Introduction: 3D Printing an Ironman Helmet
Early last year, before The Avengers came out, I approached the rapid prototyping department at my company and asked if they would be able to help me produce a replica Ironman helmet. I had tried building the helmet with pepakura files produced by a member of the thereplicapropforum.com, but I found I did not have the time/patience/skill to sit and trim out hundreds of pieces of paper and reassemble them. This is my first instructable, but I wanted to share my process for anyone who has been interested in going this route. I took photos and screen caps along the way, but I may have missed a few steps that I'll just have to explain.
I've added separate zip files with OBJ and STL files of the Ironman helmet pieces for others to use. Please credit the Replica Prop Forum and I, if you use! As I outline in Step Two, the build envelope of the printer that was used to produce this helmet was 10" x 14" x 8", so I had scaled the pieces to fit that and it is sort of a happy accident that it worked out. :)
Step 1: Modeling
As I mentioned, I had gotten the pepakura helmet file from the RPF forum. I had also purchased a copy of the Pepakura software. With a full version that allows you to create files rather than just view, I exported the pepakura file as an OBJ which I could would with in Maya. The conversion process was easy, but because the pep file is meant for paper usage, it was relatively low resolution and had no thickness.
The first step, while the poly count was low, was to extrude the model inward to give the helmet thickness. Thickness is important, it provides stability to the final product which can be brittle when it is printed too thin. Because I planned on wearing this, (and probably walking into walls/doors/people) I wanted it to be thick enough the handle a bit of abuse. The final helmet varies in thickness because while the outside has grooves and ridges, I wanted the inside to be smooth. That way, the sides and bottoms of the grooves would have extra material around then to prevent fractures. The overall helmet averages between .125" and .25" thick.
When I was done adjusting the silhouette of the low poly helmet, I subdivided the model to provide a smoother finished surface. As you'll see later, I could have gone even further with this step.
Step 2: Prepping the Model for the Printer
The printer that this model would be created with was a Spectrum z510, which has a build area of 10" x 14" x 8". Knowing that, I could see that the helmet would not fit into the printer in a single piece, so I needed to divide the model into pieces I could then easily reassemble.
To make the breakdown correctly, I created a box in the same proportion as the build area. I chose to divide the helmet down the middle so I would have a single seam to cover.
Step 3: Printing the Model or Why Thickness Is Important
Unfortunately, I don't have and pictures of the helmet being printed. So I'll just have to explain this part.
When I was happy with the way the pieces fit within the box, I deleted the box shape, exported the stack as an STL file and sent it off the the prototyping group.
Several days later, I got a call that the pieces were finished but there was some damage. When the pieces were printed, they were coated with a hardener/epoxy resin then put into the oven to cure. Because the helmet pieces were too thin, they warped, buckled and cracked while in the oven. Because of the varied thickness, some parts hardened faster than others. You can see this in the uneven color of the helmet halves. The bottoms were thicker than the top which ended up distorting.
The faceplate was thick enough and didn't end up warping. As you can see in the second picture, you can still see some of the tessellation from modeling. If I had further subdivided the model, these blocky areas would have been less prevalent.
I went back to my original files and did some more thickening, bulking up the whole thing to the .125"-.25" I mentioned before. The second picture is what resulted from that printing. But I also requested that they skip the epoxy hardener since I would be sanding, fiberglassing, and using filler on the seams. Overall, it was a much better print.
Step 4: Assembling the Pieces
The first image is from a little later in the process, but I forgot to take a picture of the inside during first assembly. To connect the two halves of the helmet, I clamped the halves together, then laid down 3 layers of fiberglass cloth and epoxy resin. Once the inside hardened, I went through several rounds adding a thin layer of bondo to the outside and sanding to fill the gap on the exterior surface. The second and third versions show the results of bondo and sanding.
Remember to wear rubber gloves, long sleeves, breathing mask and eye protection throughout this process. Fiberglass dust can be very irritating to your skin and painful in your eyes!
Step 5: Hinges & Connectors
Hinges
As you could see in the last step, I've used cabinet top hinges to control the opening and closing of the face plate. As you can see from the sanded patch behind it's location, positioning these correctly was pretty tricky. First I hot glued the top piece to the top edge of the interior face of the faceplate. I then put the helmet on to find out where about my temples were and marked a point a bit forward and up from that point. I attached the body of the hinge to this point and spent quite a bit of time opening and closing to find the correct distance and angle to allow the faceplate to rest just above the eye line. I will show later how I kept the faceplate open once it is up there.
Connectors
Since the neck opening is not large enough to get my head through, I added center release buckles to each side, with half on the jaw and half on the helmet. Once I was happy with the placement, I traced off the position of the buckle, removed it and added a small amount of gorilla glue. Then carefully placed the buckle back while preventing the glue to seep into the space between the helmet and jaw, OR onto the release button for the buckle. I added weight and let it sit overnight.
Step 6: Padding the Helmet
Once the hinges and jaw connetors were worked out, I added a layer of padding to make the helmet snug and keep it from jostling around when I moved my head. This was simple, I simply cut several 1" wide strips of foam and attached them to the back with a dab of hot glue. The two wide horizontal pieces prevent my neck from sliding too far back and bring my eyes closer to the holes in the mask. Adding the padding made it much easier to turn my head and made it much more comfortable than having the hard plastic pressing against my skin.
Step 7: Lighting the Eyes
Unfortunately, I forgot to take a lot of photos during this phase. I was doing a lot of trial and error to get the right combination of angles and lights. What I did end up with is a .375" wide circuit board, with 5 superbright white LEDs inside a container made from an index card and electrical tape.
This was my first experience working with LEDs or any sort of circuits so to be safe (because the battery is less than an inch from my face, I wanted no overheating or exploding) I have the split into two groups two LEDs connected to 1 capacitor and the other three connected to another capacitor. It does dim the light output noticably but it protects my eyes, the battery, and the LEDs and it still remains pretty bright.
As you can see from picture 4. I had to do a bit of work sealing off the light from leaking through the surrounding plastic. Several layers of black primer on the interior and 2 layers of grey primer on the exterior as well as better enclosing the light casing, and I was able to solve the light leaking.
Finally, under the decorative screwhead on the right side of the mask, I placed an on off switch that I pulled out of a tap light from the dollar store. This allow me to turn the lights off while wearing the mask without having a visible switch.
Picture 1: Test photo when under construction.
Picture 2: Shows piece I cut from eye as template
Picture 3: Completed "eyes", wiring and battery holder.
Picture 4: Test fitting lights
Picture 5: Eye light on/off button
Step 8: Priming
Not much secret to show here. Just several layers of primer and lots of sanding sanding to smooth the surface. As you can see on the forehead, just below the widow's peak, the tessellation of my model is still showing through a bit. I used a sandable primer so that I could work out a few of the divots that had made it through to this point. Because the faceplate is the most prominent feature of the helmet, I ended up sanding it down to nearly bare plastic several times to get the smoothness I wanted.
Remember your Spray Painting 101 lessons: Only paint in a well ventilated space. The primer I was dry to the touch in 15 min and sandable within 30. Volatile chemicals make for fancy paints but bad lungs.
Step 9: Painting & Sanding
For the painting, the colors were both Duplicolor Perfect Match colors: the Red was Medium Garnet Red Metallic and the Gold was Sunburst Gold Metallic. I put 4-5 thin coats of paint on with a very light sanding between each coat.
Again, remember to wear breathing protection in a well ventilated area for this step. Automotive paints are brutal to your lungs.
Step 10: Keeping the Faceplate Up OR Magnets: How Do They Work?
As I said before, here's how I finally figured out how to keep the faceplate up. I created a slight recess in the upper rim of the face opening and glued a .1875" round rare earth magnet in the opening. Then I had to get a little creative on how to attach the magnets to the hinge arm. I ended up cutting a short length of wire that would span the width of the arm and would be more area to attach the magnet to. On one side, I need to add a second magnet because the first wasn't making contact. (I inset the helmet magnet a bit too far)
Step 11: Final Touches and Finished Helmet
And here's the final results!
I was told to lightly wet sand the surface with 2000 grit when I was finished painting, but I haven't yet as I like the mild diffusion that the surface has.
Also, for a bit more ear comfort, I added black felt to both sides of the helmet. If I haven't mentioned it before, raw prints feel a bit like sandpaper and the tips of my big ears don't appreciate the feeling after a short while.
Hope this has been helpful! Let me know if there are any questions!
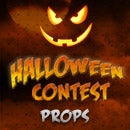
Finalist in the
Halloween Props Contest
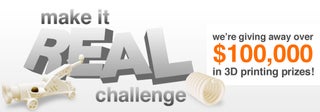
Participated in the
Make It Real Challenge