Introduction: Acrylic Skeleton Clock
This is a clock made fully out of acrylic!
This was originally was my year 13 mechanical engineering college project, we had to research, design and build a project for a stakeholder, this including lots of recording so there is no shortage of photos.
the use of acrylic for a main building material was decided to make a new feature piece, it also is a simpler material to work with, with the limited machinery you find in a college workshop. The clock is fully my design and took about 13 weeks with about 16 hours a fortnight. I wanted something a bit different from the standard clock with three hands and circular design, i wanted to included the look and mechanical workings in the old grandfather and skeleton clock. This is where the open design comes from so all workings are visible so you can see how it operates.
because of its design out of all flat material this clock could easily be all cut out with a laser or CNC cutter, or even 3D printed ,making production quicker and more accurate. Because Autodesk Inventor was used to design the clock, all the files needed very little work before been sent to a cutter or 3D printer.
As the title my suggest the clock is mostly 3mm acrylic, this could be any color weather its transparent or opaque, its your choice. the only other materials are:
- 5mm shaft (brass, steel or other depending on what you fancy)
- back can be thick acrylic, hard wood, metal of any type, or any other strong material
- .Lead, or almost any heavy material for weights, depending on what you want it to look like and how good your cutting of gears are.
- Nylon or other twine for weights.
- Acrylic cement
- Dome nuts
- 80mm diameter aluminum stock for winding barrels. (could be made out of wood)
- 30mm diameter aluminum stock for pulleys (Could be wood)
TOOLS
- Scroll saw
- small hand files
- band saw (not necessary)
- dremel (only needed if engraving numbers, stick on or painted numbers can be used)
- Belt sander (Not necessary, everything can be hand sanded)
- Computer ( to print out gear templates)
- Lathe for metal and some wood work (depends on your changes to the design)
Step 1: Design
the first idea were done on a whiteboard but were developed with Autodesk inventor, a free software available to student or a relatively small price for other people. it enables the user to complete complex 3D and 2D designs cover all functional and atheistic needs. Because gears are a pain to do with the software, in the CAD designs i didn't do the teeth as they will be in the clock, i just had them rounded. This means i could get all the sized right and do tests but i didn't waste lots of time calculating gear teeth. Once i knew what size gears i needed, I used an online gear template calculator that gave me the templates to create the gears.http://woodgears.ca/gear_cutting/template.html
Here is the Autodesk inventor CAD files if anyone can use them. I don't know how useful they will be as I only used them for planning the layout, not for templates, so they would need a fair amount of work to be laser cut. https://drive.google.com/folderview?id=0B4V1Ma-qByctOGprQ0NWV3Nac00&usp=drive_web
I would recommend getting the gear templates for each gear and laser cut them, then use the CAD files just for the frame, but check it has the right dimensions between holes as your gears might not run nicely otherwise.
Attachments
Step 2: Gear Construction
The acrylic gears were the most time consuming part of the build. each gears was cut by hand on a scroll sow then filed down to the final shape. There is over 400 teeth that are individually shaped so this will take time.
The fist step is to print out the gear templates from the gear template generator found in the design step and the sizes of the gears can be found at this link https://drive.google.com/file/d/0B4V1Ma-qByctNG1hRGQ2aGd4blE/edit?usp=sharing. Glue the template onto the paper covering on the acrylic making sure it is flat and not warped.
Now cut around the template with a scroll saw, taking care not to go too close to the line, as filing can clean this up later.
The filing stage is the longest and needs the most care. the first filing take the gears down to the black like on the template, this gives you the finished gear. The next bit of filing is done after the clock is assembled, and is done to remove any tight spots to let the gears run freely.
I would recommend if you have access to a laser of CNC cutter the template could be directly used and would decrease production time dramatically as well as no need for the filing.
Step 3: Frame
The frame of this clock needs to be robust to support the weight of the pendulum as well as looking good, as it will be exposed. wood looks nice but wouldn't work that well for a clock as with temperature and moister changes, wood moves which would mean the gears wouldn't mesh properly. I ended up finding a hard plastic that was once used for hard wearing bench tops, it had been made to be a substitute for granite and so looked quite nice.
The only other parts of the frame are the shafts that the gears rotate round and a clear layer of acrylic on the front of the clock and one in the center, acting as a sort of spacer, these have the same holes and shape as the back piece so the same template can be used. You will see two different frames in this clock, the first one is grey then the new one is white. I changed half way through because i changed the pendulum. If you follow the design the old back will work fine. The shafts are held in the base with a friction and a bit of super glue, i didn't do this until the clock was running as the frame held the shafts in by just friction and i ended up dismantling it multiple times. Like the gears this back could be laser or CNC cut which would reduce production time dramatically, and make it far more accurate.
Step 4: Bearings
For the gear train to rotate freely it was decided to use bearings. The bearings are ball races out of a hard drive and needed to be glued into the gears straight.
Super glue was used to attach the bearing into the gears and the shaft was used to keep them straight and aligned in the gears while gluing. First all the gears were already drilled out to 5mm (the same diameter as the shafts) so the shaft fitted into the gears tightly. The bearing holders which are round pieces of the clear plastic, cut about 3mm bigger than the bearing with a 13mm hole board in the center which was a snug fit for the bearings. The bearing were then pushed into these holders without glue and along with the required gears and spacers ( clear plastic with 5mm hole board in the center, to space gears) were assembled onto a 5mm shaft to keep them all aligned.
To keep the gears perpendicular to the shaft while gluing, a 5mm hole was drilled in a flat machined piece of wood, with the drill press. This gave a vertical hole that the shaft with all the gears and spacers were pushed onto, went into. Now the glue was places between the required gears and spacers, being careful not to glue the bearing or the shafts in, then they were pushed together onto the flat surface of the machined wood the shaft is pushed into. This ensured the gears are all perpendicular to the shaft, and that they would rotate without a wobble.
After 10min to let the superglue set, the shaft and bearing were removed from the gears and the original 5mm hole which kept the gears aligned, was drilled out to 6mm so only the bearings came into contact with the shaft, this means there is very little friction on the shaft. The bearings and shaft are now put back in and the bearing are glued in to prevent them coming off. Use the shaft again to keep the bearings straight while gluing into the gear.
It was important before the glue fully dry’s on the bearing to make sure when the gear is spun; the gear does not wobble sideways and is also centered. if it isn't, take out the bearings and try correcting the errors.
For the power gears, which are the first gears in the gear train, they can’t be mounted on ball races unless you have a 3mm thick bearing with a 12mm inside diameter. Small bronze bearing are made for this part. These were done on the lathe and had a 12mm inside diameter for the ratchet and were just over 3mm thick so it stopped the ratchet or gear scratching the clear plastic frame. the outside diameter was 18mm and was a press fit into the clear plastic frame.
Step 5: Pendulum
The pendulum was pretty simple, it was a 2m long piece of 8mm diameter aluminum rod with a thread in one end for attaching to the pivot at the top of the clock. Aluminum probably wasn't the best for a pendulum as it changes size with temperature, which will vary the timing but using the clock in a room out of direct sunlight, means temperature variation will be little.The pivot on the end is a ring of aluminum bolted to the top of the pendulum with a pin in the top that the pendulum pivots on. The photos probably explain this better. The pendulum bob was two layers of the clear acrylic plastic, bolted either side of the pendulum. This could do with being a little bit bigger to improve the timing but i haven't bothered to change it.
Step 6: Power!
The power for this clock will be coming from gravity though the use of weights and pulleys. I decided i wanted the main weights for the clock to be wooden, to keep in the same design as the house and the style of clock, but for this to work a dense wood is needed so the size of the weights can be kept down, for this issue i used iron bark. In the end wood didn't end up being heavy enough to power the clock so i used glass weights full of water, which nicely kept in the clear theme of the clock. If you still wanted a wooden look you could make your clock extremely efficient or hollow out the wood and fill it with lead. My plan for glass weights were made by cutting the parallel section out of a clear wine bottle, then caped with aluminum and filled with water. Theses will give me plenty of weight to run my clock and also kept in the clear theme of the rest of the clock.At this stage i am yet to come across two identical clear bottle so I am just using lead weights which look terrible, but keep the clock running well.
The aluminum drums are the spools which the wire is wound onto to power the clock, they consist of a spiral around the outside to keep the wire nicely coiled and a recessed face which is used as a ratchet and will be covered in the next step. For his part you will need a lathe and good lathe skills and it involves threading the spiral. The inside of the drums were hollowed out so that it was lighter, and didn't add so much weight to the clock. this could be left out if you didn't have access to the required tools.
Step 7: Ratchet
The ratchet is the part of the clock that allows the weights to be re-wound at the end of each week, without the whole clock having to run backwards. The ratchet rotates on the shaft of the power drums and the brass bearing that is in the second layer of the frame. This means the shaft for the drums can run though the ratchet for a key to be fitted onto for winding. The ratchet has three main parts, the main body which the fins attach onto as the ratchet in the power drums and a threaded bolt which is threaded into the center of the main ratchet to lock the power gear on, and it also has a 5mm hole in the middle to rotate on the shaft of the power drum.
To attach the fins on, two flats were milled out in the main ratchet and the fins which are thin strips of spring steel then were riveted on then bent back so they would lock into the power drums. Make sure you use thick enough fins otherwise they can bend around and allow the weights to go crashing to the ground.
The drum has eight holed drilled in the front, with the center lathed out so it leaves eight semi-circles, this is where the ratchet slots in so it is recessed inside. The images show this part very well and the design is shown in the full project found of the introduction page.
Step 8: Markings
A clock isnt a clock without numbers. theses were done by hand with a dremel and a template to trace around. To get the numbers you want, print out the size and font of the words/numbers and place them under the parts you are engraving onto. if the material you are engraving onto is opaque, either glue the template on-top or tape it down if you don't want to damage the surface and engrave though it. When engraving clear materials with the template underneath, make sure you line the numbers up right as the low angle you use when engraving, moves the image you see along. I did a lot of practice on scrape plastic before you do parts on your real clock, as practice helps a-lot! I was quite please with how the numbers came out, the were neat and showed up well against the red background that the clock was going to be mounted on. If you didn't want white numbers, the rough recessed surface of the engraved numbers is easily painted.
Step 9: Assembly
During assembly the gears are modified to make sure there is no tight spots where the gears could bind. this is done by carefully filing any gear teeth that don't mesh properly. This was every gear and i ended up going over each multiple times to get it right! to make sure the gears don't slide along the shafts you could lock tight the bearing onto the shaft, while i was testing though i just used a lot of washer so i could adjust the distances. The washers also had another good effect of making the spacing of the frames easy, so when i got the final distances i replaced the washed with aluminum spaces which were a lot neater.
Step 10: Changes
During construction i came across a few issues or things i wanted to change. One of the major ones was the clock wasn't running efficiently on the original escapement, which was attached straight to the pendulum. I altered this so it used a yoke, which increased the leverage on the pendulum which increased the power applied to each swing. With this change, it meant i had to extend the back frame up to accommodate mounting the pendulum higher. When i re-made the back, apart from lengthening the top, i also changed the shape purely for aesthetic purposes. This you can make almost any shape you want, as long as it has the required holes. The design doesn't include the changes to the pendulum, but if you build the clock good enough you shouldn't need it, i tried mine after i got it running and it worked fine.
Step 11: Finished Product
The clock may not be the most accurate but after been calibrated, it could keep good time between winds. I was happy with the final product and it seemed to not have too many major issues. Being made out of acrylic means it will never be the most efficient or accurate clock, but it does work and makes quite a feature piece in my house.
I would highly recommend using CNC or laser if you have access, as it will make a far better clock overall, much faster than by hand. This project did take a lot of patience but the results I'm more that happy with.
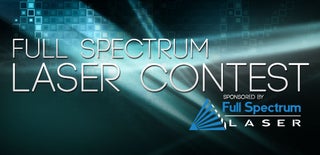
Third Prize in the
Full Spectrum Laser Contest

Participated in the
Gadget Hacking and Accessories Contest