Introduction: All Lasercut 3D Printer (Prusa I3) Under 200$ Outstanding Performance No Printed Parts!
Hi everyone. I have used so many guides and tips from Instructables and it has helped me very much on my way and I felt that its time to give back to the community. Excuse my English if there are any errors! I remember the first days that I was introduced to 3d printing technology and my first 3d printer build. It was a prusa with a lot of printed parts. Even now still in my country 3d printing is not that widespread and printing services are really expensive. I remember the frustration of sourcing parts and finding replacements and getting everything to work! On the other hand laser cutting can be found cheaply and as I was searching I didn't find any all laser cut printers and when you dont have a printer, sourcing the printed parts can be bit of a pain. So in my free time I started redesigning the printed parts so they can be produced with lasercutting. I hope this can help people like me in the past, who dont have access to 3d printing but want to build a 3d printer for themselves. I have tested it, it works really good and gave outstanding results and prints, in my opinion some of the part are even better off laser cut than printed. But if you like you can self improve to printed parts that are printed on your own printer free of charge!
It has the same specifications as a Prusa i3 except for the z axis that can move a few centimeters shorter because of the bed being raised a bit but this can be over come by raising the extruder mount a bit. I have printed both PLA and ABS with it, and as low as 30 micron layer height, it prints perfect circles and nice overhangs and smooth surfaces and tall object are not crooked.
Im sorry that I dont have pictures of all the steps because as I was experimenting I thought things would change, but worked really well and I haven't had the time to take them apart and get pictures of all steps but I will explain the steps as well as I can!
Note that the files that say 6mm should be cut out of 6mm acrylic and the ones that say 3mm should be cut out of 3mm acrylic. I myself did not have 6mm acrylic at hand so I cut the 6mm parts two times out of 3mm acrylic and glued them together. But if you have access to 6mm acrylic it will make a more rigid printer!
I hope this can help! Lets get started then! PLEASE VOTE FOR ME IF YOU THINK MY WORK DESERVES IT :)
Step 1: Parts
The printer uses the same mechanical an electronic parts as other prusa printer.
Mechanical:
1. Smooth Rods 8mm diameter, 2 * 380mm X axis, 2 * 410mm Y axis, 2 * 320mm Z axis totaling to 2220mm but get a few centimeters longer so your not short after cutting.
2. Threaded Rod 8mm diameter, 2 * 450mm totaling to 900mm but get a few centimeters longer so your not short after cutting.
3. Stepper motors 4 * Nema 17 Motors
4. 10 * Linear Bearing LM8UU
5. 2 * 300mm T8 8mm Leadscrew with copper nut
6. 2* Motor to Leadscrew Flexible Coupling 5*8
7. GT2 Belt 850mm Y axis, 800mm X axis totaling to 1650mm get it in one piece and cut to size when your fastening the belt, also get a few centimeters longer.
8. 2 * GT2 Timing pulley 20 Teeth 5mm bore, 2 * GT2 Timing Pulley Idler 20 Teeth
9. 12 * 8mm Nut and Washer for threaded rod
10. 60 * M3 screw 15mm length
11. 75 * M3 screw 10mm length
12. 10 * M3 screw 30mm length
13. 150 * M3 Nut and Washer
14. Lasercut Parts
15. 4 * Spring for Bed
Electronics:
1. 1 * RAMPS Board
2. 1 * Arduino Mega 2560
3. 4 * Pololu A4988 Stepper Motor Driver
4. 3 * Endstop w/ cables Optional
5. 1 * Power supply 12 V 15 A w/ cables
6. 1 * MK2 PCB Heatbed 200*200mm
7. 1 * 100K Thermistor
8. 1 * Extruder Fan Optional
9. Wires as needed
10. Glass Plate 200mm * 200 mm, 3mm
11. Kapton Tape
12. 4 * Binder Clip
13. MK8 Extruder*
14. RepRap Discount Full graphic smart controller Optional
The Extruder mount is designed for a MK8 extruder but can be easily redesigned to work with anything. If your having problems or have any questions feel free to contact me I'll be happy to help! :)
Make sure you have everything in advance then start building.
Step 2: Frame
For this part you will need the laser cut parts of the file Frame.dxf, threaded rods, GT2 pulley, flexible couplings and 3 of the motors.
Whenever feeling lost refer to the pictures.
Firstly fit the main part of the frame with the two large triangular parts and screw them together using 15mm screws. Remember to use washers, they prevent the screws becoming loose because of vibrations and also prevent the acrylic from cracking. Also don't over tighten the screws you wouldn't what to break the acrylic. There are spaces to put the nuts in the parts and after fitting them together insert the screw and tighten it. Should be pretty easy.
Then screw the 3 stepper motors to the motor holders, two of them are alike which are for the z axis and the other shorter one is for your y axis. I think it will need 10mm screws. Fit the z axis motors with the flexible couplings, there is a chamfer on the motor shaft, one screw on the coupling should match the chamfer. Tighten the screws on the coupling using a hex wrench. Also fit the y axis motor with the GT2 pulley using same procedure, it will need adjusting later on so only tighten it so it will stay in its place. Fit the four square legs to the sides of the z axis motor holders and tighten with screws. They were originally triangles but I redesigned them so the frame will be more rigid. Also tighten the little triangle part to the y axis motor holder.
Next will be the y axis. First fit the back plate with the end of the frame and tighten with screws. On each of the threaded rods put a nut then two washers then another nut and screw until they are like 15cm to one side, also put a nut and washer in each end. Next insert the two threaded rods in the back plate (with the nuts and washers on the middle of the rod closer to the back plate) and at the other end into the front plate. It should be so that on each side where the rods meet the frame there would be a nut then a washer. Also put washers and nuts where the rods come out of the front and back plate. Only tighten so much that it keeps together no need to tighten it all the way as it will need adjustments later on.
Screw the two little parts that will hold the y axis idler GT2 pulley to the front plate. Also screw the z axis motor holders to their appropriate locations on the main frame and the y axis motor holder to the back plate with the motor shaft facing inwards. Remember to route the motor wires through the places designed in the frame to one side of the printer that the electronics would go preferably the left side looking from the front.
The frame is complete! You should have three laser cut pieces left from this part, put them aside.
Step 3: Bed
For this part you will need the laser cut parts from Printbed.dxf, 3 LM8UU bearings, 410mm Smooth rods, GT2 idler pulley and GT2 timing belt.
Whenever feeling lost refer to the pictures.
First you should put together the y axis busing. Each busing consists of four parts. First screw the top holder and middle holder to the main part then insert a LM8UU bearing and lastly secure the bearing by screwing the bottom holder. Do the same for the 2 remaining busing.
Insert one end of each smooth rod into the back plate, then put two of the busing on one rod and another on the other rod and secure the other end of the smooth rods in the front plate.
Secure the four ends of the smooth rods by screwing the caps on the front and back plate. Tighten the nuts on the threaded rods around the front plate with little of the rods sticking out to give it a clean look and let the extra length stick out the back. Then tighten the nuts on the threaded rod around the back plate make sure it doesn't put pressure on the smooth rods and the back plate, also tighten the nuts around the main frame. Make sure it doesn't put pressure on the main frame or the back plate because the length between the main frame and the back plate is fixed and make sure it makes a perfect rectangle meaning the length between the back plate and main frame or front plate and frame are the same on both the sides. You may have to play a little with it to get it right. Making errors may result in cracking the front plate, back plate, smooth rod caps or the main frame so proceed with caution and pay attention. Make sure everything is nice and tight so you have a completely rigid frame.
Lastly you should construct the belt clamp. First screw the GT2 idler pulley to the front plate. Then put nuts in the designated locations on the bottom plate and screw the 3 belt holders in place loosely. Afterwards screw the spacers on the two sides of the bottom plate. Secure the free end of the belt (smooth side up) under two of the belt clamps on the bottom plate. For belt tensioning loosen the inside nuts of the front plate on the threaded rod so the plate moves a few millimeters inwards. Then route the belt around the idler pulley to the pulley on the motor shaft and back to the clamp. Now you should tighten the pulley on the motor shaft so that the belt is completely straight. Now tighten the belt with the last clamp as much as possible. Cut the excess belt after leaving a few centimeters to be sure! Again tighten the nuts of the front plate on the threaded rod so that the plate moves back to its original place and tensions the belt with it. fasten screws and a nut as a spacer on the three busing and the top plate of the belt clamp. Then screw the top plate to the rest of the clamp. At last screw the bed piece from the last step on top of the busing and belt clamp.
The bed is complete!
Step 4: X Axis
For this part you need the laser cut parts from the file Xmotormount.dxf and Xidler.dxf, 4 LM8UU bearings, GT2 pulley, GT2 idler pulley, stepper motor and the leadscrew copper nuts.
Whenever feeling lost refer to the pictures.
These parts are a bit tricky. First we will start with the motor mount part. The motor side should be on the left. At first screw the top bearing holder (A) on the front. Second screw the two rod holders (B) and (C) and the end part (D) on the back. They all look alike so make sure you have the right parts or it will not fit. Third Screw the two middle bearing holders (E) and (F) on the front. Fourth screw the other rod holder (G) and end part (H) on the back. Fifth insert two LM8UU bearing in the bearing holder and screw the bottom bearing holder (I) to secure the bearings in place. Sixth screw the bottom rod holder (J) into place on the back. Seventh screw the leadscrew copper nut to part (K) and then screw it into place at the top on the front. Keep in mind the indent on the part should face the bearings.
Screw the GT2 pulley to the motor shaft as described before. Then screw the motor to the motor plate and then screw the spacers to the plate and finally screw the motor assembly to the other part.
For the idler part follow the same descriptions as above only this time the idler pulley side should be on the right.
After that screw the idler pulley to the part on the backside.
The parts are complete! You should have 4 parts left. Leave them for now.
Step 5: X Carriage
For this part you will need the laser cut parts from Extruder.dxf and 3 LM8UU bearings.
Whenever feeling lost refer to the pictures.
It should be pretty simple now! Screw the bearing holders insert bearings and secure them.
Screw the three belt clamps loosely in place but do not screw it on the carriage yet.
Also mount the MK8 Extruder on the bottom plate and screw the parts that wrap the extruder and hold it into place. This part will be screwed onto the carriage after final assembly.
Proceed to the next part and final assembly.
Step 6: Final Assembly
For the final assembly you need all the mechanical parts left and the x carriage and Motor mount and Idler.
Whenever feeling lost refer to the pictures.
Get the 380mm smooth rods and insert them in the x carriage's bearings with the single bearing being at the top and the flat face of the carriage facing up. Put the x motor mount and idler in front of you with the rod holders facing up and the motor mount to your right and the idler to your left. I myself placed some foam in the rod holders to dampen vibrations and secure the x axis rods so they wont fidget. Flip the x axis rods plus x carriage so the bearing are towards you and put the ends of the rods in the rod holders on the motor mount and idler. Secure the rods by screwing the 4 lids left from the last step on top of the rods and tighten the other ends with 4 zip ties inserted inside the space above the screws.
Next insert the leadscrews in the flexible couplings and tighten the screws. Also place the 320mm z axis smooth rods in the holes on the z axis motor mount plates.
Flip the whole x axis assembly so the motor is on the left and lift and insert the z axis smooth rods in the bearing and also insert the leadscrews in the copper nuts and screw it a bit manually so the x axis gets mounted in place.
After that screw the two plates left from step 2 on top of the frame at each side securing the end of the rods and leadscrews.
Next secure one end of the belt under two of the clamps and route the belt over the idler pulley all the way to the motor shaft pulley and back to the clamp and tighten as much as possible. Now you should adjust the idler pulley and the motor shaft pulley so that the belt does not touch anything and also is straight. You may need to unscrew the motor plate to adjust the GT2 pulley. Also screw the belt clamp to the x carriage. Cut the excess belt after leaving a couple centimeters.
Lastly screw the MK8 extruder assembly to the carriage
Congratulations the frame is complete! Make sure its as rigid as possible and there are no loose screws and you will get perfect prints!
Step 7: Electronics
For Its electronics the printer uses a Arduino Mega 2560 and Ramps 1.4.
First plug the ramps board onto the arduino mega board. Next insert three jumpers under each stepper driver to get 1/16 micro stepping. Next stack the Pololu steppers on top of the RAMPS 1.4 shield. The potentiometer (the little screw like thingy) should be facing away from the “D10 D9 D8” side on the RAMPS 1.4 shield. Make sure orientation is correct. Install the heat sinks on the Pololu drivers. Connect the power supply wires to the included connector. Next solder two wires to the heatbed. Also using the kapton tape, tape the thermistor to the little hole in the middle of the heatbed so that the temprature readings are from the glass and accurate. Screw the heatbed to the print bed using 35mm screws and spring and washer between them. Place the glass on top and secure with 4 binder clips. Some wires maybe short so I just extensioned them with dupont jumper wires. Motors, and the heatbed thermistor have bare wires so you need to crimp them. Lastly connect everything to the board according to the picture. I used wire wrappers to tidy up the wires but its optional. Make sure everything is connected properly and securely before proceeding and powering on. Also whenever you want to disconnect something make sure to power off the board and disconnect the usb cord.
Step 8: Firmware
For the firmware I used RepRap Marlin. To get started install the Arduino IDE from https://www.arduino.cc/en/Main/Software. Also download the marlin firmware I have provided. Its just calibrated for this printer. Note that it does not use endstops now and I have printed my endstop holders afterwards so you should calibrate the bed manually at first to print endstop holders. You can also use the printer without endstops but you should calibrate the bed manually before each print. Next connect the green power connector to the ramps board. Check the wires corresponds to the input (+) and (-). Reversing +/- power can destroy your board so be careful. Make sure everything is connected correctly including the stepper driver orientation and then turn on the power unit and then connect the usb to your computer.
Open the arduino IDE software. Select you board model by going to Tools --> Board --> Mega 2560. Select the COM port by going to Tools --> Ports --> COM3 (Mega 2560). Note that the port number may differ on your system. If unclear, take a look at the ports then unplug the arduino board and take a look again and see what has changed.
Next click file --> open and browse to the place you have saved the firmware and open Marlin.ino. Then click on the "tick" to verify there are no errors (there shouldn't be but just to be safe) and after that press the arrow icon to upload the code to the board.
Note that the firmware uses the RepRap discount full graphic controller and if you do not want it you should disable it in the Configuration.h file.
You should now have a working printer!
To test manually position the printer axis at the center of each axis. Open a host software like pronterface and click connect. Keep your hand close to the stop button of the ramps board just in case. First look at the temperature readings from the hot end and bed to see if the thermistors are working. Next move each axis a little amount like 10mm to each side to see if steppers are functioning properly. If the direction is reversed disconnect the printer and and usb and power off the board and flip the corresponding motor connector or change the direction in the marlin firmware. Change the true/false in the lines
#define INVERT_X_DIR false
#define INVERT_Y_DIR false
#define INVERT_Z_DIR false
#define INVERT_E0_DIR false
in the Configuration.h file. There are tons of tutorials on the marlin firmware so I'm not gonna go deeply into that here. If the axis moves more or less than the amount commanded, then your stepper motor specifications are different than mine and you need to change it in the Configuration.h file. Here is a calculator to calculate steps per mm based on your stepper specifications. http://www.prusaprinters.org/calculator/
To change the steps per mm in Configuration.h file scroll to the line
#define DEFAULT_AXIS_STEPS_PER_UNIT {X,Y,Z,E}
and replace the amounts in place of {X,Y,Z,E} respectively.
Note that before uploading the code every time, you should disconnect the host software and also verify to see if there are any errors.
At last heat up the heatbed and hotend to see if the heaters work.
Congrats on the new printer! Have fun!
Step 9: Calibration, Prints and Improvements
For calibration make sure the axis move as should and when commanded to move like 10mm they actually move 10mm. If not right go back to the last step and change the steps per mm to achieve accuracy. You may have to play around with it a little. Next make sure the X axis is horizontal. To do so I measured the length of both sides to the top of the printer and adjusted manually. Also you should oil the bearings and rods and lead screws so they don't wear off and also don't get stuck. Heat up the extruder and insert some filament in the extruder an extrude a bit so that plastic starts oozing out keep extruding a bit for the first time so that the extruder system cleans itself. Clean the nozzle of plastic with some tissue paper and turn of the hot end. Put blue painter's tape on the glass bed. Move the nozzle to the front left corner of the bed and move it down until a piece of paper can be pulled from between the nozzle and the bed without a lot of force. Move the z axis up 10mm and then move the nozzle to the front right corner and again move the z axis down for 10mm and do the same test, make sure you don't move the z axis anymore and move the bed by fastening or loosening the screws to achieve perfect contact. Do the same for the other corners until your bed is completely parallel to your x axis and the height from the nozzle to the bed is the same every where.
Now you can start printing. Find a model, open in a software like cura, remember to disconnect from host software (pronterface), input desired settings and start the print. It should have no problems and print perfectly. If there are any problems contact me and I will be happy to help :)
I improved the x motor mount and x idler to printed parts later on. To do so download the models below and print them. They are compatible with the current setup and there should be no problems.
You could see my prints in the photos above. They are just wonderful and I am very happy with this. If everything is done right you should get the same results!
If there are any problems or anything that I have forgot with the instructable or the build please let know and I will correct it as soon as possible.
I would very much like to see your builds so send them to me! I hope this helped!
Good luck!
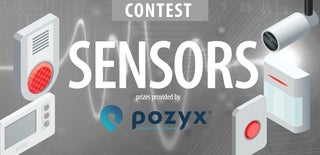
Participated in the
Sensors Contest 2017
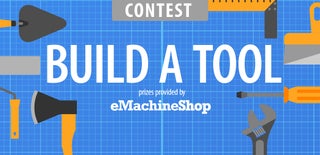
Participated in the
Build a Tool Contest 2017
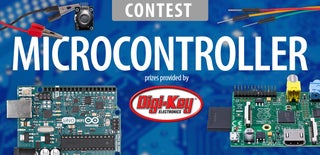
Participated in the
Microcontroller Contest 2017