Introduction: All in One Work Bench
Built this workbench to maximize my work area in the garage. I wanted lots of tool storage with power built in and a table saw outfeed table. It had to be movable
Step 1: Start With Lumber and a Sketch
I started with a trip to the big orange store.15-2x4
2-4x4
4-1x2 pine strips
2 sheets of cabinet grade 3/4
3" wood screws
Epoxy paint and primer
Wood stain.
I then drew a sketch of what I wanted
Step 2: Practice Your Joints.
I took some scrap wood and practiced the joints I wanted to you. I used half laps so I set my sliding compound saw to the depth I needed and made lots of cuts next to each other
Step 3: Start Cutting Wood
Start cutting your frame work. Make sure you test each joint as you go
Lots of cutting here
Step 4: Assemble
Assemble all the framing components. Make sure everything is square
I used wood glue and 3 inch wood screws here
Step 5: Add Casters
I added caster to make it easier to move around
Step 6: Cleaned Up Joints and Add Power
Next I cleaned up the joints using wood filler and added electrical boxes under the table. I worked the 4 electrical boxes together then wire a cut off extension cord to the last box to plug into the wall.
Step 7: Prime Bench and Stain Top
Next I primed the bench with kills primer and stained the top of the bench.
Step 8: Put in the Sun to Dry
Drying.....
Step 9: Paint
I wanted a strong finish so I used a oil based epoxy paint. 3 coats
Step 10: Add Lower Shelfing
For this is used 2x6 lumber. I cut it all to fit them removed and stained it before screwing it down with pocket holes from the bottom
Step 11: Make Edge Trim
I made edge trim to hide the plywood edges. I but to size, mite red the corners and stained them. I used pocket screws to attach them
Step 12: Lower Shelf
Made the lower shelf the same way, cut, stained , edge trim, then pocket hole to attach
Step 13: Finish With Polyurethane to Protect Finish
Used 3 coats of polyurethane to protect the top surface
Step 14: Load It Up With Tools
Got all my stuff put on it
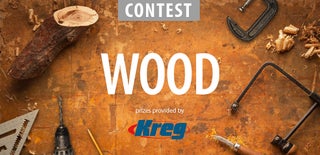
Second Prize in the
Wood Contest 2016
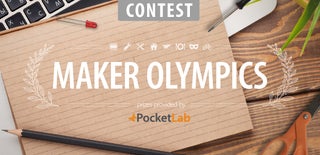
Third Prize in the
Maker Olympics Contest 2016
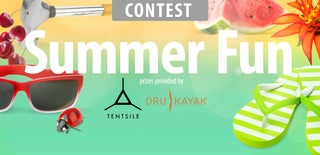
Participated in the
Summer Fun Contest 2016