Introduction: Smartphone Charger Powered by Fire
Portable, Compact and Adjustable ThermoElectric Emergency Generator.
Background:
The reason for this project was to solve a problem I have. I sometimes do several days of hiking/backpacking in the wild and I always bring a smartphone with GPS and maybe other electronics. They need electricity and I have used spare batteries and solar chargers to keep them running. The sun in Sweden is not very reliable. When you need it as most it´s either raining or other circumstances that makes it impossible to charge with solar panels. Even when it´s clear weather it simply take too long to charge. Batteries are good but heavy. I have looked for alternatives but they are either very expensive or too large.
One thing that I always bring with me though on a hiking is fire in some form, usually an alcohol or gas burner. If not that, then at least a fire steel to make my own fire. With that in mind, I got stuck by the idea of producing electricity from heat. I know, the efficiency is very poor but it is at least possible! So, with inspiration from my previous project (Thermoelectric-Fan-Driven-by-a-Candle) I decided to build my own thermoelectric charger. There are similar projects available but not that fulfill my requirements (what I could find).
Concept:
I´m using a thermoelectic module, also called peltier element, TEC or TEG. You have one hot side and one cold. The temperature difference in the module will start producing electricity. The physical concept when you use it as a generator it's called the Seebeck effect. Thermoelectic modules are mainly used for the opposite effect, the Peltier effect. Then you apply a electric load and it will force a heat transfer from one side to the other. Often used in smaller refrigerators and coolers. Read more about i here:
http://en.wikipedia.org/wiki/Thermoelectric_effect
My requirements:
- As small, light and portable as possible
- Robust
- Adjustable voltage (want to use with broad range of products)
- At least 5V/0.2A (1W) to charge an iPhone 4s, 2W if possible
- Compatible with alcohol/gas burner, campfire and candles
Solution:
With lots of testing and experimenting I come to the conclusion I would need a powerful TEG-module. I have previously used a cheap TEC-module (8€) but it only produce about 0.5W and too low voltage and max temperature. I could use several of them but it will be a more complicated and heat limited construction. I found a 40x40mm TEG that produce 5.9W (4.2V/1.4A) at 180ºC difference. It has a maximum operating temp of 350ºC (180ºC cold side), that should be enough. It´s quite expensive though, about 50€ but that is still cheaper than most solar chargers and much cheaper than other commercial thermoelectric chargers I found.
To transport away all heat and cool it with air you usually need a large heat sink. As my construction need to be compact and light weight, I was thereby limited to very small heat sinks. I then decided to "steel" a small amount of electricity and cool the construction with a motor/fan. That would result in less charging energy but that was the only thing I could think of to keep the size down (and not using water cooling). As it gets warmer, it produce more electricity and also more cooling power from the fan. To block heat from transferring to the cold side I used two heat insulated washers for the fixating and also a layer of insulation between the metal blocks.
First priority was to get a steady 5V source to drive different USB-devices. The module itself produce less than 5V. I solved that by constructing an adjustable regulated voltage Step-up. The detailed specifications can be found later in this project.
Result:
When I started this project I had no idea it would actually work. It turned out it even works over my expectations! I can charge my iPhone which was the main goal and it is completely self-cooled even with extreme heat sources.
The cooling is not optimal due to it´s small size, but I´m quite satisfied because I can bring it with me. I would happily see you construct even better solutions, I´m absolutely certain it could be made even cheaper and more efficient. There is a lot waste heat in this construction!
To actually make this yourself, keep reading! More testing and results in the end.
Features:
- Adjustable output voltage
- Adjustable RPM of cooling fan
- Adjustable temperature monitor
- Adjustable voltage limiter
- Adjustable construction height
- Optional USB-connector
- Easy to assemble/disassemble
- 400g
- 90x90x80mm
Applications:
This can be used with a broad range of heat sources and power a broad range of products.
- Candles (low output power)
- Spirit burner/stove (hard to control)
- Gas burner/stove (best so far)
- Wood stove (not yet tested)
- Camp fire (not yet tested)
- Metal can with fire (not yet tested)
- Barbecue (not yet tested)
- Light in the dark (LEDs)
- USB charger (Phones, batteries, etc.)
- External fan (cooling effect, fire booster, etc.)
- USB-gadgets (music player, drink cooler, etc.)
- Charge super capacitor and power high intensity SOS signals
Step 1: Materials
This is what I used.
- 1x high temperature TEG module: TEP1-1264-1.5
- 2x voltage step-up (from this project: https://www.instructables.com/id/Adjustable-Voltage-Step-up-07-55V-to-27-55V/)
- 1x small heat sink. From old PC (BxWxH=60x57x36mm)
- 1x Aluminum plate: BxWxH=90x90x6mm
- 1x 5V brushless DC motor with plastic fan (could be hard to find, check this link)
- Fixation for heat sink: Aluminum bar (6x10x82mm)
- 2x M3 bolts+2nuts+2x washers for heat sink: 25mm long
- 2x M3 1mm thick metal washers
- 4x M4 bolts+8x nuts+4x washers as construction base: 70mm long
- 4x M4 1mm thick metal washers
- 4x M4 bolts: 15-20mm long
- 4x Drywall screw (35mm)
- 2x heat insulated washers: Constructed from cardboard and old plastic food turner
- 80x80x2mm corrugated cardboard (Not very good at high temperatures)
- 2x pull springs: 45mm extended
- (Optional) Components for a temperature monitor and voltage limiter. Described further on
Tools:
Drill and thread tap for M3 and M4
File and abrasive paper
Screwdriver
Pliers
Loctite power glue (Repair Extreme)
Price:
It cost me about 80€ for everything but the most expensive part was the TEG-module (45€).
TEG spec:
I bought the TEP1-1264-1.5 at http://termo-gen.com/
Tested at 230ºC (hot side) and 50ºC (cold side) with:
Uoc: 8.7V
Ri: 3Ω
U (load): 4.2V
I (load): 1.4A
P (match): 5.9W
Heat: 8.8W/cm2
Size: 40x40mm
Next step: Construction of base plate
Step 2: Construction (Base Plate)
This will be the "hot side". It will also act as construction base plate to fixate heat sink and some legs.
- How you construct this depends on what heat sink you are using and how you want to fixate it.
I started to drill two 2.5mm holes to match my fixation bar. 68mm between them and the position is matched of where I want to put the heat sink. Holes are then threaded as M3. - Drill four 3.3mm holes at the corners (5x5mm from outer edge). Use a M4 tap for threading.
- Make some nice looking finishing. I used a rough file, a fine file and two types of sand paper to gradually make it shine! You could also polish it but it would be too sensitive to have outside.
- Screw the M4 bolts through the corner holes and lock it with two nuts and one washer per bolt plus the 1mm washer on the top side. Alternative one nut per bolt is enough as long as the holes are threaded. You can also use the short 20mm bolts, depends on what you will use as heat source.
Step 3: Construction (Heat Sink)
Most important is to fixate the heat sink on top of the base plate but at the same time isolate the heat. You want to keep the heat sink as cooled as possible. The best solution I could came up with was two layers of heat insulated washers. That will block the heat from reaching the heat sink through the fixating bolts. It need to handle about 200-300ºC. I created my own but it would be better with a plastic bush like this. I could not find any with high temperature limit. The heat sink needs to be under high pressure to maximize the heat transfer through the module. Maybe M4 bolts would be better to handle higher force.
How I made the fixation:
- Modified (filed) aluminum bar to fit in the heat sink
- Drilled two 5mm holes (should not be in contact with bolts in order to isolate heat)
- Cut two washers (8x8x2mm) from old food turner (plastic with max temp of 220ºC)
- Cut two washers (8x8mmx0.5mm) from hard cardboard
- Drilled 3.3mm hole through plastic washers
- Drilled 4.5mm hole through cardboard washers
- Glued cardboard washers and plastic washers together (concentric holes)
- Glued plastic washers on top of aluminum bar (concentric holes)
- Put M3 bolts with metal washers through the holes (will later be screwed on top of aluminum plate)
Base plate will get very hot and also the air above. To block it from heating up the heat sink other than through the TEG module I used a 2mm thick corrugated cardboard. Since the module is 3mm thick it will not be in direct contact with the hot side. I think it will handle the heat. I could not find a better material for now. Ideas appreciated!
Update: It turned out the temperature was too high when using a gas stove. The cardboard become mostly black after some time. I took it away and it seems to work as good as before. Very hard to compare but I have not seen any larger degradation. I´m still looking for a replacement material to test with.
Cut the cardboard with a sharp knife and fine tune with a file:
- Cut it 80x80mm and mark up where the module (40x40mm) should be placed.
- Cut the 40x40 square hole.
- Mark up and cut the two holes for M3 bolts.
- Create two slots for TEG-cables if neccessary.
- Cut 5x5mm squares at the corners to make place for M4 bolts.
Step 4: Assembly (Mechanical Parts)
Assembly:
- Mount TEG-module on heat sink.
- Place cardboard on heat sink and TEG-module is now temporally fixated.
- The two M3 bolts go through the aluminum bar and then through the cardboard with nuts on top.
- Mount heat sink with TEG and cardboard on base plate with two 1mm thick washers in between to separate cardboard from the "hot" base plate.
- The assembly order from top is bolt, washer, plastic washer, cardboard washer, aluminum bar, nut, 2mm cardboard, 1mm metal washer and base plate.
- Add 4x 1mm washers on the upper side of base plate to isolate cardboard from contact
Then screw the 40x40mm fan on top of the heat sink with 4x drywall scews. I added some tape also to isolate screws from electronics.
Next step: Electronics
Step 5: Electronics
You find the step-up project here:
https://www.instructables.com/id/Adjustable-Voltage-Step-up-07-55V-to-27-55V/
I added two more requirements for this project:
- TEG-module needs to be protected from overheating
- iPhone needs to be protected from to high voltages
TEG-module will break if temperature exceeding 350ºC on hot side or 180ºC on cold side. To warn the user I built an adjustable temperature monitor. It will turn on a red LED if temperature reach a certain limit which you can set as you like.
When using to much heat the voltage will go above 5V and that can damage certain electronics. The step-up can only step up and not step down. I could not find a solution that does both and thereby designed my own adjustable voltage limiter. It combines an operational amplifier and a zener diode to detect a certain voltage and then feed the output signal to a MOSFET transistor. The transistor will shortcut the whole power source but only if higher than voltage limit (5V). That will quickly increase the current and since the TEG-module has a limited output effect it will consequently drop the output voltage. That means it will burn away all energy as heat but at the same time keep a very stable voltage, it simply cannot exceed 5V. It also turns on a LED so the user can turn down the heat source until the LED goes off again. A simpler solution would be to only use a zener diode to feed output voltage to ground if above 4.7V. But that is not as distinct and probably burn up. I could only find a 5W zener and that is not enough.
The heart of this circuit is a low voltage operational amplifier. I use a MCP6002 which operates at 1.8-6V. It has two units inside which means you can combine both the temperature monitor and voltage limiter with the same circuit.
How to build it is similar to the step-up project, look at that first! Components needed:
- IC: MCP6002
- 8PIN socket for IC
- R3,R4,R5: 1KΩ
- R6: 22KΩ
- R7, R8: 470Ω
- R9: 100KΩ
- R10: 10KΩ
- R11: PT1000 temperature sensor
- R12, R13: 68KΩ
- R14, R15: 47KΩ
- P2, P3: 1KΩ (maybe 10KΩ works, not tested)
- D3, D4: Red LED
- D5: 4.7V zener diode, low effect
- T1: High effect MOSFET transistor, BUZ12 or similar
- Have a look at my circuit layout and try to understand it as good as possible.
- Measure the exact value of R3, it is later needed for calibration
- Place components on a prototype board according to my pictures.
- Make sure all diodes has correct polarization!
- Solder and cut all legs
- Cut copper lanes on prototype board according to my pictures
- Add needed wires and solder them too
- Cut prototype board to 43x22mm
I placed the temperature sensor on the cold side of TEG-module. It has a max temp of 180ºC and I calibrated my monitor to 120ºC to warn me in good time. The platinum PT1000 has a resistance of 1000Ω at zero degrees and increases its resistance along with its temperature. Values can be found HERE. Just multiply with 10.
In order to calculate the calibration values you will need the exact value of R3. Mine was for example 986Ω. According to the table the PT1000 will have a resistance of 1461Ω at 120ºC. R3 and R11 form a voltage divider and the output voltage is calculated according to this:
Vout=(R3*Vin)/(R3+R11)
The easiest way to calibrate this is too feed the circuit with 5V and then measure the voltage on IC PIN3. Then adjust P2 until correct voltage (Vout) is reached. I calculated the voltage as this:
(986*5)/(1461+986)=2.01V
That means I adjust P2 until I have 2.01V on PIN3. When R11 reach 120ºC, the voltage on PIN2 will be lower than PIN3 and that trigger the LED. R6 works as a Schmitt trigger. The value of it determines how "slow" the trigger will be. Without it, the LED would go off at the same value as it goes on. Now it will turn off when the temperature drops about 10%. If you increase the value of R6 you get a "faster" trigger and lower value creates a "slower" trigger.
Calibration of voltage limiter:
That is much easier. Just feed the circuit with the voltage limit you want and turn P3 until the LED goes on. Make sure the current is not too high over T1 or it will burn up! Maybe use another small heat sink. It works the same way as the temperature monitor. When the voltage over zener diode increases above 4.7V it will drop the voltage to PIN6. The voltage to PIN5 will determine when PIN7 is triggered.
USB Connector:
The last thing I added was the USB connector. Many modern smartphones will not charge if it´s not connected to a proper charger. The phone decide that by looking at the two data lines in the USB cable. If the data lines is fed by a 2V source, the phone "thinks" it connected to the computer and start to charge at low power, around 500mA for an iPhone 4s for example. If they are fed by 2.8 resp. 2.0V it will start charging at 1A but that is too much for this circuit. To get 2V I used some resistors to form a voltage divider:
Vout=(R12*Vin)/(R12+R14)=(47*5)/(47+68)=2.04 which is good because I will normally have a bit under 5V.
Look at my circuit layout and pictures how to solder it.
Next step:
Assembly (Electronics)
Step 6: Assembly (Electronics)
- Tape the motor to avoid shortcuts and to get better grip
- Glue the cards together so that they fit around the motor
- Place them around the motor and add two pull springs to hold it together
- Glue the USB connector somewhere (I did not find a good place, had to improvise with melted plastic)
- Connect all cards together according to my layout
- Connect the PT1000 thermal sensor as close as possible to the TEG-module (cold side). I placed it beneath the upper heat sink between the heat sink and cardboard, very close to the module. Make sure it has good contact! I used super glue that can handle 180ºC.
- I advise to test all circuits before connected to the TEG-module and start heating it
Next Step:
Test and results
Step 7: Tests and Results
I made the following tests:
- Cooling fan lowest speed: 2.7V@80mA => 0.2W
Cooling fan highest speed: 5.2V@136mA => 0.7W - Heat source: 4x tealights
Usage: Emergency/read lights
Input power (TEG output): 0.5W
Output power (excluding cooling fan, 0.2W): 41 white LEDs. 2.7V@35mA => 0.1W
Efficiency: 0.3/0.5 = 60%
Comment: Could probably get a little bit more, maybe 0.2W - Heat source: 6x tealights
Usage: Power LED
Output power (excluding cooling fan @ 30% speed): 0.44W - Heat source: gas burner/stove
Usage: Charge iPhone 4s
Input power (TEG output): 3.2W
Output power (excluding cooling fan, 0.7W): 4.5V@400mA => 1.8W
Efficiency: 2.5/3.2 = 78%
Temp (approx): 270ºC hot side and 120ºC cold side (150ºC difference)
Comment: Only run shorter periods - Heat source: gas burner/stove
Usage: Charge iPhone 4s
Output power (excluding cooling fan @ 75%): 4.25V@300mA => 1.3W
Comment: This was a long stable test. Charging at 300mA seems to be very stable regarding fan speed and temperatures. I also used the gas stove at very low power. Higher power did not help much, just increasing the temperatures on both sides for little increase in output power. - Heat source: Additional heat transfer + alcohol burner
Usage: Power LED
Output power (excluding cooling fan): 0.14W
Comment: The heat transfer is not good enough, TEG voltage too low for charging iPhone.
Prototype 1:
This is the first prototype. I constructed it at the same time I wrote this instructable and will probably improve it in the future. I have measured 4.8V@500mA (2.4W) output, but could not run at that power for longer periods. The optimum charging speed for iPhone turned out to be 4.25V/300mA = 1.3W. I tested over a long period with stable result. It is a bit tricky though to adjust the electronics for optimal output. If I increase the current over 300mA (at low gas power), then the step-up starts to limit the current (voltage) due to low input voltage from TEG (see graph images of my "voltage step-up" project). When that happen the charging power drastically drops to about 0.2W. I had to adjust the USB voltage/current to be just below that limit, 4.35V without load and 4.25V while iPhone 4s charging. I found out that a fan speed of 60-80% was optimal in this test.
I compared the "gas stove charging" with a "mintyboost charging" using two AA alkaline batteries. Two batteries weight 46g and manage to charge the iPhone from 20% up to 36%. The exactly same charging interval took 60g of gas. The batteries wins this time regarding weight, but as I wrote, this construction can be optimized in many ways! If you also need to carry back the empty batteries, then the gas wins!
- Current weight of the whole module with all electronics is 400g
- Outer dimensions are (WxLxH): 90x90x80mm
Conclusion:
I don't think this can replace any other common charging methods regarding efficiency but as an emergency product I think it´s quite good. If I can find a stable way of using this with wood (camp fire), then it would be very useful when hiking in a forest!
Improvement suggestions:
- Water cooling system (pot)
- A light weight construction that transfer heat from a fire to the hot side
- A buzzer(speaker) instead of LED to warn at high temperatures
- More robust insulator material, instead of cardboard.
- Took away cardboard insulation layer. Could not handle temperatures from gas stove.
- Experimented with additional heat transfer accessory from a more aggressive fire, see images. It can replace the base plate or be attached to the existing base plate. Tested with alcohol burner but got only 0.14W output. I guess aluminium is not good enough as heat transfer and it probably needs a layer of insulation to not cool before it reaches the base plate. The idea was to put this into a real fire with good ember, might try that also. I want to try with copper but that is expensive and hard to come by.
- I tested to replace the upper heat sink and fan with a small can of water from this project: LED Power from Fire
I could easily charge the phone with 1W of power and the weight was reduced to only 150g! Water cooling is highly recommended.
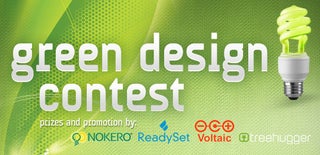
Third Prize in the
Instructables Green Design Contest