Introduction: 3D Printer Enclosure / Maker Space
Here's a video describing my enclosure and all the designs and prints that went into it... Watch this first so you can get an idea of the overall concept, design and features before I go into a step-by-step Instructable on how to build it. (Sorry in advance, but I kinda get off track in the video with other designs and my overall maker space, but everything you need to know about the enclosure is in this video.) ENJOY!
OVERVIEW:
I built this enclosure so that I could have complete climate control around my printers... It is well known that PLA, PVA, and other filament do not like moisture and/or humidity very much - so I wanted to have low humidity in my enclosure where my filament is stored at all times...
Also, it is kinda well known that ABS and Nylon, when they print - can be toxic... ABS is known to be carcinogenic and Nylon is not so well known, but nevertheless true, to release freakin CYANIDE!!! if heated too much (I know, crazy, right?) - so I wanted to create as perfect of a seal as I could in the enclosure and used a fan, blowing out through a duct, to create negative pressure and blow all those pesky micro-particles out the window and not into my living room - where I live and breath...
By adding a heater, fan and dehumidifier I now have complete control over the environment around my printers - which is an amazing thing to have and will lead to a lot better and more consistent printing at the end of the day - especially with tricky, heat sensitive filaments like ABS... It really does help with warping issues and also helps keep my heated beds warm -they also warm up quicker...
With the seal all around, this thing is pretty much sound proof, I can barely hear the printers while sitting right next to them... This is very nice, especially if your printers are in a living room like mine are... I can watch TV with the printers running and not need to hear them...
Lastly, I wanted to have all of my filament arranged in a way so that I can quickly change filaments without having to move anything around... So I have the filament sitting above the printers. Each one is fed through the platform and all the ends are resting above the printers in holders so when I unload one filament, I can just reach up and put the next one in as easy as possible... I designed the guides in such a way that even the furthest left filament can be fed into and print on the printer that's all the way on the right, and visa versa - every filament can fit into either printer.
COST, PARTS AND LABOR:
All said and done, this enclosure should cost around $300-400 to build...
The biggest expense, by far, is the acrylic - which will easily be $100-150 alone.
Lumber will cost roughly $80-100...
Paint, LEDs, fan, heater and other various things will run about another $100-150...
But if you spend a few thousand dollars on your printers, why not spend an extra few hundred to make an awesome enclosure for them to print more effectively in? It's totally worth it...
A lot of this enclosure is 3D printed...
I wanted to make a point to 3D print as many of the parts in the enclosure as I could, so there are about 100 individual 3D printed parts in the entire enclosure - including but not limited to - 20 spool holders, filament cleaners, guides, and hooks... 2 large mounting brackets and tube extenders... 2 detailed shelves, fan cover, duct, vent, and other various things I designed, printed and used... Overall, it will easily take over 200 hours to print everything needed - especially if you use the spool holders which take about 5 hours to print - each. So printing will be a large part of this project - if you want to build this - be prepared for that... Overall, this should take about 40 hours to build, minus the printing...
HOW I'M GOING TO SET-UP THIS INSTRUCTABLE TO BE USED:
Due to the fact that not everyone has the same printers as I do, I know that very few of you will need to build the same exact enclosure I did. So I did not bother including the exact dimensions or detailed blueprints of my enclosure, instead, this will be a step-by-step instruction on how I built my enclosure - in general. You can use it as a guide or take ideas from it to add to your enclosure, but your dimensions will most likely be different than mine - however, the overall concept will remain the same... So feel free to do what you want with this...
3D PRINTED PARTS AND COMPONENTS:
Here is my Thingiverse page ( http://www.thingiverse.com/jjpowelly/about ) this is where I have all of my designs, I will also post specific ones when they come up during the steps. You should reference this since it goes into greater detail on how to make the smaller compenents of the enclosure such as filament guides, bracket extenders, etc...
Also, I forgot to mention / emphasize in the video that 100% of my designs and prints that I made and that you see in the video print with a single extruder, without supports, and without a raft... I have gotten very good at designing things FOR printing... Everything I design, print, and upload prints very easily- if it doesn't - you tell me and I'll fix it... I want all my designs to be perfect and easy to print for everybody, on every printer... I take a lot of pride in my ability to engineer/design things that way, and all my designs are built directly around and with these constraints in mind - I will never design and upload something that I have not, first, made sure was perfect in every aspect for successful printing.
I'm an engineer/designer that is currently studying Computer Science at Columbia... I give a large portion of my designs and ideas out for free to be used within the open source community... I don't ask for much in return, but it is nice to get some positive feedback / suggestions from people who appreciate and use my work every now and then... So if you like this or have any ideas for me, any feedback would be greatly appreciated... I always want to make my designs better and will take positive input from anyone willing to give it to me.
Here is a link to this enclosure's specific Thingiverse page:
http://www.thingiverse.com/thing:748679
Thank you for visiting my Instructable!
Step 1: Step1: Concept / Table
OVERVIEW:
So I built this enclosure specifically for my two printers (Makerbot Rep 2 and Flash Forge Creator Pro), if by any remote chance you have the same two printers - then you're in luck... However, I am going to assume the vast majority of you do not... Never fear though, you can still build this for your printers, you're just going to need to figure out the dimensions you will need and build according to your dimensions.
GETTING DIMENSIONS NEEDED:
First, this enclosure can be made for however many printers you own... I have 2, so naturally, I built mine to fit 2 - however - this will also work for only 1 printer, or even 4 or 5 printers - it will just be massive - but it will still work nonetheless.
What you want to do is measure how big your printer(s) is/are - Length, Depth, and Height... Then decide what sized enclosure you will need around the printers... In my case, I measured that my Makerbot and Flash Forge were both approximately 20"L, 13"D, 15"H... So I decided to sit them side by side and leave myself an extra 6-8" in each direction and about a foot on top so that I can easily work in there changing filaments and work on the machines...
So the Length of my enclosure is 20+20+8=48"... Depth = 13+8=21"... and Height = 15"+12"=27"... So the entire area of my bottom enclosure = 48"L x 21"D x 27"H... I then calculated and decided how to build the wooden enclosure around those dimensions... You should do a similar method...
TABLE/BASE:
Before you do anything, first, you're going to need to build a table from which you will build the enclosure... I used regular old lumber from Lowe's... I used 4x4"s for the legs cut at 29"... I used a 1" rectangular piece of particle board for the table top... And I cut various sizes of 2x4" for all around supports as seen in the pictures... I also added a shelf at the bottom with some extra particle board I had from the table top to keep extra parts and tools easily accessible.
You can make the base table however you want, but this is how I did mine - just make sure whatever you build is very sturdy - you don't want your printers falling.
Step 2: Step 2: Building Your Enclosure
NOW, after you have figured out how big you need your enclosure to be, now you can start building it...
OVERVIEW OF STRUCTURE:
What I did was relatively simple... I used 2x4" lumber to build a frame all around.
I used another 1/2" piece of sturdy rectangular particle board for the second level where the filament sits...
Then another layer of lumber, this time 2x2" just high enough so I could fit two spools with spool holders standing on top of one another (about 19" high)...
From there, I put a roof and a back on the enclosure out of thin, malleable, particle board...
Lastly, I added a 1" diameter wooden rod in the top of the top shelf where the hooks go to hold the filament spools.
You can deduct a lot of the structural design from watching the video and looking at the pictures...
3D PRINTED PARTS:
Here are my spool holders and hooks... My spool holders are actually pretty popular on Thingiverse, even if you don't build the enclosure - these spool holders are still awesome and you should give them a try with your filament...
Spool Holders:http://www.thingiverse.com/thing:290064
Hooks:http://www.thingiverse.com/thing:748702
Here's a video on my Spool Holders
Step 3: Step 3: Paint
OVERVIEW:
Pretty simple... Now that you have all the wood together, you're going to want to paint it... Paint it however you like... I chose black because black is awesome.
Step 4: Step 4: Acrylic
OVERVIEW:
This is probably the trickiest part if you've never scored acrylic before... If you have, good, this should be easy... If not, you can do it - it just takes a lot of patience.... Go to a hardware store and pick up a good scoring knife for acrylic... DO NOTtry to use a razor or a utility knife -you will have a bad time!!! I'm not going to get into how to score acrylic here, but there are some good YouTube videos on it...
I cut acrylic all around... Four pieces for the sides... One large piece for my front filament hatch... and two pieces for my sliding glass... I won't give dimension since most likely yours will differ from mine. You're going to need to figure this out on your own...
I then epoxy glued the acrylic directly to the wood - you can see in the pictures all the dried glue... This was ugly, but there was really no way around it if I wanted to keep my perfect, air tight, seal in the enclosure... So to make it look pretty, I bought few rolls (24"x60") of carbon fiber print, cut it all up into sizes I needed, and used it to put a bezel around all the acrylic pieces and frame so that you can not see the glue and sealant from the outside - this really made the enclosure look professional - but this should be the very last thing you do when building the enclosure... I'll go into more detail with this optional step at the end of this Instructable.
TOP ACRYLIC HATCH:
For the pull-up acrylic hatch that goes to the filament enclosure, I used rubber weather foam that is most commonly used for exteriors doors on houses (I actually used this stuff in a lot of places - it makes a good seal)... This stuff is cheap and can be bought at any hardware store... I put three hinges at the top, gorilla glued one side to the acrylic and screwed the other into the roof of the enclosure... Be sure, before you mount the hinges to offset them so that the acrylic sits firmly on all four corners of the foam, otherwise, you never get a good seal...
From there I mounted magnets on the acrylic, again with gorilla glue, and the other side of the magnet to the wood as seen in the pictures... Then I added pull out extender tube supports and a large holding bracket that I designed and printed to hold the acrylic up... I apologize in advanced, but I over-engineered the bracket - both take about 12 hours to print together and they are huge... I wanted to make sure they were as strong as possible to hold up the extenders, however, in that effort, I may have made them strong enough to do pull-ups on - my bad... But if you ever want to do pull-ups - they would be perfect... The extender tubes are relatively weak compared to the brackets, I plan on redesigning a stronger extender and more practical bracket and then re-upload them sometime in the near future... But for now - these will do.
3D PRINTED PARTS:
Bracket:http://www.thingiverse.com/thing:748724
Extenders: http://www.thingiverse.com/thing:748692
SLIDING FRONT DOORS:
For the sliding doors, that was little trickier... I bought a lot of 3/4" squared finishing wood and built two rectangular frames out of them and put weather foam all around on both frames (you can see better in the picture)... From there I used more acrylic on the sides and on top to offset the new door frame from the rest of the existing enclosure.. I then inserted my doors into the frame and mounted everything to the enclosure... It would be a good idea to paint your wood before you put everything together. This was a tricky part of the build and I had to scrap two frames before I was successful on the third... But if you examine the video and the pictures, you'll be able to see how I did it and hopefully not have to go through the failed attempts that I went through... But once you get this right - it works perfectly.
Step 5: Step 5: Let There Be LIGHT!
This is the coolest part of the enclosure if you watched the video.
OVERVIEW:
First, I mounted a surge protector in the middle of my enclosure that will stay there forever, the end of the plug goes out the back of the enclosure and is sealed all around, so the whole enclosure plugs in with one plug - this will help you keep a good seal in your enclosure due to the fact you wont have 6 plugs coming out of the back - just the one to the surge protector...
I got strips of RGB LED lights, I cut them to size and put them where I wanted them in the enclosure, then I linked them all together using cut up Cat5 cable...I routed everything into an RFID receiver and now I can control the LEDs with a remote - allowing me to change the colors, the intensity, or make my living room look like a rave with strobe lights... These LED lights have an awesome effect on the filament that causes them to change colors - you can see a demo of this in the video...
LED lights are simple... You can look on YouTube on how to cut and splice them together... It was well worth using the RGB lights... All of this should cost about $25-30 to do.
Step 6: Step 6: the Fan
Here is where I try to create negative pressure so that all the micro-particles and fumes from the printers leave my house and don't go into my living room...
OVERVIEW:
I got a 4" fan from Radio Shack... I cut a circular hole in the back of the enclosure (smaller than the fan), then mounted the fan blowing out the window behind my enclosure, through a printed duct and vent... I then made a board cut out to close the window, taped all around it, and added a little bit of insulation in the duct to keep the cold out... I then sealed everything up around it. You can see the duct and window set-up in the video...
3D PRINTED PARTS:
Fan Cover:http://www.thingiverse.com/thing:748727
Step 7: Step 7: Seal Everything Up
This step is important because it creates a seal all around the enclosure so that it can have a vacuum effect with the fan in the previous step...
OVERVIEW:
Here I used FlexSeal, you know, that stuff sold on the infomercial with that crazy guy who shoots cannon balls at boats - let me tell you that stuff works GREAT!!!... You can use FlexSeal, however, and silicon or rubber based caulk should work just fine. In the pictures you have already seen, you can see where I added it all around the edges and acrylic - I applied a nice strip of it to every nook and cranny around the whole enclosure...
This took up two tubes and cost about $20...
Just a heads up, this stuff has a very strong odor to it... So try not to breath it too much until it drys...
Step 8: Step 8: Cutting Holes for the Filament to Guide Through
OVERVIEW:
Here you're going to want to drill some 4-5mm holes through the base of the second shelf where the filament sits... I drilled 20, 2 rows of 10, evenly spaced holes for all my filament to guide through... Then I printed out a filament guide, a filament cleaner, and a end holder for each hole... If you're unsure how to assemble this, I explain everything in the video and the pictures will show you where to put everything... Also, I cut a little square piece of my rubber foam sealant and stuffed them into the filament cleaners with some super glue to keep it in place... This will hug the filament as it is fed through and cleans off any dust or particles on the filament before it reaches the extruder.
3D PRINTED PARTS:
Filament Cleaner: http://www.thingiverse.com/thing:748717
End Holder:http://www.thingiverse.com/thing:748714
Filament Guide:http://www.thingiverse.com/thing:748707
Step 9: Step 9: Finishing Touches
OVERVIEW:
Here's where I added my little heater, my dehumidifier, my thermometers, shelves and other misc things. You can do whatever you want here, but these are the things I added for functionality... You can see them all in the pictures above...
3D PRINTED PARTS:
Shelf:http://www.thingiverse.com/thing:748700
Tool Shelf:http://www.thingiverse.com/thing:748697
Step 10: Step 10: Optional Trim Around Enclosure
This step is optional, I mentioned it during the acrylic part in step 4 - so I'll reiterate it here...
OVERVIEW:
I ended up epoxy gluing all the acrylic straight to the wood frame, this left white, dried up glue visible all around the acrylic and the enclosure... This was ugly, but there was really no way around it if I wanted to keep my perfect, air tight, seal in the enclosure... So to make it look pretty, I bought few rolls (24"x60") of carbon fiber print, cut it all up into sizes I needed, and used it to put a bezel around all the acrylic pieces and frame so that you can not see the glue and sealant underneath - this really made the enclosure look professional...
It's pretty simple, just cut the sized bezel you need out of the sheet, then apply it directly to all the acrylic around your enclosure, this will cover up all the glue and make everything look pretty...
This will run you about $40 for the sheets...
THANK YOU FOR READING MY INSTRUCTABLE AND I HOPE YOU HAVE AS MUCH FUN AS I DID MAKING IT!!!
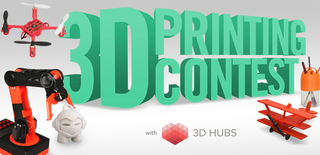
Participated in the
3D Printing Contest