Introduction: 3D Printing: 3D Print a Solderless Circuit Board
The components can be fairly easily connected together without using solder.
This technique is somewhat faster than standard etched and soldered circuit boards. But it does require some skill and attention to detail to create a reliable circuit.
This example circuit board is a simple micro controller circuit that flashes three LED's in sequence.
It is intended to be a minimal illustration of what is possible.
The short video below shows the circuit working.
http://youtu.be/vQuPP3--fxk
Step 1: How It Works
1- A circuit board is designed and printed on a PLA filament printer, in this case it was a MakerBot Replicator 2. The board consists of trace channels with standard .1" spacing and holes for the components.
2- Components are inserted in the board and the leads bent over. Pic2
3- The trace channels are filled with a conductive material. Pic3. For this example, I used a commercial conductive paint that is highly conductive, but you can also use conductive epoxy or make your own conductive material. See step 6.
The result is a working circuit board that is not as vibration resistant as a soldered circuit board, but can be quite useful for experimental circuits and prototypes.
Make no mistake, this requires some skill, with better conductive materials, less skill will be required.
While this is not going to replace conventional soldered circuits, anytime soon, it is the beginning of a fully automated 3d printed circuit.
Step 2: Materials and Tools
MakerBot Replicator 2 or other filament 3d printer. You could also send it to Shape-ways or another commercial 3d printer. The stl files for a circuit board are low in volume and would be fairly inexpensive to have printed by a service.
PLA filament
eye dropper
pointed toothpick
sandpaper
Conductive Copper, CuPro-Cote paint available from: http://lessemf.com/paint.html
This is the most conductive and affordable and easy to use conductive material that I have found.
You could also buy conductive silver epoxy, but it is more expensive.
Or, you can make your own conductive glue or paint. See step 6.
Picaxe 08m microcontroller
3 LEDs
3 resistors (see schematic)
Step 3: Design a 3D Printed Circuit Board
I used the free program 123D Design--the beta version, but you should be able to do it with the newest version.
Step 3 Pic-Draw your design in 2d making sure the walls are .03" wide and the trace channels are .07" wide.
Pic2-Extrude the drawing .06" thick, that is the depth of the conductive trace channels that will be later filled with conductive material.
Add a front panel that is .03" thick.
Cut square holes for components that are .07" square. I made mine too small and some of them had to be cleaned out with drill bit. With holes this small, a square hole ends up fairly round when printed. Drawing a round hole here will tend to close up when printed.
Step 4: The Experimental Circuit
This simple circuit was a preliminary test of the whole technique.
You will probably want to try your own circuit, but should anyone be familiar with the Picaxe microcontroller and want to try this circuit, I have provided the STL file, and the schematic.
Here is the simple Picaxe program code that blinks the lights in sequence:
loop2:
high 1
pause 200
high 2
pause 200
high 4
pause 200
low 1
pause 200
low 2
pause 200
low 4
pause 200
goto loop2
Attachments
Step 5: Print, Populate, and Glue.
Print the STL file
I used a MakerBot Replicator 2 with the following settings:
Standard resolution with a raft
10% infill
2 shells
.2mm layers-standard resolution
It takes about 8 minutes to print.
Populate the board with components and cut and bend over the leads, see step 5 pic. Make sure the leads do not stick above the channel walls. Generally, the longer the leads the better the electrical connection. If you can double bend the leads, even better.
Glue the Components
I found that an eyedropper with tubing and a tube small enough to fit into the channel the easiest way to fill the channels with conductive paint. Fill them up to just below the height of the walls and don't worry about spillover and shorts. I used a toothpick to work out bubbles and made sure the leads were well surrounded with paint. See pic2. Let it dry overnight at room temperature.
Conductive materials only glue with light to medium strength onto copper or tinned component leads. So care has to be taken to make sure the leads are bent and well surrounded with conductive material so that they have a strong mechanical connection.
Touch Up The Traces
The conductive material will tend to shrink as it dries.
So use fresh paint to fill in any holes or gaps or bubbles.
When the second coat is dry, use sandpaper on a flat surface to knock off any conductive material off the wall that could short the traces. pic3 is the result.
The circuit is done and ready for testing.
Important Considerations
This conductive paint is a water based acrylic or latex paint and as such should not be allowed to freeze.
While it is very affordable, you should be advised that it is copper particles that have been treated with a proprietary process to resist oxidation. So it would probably be a good idea to seal the whole circuit, after it has been tested, with silicone or some other sealer that would prevent moisture or oxygen to enter. Embedding the whole thing in silicone or epoxy would also prevent the components from shifting under vibration or pressure and losing their connections.
Conductive epoxy, although more expensive, would probably work the best best for longer lasting circuits as it is a stronger and more moisture resistant conductor.
Step 6: Make Your Own Conductive Glue or Paint
Commercially made conductive materials like silver filled epoxy or the copper-based paint I used here are highly conductive. The conductive trace channels are .07" wide and .06" deep. In such a channel, the conductive paint has a resistance of around 1 ohm per inch.
You can make your own conductive materials but they will have a higher resistance than the commercial products. Typically they have a resistance of 200 ohms or more per inch in this size of a channel. So, if you try making your own, it would be a good idea to make the trace channels two or three times as deep to lower the resistance.
Make Conductive Glue
Here are the details on how to make your own conductive glue: https://www.instructables.com/id/Make-Conductive-Glue-and-Glue-a-Circuit/
Or here: https://www.instructables.com/id/Conductive-Glue-And-Conductive-Thread-Make-an-LED/
Make Conductive Rubber
Here are details on how to make your own conductive rubber: https://www.instructables.com/id/Conductive-Rubber-Make-Touch-Sensitive-Robot-Skin/
Or here:
https://www.instructables.com/id/Make-Conductive-Rubber-Transparent-stylus-iPodiP/
Step 7: Other Possibilities
Totally Automated 3d Printed Circuit Board Print
It should be possible at some point, to print Plastic and solder or a conductive material at the same time to create a full circuit board in one or two prints. A component holder would be printed, components would be inserted, and then the board and conductive traces would be printed to hook the circuit together.
Circuit Shells
You could make a circuit that is part of the device case
Coils And Antennas
Some small coils and high frequency antennas can be made that are part of the case of the device.
Capacitors
Low value capacitors and high voltage capacitors can also be made using this method.
Curved Circuit Boards
The circuit can be made as part of the structure or enclosure of a device. For example, a circuit could be made as part of the 'bones" or exoskeleton of a robot. Step 7 pic shows a curved circuit board lantern I made using bendable, conventional circuit boards: https://www.instructables.com/id/Curved-Circuit-Art-Make-A-Double-Helix-LED-Lanter/
Similar things could be 3d printed.
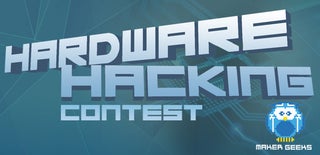
First Prize in the
Hardware Hacking
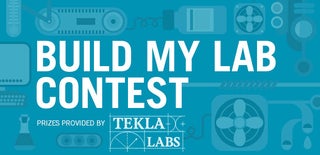
Participated in the
Build My Lab Contest
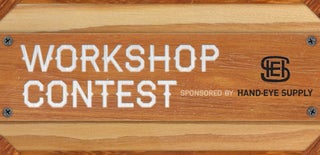
Participated in the
Workshop Contest