Introduction: 3D Printer Bed Upgrade/Replacement
Update: This was written a few years ago, before I figured out how to make a proper kinematic mount. While this works and is a big improvement over the original bed, a kinematic version of this is better. See: https://drmrehorst.blogspot.com/2019/01/son-of-megamax-gets-new-y-axis.html
Now back to the original post:
The glass bed on a Taz 3 printer at the Milwaukee Makerspace did what glass likes to do - it broke after someone printed on it with glue applied directly to the glass. I wasn't there when it happened so I don't know if the cooling, shrinking print caused it to break or if the print was stuck hard and someone broke the bed trying to get it loose. Either way, it was up to me to fix it.
I wasn't very happy with the bed on that printer, anyway. It had two main problems- first it was glass, and second it used 4 point "leveling". It was hard to get prints to stick to it and we couldn't use very much of the bed's area.
What's wrong with glass? Besides its remarkable ability to break when removing prints or dropping tools or filament spools on it, it is a thermal insulator. In this particular printer, the heater was glued directly to the glass without any sort of heat spreader. Look at the thermal image- you can see >30C variation in temperature over the surface of the glass. How are you going to get prints to reliably stick to that?
What's wrong with 4 point "leveling"? A printer's bed is supposed to be a flat plane. If it isn't flat, the first layer will vary in thickness and will refuse to stick in some places. That can't be good! In some odd corner of the universe, maybe inside a black hole, it may take 4 points to define a plane, but in our galaxy, high school geometry teaches that 3 points define a plane. So why do so many printers have 4 corner leveling screws? Because the bed has four corners and the "designer" didn't think about it. Doh! Using 4 corner screws causes the bed and undercarriage plates to bend. You don't end up with a very flat surface and if it isn't flat, how can it be level?
Combine the uneven heating with the unflat surface and it's a wonder prints can be made to stick at all. I decided to fix both problems. The fix can be applied to any 3D printer with a less than perfect bed (most of them). Fixing these two problems allows printing over the entire bed surface because it is easy to get prints to stick when you have a flat, level, evenly heated surface.
Step 1: Materials
Here's what you'll need, give or take a few items
- a new bed plate- cast aluminum
- high temperature silicone adhesive
- 3X Teflon or phenolic blocks
- 3X #10-32 flat head screws
- 6X #6 sheet metal or plastic thread rolling screws
- 3X stiff springs that fit over the #10 screws
- a saw, a drill, a ruler and handy but not essential- drill press, milling machine, band saw, countersink bit, 10-32 tap
I like to use aluminum bed plates. They are thermally conductive so they heat up evenly, and they don't break, ever. Also, unlike glass, you can easily drill holes in aluminum. But you can't use just any old aluminum. Aluminum plate is normally extruded and/or rolled, and will always have a curve. That won't work. You have to get the right stuff. I'm talking about "cast aluminum tooling plate", sometimes called "cast aluminum jig plate". Sold under brand names like "MIC6" or "ALCA 5", you can get it from online metals dealers such as Speedy Metals, Metals Supermarket, and from dozens of Ebay dealers. The thing that makes this stuff so good for 3D printer bed plates is that it comes milled flat on both sides. I used a piece of 12" x 12" x 1/4" ALCA 5 that I picked up at my local Speedy Metals for $40. If you happen to live in the Minneapolis or Milwaukee areas, you can buy cast aluminum tooling plate from Howard Precision Metals for scrap price ($2.50 per lb). My latest printer project uses a 300 x 300 x 8 mm bed plate that cost just $15 at HPM.
I reused the printer's original undercarriage which saved a lot of time and effort because I didn't have to lay out and drill all those holes for mounting the bearings. I did cut away about 50% of the original material to reduce the weight, which brings up an important point. 1/4" cast aluminum plate weighs about 2X as much as the original glass. When you increase the moving mass you may have to change your printer's acceleration settings, depending on the motor torque. More on that later...
The high temperature silicone is used to attach the heater to the new bed plate. You can get this stuff from any auto parts store for about $5 a tube. Look for high temperature silicone gasket/adhesive. If you buy a new heater that has adhesive on it you won't need this stuff at all, just peel and stick.
I used Teflon blocks to support the new bed. Teflon has no problems with the temperature of the bed plate and is very easy to cut and drill. You can find small pieces of Teflon (aka PTFE) at local plastics shops or via ebay. Phenolic should be OK at these temperatures too. You can use any material that's heat resistant and easy to cut and drill. Please don't use wood, MDF, printed PLA, or even printed ABS. You need stable, thermally insulating material for this job. It shouldn't cost more than $5 for a piece of Teflon that you can cut up to make the supports.
I used #10-32 bed leveling screws because they are pretty sturdy and the threads will allow fine adjustment of the bed level. You can use any screws you have handy, but flat heads are optimal because you can countersink the holes in the bed plate and keep the head flush with the top of the plate so there's nothing to bang into your extruder. It is best to tap the holes in the Teflon blocks, but if you don't have a tap it's OK- just drill a hole that's a little smaller than the screw and drive the screw in- it will roll its own threads.
The Teflon blocks are screwed to the undercarriage using #6 plastic thread rolling screws. You can use almost any screws for this job, including wood screws. Drill undersized pilot holes and drive the screws in. It will be OK. Don't worry about the teflon "creeping". I've used this same arrangement on the print bed in my printer for over 2 years without anything creeping.
You want very stiff springs to push the bed plate up against the leveling screw heads. No, the springs are not there to protect your extruder in the event of a head crash! If they were soft enough for that, the plate would bounce every time it reverses direction and that will be bad for print quality. There is no protecting the extruder from a head crash, so as they say in NYC (or is it Jersey?), fageddaboudit.
Step 2: Make a CAD Model
I started this project the way I start so many these days- with a CAD model of the undercarriage plate and some measurements from the printer. I use DesignSpark Mechanical because it is very easy to learn and use and produces high quality STL files (that don't require "repair") for 3D printing.
I wanted to use three leveling screws and they had to attach to the undercarriage via a thermal insulator that would grip the screws tightly and not let the bed plate wobble when it reverses direction. I had to measure the available clearances and plan out where to put the leveling screws and their support blocks, and where to drill the holes in the new bed plate.
When you lay out the leveling screws, two of them should line up along one axis of the printer (X or Y, it doesn't matter) at one edge of the bed plate. The third screw goes into the opposite edge of the bed plate. The first two adjust the pitch in their axis (X in this case) and the third screw adjusts the roll. When you adjust the roll screw it has no effect on the pitch which makes leveling the bed quick and easy. This printer seems to hold the level setting quite well and since initial setup over a month ago, hasn't needed any adjustment.
Attachments
Step 3: Cut the Teflon Blocks
I used 1/2" thick Teflon and cut three identical blocks from it. I notched the blocks so they'd "hang ten" over the edge of the undercarriage plate to save a few mm of vertical space, but it isn't entirely necessary. I drilled and tapped holes for the 10-32 leveling screws and just drilled pilot holes for the mounting screws. Each block is solidly attached to the undercarriage plate by two #6 plastic thread rolling screws.
Dimensions of the blocks aren't critical and will depend on the machine you're working on. You can use simple rectangular blocks of any sensible size with equally sensible spacing between the screws. In this case, the blocks are 15 mm deep where the leveling screw holes are drilled, and about 12 mm deep where the mounting screws go. That provides for a very rigid assembly. Make sure your leveling screws go all the way through the block to maximize rigidity. You might be able to get away with smaller dimensions to preserve more of your vertical build capacity. When you're finished, the bed plate and undercarriage should move as a single piece with no wobble at all.
Step 4: Prepare the Undercarriage and Install It
Once I had everything worked out in the CAD model I transferred the cutting lines and hole locations to the undercarriage plate then cut it and drilled it. I started with marking the center line through the existing screw holes and measured everything from there. I cut the plate on a band saw but you can use a jig saw or even a hack saw to make straight cuts in aluminum. The edges can be cleaned up with a bit of sandpaper or a file. Easy-peasy lemon-squeezy!
I screwed down the Teflon leveling screw support blocks, remounted the bearings and checked for smooth motion. It was a little wobbly, so I shimmed a couple of the bearing blocks using strips of aluminum cut from a soda can to smooth things out without allowing any wobble. Once the motion was smooth, I reattached the belt.
Step 5: Prepare the Bed Plate
I drilled oversized holes so the leveling screws are free to pivot a little when making leveling adjustments then countersunk them so that the screw heads would be below the surface level of the bed so the extruder couldn't crash into them. It is critical that you drill the holes in the bed plate at locations that correspond to the holes in the teflon blocks attached to the undercarriage. Measure twice, drill once!
Next I cemented the heater to the plate. I just squeezed out some of the silicone onto the plate, smeared it around a bit then carefully laid the heater down on it and piled some weight on top and let it sit overnight.
If your heater doesn't get hot enough, and you're going to replace it, you want to find a heater that is rated for about 0.4 W/cm^2 or more. Any less than that and it will take a long time to reach print temperatures if it gets there at all. The heaters that come attached to aluminum heat spreaders aren't usually powerful enough or flat enough to print on without adding glass. Printed circuit board type heaters are usually not going to do the job either. Silicone heaters are usually available in adequate power densities. You can find plenty of them on amazon.com, ebay, aliexpress, etc., for reasonable prices. Be sure your printer's power supply can handle the extra load- if not, you'll need a higher current power supply- and that the MOSFET on the controller board can switch the extra current or you may need to use an SSR to switch power to your new heater. You can use line powered heaters but you have to be pretty careful with the wiring to keep things safe.
If you replace the heater you may have to tweak the thermistor settings in your firmware to match the thermistor in the new heater.
Step 6: Install the Bed Plate
Put the leveling screws through their holes in the bed plate (don't forget the springs!) and screw them into the Teflon blocks. Screw them down pretty far so the springs are well compressed and providing a lot of upward force on the bed plate. You want the bed pushed firmly against the screw heads so it can't bounce when the bed changes direction.
This mod reduced the vertical printing capacity by about 10 mm, so I had to print an extension for the zero adjust screw that would allow the bed to be zeroed at its new height. I just printed a small cylinder with a small hole so the zero adjust screw could thread into it. I could have used a longer screw, but couldn't find one at the Makerspace so I printed the extension. Your printer may need some other treatment depending on how the zero switch is set up.
Don't forget to reconnect the heater and thermistor wires!
If you have struggled to level your printer's bed with 4 screws, you're going to love 3 point leveling. Just heat up the bed and extruder, adjust the two screws at the front of the bed to catch paper between the bed and nozzle, then move the nozzle back and adjust the screw at the back of the bed to do the same. Move the nozzle to the center of the bed and adjust the zeroing screw and you're ready to print.
For the final step I put a layer of PET tape on the bed. ABS and PLA will stick to clean PET and Kapton without any additional glue or other slop. Keep your grubby fingers and greasy tools off the bed surface and clean it frequently with acetone while the bed is cool, and you'll have no trouble with prints letting go before they finish.
When you change the bed plate and/or the heater, if you're using PID temperature control, be sure to run the PID auto tune function to optimize the temperature control. See http://reprap.org/wiki/PID_Tuning for instructions. If you don't run the auto tune and save the PID values, it may take longer for your new bed to heat up and temperature regulation might not be very good. This bed conversion added a lot of mass which takes longer to heat up, so now it takes about 9 minutes to get to 105C for printing ABS.
Does it work? Compare the thermal image above to the one on the first page. Of course it works!
For this printer I did not have to make any adjustments (other than PID auto tune), but as I mentioned earlier, the extra moving mass may require tweaking the configuration of your printer, specifically the acceleration settings. After installing your new, massive bed plate, try a few test prints with a lot of small details that cause the bed to jerk back and forth a lot. If the layers start shifting, turn down the acceleration. This is mainly going to be a problem in printers with the bed moving in the Y axis. More sensible printer designs with the bed moving in the Z axis shouldn't have any problems at all.
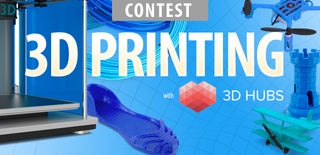
Participated in the
3D Printing Contest 2016