Introduction: Arduino Nano Based Microbot
I created this as a simple project for those just starting out in robotics. It is relatively inexpensive, requires minimal tools and is easy to build. Once finished you have an expandable robotic platform that fits in the palm of your hand and can be easily programmed in the Arduino environment.
Here is is driving in a triangle, without any special add ons
In the instructions I'll walk you through how to:
- Modify the servos for continuous rotation
- Fit the track hubs on to the servos
- Make a custom battery pack
- Wire it with a few connections
- Assemble it
- Program it
- Customize
For the basic platform the following supplies are needed:
an Arduino nano
a small rechargeable battery
a pair of 9 g servos, modified for continuous rotation
part of a Tamiya track set
a 40 pin dip socket
a rubber eraser
some zip ties
Step 1: Construction: Modify the Servos
Pictures:
- Remove the tiny screws and open the case
- Cut the potentiometer wires, these are where you will attach the resistors
- If you have surface mount resistors, place a 5k (1k to 10k should work) on the pad from each of the side pads to the middle pad, if you don't twist a pair of through hole resistors like this
- Break out the stop on the potentiometer with some small pliers, you need the pot for its use as a rotational bearing
- solder on the resistors, if you used the pair of through hole ones, I recommend bundling them in electrical tape like so. For the servo that will go on the front, cut a notch for the wire to exit through the side so it doesn't come from under the robot.
- (not shown) Before you close up, put a hole in the back part of the case opposite the spline to mount the idler (wheel with no teeth).
- Use some angle cutters or pliers to remove any mounting flanges from the cases and file or sand down the ridges they leave, these can get in the way later.
Step 2: Construction: Drill the Hubs to Size
- Cut the stems on the hubs so that they just stick past the inner edge of the tracks when installed. This can be done with a hobby knife saw or a coping saw. Be careful you don't slash your hand! For safety I held the hub on a cutting board on its side with my fingers on the other side of the wheel from the stem, and then I rotated it against the cutting board dragging the knife along it, this way if you slip you just hack the board.
- Drill the hole for the bolt that will hold it on to the servo in the cap of the drive wheel (the wheels with teeth). You may be using the hub screw that came with the servo. Whatever screw you use that fits in the servo spline, drill the hole to fit.
- Since the small Tamiya hubs don't fit on the servo ends, you'll need to drill them to size. Since these are small and already have holes you don't need a drill press, but you will need something to clamp it down. Servos vary in spline size, so I can't give you an exact size to use. I would suggest you go a bit small, and step it up until the hub fits tightly, these will be transmitting the torque. You also must be careful with depth so the hubs don't rub against the servo body. Measure your servo spline and make the dept of the mounting hole just slightly less than this. I suggest the method of putting masking tape around your drill bit at the depth you want to stop. Then you can hold it next to the servo spline before you drill to confirm it is slightly less.
- To install the hubs, the idler should be attached using one of the screws from the Tamiya kit, or another screw of the right length, I got mine from my random hardware jar, and don't have a specific size. Tighten it just enough that it doesn't pinch the wheel down.
- On the other side, use one of the screws that comes with the servos through the hole in the driver wheel to snug it down.
Step 3: Construction: Make the Battery Pack
I went with NiCd because I had some old cordless phone batteries with 1/3 AAA cells in them that I could make into the roughly 5 V packs I needed. Each cell is 1.2, so I used 4 to get 4.8 v. They also don't require special circuitry to charge.
If you can get a LiPoly and a charger, like the kind they sell on ebay for syma 107 helicopters I think that would work well too.
The photos explain how I did this better than words can:
- Picture of the battery as is, I had more than one of these
- Remove the shrink wrap
- Cut them apart where needed, so they can fold into shape.
- Put the 4th cell, taken from another pack in place
- Fold it in to shape
- Wrap it up in electrical tape
- Picture how it fits on the chassis
Step 4: Construction: Connect the Wires to the Socket
A socket is used to mount the Arduino Nano to the robot, besides making the Arduino removable so that it can be used for other projects, this simplifies attachment to the rest of the machine. Alternatively you could buy a small breadboard for $4 (as shown in the second picture below from sparkfun.com) and zip tie it to the top in a similar way for more modular design.
In my case I wired the servos into D11 and D10, but you could use any of the PWM outputs, as shown in the first picture below. I then wired the battery to a free pin on the socket in between pins that I wired to the power for the arduino (Vin) and the servos, so that I could switch them on and off with jumpers. I smashed the legs of the socket outward so they are easy to access for expansions. Notice that this placement also makes the USB connection and reset buttons easily accessible, at the end of the robot.
To charge the battery, power can be applied by putting the jumpers in the off position (stored on the other side of the socket) and plugging charging leads into battery +, and ground. Again, for this battery the easiest charging method is to connect gator clips to the outputs of a 1.5-9V NiCd charger. If you are using a different type of battery charge accordingly.
Step 5: Construction: Assemble the Microbot
Here is where the eraser comes in. If you have the assembled servo/wheel sets from step 2, you can put the belts on them with the servo that has a wire coming from the side upright and the other laying with its long end pointed toward the upright one, as shown in the fist picture. Pull them to light tension, so the belts are nearly flat but not taught, and measure the gap between the servos. Cut a section of eraser to wedge in this gap. This works like suspension, allowing the frame some flexibility while holding it in place under most forces it will encounter. It's the white part in the picture.
The battery fits in the crook between the upright and flat servos and the socket sits on top (second picture). Make sure the sockets legs are smashed outward for easy access. Then use one or two zip ties to strap the whole thing together, be sure the buckle is on the front or back, not underneath or above the socket, you don't want it to get in the way of ground clearance or plugging in the Arduino. If you are using the mini-breadboard variant, you may need to file the middle channel a bit deeper for the zip tie to set in.
Finally, plug in that Arduino (third picture), you can make the jumpers by simply bending some stripped wire with pliers.
Step 6: Programming: Basic Operation
This is built with an Arduino so that you can program it to do whatever you like. Here are the basics. Further expansions are covered next. To test things out you can upload the code and move the jumpers both to the on position.
Really, the basic code to build on is just this:
//---------------------------Start Code
#include <Servo.h>//Loads commands to create Servo objects which generate PWM signals
Servo leftDrive; // create servo object to control a servo
Servo rightDrive; //another servo object for the left side
void setup()
{
leftDrive.attach(11); // attaches the servo on pin 9 to the servo object
rightDrive.attach(10); // attaches the servo on pin 9 to the servo object
}
void loop()
{
//here put commands which drive the servos
//use the commands
//rightDrive.write(any number 0-180);
//leftDrive.write(any number 0 to 180);
//to set the servos turning 0 is full one way, 180 is full the other, 90 should be near stop
//which way is forward depends on your servos
}
//end code -------------------------------------
So that gives you an idea how simple this can be.
Here is a basic code example for just driving around in a square. Note that the video was with the delays set to 600, which resulted in a triangle, 450 gives you more of a square. (code starts after this line):
//------------------------------------------------------------------------------------------
#include <Servo.h>//Loads commands to create Servo objects which generate PWM signals
Servo leftDrive; // create servo object to control a servo
Servo rightDrive; //another servo object for the left side
int pos = 0; // variable to store the servo position
void setup()
{
leftDrive.attach(11); // attaches the servo on pin 9 to the servo object
rightDrive.attach(10); // attaches the servo on pin 9 to the servo object
}
void loop()
{
//example routine, drives in a square
turnRight();
driveForward();
turnRight();
driveForward();
turnRight();
driveForward();
turnRight();
driveForward();
}
//the following functions are examples, you could easily make the robot
//move on curved paths or at varying speeds by changing these numbers
//0 is full forward, 90 is stop and 180 is full reverse. The case may be the
//opposite for your build
//turns right about 90 degrees
void turnRight()
{
leftDrive.write(0);
rightDrive.write(180);
delay(450);
}
//turns left about 90 degrees
void turnLeft()
{
leftDrive.write(180);
rightDrive.write(0);
delay(450);
}
//drives straight for 1 second
void driveForward()
{
leftDrive.write(180);
rightDrive.write(180);
delay(1000);
}
//drives straight backward for 1 second
void driveBackward()
{
leftDrive.write(0);
rightDrive.write(0);
delay(1000);
}
//end code---------------------------------------------
So, the point of this is to be a platform. Making a robot just drive about can be fun, but the most fun is always making your own things. Since this is an arduino there is example code to add all kinds of controls, devices and sensors to customize your bot.
Step 7: Customize It
The idea I'm sharing here is how I made a compact simple to control robotic platform. I feel that showing you what to do with it exactly would not have much of a point, you can do whatever you like with it.
That said, I'll make some suggestions of how you could expand this robot without reinventing the wheel. Other Instructables are suggested to get into the low level details of these features, and links are provided to buy them where available. I didn't make these Instructables, but they will integrate nicely, that's the great thing about an online community after all:
Gripper
The easiest way to add a gripper is with another micro servo, one that isn't modified for continuous rotation. You would add its control to code simply by attaching another servo, and giving it a position command, as seen in step 6.
Here is an example which would fit right on:
https://www.instructables.com/id/How-to-make-a-robot-gripper/
The same method could be used to add a scoop or other manipulator as well.
If you want to just buy one, something like this would work nicely:
Jameco 1.3 inch gripper
Radio Control
A fun thing to add to any robot, there are piles of tutorials on how to do this with an Arduino.
You can do it with blue-tooth (easy but expensive)
https://www.instructables.com/id/how-to-Control-arduino-by-bluetooth-from-PC-pock/
Or you could use an XBee (easy, and less expensive)
Since the XBee is wider than the Arduino nano, and can't plug into it, I would actually suggest setting it over the nano and wiring it in around it.
Examples of the code needed are widely availible, heres an XBee library for arduino.
Of course, you could get an XBee/Arduino nano board, like this one from robotshop, and your robot would have a swanky tail.
You can do it with a bare transmitter receiver (cheapest, but requires knowing what you are doing):
http://www.robotshop.com/productinfo.aspx?pc=RB-Ons-02&lang=en-US
Detect movement (PIR)
This is actually remarkably easy, a PIR sensor compares the infrared map of its environment with one it has built over time. So it detects changes. They can be found for $10 at several stores including sparkfun and robotshop
These have everything integrated, and the output pin goes high for a few seconds when motion is detected. All you do is give it power from the battery and connect the output to an input pin on the Arduino. Then set an interrupt or check the state of the pin. As seen on the customization of the platform above. This lets your robot react when someone approaches.
Ultrasonic Range finding
Ultrasonic range finders are an inexpensive way detect the distance in one direction with decent reliability in the range of about 0.1 to 10 meters. They tick out ultrasonic pulses at about 10Hz and detect how long they take to return. Most pick up obstacles in a conical span, so they can be fooled by things that aren't really in the way. It's no LADAR or computer vision, but it costs 1/1000 as much.
This is also on the robot customization shown here. I used an HC-SR04 range finder and this library. I just got that from ebay for $6.
There is also support for the PING range finder: http://arduino.cc/en/Tutorial/Ping
And even if you use the cheaper one I used, this may help you understand how it works
GPS
If you want to give your robot a sense of its/his/her place in the world, there is example code to use a parallax GPS module on Arduino Playground here.
Future Steps
I'm planning a few fun projects with these. One will be to add wireless cameras, remote control, and little grippers, and then make tiny obstacle courses for them to explore in teams.
Another fun project would be to mount a Kinect on the roof and make a bunch of these with wireless act as a swarm in formation.
In general I'm going to use these as a basis for lots of projects, and I will be going into more detail about possible add-ons in that way. I would be very pleased to see this used in other Instructables and expanded. After all, sometimes you want to use a robot, but don't want to write about developing the basic stuff.
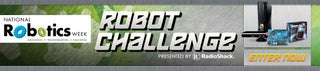
Second Prize in the
Robot Challenge