Introduction: Affordable Rock Tumbler
This is my affordable rock tumbler designed to tumble 3D printed parts, printed with ColorFabbs metal filled filaments (BronzeFill, BrassFill, CopperFill). It is also possible to add a 'golden' shine to regular PLA when the parts are tumbled with brass screws. It should be possible to build this tumbler for less than € 40.- which makes it much more affordable than 'professional' tumblers that can do nothing better than this one ;-)
With the 110mm drum it turns with approx. 22rpm - feel free to adjust the speed using different gear wheels (see note below).
You can go with a drum of your choice (i.e. old tins, etc.) but I found that PVC pipe couplings that are sold in hardware stores are perfect and cheap. This tumbler is designed to run with either diameter of coupling like 110mm, 125mm or 160mm (latter not tested yet). The 110mm drum is large enough for most of my parts and should be the starting point for your first try. For those who like a rubberized drum it is a good idea to print the inset for the drum with flexible filament.
Parts List:
- Geared Motor: 12V, 1:50, 100 RPM, 20 Ncm regularly called RB30 or RB35, available at Conrad, ebay, etc.
- Threaded Rods M8: 4x 250mm, 1x 275mm, 1x 235mm
- 29x 8mm Hex nuts, 1x 8mm locking nut & a couple of 8mm washers. 1x 3mm nut and 1x M3 x 20 screw (for the smaller gear wheel. 3x M3 x 16mm screws for the motor + 3 M3 washers.
- 4x O-rings 22x2,4mm
- 3D Printed Parts:1x Frame left, 1x frame right, 2 gear wheels and 4 pulleys
- 1 Power source 12V, 1A (actually 500mA should be enough) + 1 power cord, long enough, to be soldered to the motor and connected with the power source.
- 4x ball bearings 608zz
If you want to go with the suggested drum:
- PVC pipe coupling + 2 caps.
- 3D printed inset for the socket
The files for the 3D printed parts are available here: Rock Tumbler STL Files
The gear wheels are designed with this really cool customizer: http://www.thingiverse.com/thing:6544
Thanks to ScribbleJ.
Step 1: Cut the Threaded Rods
Cut the threaded rods to the following lenghts:
4x 250mm for joining the 2 frame parts
1x 275mm (this one will carry the larger gear wheel)
1x 235mm (this one is the second, free rotating, axle)
Step 2: Attach the O-rings to the Pulleys and Loose Fit the Pulleys to the Axles
Attach 1 o-ring to each pulley
Loose fit the pulleys to the axles (you need the 235mm and the 275mm axle in this step)
See photo for the rough position of the pulleys. The distance between depends on the barrel you choose.
Slightly tighten the M8 nuts.(Not to tight yet, in order to adjust th eposition later if necessary)
Step 3: Push Fit M8 Nut Into Larger Gear Wheel
Step 4: Push Fit Ball Bearing Into Frame Parts
Carefully push fit the bearings into the frame parts. Sometimes it is helpful to use a piece of scrap wood in order to push it nicely flat.
Step 5: Add 4 M8 Nuts to the Remaining Threaded Rods
Step 6: Attach the Threaded Rods to the Right Frame Part
The right frame is the one where the motor is *not* attached. Top is where the frame parts are longer!
Step 7: Push the Other 2 (moving) Axles Through the Ball Bearings
Step 8: Attach the Left Frame Part to All Rods
This step might be a little bit tricky. It helps if you slightly tighten the hex nuts on the right side
Step 9: Attach the Motor to the Frame
But not tighten the motor screw now
Step 10: Assemble the Gear Wheels
The smaller gear wheel (with a M3 hex nut + M3 x 20mm screw) goes on the motor axis
The larger one goes on the longer axle. Loose fit the gear, mark motor position and detach the smaller gear wheel. Now fix the motor on the marked position. Re-assamble the smaller wheel to the motor while simultaneously push the longer axis parallel.
Now let the motor run for a few seconds in order to check everything works fine. May be you have to re-adjust the distance of the gear wheels.
If everythings works well tighten the gear wheels and all threaded rods that are connecting the frames.
At least you should counter the nuts on the moving axles. Allow enough space that the axles can rotate freely.
Now you can finally check the distance between the pulleys and tighten the nuts.
Step 11: Let's Get Ready to Tumble :-)
Ok, you're finished with the assembly, now lets tumble:
First of all I recommend to drill a hole into each of the caps that close the socket. One cap will always stay into the socket. This one schould get a 2-3 mm hole. The second caps needs a larger hole in order to attach a M8 or better M10 screw with some washers on it which will help to open the barrel.
Add your 3D printed parts into the barrel and add a whole lot of different brass screws.
Close the barrel and let the tumbler run for a minimum of 6 hours (better is 12 hours or more - depends on the part to be tumbled)
Step 12: Have Fun With the Result :)
After tumbling it is a goo idea to finish the parts by polishing with a buff wheel
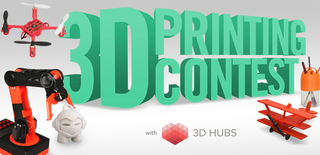
Participated in the
3D Printing Contest