Introduction: 8 Planet Motorized Orrery - 3D Printed
For those not familiar with what an Orrery is I would like to offer a brief description. It is an apparatus used to illustrate the relative motion and sizes of planets to each other and their orbits around the sun. To put the orbit times in perspective I have listed the times for the planets below. The planetary orbits around the sun are in days/years.
Mercury- Orbits the Sun once every 87.97 days (.24 years)
Venus- Orbits the Sun once every 224.7 days (.61 years)
Earth- Orbits the Sun once every 365.26 days (1 year)
Moon- Orbits the Earth once every 27.32 days (13.37 times per year)
Mars- Orbits the Sun once every 686.98 days (1.88 years)
Jupiter- Orbits the Sun once every 4,332.82 days (11.86 years)
Saturn- Orbits the Sun once every 10,755.7 days (29.45 years)
Uranus- Orbits the Sun once every 30,687.15 days (84.01 years)
Neptune- Orbits the Sun once every 60,190.03 days (164.79 years)
Pluto- Orbits the Sun once every 90,553 days (247.91 years)
After discovering what an Orrery is I was surprised to find that a 3d printed version of any size was not common. I would like to mention that Dragonator has a nice 3D printed Orrery on Instructables. There are many finely crafted brass Orrerys available for purchase if you are so inclined to purchase one. I had discovered some very nice wooden Orrerys available as well. What I also discovered is how coveted the information is on how to make one. The craftsman who design these things do not like to share their information, particularly on what gear ratios they use achieve the correct relative planetary orbits around the sun. To speed this process up I created an Excel spreadsheet. To quickly change ratios I merely had to change the number of teeth in any or all of the appropriate cells and a ratio was calculated instantly. This saved an unbelievable amount of time. For anyone interested in playing with this I have included it in this instructable. Enjoy!
Attachments
Step 1: Materials and Tools You Will Need
Attached is a complete material list of items needed to build this Orerry. Also included are data sheets for some of the purchased items that you may find very helpful. The tools needed are as follows:
1. Phillips screwdriver (medium and small)
2. Flathead screwdriver (medium and small)
3. Small adjustable wrench
4. Drill bits- 1/8, 5/32, 3/16, 7/32, 1/4, 9/32, 5/16, 11/32, 3/8, 13/32
5. Utility knife
6. Soldering iron, and solder (preferred if available)
7. Wire strippers (preferred if available)
8. Dremel (preferred if available)
9. Glue gun
10. Pliers (used to hold threaded rod when turning nuts on).
Step 2: 3D Printed Parts Discussion
This project is not for the faint of heart. There are over 100 parts used in the build of this Orrery. One of my goals in designing this project was to build it as large as I could (within reason) using a 200mm x 200mm print bed. The actual print bed size is larger than this. As you can see from the photo I pushed the limits of the printer with the frames and the Mercury driver gear. You may or may not be able to move your limit switches enough to use the entire print bed. I printed these parts on one of my DIY printers and could move the limit switches out further. If necessary there are many companies out there that can print these for you for a reasonable cost. Pay close attention to the parts as you import them into your printing/slicing software. Some of the frames for example have spacers incorporated in them so that side will need to be faced up. Some of the gears are compound gears (2 gears in one part). They will also need to be positioned correctly.
With a couple of exceptions I printed all of the parts at 50% fill. Feel free to try a different amount. The exception to this were the gear spindles. I printed these at 100% because I wanted the strength. Caution here, if you print only one or two at a time the parts may not have enough time to cool a little between layers and they may sag. Use a cooling fan, slow the print speed down or print a few extra spares. The added number of parts will also allow more time between layers. The planets can be printed 20-30% fill. The lighter they are the less sagging of the longer planet support rods you will have. I also recommend using supports enabled when printing to improve the way they look on the bottom side. The Earth's Moon was not printed. I used an airsoft plastic bb for this. It was 6mm in diameter. You can use anything that is approximately this size. Remember that you will have to drill a small hole in it for the support.
I used drill bits to clean-up the holes in the printed parts. 3D printed parts in general are not super precise. I designed the parts with the exact hole size knowing that they would be slightly smaller. It was important to have a nice fit for the brass tubes. All of the other holes in the gears and frames on the driver side as well as the secondary gears are 1/4". Make sure to run the bit through the parts straight, otherwise your gears may wobble.
You will notice that the printed parts for the motor and mounting brackets are different than what the video shows. The motor itself is also different. When I made this originally I used a motor I had laying around. When I decided to post this I knew I would have to buy something so I could provide the part number and information to order it by.
I have tried very hard to make sure that the fits are good and minimal work will be needed in cleaning the parts. I would however like to make you aware that the gear teeth will need a little cleaning up on the print bed side, especially if you use larger print nozzle sizes. Since you want good adhesion of your part to the print bed the first layer is usually squished down pretty good. This will create a raised area along the teeth. If you are having issues with warping and use a brim around the edge you will of course need to clean the edges up. Since it is important the gear teeth mesh well this will need to be cleaned up a bit. I like to use a utility knife by scraping it (not cutting) along the edge of my parts. I have added a radius along the edges to help some with cleanup.
One final word about the printed parts. If you will notice in the video I have printed each planet, planet arm and gears the same color. I thought it would be nice to see which gears were actually driving each of the planets. You certainly do not have to do this, I just thought I would mention it.
Attachments
Orrery 3D Printed Parts List 1 of 4.pdf
Orrery 3D Printed Parts List 2 of 4.pdf
Orrery 3D Printed Parts List 3 of 4.pdf
Earth ring bottom spacer.stl
Orrery 3D Printed Parts List 4 of 4.pdf
Orrery 3D parts.zip
Orrery Autocad files.zip
0.5 frame spacer.stl
0.9 gear spindle.stl
0.9 neptune gear spindle.stl
Saturn Driver Gear Bottom Spacer.stl
Saturn Driver Gear Top Spacer.stl
Step 3: Let's Start Building - Frames
Assuming at this point you have purchased all of your materials, printed all of the parts and gathered the tools you are ready to start the assembly. Listed below are the first steps.
1. Bolt Frame 1 Driver Side Frame to Frame 1 Driven Side Frame using 4-40 x 1 1/4 lg. machine screws and nylon locknuts.
2. Repeat for Frames 2, 3 and 4. Completed frames will resemble image shown.
3. Install Frame Foot onto one end of #10-24 x 8 5/8" threaded rod and then install #10 washer followed by a 10-24 nylon locknut. Screw nut on until 1/8" of threads are showing. Repeat this for the remaining six rods. Shown in image above.
4. Slide the threaded rods up through the bottom of Frame 1 assembly rod holes. See image above.
5. Secure center Frame Foot with a #832 x 3/4" machine screw, flat washer and nylon locknut (washer and nut on foot side).
5. Set this aside for now.
Step 4: Driver Gears - Mercury to Mars
1. Slide the gears and spacers onto the 1/4" Driver Shaft as shown in image. Additional notes for clarification are on the images. These items will need to be glued together. Apply a little Goop between each gear and spacer. All of the gears that will be mounted to the driver shaft must turn together as a single unit (no slipping). The order of installation is:
Mars Driver Gear, Mars Driver Gear Bottom Spacer, Earth Driver Gear, Earth Driver Gear Bottom Spacer, Venus Driver Gear, Venus Driver Gear Bottom Spacer, Mercury Driver Gear, Mercury Driver Gear Bottom Spacer. There should be 1/4" of the Driver Gear shaft extending past the Mercury Driver Gear Bottom Spacer. After gluing and assembling set aside to allow time for glue to dry.
Step 5: Driven Gears- Mercury to Mars
It is now time to prepare the brass tubes for the gears on the driven side. If you have not done so already it is time to cut the brass tubes to the lengths specified on the "Cut Chart" located in the materials section. The tubes needed in this section are Mercury, Venus, Earth and Mars.
It is important that the gears are attached to the tubes in a manner that will not allow the gear to spin on the tube. There are a couple of ways to address this. Use epoxy only or solder a small bead on the side of the brass tube that will act as a key to prevent slipping. The bead is placed so that it will be approximately in the center of the gear body. Using a dremel or other means notch out a small area just big enough to allow the solder bead to fit into it. For added measure if you wish you can also add some epoxy. This is optional. Most of the tubes will need to be modified this way to guarantee that no slipping will occur. You can try epoxy alone however I do not recommend it with the exception of a couple of planets. These will be addressed later. For the Sun tube place the bead at the very end of the tube. Do not exceed 1/8 distance from end. The Sun tube will be inserted 1/8" into the bottom frame. This will be done later. See the photos above for solder reference .
Once the glue has set for the "Driver Gears- Mercury To Mars" it is time to assemble the "Driven Gears- Mercury To Mars" as well as the Sun. Glue spacers to the bottom of the mating gear. Be careful not to get glue in the end of the tubes. Insert the appropriate tubes into mating gears/spacers. Insert the tubes into each other as shown in the illustration and allow them to stack against each other. Put this aside and allow them to dry.
Step 6: Prepare Earth Gear Ring and Frame
Assemble the Earth Ring Gear Segments 1 and 2 using (8) #4-40 x 1 1/4 lg. machine screws and nylon locknuts. There are 2 of each part. The gear segments need to be assembled so that the ends with 1/2 tooth mate together to make a complete tooth. Make sure that the assembly is flat after it is bolted together. If not some cleaning of the mating surfaces may be needed. See illustration above.
Next prepare the earth ring tube. Temporarily mount the Earth Driver Gear Bottom Spacer on each side of the Earth Ring Half Frame. Slide the tube into spacers and frame. Find where the approximate center will be on the tube and solder a bead there. Notch the frame with a dremel for the bead and notch one of the spacers as well. Apply glue between the spacers and the frame and glue them together. Slide the tube into the notched spacer, frame and second spacer. Be careful not to get glue inside the end of the tube.
Step 7: Prepare Remaining Tubes and Driven Gears
Mars (orange gear)- Part needed is the Mars Driven Gear and Mars Driven Gear Top Spacer. Prepare tube by soldering bead as described earlier. See illustration.
Jupiter (gray gear)- Part needed is the Jupiter Driven Gear only. Prepare tube by soldering bead as described earlier. See illustration
Saturn (black gear)- Parts needed are Saturn Driven Gear, Saturn Driven Gear Top Spacer and Saturn Driven Gear Bottom Spacer. See illustration.
Uranus (tan gear)- Parts needed are Uranus Driven Gear and Uranus Driven Gear Bottom Spacer. Prepare tube by soldering bead as described earlier. See illustration
Neptune (white gear)- Parts needed are Neptune Driven Gear, Neptune Driven Gear Top Spacer and Neptune Driven Gear Bottom Spacer. No bead soldering needed. Use glue between all mating surfaces. Do not get glue into the tube. See illustration.
Step 8: Earth Arm Assembly
Earth Arm (blue)- The parts you will need are Earth Arm, Earth Moon Gear 1, (2) Earth Mon Gear 2 and 3, Moon support, Airsoft BB, (2) Earth Moon Spindles, Earth Moon Gear 3 Retainer, (2) #4-40 x 1 1/4 machine screws and nylon locknuts. Attached is a drawing of the Moon and Earth supports. Make these parts before assembly.
1. Install the #4-40 machine screws and nylon locknuts but do not tighten. See illustration 1.
2. Drill small 1/16 hole in Airsoft BB and in the side hub of Earth Moon Gear 3. See illustration 2.
3. Glue moon support/moon to the gear hub.
3. Using epoxy attach Airsoft bb to top of Moon Support and at the bottom where support enters the side of the gear hub. Allow to dry.
4. Glue spindles and gears as shown/noted in illustration 3. Allow to dry.
5. Drill in top of Earth Spindle for the support. Glue Earth support in hole. Glue Earth to support.
Step 9: Stacking Gears and Frames- Mercury to Mars
Now that the tube assemblies have been completed and the glue has dried we will continue with the assembly. Starting where we left off with the frame assembly that was completed earlier.
1. Install the Driver Gears- Mercury To Mars on the left side (driver side) by inserting the 1/4" shaft at the base of the gear stack into the 1/4" hole in the center of the driver side frame as shown in illustration.
2. Next notch the driven side frame in the center hole to accept the beaded Sun tube. (Sorry no picture of that). See the illustration for hole location. The tube will need to set in the frame 1/8". Use epoxy here by putting a little in the hole but do no allow any to get on the flat surface of the frame.
3. Install the Mercury, Venus and Earth Driven gear assemblies.
4. Install (3) 1.25 Frame Spacers on the threaded rods where the Earth Half Frame is located. See illustration.
5. Install 2.00 Frame Spacers on the remaining threaded rods.
6. Install the Earth Half Frame over the threaded rods with the (3) .5 Frame Spacers.
5. Install the Mars Driven Gear assembly and allow Sun tube epoxy to dry.
Step 10: Stacking Gears and Frames- Frame 2 and Jupiter Gears
1. Install Frame 2 assembly over the threaded rods.
2. Install Jupiter Gear Driven tube assembly.
3. Put some glue into the holes only in frame at Jupiter Gear Driven 2 and 3-4 position. Do not get any on the surface of the frame. Insert .9 Gear Spindles in both locations. Twist while you insert. This will help to coat the spindle shaft inside the hole.
4. Install Jupiter Gear Driver 1 onto 1/4" shaft all the way down to the frame.
Step 11: Stacking Gears and Frames- Frame 3 and Saturn Gears
1. Flip frame 3 assembly upside down. Glue Saturn Gear Driven 2-3 bottom spacer to top of frame under Saturn Gear Driven 2-3. You cannot see this spacer in the photos. Insert some glue into the holes as shown and place Saturn Gear Driven 2-3 and 4-5 into position and insert 1.25 Gear Spindle through each gear into the hole. Install gear 2-3 first, then gear 3-4. Make sure no glue gets on the surface of the frame. Please note in the illustration that the smaller secondary gear is facing up in both positions. Twist spindle as it is inserted into the hole. Allow to dry.
2. Install (7) 2.13 Frame Spacers over the threaded rods.
3. Install Saturn Driver Gear Bottom Spacer. Apply glue to the top of Jupiter Driver Gear and slide spacer over the 1/4" shaft.
4. Apply glue to the top of Saturn Gear Driver 1 and install Saturn Driver Gear Top Spacer.
5. Install Saturn Gear Driven 6 tube assembly over the tubes into position. See illustration.
6. Slide Frame Assembly 3 over the threaded rods with the gears on bottom. Carefully slide into position making sure the teeth mesh for proper installation. The frame should set evenly on top of the frame spacers.
Step 12: Stacking Gears and Frames- Uranus Gears
1. Install Uranus Gear Driven 6 tube assembly.
2. Glue Uranus Gear Driven 4-5 Bottom Spacer to top of frame as shown in illustration.
3. Insert glue into holes for Uranus Gear Driven 2-3 and 4-5.
4. Install Uranus Gear Driven 4-5 and insert 1.25 Gear Spindle. Twist as it is inserted.
5. Install Uranus Gear Driven 2-3 and insert 1.25 Gear Spindle. Twist as it is inserted.
6. Install (7) 2.50 Frame Spacers. onto threaded rods.
7. Allow glue to dry.
Step 13: Stacking Gears and Frames- Frame 4 and Neptune Gears
1. Apply glue to the top of Uranus gears and install Neptune Driver Gear Bottom Spacer.
2. Apply glue to the top of Neptune Driver Gear Bottom Spacer and install Neptune Driver Gear 1.
3. Apply Glue to the top of Neptune Driver Gear and install Neptune Driver Gear Top Spacer.
4. Flip Frame 4 assembly over and insert glue into the holes for Neptune Gear Driven 2-3 and 4-5. Make sure not to get glue on top of the frame.
5. Position Neptune Gear Driven 2-3 and insert 1.00 Neptune Gear Spindle. Secondary gear (small gear) is facing up. Twist spindle as it is inserted.
6. Position Neptune Gear Driven 4-5 and insert 1.00 Neptune Gear Spindle. Secondary gear (small gear) is facing up.Twist spindle as it is inserted.
7. Allow to dry.
8. Install Neptune Gear Driven 6 tube assembly over existing tubes into position resting on top of Uranus Gear Driven 6.
9. Install Frame 4 assembly over threaded rods with gears facing down.
10. Install #10-24 nuts to the top of the (7) threaded rods. Do not over tighten.
Step 14: Install Planet Arms and Earth Ring
1. Install the Planet Clamp arms in this order: Neptune, Uranus, Saturn, Jupiter and Mars. Use a small screw driver on clamp side to open it up a little to help slip in over tube. Be careful, do not open too far or it may break.
2. Install Earth Ring Bottom Spacer
3. Apply glue to the top of Earth Ring Bottom Spacer and install Earth Ring Assembly. You can glue this to the shaft. If necessary solder a bead on the tube for extra locking hold. Notch the Earth Ring for the solder bead. Apply a little epoxy inside the notched hole for the bead wouldn't hurt. Remember to align the ring so it is turned straight with the arms. It just looks better. Make sure the ring is level and allow to dry.
4. Install the Earth Arm assembly. Use a small screw driver if necessary to aid in getting it over the tube.
5. Install Venus and Mercury Planet Clamp arms.
Step 15: Mount Motor, Brackets and Switch
1. Mount motor to Motor Base using (6) 3mm x 12mm machine screws and lock washers.
1. Mount Motor Drive Gear to motor shaft. The small hub should be toward the motor. The gear should be flush with the end of the shaft.
2. Attach Motor Base to Motor Mount using (2) 8-32 x 1 1/4 machine screws, washers and nylon locknuts.
3. Attach the assembly between frames 1 and 2 as shown using (2) #8-32 x 2 3/4 machine screws and nylon locknuts. Make sure the drive gear is engaged with the Mercury Driver Gear.
4. Insert toggle switch into Enclosure Cover and install locking nut.
5. Solder the wires between motor, switch and power supply connection as shown. See the attached wiring schematic for additional reference. The wires leading to the motor from switch will exit the small hole at the back of the Switch Enclosure. Solder the wire leads to the motor last. I used connectors between the motor and switch however this is not necessary.
6. Install Switch Enclosure Cover using (2) #4-40 x 2" machine screws and nylon locknuts
7. Apply glue to the top and bottom of the Switch Enclosure and insert between Frame 1 and Earth Half Frame in the approximate location as shown in illustration.
8. Install Motor Connection Cover to the top of the motor (not illustrated).
Step 16: Planet Supports and Planets
1. If you have not done so already cut and bend the 1/8" dia. rod material following the specifications on the Cut-Bend Chart. Paint the supports with Satin Black spray paint and allow to dry.
2. Carefully insert the supports into the mating planet clamp.
3. Carefully mount the planets to the mating support rods.
4. Print out the Orrery Calendar Dial. This is larger than 8 1/2 x 11". You can take the digital file to somewhere like Staples and have it printed and laminated. Cut away inside and outside excess plastic. Attach to the top of the Earth Ring Gear using adhesive.
5. Print out the Jupiter Ring and also have it laminated. Cut out the inside and outside excess material and slip over the planet at an angle.
6. Plug in the power supply. The toggle switch will drive the planets in either direction. Center position is off.
7. Install #4-40 x 3/4 machine screws and nylon locknuts into the clamp side of all of the planet clamp arms and lightly snug if you didn't do this earlier.
7. You are now ready to go!!
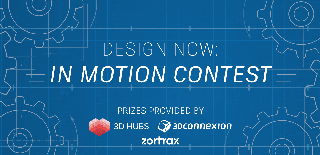
Grand Prize in the
Design Now: In Motion Contest
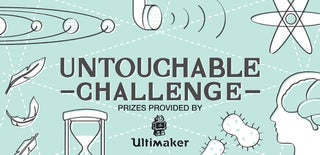
Runner Up in the
Untouchable Challenge