Introduction: Build a Massive Snowmobile Tank Bike
After getting inspired by the final episode of American Choppers and then seeing my neighbors driving around on their snowmobiles, I set out to make a crazy combination of the two as a pedal-powered monstrosity. I designed and constructed this bike in just under three weeks using three broken bikes, some steel tubing and angle iron, and an old 1990 Polaris snowmobile track.
It’s a fun challenge recycling old bike parts and converting them into a new bike, and this massive, 7 foot long bike provided some unique challenges. Integrating the tread with the bike frames and turning through a big track on a heavy bike that doesn’t allow for traditional high-speed steering is definitely an adventure.
A MIG welder and a regular hacksaw served as the primary tools for construction, in addition to a common set of wrenches and screwdrivers. This is definitely a great project for diy bike or snowmobile enthusiasts with some junk bikes, scrap material, and free time.
Step 1: Planning the Internal Frame
After getting all the necessary tools, parts and as many bikes as possible, start by planning out how to integrate the snowmobile track with the bike frames. Children’s mountain bikes with 20” tires fit nicely inside of the track, and the knobby mountain bike tires fit snugly in the gap where the sprockets are supposed to fit. I found that the limited space inside of the tread accommodated a three wheel configuration more easily than all four wheels.
Start by disassembling the two bikes for the interior assembly down to just the frame with the pedals. Cut down the frames so that they fit inside the track with enough clearance for it to rotate. The frames will be kept parallel with the addition of the third wheel between them in the back. Center the third wheel down the middle of the track by welding the seat and chain stays from an additional bike frame to the inside of the other bike frames, giving another set of dropouts where the wheel could conveniently be attached. When welding to the bike frames, make sure to sand or grind all of the paint off of the surface of the metal. The dropouts on the third wheel also make it easier to remove the tread by just taking off that third wheel first. *Be sure to dimension the assembly so that the track is snug with deflated tires so that once you inflate the wheels, the track will be tight without having any other mechanism to tension it.
Step 2: Coordinating the Drive
Originally, I wanted the pedals to go in front of the track, but for the sake of simplicity and efficiency in using the existing bike frames without having to run the chain back inside of the track to the wheels I continued to use the original pedal location inside the tread. The downside was the mild discomfort of having to straddle the wide tread while riding, but this turned out to not be a problem, as the pedal arms in the vertical position are above the top of the track. This also meant that the two sets of pedals had to be perfectly aligned so that the would rotate around the same axis when pedaling. Also, the distance from the crankset to the axle of the drive wheels must be the same so that both wheels turn the tread together. The two frames we had for the drive were not very compatible, and I needed to cut new dropouts into one of the frames to maintain the right relations. You should check the alignments, unless using two of the exact same frames, and altering the dropouts would probably be a good idea.
Once everything was aligned, remove the two interior pedal arms and cut them down to the point that they will have clearance with the third wheel as they rotate inside the tread. Weld a piece of angle iron joining the two, allowing both frames to be synchronized when pedaling, and make sure that the connection is very durable. It helped to make a jig to keep the crank arms in line to assure that the pedals would rotate on as close to a common axis as possible.
Also make sure that the gear ratios on each frame are the same to that the drive wheels remain synchronized.
At this point, we had something resembling an odd tank tread unicycle…
Step 3: Develop the Frame
Now the final, external frame must be constructed in order to attach the seat and handlebars. I simply welded angle iron segments vertically on the bike frames from which to have the steel tubing come out and up to the seat. Then add tubes across the top of the track in the front and back, making a triangular shape, with a long tube serving as the bike's spine running right down the middle for attaching the handlebars and front wheel. It helps to drill holes in the tube and angle iron between members, making a joint so that the tube can pivot. This holds it together so that you can find the right configuration and location of the frame pieces, then you just weld over the bolts to make a stable. I actually left several of these joints as just bolts so that the entire top frame can be unbolted and removed as a modular unit should the track ever need to be removed for repairs.
Make sure that the connections of the vertical members to the bike frames are durable enough to hold up the rider, but also don't interfere with the chain or other moving components inside the track. I found that it's also convenient to mount the top of the seat tube at the intersection of the rear horizontal bar and the spine.
Step 4: Steering Mechanism and the Front
Probably the most difficult challenge is finding a method to steer with the friction from the weight of a heavy bike over the large surface area of the tread.
The track has enough friction and momentum that it would plow through another regular wheel in front, and if the wheel was heavy enough to have enough friction with the ground, it would make the bike even more inefficient. The bike is also so heavy and slow that you don’t experience the usual effects of high speed turning as with a regular bike. There are a lot of options that might work, but I made use of the extra head tubes from the disassembled bikes to go with a lightweight and fun design.
Make a cross with two head tubes so that the handlebars can rotate in the traditional way for steering, but also on a horizontal axis so that the front wheel can swing up and down freely. Pushing the handlebars up/forward in a bench press motion forces the front wheel into the ground, and picks the front of the tread off of the ground entirely so that all the weight is on the front wheel and it can control the bike. The angle iron chopper bike extensions on the fork put the front wheel far enough in front of tread so that they don’t interfere, and extends the bike to its massive length of 7 feet. The addition of the long angle iron, Ghost Rider style handlebars allows you to control the wheel from back at the seat, and gives you enough leverage to easily jack up the bike while you’re sitting on it. This unconventional method takes a lot of practice to get used to shifting your weight differently during a turn and can't make very tight turns, but it still works.
Even if it’s not the most comfortable, effective, or intuitive method of steering, at least you can still push down on the handlebars for the easiest wheelie ever.
Step 5: Finishing Touches
In the end, it’s good to just go back and reinforce any weak spots to make sure the welds don’t break, particularly on the front where there’s a lot of stress from lifting the bike. I also didn’t get to run the brake cable all the way up the handlebars, and trying to stop the track from turning by squeezing it with your legs gets old, so the addition of coaster brakes after the fact might not be a bad idea either.
Finally, you can’t have a bike without some LED underglow lighting, making this tank bike perfect for any weather conditions at any time of the night!
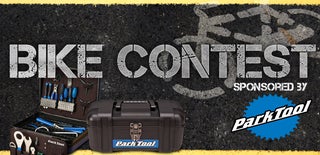
Grand Prize in the
Bike Contest