Introduction: Centrifuge Built From VCR Parts
A centrifuge is a very useful piece of equipment for isolating aquatic organisms. Centrifuging a sample of water containing micro organisms will drive them to the bottom of the container, where they become more concentrated and easier to manipulate. A high speed laboratory model costing several hundreds of dollars isn't necessary for the purpose, something much simpler will do the job quite adequately. At the most basic, you can just tie a piece of cord SECURELY to the container and whirl it around your head. You can easily generate a centrifugal force of 10 G with this method ( but do it outside in an open area, where nothing will get damaged if it comes loose ! )
A safer and more convenient solution is a motor driven apparatus, such as the one I built using parts from an old video recorder. It cost me only a couple of dollars for the plastic bowl housing the rotor head and some PVC pipe fittings, all the other parts were obtained from my “junk collection” of defunct VCRs and other “dead” electronic gadgets. If you don't have a dead VCR lying around, just ask a few friends and you are bound to find someone who will give you one. The parts required are the video recorder spinning head mechanism, plus the video cassette loading motor with its drive pulleys. Some newer VCR models may not have belt drives, a good alternative source for these components is an old inkjet printer, but these usually have stepper motors which require a special driver circuit to power them. If you can find an ordinary DC motor which will fit the pulleys it is much simpler than trying to get the stepper motor working. You will also need a 12 Volt DC plug pack. It should be capable of supplying at least 400 milliamps, otherwise it will probably burn out before long. If you need to, you can buy a new one for about $ 5, but these are very common items found in garage sales for only one or two dollars.
Step 1:
Construction of the Centrifuge :
The VCR parts were extracted along with their mounting brackets and screws, keeping the PCB with the cassette motor drive connections intact. The wiring to the video head rotor is not needed and can be disconnected. Figs 1 & 2 show the video head as removed from above and below, Figs 3 & 4 show the disassembled rotor components, and Figs 6 & 7 the reassembled configuration. The first step is to remove any superfluous bits from the video head rotor, including the PCB and the stator windings underneath ( Fig 3 ). You need to take off the flywheel with the magnetic ring to get at the inside of the rotor.
Step 2:
At this stage, prepare an old CD by cutting out the centre section to fit over the bottom section of the rotor. Drill 3 small holes in the CD and the bottom rotor section to take small self tapping screws and fix the CD to the bottom rotor section as shown in Fig 5.
The two halves of the rotor are separated and the top section refitted upside down, as shown in Figs 6. The magnetic sensor heads and their wires can also be discarded. Save the screws from the underside ( which is now the upper side ) of the top rotor section.
Step 3:
Replace the flywheel also in the reverse orientation to its original position. You should now have an assembly which looks like Fig 7, seen with the assembly turned upside down..
Depending on the model of VCR, you should have a mounting frame attached to the video head rotor with 3 or 4 screw fixing points. You will need to make up a base with some brackets or posts to allow the rotor to be mounted in a horizontal position. In the video recorder, the rotors are mounted at an angle to the horizontal to allow the tape to be scanned diagonally, so the mounting points will usually need to be at varying heights to get the rotor level when it is used as a centrifuge. Try to get it as accurately level as possible, otherwise your centrifuge will wobble wildly when it is running. I used mdf board for the base and two posts, and a metal bracket for the third mounting. You can use some washers under the mounting frames to adjust the level accurately with a spirit level / bubble level .
When the rotor assembly is mounted on the base board, the drive motor and its pulley will need to be located so that the drive belt runs around the detachable collet just above the reversed flywheel. The driving pulley and collet must be aligned in the same plane, otherwise the belt will be thrown off when the motor starts. Since the drive motor and pulley configuration will vary greatly between different models of VCR, I will not provide any specific details for this step, you will have to figure it out to suit whatever you are using. Fig 8 below shows how I arranged mine. By the way, if you don't have a drive belt of suitable length, a strong rubber band will also work.
Step 4:
The next step is to cut a hole in the base of the centrifuge bowl to fit over the rotor, and then fix it to the CD underneath with some small screws. Figs 9 & 10 show the bowl fitted in place. Make sure the bowl is accurately centred so that the spinning tubes can not touch the sides of the bowl. ( Of course, you need to get a bowl of the right diameter to accommodate your centrifuge tubes in the first place. I used a plastic microwave cooking cover )
Step 5:
To complete the centrifuge you will need to add the trunnions and rings to carry your centrifuge tubes. The tubes I use are 100 mm x 12 mm diameter, so I made two tube carriers from black plastic irrigation tubing and fitted them with trunnions as illustrated in Fig 11. The trunnions are formed from a threaded PVC collar and two self tapping screws. A piece of foam rubber is pushed into the bottom of the tube carriers to cushion the glass tubes, and another screw is inserted across the bottom to hold the tubes in place. The aluminium bracket screwed to the top of the rotor has holes for the ends of the trunnion screws, as seen in Fig 12.
To use the centrifuge, I fill the centrifuge tubes to about 15 mm from the top with the liquid, making the levels in each tube as near to equal as possible. They are inserted into the carrier tubes and a piece of thin mdf board is placed on top of the bowl as a lid, which helps to reduce the wind resistance. The centrifuge is run for about 5 minutes at 250 rpm, which generates a force of about 6 G. This is adequate to concentrate aquatic micro organisms without damaging them. It will need to be clamped to the work bench so that it doesn't run around and develop uncontrollable vibrations. Please be aware that this apparatus will cause some major damage to your fingers if you put them inside the bowl when it is running. Be very careful !
Speed Control
I did not use a speed control on the motor, because the centrifuge works quite well for my purposes at the maximum speed. Depending on the motor that you use, a speed control may be useful. This can be easily added through a LED dimmer control, shown above. These can be found on eBay for about $ 3. The wiring is very simple, with two terminals for the 12 V DC input and two terminals for the regulated output.
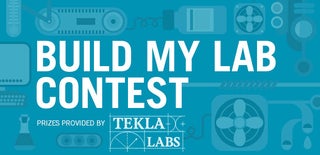
Participated in the
Build My Lab Contest