Introduction: Block Printed Beer Labels
I don't want you to get the wrong impression-- I'm definitely not a master at either homebrewing or printmaking. But, I am pretty darn good at figuring out how to make food and beverages look nice. And after relegating my homebrews to plain brown bottles, (yawn) I decided it was time to figure out how to make a label that was as attractive and carefully crafted as my beer. This is a project that can totally be tackled by a first time printmaker, and still get beautiful results. I might also add that nothing about this technique limits it to beer-- I can imagine custom soda labels, wine bottles or even jam jars would have beautiful results.
For those of you who are uninitiated to the hobby/cult of homebrewing, making labels for beer poses a few logistic challenges. First, the ink must not be water soluble. The first drop of condensation on the bottle will turn your label into a bleeding mess. So absolutely no ink-jet printing, and no water soluble inks. The oil-based inks and relatively ease with which you can make prints led me to block printing. I'll be the first to admit that my block printed design is not the easiest solution. (Printing labels with an laser printer definitely seems like the easiest.) But I loved the idea of a handmade label-- it seems to suit a handmade beer particularly well. And if you do go to the trouble to cut a block for printing, you can then print your design on all sorts of things-- cardboard (for coasters!), fabric (beer-themed canvas bags! T-shirts!) And best of all, you've got the block already made and will be able to quickly churn out new labels the next time you brew a batch of that particular beer. And if you know a home brewer and make them a custom label as a gift... Well, then you've made a friend for life.
The second obstacle is adhering the label to the bottle. If you plan on reusing your bottles (as most home brewers do) then you'll want the label to come off the bottle without leaving a messy residue. But obviously, you want the label to stay put on the bottle while you store it, chill it and serve it. I did a bunch of reading, and a few experiments and found a solution that works great: milk. (Yes, really!) Lots of brewers use milk straight from the fridge. Skim milk is the preferred choice, at it has all the adhering proteins, but none of the fat that could potentially make dried milk smelly. I don't regularly buy skim milk, so I made a glue using nonfat dried milk. Not only is this glue solution more concentrated than plain skim milk, but (because of dried milk's shelf life) you can whip up this glue even if you don't happen to have extra milk in the fridge.
.
Step 1: Materials
Materials
Depending on what materials you have on hand, you might not need to buy too may new tools to make a block print. If you haven't made prints before, there are a few that you'll need though (namely block printing ink and a brayer). If you're crafty, you've probably already got most of the other materials lying around.
For Carving Your Block:
Block -The material that you carve into is the biggest decision you'll make. You can use wood, linoleum, sheets of rubber sold for carving, or even a large rubber eraser. A harder material (like wood) will last longer. A softer material (like linoleum or rubber) will wear out and get damaged more quickly. The up side is that softer materials are much easier to carve. So you could carve a rubber eraser using a razor knife, but you'll need special tools to carve linoleum and wood.
Carving Tools- Depending on what surface you will be carving, you'll need to get the appropriate tools. Little sets of carving tools for block printing are available at art stores. Or if you have a dremel (as I do) you can take advantage of electricity. I did my carving for this block exclusively with a dremel fitted with a flex shaft. Using a dremel and a hard block material, it is possible to get pretty precise details. If I were using a softer material, it might be more difficult to get fine details to come through.
Carbon Paper- You'll need this to transfer your design to your block. But you can always use a pencil (along with some vigorous scribbling action) in a pinch.
Pencils, Pens and Paper
For Printing:
Oil-Based Block Printing Ink- The oil-based ink is the key to making printing work for a beer label. You'll find it at most art and craft stores.
Brayer- For newcomers, the brayer is the roller thing that looks like a paint roller with a smooth rubber surface. In order to make block printing work, you need to transfer an even surface of ink onto your block. This is precisely what brayers are made for. It is easiest to apply ink if your brayer is about the same width as the block you will be printing on.
A piece of glass or plastic. Smooth, non-porous surface you don't mind getting dirty. A small sheet of glass works well. I wrapped a piece of scrap wood in plastic wrap.
Large tablespoon or other smooth surface for putting pressure on the paper
Paper- Whatever you want to print on. I tried out a couple of different colors and combinations for prints. In the end, my favorites were 3 1/2" by 8" strips cut from non-glossy magazine pages printed with white ink. I like the layered effect that printing on top of another photo gives. (Also: I feel like a good little recycler, repurposing those old magazines.)
Cooking or baby oil, glass cleaner and lint-free rags . Oil based inks have lots of advantages, but they can also make a mess. I don't like to use more (toxic) solvents than necessary, so I've opted for a cleaning method that requires a little more elbow grease, but still gets the job done.
Glue:
Powdered Milk
Small Paintbrush
Step 2: Design Your Label
Before designing your label, you'll need to pick the size and shape of the block you want to create. My design is 3 1/4" square. I picked a size that I thought looked good on the bottle, and coincidentally, it also turns out to be the perfect size for making a coaster. Your block, design and paper all need to conform to the shape and size that you select.
Now on to the design part: think simple. Is this your first time carving? Think even simpler. I'd start with text and play around with shapes, spacing and placement until you've got something you like. If you are drawing by hand, fill in your design in ink to get a good idea of what it will look like. The delicacy of pencil is not going to come through in a block printed design- bold gestures and high contrast are your friends.
Because this beer recipe uses honey, I decided on a bee theme. A hexagon grid was the background, and then I fit in text with the name of the beer in one of the cells. Then I added a few bees (along with their knees), cropped the whole thing down to a square, and presto!
Step 3: Prepare Your Carving Block
If you are using rubber or linoleum, all you need to do is cut the block down to the size you want and you're ready. If you are using wood, you'll want to sand down the surface until it is very, very smooth. After doing this wood carving (my first!) I have added a second step-- paint the surface of the wood white. I found it is helpful when you're carving to be able to see when you've carved through some of the top layer.
Step 4: Invert & Transfer Your Design
You'll need to make a mirror image of your label design so that it will print the way that you designed it. If you don't have carbon paper, you can vigorously scribble in pencil onto the back of your design, then when you trace over it the design will transfer. Place your design where you want it on your block. Cut the carbon paper to fit between the block and the design template. Tape your design template to the block on one side. You want to fix the orientation of the design on the block, but I like to be able to lift it up and make sure that my tracing is transferring well. Last, trace over the design, making sure that you've got all the important details. Now remove the design template and fill in all the darkened areas with ink. (This will make it easier to not get confused when you get into carving mode).
Step 5: Carve Your Block
Now you have one last design decision to make-- which parts of your design will be printed with ink, and which will be left blank. Remember, you can use white ink to print, so the light parts don't have to be the blank ones. Once you decide to carve one color (either the black or the white) away, there is no going back.
Tips and techniques for carving will be very different depending on what material and carving tools you are using. Still I've got a few general pointers that I think help in most cases.
1 Go slow. The nice thing about making a block print is that you'll have that block to reproduce later, but if you rush the carving and make a sloppy pattern, you probably won't want to.
2. Carve similar shapes one right after the other. Just like anything else, your technique will get better with repetition, and it's more likely that your results will be consistent throughout the cut.
3. Start with the details first. (I'm sure that some folks disagree with me on this.) I find it easiest to cut all the detailed edges first, then hollow out the middle afterward.
4. Remember that (ultimately) you're carving will be reduced to just a surface which will either receive ink, or not. This is both good and bad. Good, because you don't have to worry too much about how pretty the areas you've carved away look (it won't matter to the print). But it can be bad, too, once you've carved an area away, there is no going back-- sanding and smoothing might make your block look nice, but they won't necessarily change how the print will come out.
Step 6: Print
Now it's time to clean up your block. With linoleum or rubber this is pretty simple. With wood, you'll want to make sure that you carefully brush all the sawdust out of the carving. I found it helpful to squish a small piece of scrap clay into the block to remove hanging bits of sawdust. Once you start, printing will go pretty quickly, so make sure you have everything you need together before you start. Ink, brayer, a non-porous surface to spread your ink on, a spoon (or other smooth object) to help transfer the ink and paper to print on.
Squeeze a small amount of ink out onto your sheet of glass or plastic (think the amount of toothpaste that you use.) Roll the brayer across the ink repeatedly, eventually the ink will start to spread out. Keep rolling, changing the direction every so often until you have the ink spread out thinly and evenly. With a little practice, you'll notice that the brayer makes a pleasant velcro-like sound when it is rolled over properly spread ink. You'll probably have to experiment a few times to get the hang of it. I'd err on the side of spreading your ink too thinly-- you can always add more, but if you have gloppy ink all over the place, it will be tricky to clean up.
Run your perfectly inked brayer across the surface of your block. You'll want to run it over your block a few times, and in different directions until you are satisfied that you have an even coating of ink across the surface of your design. Grab the first piece of paper that you want to print on. Pick up the block and place it down on the surface of the paper, wherever you want the print to be. Press the block down firmly. Delicately lift it up-- if all goes well the paper will adhere to the ink and you'll pick them both up together. Flip the block over so that the paper is now facing up. Take your spoon and, gently at first, press the paper down into the block. Increase the pressure gradually and keep working the paper down into the block. Now carefully lift up the paper to reveal your print! Set prints aside to dry, and move on to the next one. Before you know it, you'll have a good rhythm going and you'll have made prints on every surface within reach.
Once you've made all the prints you'd like to, you'll need to clean up all of your ink-covered tools. Run the brayer over lots of scrap newspaper to transfer off as much of the ink as you can. Then rub the brayer with a little baby oil, and wipe it clean with a rag. To clean your glass, scrape away as much ink as possible, then spray with glass cleaner and wipe off the ink residue.
Step 7: Attach Labels
Once your labels are printed and dried (oh, and the beer is brewed, primed and bottled) you can attach your labels. In a small bowl mix together 1 T. powdered milk with 1 T. water. stir the two together until there are no lumps. The larger the area that you apply glue to, the firmer the label will be affixed. But applying liquid to a larger area will also make it trickier to keep the paper from buckling and warping. So you've got to figure out a balance for your project. I found applying glue to a half inch strip on either side of the label held them firmly in place, and wasn't too difficult to apply smoothly. Carefully smooth the paper over the glass until it adheres (just a few seconds). Now smooth down the rest of the label, wrapping it around the bottle. Paint glue over the other side of the label, and hold that end down across the bottle until it adheres. Voila! To remove the labels, just soak the bottles in water, and the glue will loosen and wash off easily.
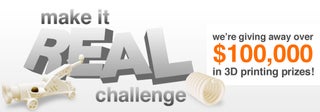
Participated in the
Make It Real Challenge