Introduction: Benchtop Media Blasting Cabinet
Recently, during the boredom of a northern winter, I restored a 70 year old Craftsman Drill Press. I used wire wheels on various drill motors, bench grinders and angle grinders with decent results, but it was a tedious process. My next project is a Bandsaw from the 1940's. It has many internal cavities in the casting that just can't be reached easily with wire wheels, so I considered media blasting. I shopped around, looking at blasting cabinets for sale and found the least expensive one to be $105.00. Me being on the cheap side, I decided to build one myself. The store bought units was only 30" wide. I needed to have 42" of width to blast the parts for my bandsaw. I built a bench top version because I only plan on using it on occasion. It will be stored on a shelf most of the time.
Step 1: Cutting the Cabinet Panels
I will start by saying that I had no plan or drawing for this project. Like many of my projects , I figure them out as I go along. Since this is a bench top version, I did not have the space (height) to build a funnel shaped hopper floor, so I built the floor of the cabinet to slope towards one end of the cabinet for abrasive removal. I decided to use 3/4" plywood for the ends of the cabinet so that the front, back and top panels could be fastened to the ends. The rest of the panels are 3/8" plywood , in a effort to keep the overall weight down. I cut the end pieces 20" wide by 25" tall with an angle on the front side close to 45 degrees. The back panel is 43-1/2" wide by 25" tall. The front panel is 43-1/2" wide by 15" tall. Both front and back panels have a 3/4" x 3/4" x 44-1/4" cleat fastened to the inside bottom at an angle. I measured up 5" from the bottom edge of the panel on one end and up 2" from the bottom of the opposite end to come up with the desired angle. Then I glued and nailed the cleats in place, they slope towards the end of the cabinet that will have the door. The door will be cut out of one of the end pieces later in the build.
Step 2: Assembling the Cabinet
I started the cabinet assembly process by ripping angles on 2" x2" boards that matched the angles on the end panels, then screwed them with 1-5/8" drywall screws ,making sure to drill pilot holes first . Again I will add, I did not pre-engineer this cabinet. I did not cut the end panel angles to any specific angle rather I used what looked good and provided an ample amount of visibility into the box. When I ripped the boards, I simply transferred the angles from the end panels to the 2x2's, then set the blade angle on my table saw to match. Some things are just easier this way, no need to over think things sometimes.
Next, I glued and screwed the back and front and top panels onto the end panels. I also added 3/4" x 3/4" cleats to the inside of the end panels to support the floor as well. I cut the floor panel to 20" x 43-1/4" and fastened it in place.
Step 3: Fitting the Window
- For the viewing window I used a 14" x 30" x .100 thick piece of clear acrylic. I installed 2"x2" cross members to support the ends of the window panel. I spaced them 30" on center. Then I used a small trim router and milled out a 3/4" wide slot, .100 deep, around the inside perimeter of the window cavity to allow the window panel to lay flush with the 2x2 surround wood. The window is sandwiched in place with plywood strips. I used 7-1/2" x 14-1/4" pieces of plywood on the right and left sides of window and 2, 1-3/4" x 28-1/2" plywood strips for the top and bottom of the window. I waited to install the window until the inside was painted, to make for easier painting.
Step 4: Creating Armholes
To create armhole gaskets I used a pair of 4-1/2" toilet flanges with a seperate metal outer ring. This outer ring is cool because it allows the plastic flange to rotate inside the metal ring. I traced holes 16" on center and cut them out with a jigsaw. The flanges are mounted from the inside of the cabinet, with only the plastic inserts protruding through the front. After a test run with my arms I decided the holes needed to be higher up in the enclosure. I re-cut the holes as high up the front of the cabinet as I could, then cut new holes in a couple of strips of plywood to cover the old holes. Viola! It almost looks like its a design accent. *Remember, " its only a mistake if you cant work past it".. This is one of the downfalls of designing on the fly.
Step 5: Creating a Door
To make a door for the cabinet I laid out lines parallel to the perimeter of the end panels, about 1-1/2" inside of the edges to maintain structural integrity. I then stood the cabinet on end , climbed on a stool and cut the door out using a circular saw and a jigsaw. Next I installed door stop around the perimeter of the door opening so the door will have something to rest against while closed. Then I placed the door in position , with a small shim under the bottom edge to maintain the proper spacing, and installed the hinges and latch. After the interior of the cabinet was painted, I installed 1/2" wide , self sticking weather strip to the door stops to provide a tight seal
Step 6: Vacuum Connection
I choose to install a vacuum line to keep the dust down inside the cabinet and help prevent abrasive leaks to the outside. I am using a small shop-vac with a 1-1/4" diameter hose end fitting (pipe). Looking through my collection of plumbing fittings I found the perfect solution. I used a 1-1/4" tailpiece connector which is normally used on a sink drain . The vacuum cleaner pipe fit inside the nylon gasket perfectly. The fitting I had was made to fit inside of a 1-1/2" schedule 40 pipe fitting ( ie. an elbow , tee etc) . In order to hold the fitting in place inside the cabinet, I cut the outer hub off a 1-1/2" reducer bushing. This left a plastic ring that I glued in place on the section of the fitting that stuck out inside the cabinet with PVC cement .
Step 7: Finishing Up
First I primed the inside of the cabinet with a latex wood primer. Then I used latex caulk to seal along all the joints and seams before applying the final coat of paint. I welded up a floor grate out of a bunch of 3/16" diameter steel rods. It rests on a couple of 1" wood blocks at the low end of the sloped floor , door end, to allow the grate to set level above the collecting abrasive. I drilled a 1" hole in the opposite end of the cabinet to accommodate the air hose and abrasive feed line. I bought some awesome gloves at Harbor freight for $7 . They reach all the way up to my shoulders. They have elastic cuffs on the end which wrap tightly around the armhole flanges, no clamps needed. I also installed a LED strip light inside on the ceiling of the cabinet. I placed it inside a clear poly-carbonate tube used to cover fluorescent light bulbs for protection.
Step 8: Conclusion
In conclusion I must say that this project has been a success. The vacuum line works very well to keep all the dust under control. The gloves are plenty long enough to reach all areas of the cabinet. I can usually blast for about 45 minutes before its time to open the door and clean out the abrasive. This is an easy task, using the vacuum to suck it out , then emptying the vacuum back into the abrasive reservoir. I also added a few pieces of scrap tin under the grate to act as a backstop for the blasting
I was able to build this cabinet with very little investment. I did not have to purchase any lumber , as I had left over scraps from previous projects. I spent $15 on the clear acrylic window , $10 for the toilet flanges, $5 on the hinges and latch, $3 on weather stripping and $7 on the long gloves...So for about $40 I have a custom sized blasting cabinet that not only saved me a bunch of money, but was a fun project to build..
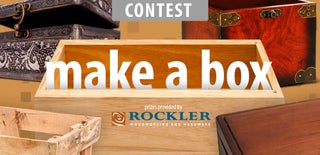
Runner Up in the
Make a Box Contest
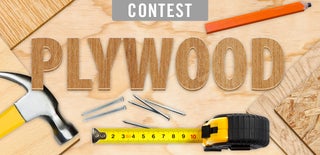
Second Prize in the
Plywood Contest