Introduction: Bentwood Rings With Stone Inlay
This is an easy bentwood ring making guide for ring bands & inlay. These rings are VERY strong miniature structures basically for wooden rings.
Step 1: Wood
Wood is a natural source so every ring does come out slightly different looking each time because of wood grain patterns. Choosing which wood is best for bentwood rings can vary with each section of veneer wood depending on the grain structure. Recommended raw (no paper backed) veneer thickness is 1/36" or 1/42. The best sections of wood are evenly spaced and straight long-grained wood. Quartersawn veneer is usually best for those results.
Once you have this veneer, make a 12" strip and 1/2" wide.
Step 2: Prep
Get a square of paper towel and wrap the piece of wood snuggly around it.
Next, get it soaked in water from the sink, and then slightly squeeze most of the water off so that the towel is not dripping any longer.
Microwave this wet paper towel with the wood strip two times. First time is for 20 seconds, re-wet the towel like previously, then again for 15 seconds.
Step 3: Prep Cont.
Get a pole that is between 1" and .5" round/thick and some regular tape along with the freshly microwaved wood strip.
Break off a 4" piece of tape and keep it within reach for later.
Begin to slowly wrap the wood around the pole. The wood does not need to be perfectly flat, this is still prep and not making the final ring. Try to do your best to keep the wood from snapping or cracking while wrapping it on the pole.
Once it is all wrapped, take the piece of tape to keep the wood wrapped while it dries in this spiral shape. Slide it off the pole for drying.
Step 4: Sizing
Ring sizes are usually measured by the inside band's diameter in mm. Whatever size you are needing, go slightly below that (-.4mm) when wrapping tape around the pole until desired thickness. This helps you have room while sanding away on the inside at the end.
Get a roll of masking tape & a pole that is smaller than the ring size you are needing for the next step.
Step 5: Wrapping
This is the big moment. Are you ready? This is the foundation of the ring so this you will need to have patiences.
First, you are going to need the pole, something to hold down the pole, masking tape, and an electronic measurer for precise measurements.
Second, wrap as much tape as you need WITH THE STICKY PART UPWARDS onto the pole until the diameter is what you need for the ring size + equal all around the tape (no waves, needs to be flat). THEN lay a separate piece of tape STICKY PART DOWN to keep the other section of tape from spinning on the pole.
Forth, sand the inside end of the prepped veneer. Make sure the veneer is dried by this point. This takes 24 hours usually, but at least give the prepped band 12 hours of drying before wrapping. You don't want the wood wet because it will cause your superglue to turn a white color when it dries.
Fifth, stick the sanded end of veneer on the sticky tape and add a drop of super glue. Wrap the veneer around tightly once until it meets the end again. Press your finger on the meeting point to make sure it dries flat to eachother. *Flatness and no gaps between the wraps is key to a good bentwood ring.*
Yes btw, you will have a serious case of "glue fingers" during this wrapping, and no you don't want gloves because the gloves WILL rip and tear and be glued into your ring forever. Super glue will eventually flick off your fingers with time. Make sure not to glue your fingers together as well.
Sixth, continue to add a couple of drops of super glue to the remaining strip of veneer as you slowly and carefully wrapp the rest of the band together.
Step 6: Sanding
I suggest using a dremel sander for this part. It will take you all day using your hands and sand paper.
When sanding the inside part of the ring, VERY carefully get rid of the end strip inside. Have a ring pole sizer handy to make sure the band stays around the correct size.
For the edges, sand until the desired ring width. For the top part, try to smooth it out without digging into the ring band too much.
Have a sheet of 220 or lower grit sand paper to flatten the edges if need be.
Step 7: Inlaying
After freshly sanding your ring to shape, get a vice and two squared pieces of wood to hold onto your ring as you work on it.
First, get some toothpicks & your super glue to help you move the tiny stones around when placing into the grooves.
Second, use a triangle shaped metal file to precisely carve away channels for your inlay. Get creative!
Third, put a single drop of super glue in the carved out channel, then start placing pieces of inlay.
Forth, once all of the channel is filled, keep applying layers of glue until the grooves are filled above the top layer of wood.
Fifth, use your dremel to carefully sand down the excess glue and stone bits so they are level with the ring surface.
Step 8: Practice
Practice makes perfect! Once you have mastered the basic bentwood ring band, then you can move onto more complicated stuff like inlaying stone.
Check out my Instagram to see what is going on in my studio as I make bentwood ring orders from my Etsy shop. @thetreehearts
Step 9: Finishing
You will need 220, 400, 600, 1000 & 1200 grit sand paper. Start from the lower grit to the highest grit.For a finish, I personally use an organic beezwax and olive oil finish. You can use mineral oil, coconut oil, walnut oil, hemp oil, or olive oil as well.
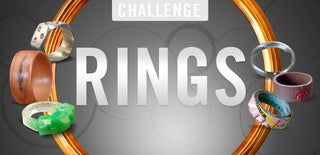
First Prize in the
Rings Challenge