller holder in place without the roller.
The top brush mounts on two screws in the top roller holder. All you do is strip about 300 mm of wire and wrap it around the two screws, then tape the loose end to the inside surface of the bowl.
There are a bunch of ways to make the brush, but the easiest is to just fold a piece of the metal tape used to cover the bottom roller over the wire. Then use a pair of scissors to snip it in many places along the length of the wire. The idea is to produce a bunch of sharp little points that will produce a strong corona effect to charge the belt.
Note: the brush should not touch the belt when the generator is operating. Leave a few mm of air between the brush tips and the roller/belt.
Step 8: Prepare the Bottom Brush
Screw the legs to the base.
Make the bottom brush just like the top brush. Also, note that the brush does not touch the belt or roller.
You want to keep a long wire (3-4 m) to connect the brush to an earth ground- either a water pipe or the center screw on an electrical outlet will work fine.
Step 9: Finish Assembly
Put the belt through the big hole in the base, then fit it over the roller and position the roller and motor and screw the motor down.
Now turn the pipe upside down and place the base over the end of the pipe with the belt hanging down inside the pipe. Lift it up and reach into the pipe and pull the belt through, stretching it over the top roller and then set the roller into position. It should now all be held together by the tension on the belt. Straighten the belt out so there are no folds or wrinkles on either of the rollers. Look down into the pipe and make sure there are no twists in the belt. Rotate the pipe so the two rollers are parallel, then use the three side holes in the base as guides and drill pilot holes in the pipe and drive three screws into the pipe to hold the base in place.
Connect the ground wire to a water pipe or the center screw on an electric outlet, and connect the motor to a battery or power supply and turn it on. The motor should start and the belt should rotate freely, and should center itself on both rollers. You'll probably be able to draw a spark from the bowl with your finger. That means everything is working fine.
Now tape the top bowl to the bottom bowl to close the sphere. Use packing tape or duct tape, not metal tape.
Step 10: Have Some Fun!
This machine should produce long, painful sparks with an evil "snap!" every few seconds. If you put a plastic bag from the grocery store over the sphere, you'll get much longer sparks that will blast right through the plastic.
You can have all sorts of fun making people's hair stand up (stand them on a stool and put their hand on the sphere while the motor runs), making bits of paper, foam, yarn, and soap bubbles levitate, etc. Do a web search for "electrostatic motor" and see what you find.
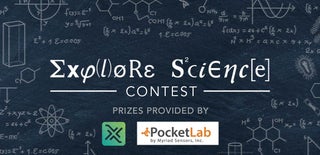
Participated in the
Explore Science Contest 2017