Introduction: Anglo-Saxon Lyre
Welcome to my on-going project!
Tools Used:
Drill Press
Assorted Forstner Bits
Sandpaper, Assorted Sanders
Jig Saw
Scroll Saw
First of all, some of you might be wondering, the heck is an Anglo-Saxon Lyre? Well, the Anglo-Saxon lyre is a box lyre popular in Europe a long time ago. There are few surviving lyres, but there are some craftsmen who try to recreate these instruments. This is my try at recreating one out of maple and birch plywood for the soundboard (If you have access to a better wood, use it!). I included the Sketchup plans for this project in the 7th step. If it isn't accessible, this may be my fault or it may be due to I had created it in the 2013 version.
Edit on 1/17/2015: After learning much, much more about woodworking, I have decided to stop progress on this blog. I may make a new one. I found that the zither pins would go through the back of the top, and multiple other problems. In addition, I believe that I am acquiring the skills to actually make a nice one, and in much less time. I am leaving this blog up to review my methods and try to find how to improve upon them if I do ever attempt to make this instrument again.
Step 1: Step One: Trace and Cut Basic Outline
This should be the easiest step. I used rulers, a compass, and a straight edge to get the outline onto my lyre. I then used a jig saw to cut out the basic shape. I then drilled holes into the space to be cut out between the arms, then used the jigsaw to cut that part out. If you use a hardwood like maple, be careful-It is a very hard wood, and will take some time to be cut in the curves needed. I apologize for the weird picture from my phone camera.
Updates, 5/26/2015: On reviewing this step, I decided I really should have made the arms wider.
Step 2: Carve the Soundbox
The soundbox can be carved different ways. If you have a router, definitely go with that, if you have the know-how. If your going old-school, get your chisels sharpened and your mallet...mallety? I do not own a router, so I set the depth on my drill press to the appropriate depth and drilled down to it using Forstner bits. Then, I used a chisel to remove any bits too small for the bits to drill into it, and then sanded for around two or three hours using 60-grit sandpaper.
Update, 5/26/2015: If I had to re-do this step, I would use the router I now have available, followed up with a chisel. I actually have sharp chisels now; the chisels I had then were unusable, as the maker had covered the surfaces in rasps and files to make it a 'multi tool'.
Step 3: Cut Out the Upper Arms
Using the pencil lines laid out in step one as a reference, first drill six holes or more using a regular drill bit of your choice. Drill one next to each of the corners, but not on the pencil lines themselves; Then drill one at the vertex of the top parabola, and at the bottom one, again next to but not on the pencil lines. Then use the jigsaw to cut out the wood. The closer you follow the lines, the less wood you will have to carve/sand down.
Step 4: Cut Out the Soundboard
The soundboard is the part of the instrument that is usually the thinnest on the lyre; it's specifics differ instrument-instrument. Usually, on guitars and ukes, the soundboard is made out of the best tonewood, as it matters the most in sound. However, I don't have mahogany or maple veneer on hand; So I used birch plywood (It's great for pyrography as a bonus, too!). I laid the body of the lyre on top of the 'soundboard-to-be', traced it, then cut it out with the jigsaw and scrollsaw. I then dry-fitted it on the body; Not exactly perfect, but not too drastic, just a few centimeters here and there. Make sure to leave an overgap in case your pencil lines weren't accurate, like mine, in some places.
Step 5: (Optional) Add Decorative Touches to the Soundboard
If you are doing pyrography on birch plywood, sand it down to 150; Then trace your design, and use your pyrography tip to woodburn the design into the wood. Then sand it down one more time up to 200, and your ready to move on.
Some other decoration ideas other builders have employed are calligraphy in ink; Jeweled corners, or decorative brass brackets on the arms.
Updates, 5/26/2015: I still like the general design. However, I do not recommend plywood: I sanded through in multiple areas of mine, and some areas splintered off. Still pretty darn cheap though.
Step 6: The Glue-Up
Carefully apply glue to the edges; depending on your grain, the wood may drink in the glue. I used Titebond III for my lyre. Then carefully align the soundboard, and use as many clamps as you can, or resort to the cutting-edge gravity clamps of Brick Co. When the glue has dried completely, then you get rid of excess wood hanging over the edge of the body. Move on to the next step when you are satisfied!
Step 7: Adding Tuning Pins and String
The stringing of the lyre can be complicated, as there are not many full examples of Anglo-Saxon lyres. The little square on the soundbox part of the lyre is where you attach the tailpiece of the lyre to. The tailpiece is usually oval, with the narrow ends perpendicular to the arches in the lyre's body. The six strings are attached in the top-facing part of the oval, and are separated at a bridge, which then lead to the tuning pegs/zither pins.
Some ideas for strings are nylgut, a synthetic gut string popular with reconstructed instrument makers; Gut strings, rather rare; and I used nylon guitar strings.
Tuning pegs can be zither pins, commonly available on websites such as C. B. Gitty or Amazon. The bridge can be simple maple, or ornately carved amber; the tailpiece can again differ between a beautiful ivory celtic knot or a simple dowel. This part of the lyre is really up to the imagination, and even more so the tuning of the instruments; There are tutorials on Youtube by different artists as to which tuning they prefer. Note: One of the reasons I was not able to finish my lyre lately is that I forgot to buy a tuning wrench for my zither pins. Make sure to get one yourself!
Attachments
Step 8: Playing the Instrument
No one alive has heard the Anglo-Saxon lyre played by it's original creators; However, the majority of players agree that the method used to play this instrument was the block and strum method. This method is where you hold the strings you wish to mute with your fingertips, and with your other hand strum the strings, producing a chord. The other way of playing is just plucking the strings, and some believe that plectrums were used in playing these instruments. Enjoy your Anglo-Saxon lyre!
Step 9: *Coming Soon: My Finished Lyre*
Well, thank you for reading this instructable, and for those who have been watching it, thanks for being patient. Part of the reason mine is taking quite a bit of time is that 1. I have a really low attention span 2. I have no idea what I'm doing 3. I lacked the supplies to finish it. Number 2 is also related to the fact that I seriously underestimated the difficulty of this project. Luckily, one day at Woodcraft I found a massive pile of mahogany cut offs. I promptly picked up one of these boards, to use for a nice contrasting color in the lyre. Right now, I am experimenting with the bridge and the tailpiece designs, while waiting for the main reason this project is taking me so long-finding something to tune the zither pins with.
Update on 5/26/2015
I have found zither tuning keys for a reasonable price on Harp Kits! Hot diggity Dog, I may be able to wrap up this project! Also bought a set of kantele strings to make a kantele for a friend.
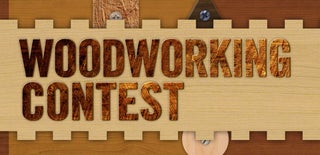
Participated in the
Woodworking Contest