Introduction: Asterism Series
Asterism: Recognizable figure within a larger constellation - i.e. Big Dipper is comprised of the seven brightest stars in Ursa Major.
Building on the ideas of (re)STOCK (highly customized 3D connections paired with already highly efficient stock sections), the Asterism projects serve as working prototypes for adapting any number of geometries into architectural, structural or furniture systems through the use of parametric strategies.
Initially, design research looked at versions of node connection types - i.e. accommodating round tube, round solid, square tube, wood dowels, etc. Layers of function specific to node type were also explored - features such as tenons, plugs, holes and slots for glue or welding, and pre-tapped standoffs (for attaching surfaces) all added to the potential adaptability of these systems. Subsequent design efforts were directed at the ordering and sorting of members, nodes, and the optimization* of nodes for material and fabrication efficiencies.
As the name implies, larger, more expansive systems potentially exist, however these projects are thought of as smaller recognizable subsets and as such, the bounds or figures were defined as legible ‘products’ for prototyping.
The freestanding spatial ‘screen’ leverages a traditional cross-shaped stub tenon for quick and precise assembly. High resolution 3D printed joints (optimised for minimal length) interface with slotted dowels - done with traditional table sawing and custom jigs.
The stool incorporates 3D printed stainless nodes coupled with stainless tube struts - plug welded to the nodes. Tapped holes on the upper nodes provide the means for fastening the seat with cap screws. These nodes provide substantial structural capacity and therefore move beyond use of 3D printing for mere formal exploration to fully functional components.
*optimization/sorting was done in collaboration with Peteinarelis Alexandros
Step 1: Overview
Tools/Materials:
⅝” Walnut dowels ⅜”
Stainless tube
3D printed plastic and metal parts
3/16” Aluminum plate
Various hardware
TIG welder
Silicon bronze filler (.040)
Table saw and custom end notching jigs
Waterjet cutter
Since much of the design philosophy was laid out in the introduction I won’t get into design specifics. Basically these projects are prototypes which operate on the premise that complex geometries and assemblies can be made as easily and efficiently as similarly scaled projects which have much simpler geometry or standard assembly methods. I chose two very different material tectonics and corresponding joint types to make prototypes with as proof-of-concept.
Step 2: Wood Node Types
With the ‘screen’ structure being primarily a wood structure (walnut dowels) an appropriate joint type needed to be used. I worked on a few iterations of dowel / tenon combinations. A single tenon looked nice, but even with a smaller dowel pin to secure it, the joint wasn't as solid as I wanted it. The cross shaped stub tenon type looked great and held together nicely. With the thin kerf table saw blade making .1” slots in the dowels a ⅝” dowel worked well. I designed and made a few versions of a dowel slotting jig to make this a fairly repeatable process. Unfortunately aligning the notching from one end to the other seems to be left to good ol’ intuition. Fortunately the human eye seems to be pretty accurate for such matters. It gets difficult on very long dowels (this alignment issue is something to work on for future jigging).
Step 3: Stainless Node Types
I had been wanting to experiment with printed stainless parts in a slightly more substantial way for a while. I had printed some smaller joints for testing a few years back, but they were smaller and therefore fairly difficult to weld. Because the stainless is infused with bronze, they need to be welded with silicon bronze (ERCuSi-A). The joint / detail developed for the stool took this into consideration - it also tried to minimize the material volume, as the cost (priced by volume) of printing stainless can be substantial. I had an extra node printed (by Shapeways) so I could test weld a few options before welding all the nodes. One option was to weld all the way around each strut - at the butt between the strut and the joint shoulder. The other option was to drill a hole at each end of the strut to plug weld to the flange of each node leg. This second option proved to be the cleaner, simpler method. For the nodes that met the seat, I left small holes which were hand tapped for small cap screws prior to assembly.
Step 4: Strut Fabrication
For the wood and the metal joints the strut lengths were determined by the parametric definition (simple linework is fed into the design and the definition produces the nodes and labels and organises the struts, so fabrication was not much more difficult than cutting to length and prepping the ends. For the wood struts, this meant notching the dowel ends (see my instructable HERE for how to do just this) and for the stainless system I simply drilled a 3/16” hole on each end of the strut at a specific distance from the end and both in the same orientation.
Step 5: Joint Printing
The ‘screen’ project used plastic prints from the Objet Polyjet printers here at Pier 9. The process was quite simple from digital model to print with cleanup of the build material from the nodes themselves being the most difficult. For the stool I first test printed some nodes with the Objet printers to check fit and tolerance. I then sized down just a bit since I didn’t want to have to remove stainless material in case the finished nodes didn’t fit! Once I got the test nodes right, then I uploaded my models to Shapeways and then ordered them.
Step 6: Assembly
Since the parametric definition sorted all the struts from shortest to longest, I never had to label the parts - I just arranged them in order by length. For the Asterism Screen, assembly took about 5-10 minutes with the 3D model open to use as an assembly guide. The stool took a bit longer (under an hour to weld) but not very long considering the complexity of the geometry. I never had to check or measure angles. With the struts cut to a precise length I just pre-assembled the stool (it was essentially self registering) and then went through and plug welded the 20 ends. A plywood seat template held the upper nodes in place since the aluminum plate seat was at the anodizer at the time of assembly.
Step 7: Conclusions
This seems like just the beginning for this line of design research. The applications seem endless and many more variations seem possible. 3D printing is evolving so rapidly that the quality and material choices for real print-to-use parts should increase greatly along with accessibility to new machines while cost will go down. I’m excited to move on to more projects testing these ideas!
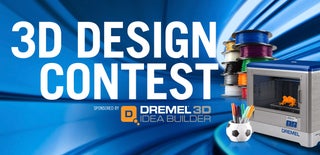
Participated in the
3D Design Contest