Introduction: 3d Printed RC Motorcycles: 2016 Ducati Draxter and 2016 Suzuki GSX-RR MotoGP
By: Brett Turnage
@3dprintRaceTech
Media:
Motorcycle News http://www.motorcyclenews.com/...
Motorcycle.com http://www.motorcyclenews.com/...
3DPrint http://www.motorcyclenews.com/...
All3dp http://www.motorcyclenews.com/...
Adafruit http://www.motorcyclenews.com/...
The Drive http://www.motorcyclenews.com/...
Le Repaire des Motards http://www.motorcyclenews.com/...
Project Jibril: This project consists of two 3d printed RC motorcycles: the 2016 Ducati Draxter Concept Drag Bike RC and the 2016 Suzuki GSX-RR MotoGP RC motorcycle. This project includes two bikes because the motorcycle world is very diverse. I hope that everyone can find one that appeals to them. Name sake: My friend Jibril is crazy about motorcycles, so this project was named after him as he was the inspiration for it. RC motorcycles are almost like black magic, the fact that they can ride and balance themselves is accomplished with gyroscopes (either passive or active), and kits like the Kyosho Hang on Rider brought realism by having a rider that actually moved. This project remakes that magic for the 3d world with two 2016 bikes that were designed not as chassis, but as the individual motorcycles with unique parts that aim to recreate the realism of the actual bike. Both the Ducati and Suzuki feature a 3d printed functional front fork, adjustable rear suspension, and drivetrain that translates power from gears to a belt drive system which turns the rear wheel. They stay upright by using a weighted front wheel which acts as a passive gyroscope, and both bikes have to option run either TPU 3d printed rear tires or a rubber F1 RC tires for better grip. This is just some of the beauty and engineering that went into the bikes, but in order to really make these motorcycles come to life, the rider has to move. The Rider which is a 3d wonder in its own right. It works by having a brain, backbone, and pelvis. The brain is a super tiny ultra micro servo which is located in the head of the rider. It attaches to the backbone that is a metal rod which runs through the body and is attached to the pelvis, translating the movement of the servo. More than just realism, The Rider steers the bike. The lower left arm is attached to the main servo, and it moves the arm forward and backwards. This movement turns the handlebars which steers the bike. When both bike and rider are married together, you get an amazing experience of two futuristic race bikes that were never available to the public with a rider who’s sitting on the bikes in the way an actual rider would. This project has taken me over 5-months of work, lots of iterations, multiple different bikes, many older versions that will never be released, and months of testing. These two bikes are the result of all of that hard work. I hope you enjoy it, I hope you are inspired by it, and I hope that in turn you inspire others. 1:12 scale
Filament used Solutech3d
Designed in Fusion 360
Sliced with Simplfiy3d
Wheel weight cut with Othermill Pro
Step 1: Download Files
Step 2: Ducati Body Overview
Parts Needed:
(1) Main Frame
(2) Bottom Fairing (L & R)
(2) Body Front (L & R)
(2) Body Rear (L & R)
(2) Engine Parts Silver (L & R)
(2) Engine Cover (L & R)
(2) Seat Brace (L & R)
(1) Hitec Servo HS225BB
(1) Racer’s Edge Hitec Servo Arm (1) 7200KV motor
(2) m2 x 8 screw
(2) m2 x 10 screw
(4) m2 nuts
(2) m2.5 screws and washers
(1) m3 x 10 screw
(1) Body Brace decoration
Use the guide above to assemble. First glue the pairs of each parts together, and then
assemble.
1. First assemble the body front and then the body rear. Then attach. 2. Attach the seat braces.
3. Place in the Hitec HS225BB servo
4. Attach the main frame.
5. Glue the bottom fairings together.
6. Install motor into engine parts silver left with 2.5 screws and washers.
7. Tap bottom fairing front bolt hole on the rear post, and screw in m3 x 10 screw to attach the seat brace to the bottom fairing.
8. Place the ESC (Electronic Speed Controller) inside of the main frame, so that the fins of the
ESC are facing foward. Run all of your wiring out of the front.
9. Screw in the Engine Parts Silver with m2 x8, m2 x 10 screws, and m2 nuts.
10. Attach all decoration pieces: Engine Covers and Body Brace decoration with 5-minute epoxy.
Step 3: Ducati Feet Brace Assembly
Parts Required
(2) Fender Brace (Left and Right)
(2) Pedal Attachment (Right and Left)
(1) Feet Brace Bar
(2) Long 4.8mm ball studs (Losi B1444 Ball Stud Long & Shock Mounting Brace: MRC) (2) 2mm Spacer Set (3Racing 2mm Spacer Set M4WD-01/PK)
Steps:
1. Drill the holes on the feet bar braces with a 2.5mm drill bit and tap the holes with a m3 x 0.5
tap.
2. Install a long 4.8mm ball studs with the 2mm spacer onto each feet brace.
3. Glue the assembly together as shown above with 5-minute epoxy.
4. Glue the completed feet brace assembly to the Seat Brace as shown above.
Step 4: Suzuki GSX-RR Body Overview
Parts Required:
(1) Turnigy 1000mAh 2S 20C Lipo Pack HobbyKing RC Battery (dimensions 70 x 35 x 13mm) (2) Main Body (L and R)
(2) Front Fender (L and R)
(2) Rear Fender (L and R)
(2) Tank (L and R)
(2) Main Frame (L and R) ***Main frame L should be printed at 100% infill****
(1) Servo Holder
(1) Hitec Servo (HZS-225BB)
(1) Racer’s Edge Hitec Servo Arm
(1) Hot Racing SMLT4825 48p 25 teeth pinion gear
(1) 7200KV motor (GoolRC 2430 7200KV 4P Sensorless Brushless Motor with 25A ESC) (1) 5 mm Diameter x 45 mm Long Shoulder
(2) M2.5 x 0.45 x 20 Long screw
(2) M2.5 x 0.45 x 25 long screw
(1) Metric Alloy Steel Dowel Pin, M5 Diameter, 28 mm Length
(1) Tight-Tolerance Shoulder Screw, 18-8 Stainless Steel Socket Drive, 4 mm Diameter x 18
mm Long Shoulder
(2) M2.5 x 0.45 x 8 screws
(2) M2.5 washers
(1) 5-minute epoxy
(1) M2 x 0.45 tap
Use the guide above to assemble. First glue the pairs of each parts
together, and then assemble.
STEPS:
1. Glue both main frame sections to the servo holder with 5-minute epoxy. Place a screw in the rear swing arm hole to keep them aligned.
2. Glue rear fender onto the main frame assembly.
3. Glue tank assembly onto the main frame assembly and rear fender assembly..
4. Install motor using M2.5 x 8 screws and washers.
5. Use the M2 x 0.45 tap on the holes on the bottom of the servo holder.
6. Glue the Main body sections together
7. Glue the front fenders together and then glue them to the Main Body.
8. Place the battery into the Main body. Make sure it sits into the depression with the wires
hanging out towards the rear of the bike.
Step 5: Motor Specs
7200 KV motor. Any motor with these specifications will work.
24mm diameter canister. The lenght is 30mm long. 2mm shaft.
I used:
GoolRC 2430 7200KV 4P Sensorless Brushless Motor with 25A Brushless ESC(Electric Speed Controller)for 1/16 1/18 RC Car Truck which can be found on Amazon.
Test the motor when you get it. Make sure that it spends freely. I had one that had a bad Electronic Speed Controller. If you have any problems return it for a replacement.
Step 6: Front Fork Assembly
Parts Needed:
(2) Shock Top
(2) 7/32 x 1 x .016” Compression Spring [C-552 Century Spring Corp.] (1) front fork
(2) Retaining Ring
(2) m4 x 26 dowel pin stainless
(2) front spindles (left and right)
silicone grease
5-minute epoxy
STEP 1: Layout Parts
Clean all holes with the appropriate drill bit to make sure they are the exact size needed and clear of debris.
Holes on bottom of front fork require m4 drill bit. Top of front fork requires m6 drill bit
Spindles m5 drill bit, m4 drill bit on top spindle holes Retaining Rings m4 drill bit
STEP 2: Slip Retaining Rings onto Dowel Pins
You want the retaining rings to be located on the top. Stand them up and affix them with 5- minute epoxy.
STEP 3: Slide the Dowels into the Front Fork
Retaining rings will ensure that the dowel pins stay inside of the assembly. Move the dowel pins up and down to make sure that they move smoothly.
STEP 4: Place grease inside the tubes
STEP 5: Install Springs
Slide the two springs down into the front fork.
STEP 6: Install Shock Tops
Before beginning, clean off the top of the front fork to remove any silicone that remains on the top of the front fork.
Place the Shock tops inside. Use 5-minute epoxy and bond them together.
You may need to use a bulldog clip to keep the shock tops affixed secure to the front forks while the epoxy is curing.
STEP 7: Install Spindles
Place 5-minute epoxy in the holes. Grip the dowel pins with pliers and press the spindles onto the dowel pins. Make sure that the spindles are installed on the correct side. It should like the picture above.
Step 7: FRONT WHEEL ASSEMBLY
Parts Needed:
Assembled Front Fork
(1) Front Tire
(2) Wheel weights (A & B)
(1) Front Rim
(2) 6 x 10 x 4 bearings
(2) Aluminum Unthreaded Spacer, 8 mm OD, 2 mm Length, for M5 Screw Size (2)Aluminum Unthreaded Spacer, 8 mm OD, 6 mm Length, for M5 Screw Size (1)5 mm Diameter x 35 mm Long Shoulder bolt
(1) m5 nylock
NOTE: WHEEL WEIGHTS CAN BE BOUGHT AT MY WEBSITE WWW.BTIFAB.COM OR YOU CAN
MAKE YOUR OWN IF YOU HAVE A MILL. SCHEMATICS FOR WHEEL WEIGHTS ARE PROVIDED BELOW.
THE BIKES WORK BY HAVING A PASSIVE GYROSCOPE, OF A WEIGHTED FRONT WHEEL.
STEP 1: Assemble tire
Tires are best made out of TPU flexible filament. Install the wheel weights into the tire first. Then press the rim inside of the tire.
STEP 2: Install Bearings
STEP 3: Install Front Rotors
Press front rotors on to either side of the front rim.
STEP 4: Install front rim
Using one spacers align the rim until it it centers in the front fork.
Insert 5 mm Diameter x 35 mm Long Shoulder bolt through the rim and secure with m5 nylock on the other side. Ensure that the wheel spins freely.
STEP 5: Install Front Fender
Place 5-minute epoxy on the front spindles, and install the front fender. Make sure that the front fender trailing edge is parallel to the front fork.
Step 8: Suzuki Specific Handlebars
Additional
Parts Needed:
(3) 4.5 ball stud with hex end
Steps:
1. Install the three 4.3 ball studs into the handle bars
Step 9: INSTALL FRONT FORK ONTO MOTORCYCLE MAIN FRAME
Parts Needed
(1) Metric Alloy Steel Dowel Pin, M5 Diameter, 28 mm Length Silicone Grease
STEP 1: Clean out the hole
With an m5 drill bit ensure that the hole on the front fork and bike’s mainframe are to the correct size and clear of debris.
STEP 2: Insert Grease in Mainframe
STEP 4: Align Parts
Place front fork onto mainframe.
STEP 5: Insert dowel pin
Press in with pliers.
Step 10: Ducati Rear Swing Arm Assembly
Parts Needed:
(1) Swing Arm
(1) Rear Fender (right)
(1) Atomic AMZ-AMZ001-GS grease shock (combine 2 springs)
(2) 5x10x4bearing
(1) 38 Tooth drive gear (3Racing SAK-D135)
(2) Drive gear adapter (Front and Rear)
(1) 5 x 40mm Shoulder bolt
(1) m4 nylock nut
(2) 4mm ball studs
(3) m3 x 10 screws
(3) m3 flat nuts
(1) 4 mm Diameter x 20 mm Long Shoulder, M3 x 0.5 mm Thread Size (2) m2.5 x 0.45mm thread, 20mm long screw
(1)8mm OD, 13mm Length, for m5 screw unthreaded spacer
(1) 8mm OD 2mm Length for M5 Screw unthreaded spacer
Steps:
1. Bolt the Swing Arm and Rear Fender together.
2. Install bearing on either side of the swing arm hub hole. Press them in. (You may need to
clean the hole out with a m8 and m10 drill bit. Set the drill to reverse to only clean out the
holes, not to cut.
3. Assemble Grease shock. Use 2 springs by together so the coils are overlapped.
4. Install m4 ball stud and install grease shock onto the assembly.
Step 11: Suzuki Rear Swing Arm Assembly
Parts Needed:
(1) Swing Arm (either standard or for rubber tire) (2) Drive Gear Adapter (Front and Rear)
(2) 5 x 10 x 4 bearing
(1) Rear Fender
(1) 5mm Diameter x 50mm Long Shoulder bolt
(1) m4 nylock nut
(1) Associated FT Rear Aluminum Shock Kit Blue RC18T / FGX (2pcs)
(2) 4mm Ball Nuts
(2) Seat (L and R)
(1) Rear Seat Pad
(1) 38 tooth drive gear (3Racing SAK-D135)
(1) Tight-ToleranceShoulderScrew,18-8StainlessSteelSocketDrive,4mmDiameterx18
mm Long Shoulder
(1) m3 nylock nut
(2) 8mm OD, 2mm Length for M5 Screw Size Unthreaded Spacer
STEPS:
1. Install bearing on either side of the swing arm hub hole. Press them in. (You may need to
clean the hole out with a m8 and m10 drill bit. Set the drill to reverse to only clean out the holes, not to cut.
2. Assemble Associated Shock
3. Install m4 Ball stud and insert into the top hole of the shock.
4. Attach the shock to the rear seat mount, by either tapping the hole with an m3 x 0.5 tap or
drilling the hole and using a bolt.
5. Place the rear shock through the hole in the rear fender and glue with 5-minute epoxy.
6. Glue the Seat and Rear Seat to the rear fender.
7. Install an 4mm ball stud into the rear swing arm. It should be facing to the right.
8. Install the Rear Swing Arm into the motorcycle by inserting the 4mm Diameter x 18 mm
Long Shoulder bolt and fixing it with a m3 nylock nut.
9. Press the rear shock ball socket into the 4mm ball stud that is located on the rear swing arm
(adjust the rear shock to your desired rebound setting).
Step 12: REAR DRIVE ASSEMBLY
1. Assembly Rear Drive Gear as shown, use (3) m3 x 10 screws an nuts to secure the unit
together.
Step 13: Ducati Rear Tire Assembly
Required Parts
(1) Rear Tire [TPU filament] (1) Rear Rim
Slip the tire over the rim.
STEP 1: Slide shoulder bolt into the rim
Place some 5-minute epoxy inside the rear rim before you slide the shoulder bolt inside. If you forget this step the rear wheel will not be fixed and it will not transfer the power from the motor to the ground.
STEP 2: Insert the shoulder bolt into the swing arm
Align the rim so that there is a small gap between the rear of the rim and the swing arm. You can use an m5 x 2 spacer.
STEP 3: Install the drive gear assembly onto the shoulder bolt
Do not affix yet with glue, wait until you install the belt in following steps, but when you are ready to make it permanently attached, use some 5-minute epoxy to stop the drive gear from spinning on the shoulder bolt.
Attach Rear Swing Arm Assembly to Body
Attach the entire rear assembly to the body by using 4 mm Diameter x 10 mm Long Shoulder,
M3 x 0.5 mm Thread Size
Step 14: Suzuki Rear Tire Assembly
Required Parts:
(1) Rear Tire [TPU filament] Rear Rim
(1) Rear Rim (either standard or for Rubber tire)
Slip the tire over the rim. For Rubber Tire use super glue.
STEP 1: Slide shoulder bolt into the rim
Place some 5-minute epoxy inside the rear rim before you slide the shoulder bolt inside. If you forget this step the rear wheel will not be fixed and it will not transfer the power from the motor to the ground.
STEP 2: Insert the shoulder bolt into the swing arm
Align the rim so that there is a small gap between the rear of the rim and the swing arm. You can use an m5 x 2 spacer.
STEP 3: Install the drive gear assembly onto the shoulder bolt
Do not affix yet with glue, wait until you install the belt in following steps, but when you are ready to make it permanently attached, use some 5-minute epoxy to stop the drive gear from spinning on the shoulder bolt.
STEP 4: Install the rear fender
With glue, attach the rear fender onto the opposite side of the 4mm ball stud that is located on the rear swing arm.
Step 15: Drivetrain Assembly
Required Parts:
(1) Spur gear Adapter
(1) 4mm x 14 shoulder bolt
(1) Aluminum center pulley T13
(2) 4 x 8 x 2.5 bearing
(1) 71 tooth 48 pitch Spur Gear
(2) m3 x 8 screws
(2) m3 washers
(1) Hot Racing SMLT4825 25 Tooth 48 Pitch Pinion Gear 2mm Bore (1) m4 washer
Spur Gear Assembly
DRAXTER BOLT IS A 4 MM DIAMETER X 30 MM LONG SHOULDER INSTEAD OF BOLT SHOWN IN DIAGRAM.
Place some epoxy on the Aluminum Center pulley to stop it from spinning.
Attach the Spur Gear to the Spur Gear Adapter by screwing in the m3 screws and washers.
Place the second bearing on the shoulder bolt and install the Spur Gear Assembly to the Main frame.
Install Hot Racing SMLT4825 25 Tooth 48 Pitch Pinion Gear 2mm Bore onto the motor.
Step 16: Install Belt
Parts needed
BESTORQ 234-3M-15 3M Timing Belt, Rubber, 234 mm Outside Circumference, 15 mm Width, 3 mm Pitch, 78 Teeth
ARC R-11 belt tensioner
STEP 1: Cut the belt down to size
The belt needs to be 3-4mm. Measure and then cut wth a box cutter.
STEP 2: Install the belt STEP 3: Align the pulleys
Mark where the rear drive gear is on the shoulder bolt.
STEP 4: Affix the Rear Drive Gear Assembly with epoxy.
Use 5-minute epoxy and permanently install the Rear Drive Gear Assembly onto the shoulder bolt.
STEP 5: Re-install the belt
STEP 6: Install belt tensioner.
mount ARC R11 belt tensioner to the bottom of the swing arm. Use an extra bear in and longer bolt to make sure that belt does not jump off of the tensioner.
Step 17: Rider Assembly
Parts Required
(2) Helmet (Left and Right) (1) Body Bottom
(1) Body Top
(1) Pelvis
(1) Bottom Pivot
(1) vertebra
(1) M3 x 60 dowel pin
(1) m4 x 8 shoulder bolt
(1) 3 x 6 x 2.5 bearing
(1) Ultra micro servo (Hobby King HK-5320 Ultra-Micro Digital Servo 1.7g / 0.05sec / 0.075kg) (2) Shoulder (Left and Right)
(2) Lower arms (Left and Right)
(2) Thighs Inner (Left and Right)
(2) Thighs Outer (Left and Right)
(2) Lower Legs (Left and Right)
(1) Spare servo for wire (SG-90 or other expendable servo)
(6) 4.8mm Ball studs
(2) m2 x 10 screws
(2) m2 x 16 screws
STEP 1: Prepare Servo
1. cut the top wing mount off of the servo. It should be the one closest to the servo horn splines.
STEP 2: Cut the arm off of the servo horn
STEP 3: Make the remaining servo horn circle smooth
STEP 4: Attach vertebra to the servo horn
Use some 5-minute epoxy to make the servo horn circle and the vertebrate permanently bonded.
STEP 5: Put Bearing on Spine and Place the backbone Into the Body Bottom
1. Press the 3 x 6 x 2.5 bearing onto the dowel pin. It should be 24mm from one side. 2. Press the dowel pin and bearing into the bearing holder in the Body Bottom.
STEP 6: Attach Vertebrae to Spine
Use the 5-minute epoxy to clue the vertebra onto the m3 x 60 dowel pin.
STEP 7: Install Ball Studs in Shoulders and Lower Arms
Drill and tap the hole with a 2.5mm drill bit, and then tap with the m3 x 0.5 tap.
STEP 8: Join Shoulders and Lower Arms
STEP 9: Glue Inner and Outer Thighs together
STEP 10: Insert ball studs into Thighs
Drill and tap the hole with a 2.5mm drill bit, and then tap with the m3 x 0.5 tap.
STEP 11: Join Lower Legs and Thighs
STEP 12: Install Servo in Head
Drill and tap the holes in the head with a 1.6mm drill bit, and then tap with the m2 x 0.4 tap.
Using the 5-minute epoxy, place some glue in on the servo mount and attach it as shown in the picture.
STEP 13: Join Head sides with screws
Using the m2 x 10 screws, join the head sides together
STEP 14: Assemble Pelvis
Drill and tap the hole with a 2.5mm drill bit, and then tap with the m3 x 0.5 tap.
STEP 15: Install Bottom Pivot
Slide it on, and make permanent with 5-minute epoxy. The larger hole goes on the dowel pin.
STEP 16: Join Arms to Body Bottom
STEP 17: Attach Body Bottom and Body Top
1. Drill and tap the holes in the body top with a 1.6 mm drill bit, and then tap with the m2 x 0.4 tap.
2. Using the M2 x 16 screws, join the top and the bottom.
STEP 18: Attach legs to pelvis
STEP 19: Attach Head to Vertebra
The bottom pivot should be facing down in order to center the head on the body.
STEP 20: Join Upper and Lower Body
You may beed to tap the bottom pivot to allow the screw to go into the hole.
STEP 21: Extend Servo Wires
Cut the wire off of the expendable servo and extend the ultra servo wires via soldering.
Step 18: Attaching the Rider to the Motorcycle
Requires Parts:
(1) Feet brace Assembly for Ducati Draxter
(2) Foot pegs (Right and Left) for Suzuki
(2) 4.3mm ball stud with a hex end.
(2) Long 4.8mm ball studs (Losi B1444 Ball Stud Long & Shock Mounting Brace: MRC) (4) 2mm Spacer Set (3Racing 2mm Spacer Set M4WD-01/PK)
(1) TT02B Full Turnbuckle Set (For Ducati) (1) 4mm ball stud
5-minute epoxy
*MANUAL STEPS DIFFER DEPENDING ON BIKES. THE DIFFERENCES WILL BE
NOTED IN THE STEPS.
STEP 1: Attach the Footpegs to the Motorcycle.
Drill the hole with a m2.5 drill bit and Tap it with the m3 x 0.5 tap.
Attach two spacers to the long 4.8mm ball studs, and screw them into the hole on the Foot
Pegs for Suzuki or the the Feet Brace Assembly if not already done in the previous steps.
Epoxy the Suzuki Feet pegs to the body of the motorcycle as shown in the picture above.
STEP 2: Attaching ball stud to lower left arm.
B. Ducati Draxter and Suzuki
Install a 4mm ball stud and screw it into one of the holes in the servo arm.
Install the servo arm onto the servo.
Install a 4mm ball stud into the arm of the rider. You may need to drill with a 2.5mm drill bit
and a m3 x 0.5 tap.
(Ducati Draxter only) Using the TT02B Turnbuckle set, assemble a turnbuckle with one 3 x
32mm adjustable shafts and two plastic ball cups.
The finished linkage should have one ball cup facing the opposite direction as the other, so
opposing.
Snap the linkage into the ball stud on the servo.
STEP 3: Attaching the Rider to the Motorcycle
A. Suzuki GSX-RR
Place the rider on the bicycle.
Attach the legs by snapping the feet onto the ball studs. Support the feet brace assembly
and use plies to prevent the assembly from breaking.
Using a wrench screw in the ball studs located in the hands of the rider into the handle bars of the front fork. Slowly screw it in.
Attach the servo arm into the servo and secure with the 2 screws that came with the servo arm.
B. Ducati Draxter
Drill the holes in the handle bars with a 2.5mm drill bit and tap then with the m3 x 0.5 tap. Be very careful in this step—a tip is to support the handle bar while you are tapping it. You can also skip this step by drilling the hole with a m3 drill bit and then epoxying the ball stud in
Snap the 4.3mm ball stud into the hands of the rider by pressing down.
Place the rider on the bicycle.
Attach the legs by snapping the feet onto the ball studs. Support the feet brace assembly
and use plies to prevent the assembly from breaking.
Using a wrench screw in the ball studs located in the hands of the rider into the handle bars of the front fork. Slowly screw it in.
Attach the ball cup from the steering linkage to the 4mm ball stud on the lower left arm of the rider.
Attach the servo arm into the servo and secure with the 2 screws that came with the servo arm.
Step 19: Suzuki Steering Linkage
Parts Needed:
(2) 4.3mm ball cups
(1) m3 x 16 set screw
STEPS:
1. Cut Ball Cups to Size.
2. Thread the Ball Cups and install m3 set screw.
3. Install Linkage on to Servo and onto the inner 4.3mm ball
stud.
4. Install the Riders hand onto to outer ball stud of on the
handle bar.
Step 20: WIRING THE ULTRA MICRO SERVO IN THE RIDER'S HEAD
1. Take the spare servo and cut the wires off of it.
2. Cut the connector off of the ultra micro servo.
3. Solder the spare wire servo to the ultra micro servo’s wires. Use shrink tubes to seal the
connection. Coordinating the wire colors. (Black/Brown is Ground, Red is power, Yellow is
signal).
4. Run the wires through the body, down the neck and out the back by the hips.
5. Next, Cut the connector off of the both the lengthened ultra micro servo and the Hitec Servo
HS225BB and solder those wires together as well. Correlate the wire colors like before and use shrink tubes to seal the connection. This will make both the servo steering the motorcycle and the one in the head work in concert.
Step 21: CONNECTING THE ELECTRONICS
PARTS NEEDED:
(1) 7200KV or equivalent 4 pole brushless motor
(1) 25A or equivalent ESC (Electronic Speed Controller) (1) Radio Transmitter and receiver
BATTERY OPTIONS
(1) 1000mAh battery for Suzuki GSX-RR like Turnigy 1000mAh 2S 20C Lipo Pack with 70mm x 35mm x 13mm dimensions.
(2) 1000mAh battery for Ducati Draxter like Turnigy 1000mAh 2S 20C Lipo Pack with 70mm x 35mm x 13mm dimensions.
BECAUSE THE SUZUKI GSX-RR BATTERY IS INTERNAL IT USES A SMALLER BATTERY.
DUCATI DRAXTER RECEIVER HAS TO BE MOUNTED ON THE RIGHTHAND SIDE BOTTOM FAIRING.
The Battery for the Ducati fits underneath the bottom fairing with 3m automotive double stick
tape. The receiver mounts the Right Bottom fairing with 3m automotive double stick.
ESC
Motor
Receiver
Tramsmitter
Servo, esc (blue finned thing), receiver, and battery.
1. Attach the servo to esc
(speed controller) in Ch1 with the black wire (ground) aiming in the direction that pictured. (Yellow/Signal facing to the left)
2. Attach the speed
controller (esc) to Ch2. Ground wire should be in the same position as previous wire.
Step 22: ESC Wire Adapter
AGNE11170A Align JST Female Connector
If you’re using the GoolRC electronics then you will need
to the AGNE11170A Align JST Female Connector to connect to the battery connector.
Step 23: Go Riding!!!!
Place on the roll one bars with double stick and go have some fun!
Step 24: How I Feel After Winning the Grand Prize in the Design Now: 3d Printing Contest 2016
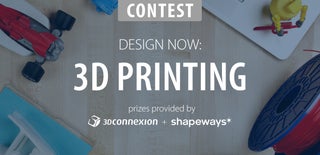
Grand Prize in the
Design Now: 3D Design Contest 2016
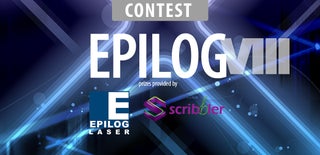
Participated in the
Epilog Contest 8