Introduction: Build a Plank on Frame Model Ship
Welcome! My name is Bob Hunt and I build model ships for a hobby. I've been building these wonderful models for over 23 years now. I want to share with you a very detailed set of instructions on how to build a fairly simple "Plank on Frame" model ship.
The ship I've chosen for this Instructable is known as the Hannah. It was the first ship in George Washington's Navy. The first photo shows what the finished model will look like.
"Plank on Frame" means that the planking on the hull is laid across actual frames that are similar to the actual frames of a real ship of this time period. This particular model is not what we modelers call "historically correct" because the framework that makes up the hull is a stylized method of framing and not an actual duplication of the historical framework used.
The woods used in this model are not your garden variety of woods. In other words, you can't run down to your local home improvement store and buy them. But they are readily available through certain exotic wood importers such as http://www.gilmerwood.com . They sell all kinds of wood including woods that are well suited for model ship building.
The frames, keel, and some of the outer planking are made of a wood known in the hobby as boxwood. This is not the same boxwood shrub that might grow in your yard. It's a kind of tree that grows in various parts of the world and has virtually no visible grain and is very hard.
Some of the outer planking is Virginia holly, a very clear, white wood, as is the deck planking. The pinkinsh wood is called Swiss Pear and is also used for the upper planking, mouldings and some of the deck furniture. The black wood across the hull is ebony.
All of these woods can be obtained through Gilmer Wood (mentioned above). Milling the wood to the dimensions needed to build this model does require a miniature table saw and a regular woodworking table saw or band saw. Additional information on milling the wood will be covered in the next step of these instructions.
To build this model, a set of plans are needed. For this model, I needed to create the frame drawings in particular. After doing some additional research I was able to find the two key drawings needed to loft a set of frame drawings. A body plan and waterline drawing for a Colonial Fishing Schooner very similar to the Hannah. These drawings were drawn by a gentleman by the name of Howard I. Chappelle, who is no longer alive, however, many of the books he wrote on naval architecture are still found in bookstores today.
Using Chappelle's body plan and waterlines, I was able to loft a set of frame drawings for my model. Photos of some of my CAD work are shown with this step. I am providing a complete set of my CAD drawings for this Instructable in a ZIP file. All drawings needed to build the model are included in PDF format and can be printed on standard 8-1/2" x 11" bond paper. Some of these drawings would not fit on a single sheet of paper, so 2 or 3 drawings were created that can be taped together to form the complete drawing (using the black reference lines found on both halves).
The drawings can be downloaded from my website at http://bobsmodelships.com/HannahDrawings.zip . You might also want to browse my website to see additional photos of my construction of the Hannah model as well as some other models I've designed in AutoCAD and buit from scratch. Hannah was the first scratch built model I made where I developed plans in AutoCAD. In later models I not only used AutoCAD to design them but CAM software and a router mill to cut all of the parts out. Feel free to check out my website at http://bobsmodelships.com for photos of some of these models.
After downloading the ZIP file, unzip it to any directory you wish to work from. You may open the unzipped PDF files with Acrobat Reader. These files all have meaningful names that you can easily distinguish. You will be told what drawings need to be printed for each step of these instructions.
To aid in the framing of the model, a special jig is used. This jig holds the framework in perfect alignment until the outer hull planking is applied. I'll cover the construction of the jig in full detail later in this Instructable.
Please do not be intimidated by the complex appearance of the finished model. These instructions will explain the complete construction of the model in step by step detail. Anyone with wood working skills should be able to build this model, provided of course, that they have the proper tools. I will be covering tools needed as well.
So let's get started!
Step 1: Tools and Supplies Needed
First, I'd like to cover some of the tools you will need to build this model. Many of these tools can be purchased from Micro Mark (http://www.micromark.com) or Model Expo (http://www.modelexpo-online.com). Here is a list of tools I find helpful in all of my model building (Not every tool is needed to build this model. I will tell you what tool I used for making each part at the beginning of each step of these instructions):
1. No. 5 Exacto knife handle (Micro Mark #36117).
2. No. 2 or equivalent Exacto knife handle (Micro Mark #14351 or 70233).
3. #10, #11 and #22 Exacto blades (Micro Mark #14360, 36102 and 36113).
4. Micro Saw Blades (Micro Mark #14346)
5. Dremel Rotary Tool (Micro Mark #82592)
6. Helping Hands (Micro Mark #21120)
7. Variable speed scroll saw or Jewelers Saw (for cutting out frames - Micro Mark #22105)
8. Byrnes Miniature Table Saw (for cutting small parts - http://www.byrnesmodelmachines.com/)
9. Swiss style watchmakers tweezers (Micro Mark #19101)
10. Deluxe pin vise (Micro Mark #82110)
11. Dimensioned mini-square (Micro Mark #82147)
12. Steel machinist square (Micro Mark #10117)
13. Angled high precision micro shear (Micro Mark #80334)
14. Tweezer nose pliers (Micro Mark #80338)
15. Mid size file set (Micro Mark #81063)
16. Stainless steel 6” ruler (Micro Mark #10114)
17. Sand It (Micro Mark #84048)
18. Micro drill bit set (Micro Mark #60362)
19. 3” Toolmakers angle plates (Micro Mark #60626)
20. Office clips, small and medium size
21. Pan vise (Micro Mark #21123)
22. Bench top mini disk/belt sander (Micro Mark #82218)
23. 9” band saw or 10" table saw (for milling your own wood)
24. Veneer Calipers for measuring wood thickness (Micro Mark #82556)
25. Planer or thickness sander
There are several items I use regularly in my model building that constantly need replenishing. So that you will be prepared when the time comes, here is a list of certain supplies you will find yourself using routinely:
1. Weldbond White Glue
2. Zap A Gap Super Glue (Micro Mark #80877 or 80878)
3. Z Ends (for Zap A Gap - Micro Mark #80890)
4 Five Minute Epoxy
5. #10, 11, 13 and 22 Exacto Blades and Knife
6. 100, 150, 220, 330 and 400 Grit Sandpaper
7. #0000 Steel Wool
8. Polyurethane Satin, Wipe On Poly or Sanding Sealer
9. Toothpicks (for mixing epoxy)
10. Rubbing Alcohol (for ungluing Weldbod if you make a mistake)
11. Single edge razor blades (for making moldings)
Other items may be needed as we progress and I will try and give some advance notice of these items when they come up.
CAUTION: PLEASE READ THE INSTRUCTIONS THAT CAME WITH ALL OF YOUR POWER TOOLS TO UNDERSTAND THE SAFETY PROCEDURES ASSOCIATED WITH THE USE OF EACH TOOL. USE EXTREME CARE AROUND ALL MACHINERY AND EXERCISE DILIGENCE. MODEL SHIP BUILDING IS A FUN HOBBY BUT SAFETY IN THE WORKSHOP IS RULE NUMBER ONE. BE ESPECIALLY CAREFUL WITH HOBBY KNIVES. REMEMBER, A DULL BLADE IS MORE DANGEROUS THAN A SHARP ONE BECAUSE YOU TEND TO USE MORE FORCE TO MAKE THE BLADE WORK FOR YOU. A SLIP OF THE BLADE CAN CAUSE SERIOUS INJURY. CHANGE BLADES OFTEN, KEEP ALL EQUIPMENT CLEAN AND SHARP, AND BE CAREFUL! KNOW YOUR TOOLS AND HOW TO HANDLE THEM.
Step 2: Milling Wood
Before I begin with the actual instructions for building this model, I'd like to go over the process I use to mill wood for a model ship. Any serious model ship builder will have these tools in his workshop.
Tools Needed:
10" table saw or 14" band saw with resaw blade
Planer or thickness sander
Byrnes miniature table saw with .035" blade
CAUTION: PLEASE READ THE INSTRUCTIONS THAT CAME WITH ALL OF YOUR POWER TOOLS TO UNDERSTAND THE SAFETY PROCEDURES ASSOCIATED WITH THE USE OF EACH TOOL. USE EXTREME CARE AROUND ALL MACHINERY AND EXERCISE DILIGENCE. MODEL SHIP BUILDING IS A FUN HOBBY BUT SAFETY IN THE WORKSHOP IS RULE NUMBER ONE. BE ESPECIALLY CAREFUL WITH HOBBY KNIVES. REMEMBER, A DULL BLADE IS MORE DANGEROUS THAN A SHARP ONE BECAUSE YOU TEND TO USE MORE FORCE TO MAKE THE BLADE WORK FOR YOU. A SLIP OF THE BLADE CAN CAUSE SERIOUS INJURY. CHANGE BLADES OFTEN, KEEP ALL EQUIPMENT CLEAN AND SHARP, AND BE CAREFUL! KNOW YOUR TOOLS AND HOW TO HANDLE THEM.
Most of the wood purchased from Gilmer Wood comes in small boards that are 2" to 4" wide and 1" to 2" thick. As an example, let's say that you need billets to make frames for this model. Those billets must be 1/8" thick or .125" thick. They must be 24" long and 1" wide.
Start by first cutting your boards into billets that are 1/4" thick using your table saw or band saw. The extra thickness is needed so that the finished billets will be smooth on both sides, without saw blade teeth marks.
After cutting your board into billets 1/4" thick, run them through a planer taking a little off each side until the thickness is 1/8". I use veneer calipers to measure my billets. A tolerance of +/-.010" is acceptable for model ship building.
Once you have created these 1/8" thick billets, rip them to their proper width, 1" in this example, using your table saw or miniature table saw. Then cut them to length, 24" in this example.
For smaller pieces of wood needed to make various parts on the model, I first mill a billet that is the required thickness of the part I want to make. For example, the hatches on this model are .093" thick and .210" wide (length varies). To make such a small part, I would first cut a board into billets that are 5/16" thick. Then I would run the billet through a planer until the thickness had been reduced to .210" (+/- .010").
From that billet, I can now use my miniature Byrnes table saw to rip strips that are .093" thick. It's the same process you might use to cut large boards down to smaller boards to make a piece of furniture. The only difference is that you are working with much smaller dimensions so you need a much smaller saw to cut such pieces without tearing the wood up. The Byrnes miniature table saw was designed for model ship builders precisely for this purpose.
Step 3: Making the Keel
The various PDF files that you downloaded are used as templates to make the various parts of the model. Whenever I say to use a particular drawing as a template to make a particular part, you should print an extra copy of that drawing so that you still have the original for reference. Some part templates are cut out from a particular drawing. For example, in this step, the keel template is cut out from the Side View drawing.
Because a model ship often uses wood that must be milled to very small dimensions, all fractional measurements given in these instructions will be in thousandths of an inch. For example, rather than use 1/4", I will use .250" when giving this measurement.
Wood needed for this step:
(1) 17" x .250" x .250" boxwood - keel
(1) 15" x .062" x .250" boxwood - rising wood
(1) 15" x .250" x .125" boxwood - frame spacers
Tools needed for this step:
Byrnes miniature table saw
Xacto knife handle
#10 or #22 Xacto blade
Rubber cement
CAUTION: PLEASE READ THE INSTRUCTIONS THAT CAME WITH ALL OF YOUR POWER TOOLS TO UNDERSTAND THE SAFETY PROCEDURES ASSOCIATED WITH THE USE OF EACH TOOL. USE EXTREME CARE AROUND ALL MACHINERY AND EXERCISE DILIGENCE. MODEL SHIP BUILDING IS A FUN HOBBY BUT SAFETY IN THE WORKSHOP IS RULE NUMBER ONE. BE ESPECIALLY CAREFUL WITH HOBBY KNIVES. REMEMBER, A DULL BLADE IS MORE DANGEROUS THAN A SHARP ONE BECAUSE YOU TEND TO USE MORE FORCE TO MAKE THE BLADE WORK FOR YOU. A SLIP OF THE BLADE CAN CAUSE SERIOUS INJURY. CHANGE BLADES OFTEN, KEEP ALL EQUIPMENT CLEAN AND SHARP, AND BE CAREFUL! KNOW YOUR TOOLS AND HOW TO HANDLE THEM.
We'll begin construction of our model with the keel. Start with your keel piece that is 17" x .250" x .250". At the fore end, a scarf joint is cut. The first photo in this step shows this scarf joint. Use the drawing(s) with the file name "Frame Plan 1.pdf", "Frame Plan 2.pdf", and "Frame Plan 3.pdf" for a template of the keel (tape the three drawings together).
When I say to use a drawing as a template, I mean that you must cement the drawing to the wood using rubber cement. After cementing the template to your keel wood strip, cut the strip to the precise length using the template and your Byrnes miniature table saw.
You will notice that the aft end is cut at a slight angle. You can use your miniature table saw to cut this angle by setting the cross cut slide to match the angle in relationship with the blade. Making small parts for a model ship is no different than making large parts for a piece of furniture. Other than the tool used, the process is the same.
The scarf joint can be cut on your Byrnes saw also. Using calipers, lock the calipers at a length/height of .095". You should set the height of your Byrnes saw blade to this measurement by placing the caliper extension on the top of the saw table and raising/lowering the blade to touch the bottom of the caliper fixed length end. I like to use a blade with a thickness of .035" for this kind of cut.
Once the blade is set to the right height, set the cross slide to 90 degrees to make a cut across the top of the wood strip. You want to align the edge of the blade with the edge of the joint.
After making the first cut, set the blade to a height of .170" and make a second cut at the other end of the joint, again, aligning the blade with the template pattern joint edge.
With these two cuts made, you can complete the joint using your Xacto knife with the #10 or #22 blade. Refer to the first photo in this step to see and understand the exact shape needed for the scarf joint.
Before removing the keel template from the wood strip, you must also cut the sternpost joint at the aft end. This joint is .043" deep. It is best to use your Xacto to cut this joint due to the angle of the joint. The Byrnes saw blade cannot be tilted so cutting the two sides of the joint can only be done with hand tools. After cutting the joint out, you can remove the paper template. Be sure to rub all of the rubber cement off with your finger as well.
The next step is to cut the rabbet joint in the keel. The rabbet joint was common on all wooden ships. It is a "V" shaped groove that runs the length of the keel and helps to make a water tight seal where the planking meets the keel. You can see a pencil line across the keel which will be the top of the rabbet joint. This line is .062" below the top of the keel. The "V" groove will be cut from the top of the keel to this line. It is .062" deep. This means that the center of the joint is .031" from the top of the keel.
If you haven't already done so, remove the template since it is no longer needed. Make sure you rub off all of the rubber cement with your finger. Then draw a line across your keel exactly .062" from the top. Now, using your Xacto with the #10 or #22 blade, cut from the line at an angle to a point in the center of the line and top of the keel. Short cuts from the line upwards and from the top of the keel downwards are used.
The 2nd photo shows the cutting of the rabbet joint using a hobby knife. Take your time, and try to keep the "V" groove straight and consistent in shape and depth. You may want to practice first on some scrap wood.
The rabbet joint extends to the point where the aft side of frame 23 sits. Stop cutting the rabbet joint at that point. Of course, you will have to cut the joint on both sides of the keel.
In the 3rd photo, folded sandpaper is used to clean up the rabbet joint and the 4th photo shows the completed rabbet joint. In that photo, the rising wood has been added. This is the strip of wood that is 15" x .062" x .250". You want to cut this piece to length first so that it matches the Side View drawing. Notice that it stops at the fore side of the sternpost and is cut at an angle to match the angle of the stern post. The fore end starts at the scarf joint.
Your keel should now look like the 4th and 5th photos in this step. Now you will add the frame spacer pieces. You will need the piece of wood stock that is 15" x .125" x .250" for these pieces. Each piece is the cut to the exact same length, .336".
Making a series of pieces the exact same length on the Byrnes saw is not as difficult as it may sound. First, take a piece of wood of any thickness and about 2" long. Using an office clip, clamp it to the blade side of the fence. The tip of the wood piece should be positioned at about the middle of the blade
Next, move the fence so that it is exactly .366" from the clamped piece of wood (use your calipers to make this measurement). Once you've set the fence, all you have to do is use your cross slide to make slices of the wood strip. Slide the wood strip up against the clamped scrap on the fence and make the cut. Each piece will be exactly the same length. You will need 21 of these pieces.
After cutting these spacers, lay your keel over the Frame Plan drawing and mark the location of each spacer, then glue each one on at the marks you made.
In the 6th photo, you can see how the rising wood relates to the rabbet joint and how the frames sit on top of it. To keep the frames spaced properly, these spacers lock each frame in position. The 7th photo in this step shows the keel after gluing these frame spacers to the top of the rising wood. The eighth photo shows how a frame is held snugly to the keel using these frame separation pieces.
This completes the construction of the keel. In the next step, you will make the stem and fore deadwood.
Step 4: Adding the Stem
You will remember from the previous step that there was a scarf joint at the fore end of the keel. Now you will make the stem which has a corresponding joint where the two parts are joined. The fore deadwood sits on the keel and inside edge of the stem. The curved line that this joint forms is the forward stem portion of the rabbet joint. The 1st photo shows these two parts.
Wood needed for this step:
(1) 6" x 3" x .250 boxwood - Stem and fore deadwood
Tools needed for this step:
Variable speed scroll saw
Xacto knife handle
#10 or #22 Xacto blade
Scissors
Rubber cement
CAUTION: PLEASE READ THE INSTRUCTIONS THAT CAME WITH ALL OF YOUR POWER TOOLS TO UNDERSTAND THE SAFETY PROCEDURES ASSOCIATED WITH THE USE OF EACH TOOL. USE EXTREME CARE AROUND ALL MACHINERY AND EXERCISE DILIGENCE. MODEL SHIP BUILDING IS A FUN HOBBY BUT SAFETY IN THE WORKSHOP IS RULE NUMBER ONE. BE ESPECIALLY CAREFUL WITH HOBBY KNIVES. REMEMBER, A DULL BLADE IS MORE DANGEROUS THAN A SHARP ONE BECAUSE YOU TEND TO USE MORE FORCE TO MAKE THE BLADE WORK FOR YOU. A SLIP OF THE BLADE CAN CAUSE SERIOUS INJURY. CHANGE BLADES OFTEN, KEEP ALL EQUIPMENT CLEAN AND SHARP, AND BE CAREFUL! KNOW YOUR TOOLS AND HOW TO HANDLE THEM.
The template for making the stem is the file "Stem and Stern Deadwood.pdf." To simplify things, you can cut the stem and deadwood out as one piece if you like. First cut out the template using scissors. Then rubber cement it to your wood. Use a scroll saw to cut the part out. There is a disadvantage to using a single part though. It makes cutting the rabbet joint much more difficult. That is why I recommend cutting the two individual parts out rather than cutting one complete part of the two. Cut them out on the scroll saw.
You want to test fit the scarf joint of the stem with the scarf joint of your keel. If you were careful in cutting the stem with its joint on the scroll saw, the fit should be pretty close. You can use your Xacto and #10 or #22 blade to make small adjustments. The 2nd photo shows the stem mated to the keel using the scarf joint.
You will notice that when the stem is mated to the keel. the top edge meets the top edge of the rabbet joint. You want to continue the rabbet joint up the top edge of the stem, but the shape changes from a "V" to a "U" channel as shown in the 3rd photo. Again, use your Xacto to make this cut, and be sure to make it on both sides before you glue the stem to the keel.
The last step is to glue the fore deadwood to the stem. The aft end of the deadwood should connect to the rising wood . The 4th photo shows what the completed assembly looks like. You should lay your keel assembly over the Frame Plan drawing to be sure that it matches as closely as possible.
In the next step you will make and attach the sternpost and stern deadwood to the keel.
Step 5: Adding the Sternpost and Stern Deadwood
The final assembly of the keel structure is to add the sternpost as shown in the 1st photo and the stern deadwood as shown in the other photos.
Wood needed for this step:
(1) 5" x 3" x .125 boxwood - stern deadwood
(1) 5" x .250" x .375" boxwood - sternpost
(1) 17" x .062" x .250" walnut - false keel
Tools needed for this step:
Variable speed scroll saw
Byrnes miniature table saw
Xacto knife handle
#10 or #22 Xacto blade
Scissors
Rubber cement
CAUTION: PLEASE READ THE INSTRUCTIONS THAT CAME WITH ALL OF YOUR POWER TOOLS TO UNDERSTAND THE SAFETY PROCEDURES ASSOCIATED WITH THE USE OF EACH TOOL. USE EXTREME CARE AROUND ALL MACHINERY AND EXERCISE DILIGENCE. MODEL SHIP BUILDING IS A FUN HOBBY BUT SAFETY IN THE WORKSHOP IS RULE NUMBER ONE. BE ESPECIALLY CAREFUL WITH HOBBY KNIVES. REMEMBER, A DULL BLADE IS MORE DANGEROUS THAN A SHARP ONE BECAUSE YOU TEND TO USE MORE FORCE TO MAKE THE BLADE WORK FOR YOU. A SLIP OF THE BLADE CAN CAUSE SERIOUS INJURY. CHANGE BLADES OFTEN, KEEP ALL EQUIPMENT CLEAN AND SHARP, AND BE CAREFUL! KNOW YOUR TOOLS AND HOW TO HANDLE THEM.
The 1st photo shows that the keel is tapered at the stern. This is simple to shape with your Xacto knife and #22 blade. By scraping the surface of the keel on both sides, you can reduce the thickness of the keel at the sternpost. The tapering should begin where frame "23" is located.
The sternpost is made from a single piece of wood that is .250" thick. The piece of wood must first be cut to length, and the lower joint must be cut out. This can be done with an Xacto. Use the Frame Plan drawing to ensure that the sternpost is set at the proper angle on the keel.
You can rubber cement a template (taken from the Frame Plan drawing) to the wood so that the joint can be cut and the overall shape of the sternpost can be cut out. You will notice that the sternpost tapers from top to bottom. It also tapers from side to side so that the lower end matches the width of the keel.
After shaping the sternpost, glue it to the keel using Weldbond. Lay the keel assembly over your Frame Plan drawing to make sure that the angle of the sternpost is correct. Leave the assembly alone until the glue has dried.
While the glue is drying on your sternpost, cut out the stern deadwood on your scroll saw. Use a template taken from the Frame Plan drawing, and rubber cement it to the piece of wood. It's best to cut the angled lower end first on the Byrnes saw so that you have two straight edges. Then the remainder can be cut on the scroll saw.
The deadwood is attached to the keel and sternpost as seen in the 3rd photo. Use Weldbond to glue it. It should be aligned side to side on the keel so that it is centered on the keel. This will leave a recess on each side of about 1/16" or .062", but that recess will get smaller at the sternpost because you tapered the keel on each side.
The rabbet joint you cut into the keel earlier needs to be extended about 1/4" so that it extends onto the stern deadwood. This extension of the rabbet joint is "L" shaped. You can see a faint pencil line on the keel in the 3rd photo where the rabbet joint needs to be extended. This can be done with your Xacto knife.
Next, you need to taper the stern deadwood in the corner where it meets the sternpost. If you look at the 3rd photo which shows a "before" shot of the stern deadwood, and look at the 5th photo, you will see how the deadwood has been shaped with a hobby knife so that the aft corner area is recessed. This is necessary so that if planking were applied to the lower hull, it would be flush with the sternpost where the planks lay across the deadwood.
You can make a template of the curved area that is tapered by tracing the bottom of frames 25 through 28 shown on the Frame Plan drawing. The frames will attach to the side of the deadwood later on, so the deadwood must be flat and perpendicular to the keel in the area where the frames attach. However, the area below the frames should be tapered so that the recessed lip formed by the deadwood is the same width from end to end. This is all part of the rabbet joint where the planking would lie against the frames and deadwood.
If you look at the 5th photo, you can see that the rabbet joint also extends upward across the deadwood where it is attached to the sternpost. The shape goes from an "L" shape at the corner of the keel and sternpost, to a "U" shape as it extends upward across the deadwood to the top of the sternpost. The sternpost helps to form the rabbet joint just as the fore deadwood did at the bow. Keep in mind that the purpose of the rabbet joint is to enable the planking to form a water tight seal where it meets the keel, fore deadwood, and stern deadwood.
The last photo shows the keel fully assembled. A contrasting piece of wood has been glued to the bottom of the keel serving as the false keel. I like to use a contrasting wood for the false keel because it just gives the structure some class.
Step 6: Making Frame Blanks
To make the frames, you will use a method of making frame blanks made from strips of wood glued up in two layers. This layering technique is commonly referred to as sistered framing. The ZIP file of drawings includes an individual drawing for each frame as well as 3 different frame blank drawings. The frame drawings are all in the PDF file called "Frame Drawings.pdf." The frame blank drawings are labeled according to the frames that can be cut out from the blank. The shape of the blank pieces can be seen in the first photo for this step. There is also a drawing for each frame blank called "Frame Parts 1.pdf", "Frame Parts 2.pdf", and "Frame Parts 3.pdf" which shows the individual parts for each frame blank.
Wood needed for this step:
(46) 24" x 1" x .125 boxwood - frame blanks
Tools needed for this step:
Byrnes miniature table saw
Xacto knife handle
#10 or #22 Xacto blade
Rubber cement
Scissors
Office clips
CAUTION: PLEASE READ THE INSTRUCTIONS THAT CAME WITH ALL OF YOUR POWER TOOLS TO UNDERSTAND THE SAFETY PROCEDURES ASSOCIATED WITH THE USE OF EACH TOOL. USE EXTREME CARE AROUND ALL MACHINERY AND EXERCISE DILIGENCE. MODEL SHIP BUILDING IS A FUN HOBBY BUT SAFETY IN THE WORKSHOP IS RULE NUMBER ONE. BE ESPECIALLY CAREFUL WITH HOBBY KNIVES. REMEMBER, A DULL BLADE IS MORE DANGEROUS THAN A SHARP ONE BECAUSE YOU TEND TO USE MORE FORCE TO MAKE THE BLADE WORK FOR YOU. A SLIP OF THE BLADE CAN CAUSE SERIOUS INJURY. CHANGE BLADES OFTEN, KEEP ALL EQUIPMENT CLEAN AND SHARP, AND BE CAREFUL! KNOW YOUR TOOLS AND HOW TO HANDLE THEM.
Frame blanks consist of two layers of wood glued together to form a "U" shape. The two layers are made up of several parts cut at different angles to form this "U" shape. The joints of one layer are in a different location than the joints of the other layer. It's kind of like making your own plywood with two layers of wood. We all know how strong and sturdy plywood can be.
The 1st photo shows the shape of the pieces in the frame blank that must be cut out. On the right side of the photo you see the pieces for half frame blanks, frames 24 through 34. On the left side you see the pieces for the frame blank for frames 1, 21, 22 and 23. The frame blank for frames 2 through 20 is similar to the blank from frames 1, 21, 22 and 23.
The wood for these layers will be .125" thick. The width of the frame blank pieces is 1". A single strip of frame blank material is 24" long so all of the pieces for one half of a frame will fit on the frame blank material. That means that you will need approximately 68 strips to make all of the frames, but for this step, you only need 46 as I will cover the half frames and their blanks in another step.
Let's look at a frame drawing as shown in the 2nd photo. This CAD drawing I made shows a profile of the frame. You can see that one of the layers of wood stops short of the full height of the frame. We won't worry about this when our frame blanks are made. I'll explain this later on in these instructions.
You'll also notice in the 2nd photo that the actual frame is only about half as tall as the frame blank. This is by design. Later I will show how the frames are installed into a special jig which will hold them all in alignment. In the end, this extra length of wood will be cut off when the model is cut away from the jig that held it together.
The 3rd photo shows how the patterns for the frame blank are laid out on a billet of wood for cutting. For cutting these pieces, you want to use a thin blade such as the .035" blade I mentioned earlier. It makes a very clean cut and easily slices through the frame blank material.
The following videos show and help to explain the process I used to cut frame blank pieces out on a Preac table saw. (NOTE: The Preac table saw is no longer available. I bought it over 20 years ago when I first started building model ships from scratch. It is very similar to the Byrnes miniature table saw I recommended earlier in these instructions).
Photos 4 through 14 show how the frame blank pieces were cut out as you saw in the video clips. The 15th photo shows a stack of frame blank pieces waiting to be glued together.
Photo 16 and 17 show how a frame blank is glued together. You may use any good carpenter's glue to glue these. I prefer Weldbond but Titebond works just as well. Weldbond is thicker and can be unglued by soaking the joint in alcohol.
I like to dry fit the pieces together first, and I lay a frame drawing over the blank to make sure that it will fit on the blank. Sometimes slight adjustments need to be made to the intersections of the frame blank parts. This is the nice thing about these blanks. By adjusting the location where they get glued, you can make the blanks slightly larger or smaller in overall size.
NOTE: You will need to print out a copy of each frame drawing that came in your ZIP file. Then you will need to cut out the frame drawing by cutting around the outside edge only. Do not cut the inside edge. I'll cover this later in the next step.
The layers are glued up separately. When the glue has been given ample time to dry, clean the excess glue off of the surface by scraping it, not sanding it. Then glue the two layers together as shown in the 6th photo. As you can see, the top layer has a butt joint in the center bottom area, and it is centered over the other layer which does not have such a joint. This is not only by design but also represents some historical accuracy. The layer with the center bottom joint represents the first futtock and top timber. The layer without this joint represents the floor and second futtock which make up a complete frame. Just a little trivia for you. There'll be a test later on! Just kidding.
The remaining photos in this step help to explain the making of the frame blanks and how the frame drawings are used to double check the fit. In the next step, I'll show you how to turn this frame blank into an actual frame. For now, you'll need to make up all of your frame blanks numbering each one with the frame number that will be cut out from it. After gluing the blanks and allowing the glue to dry, sand the surfaces with a sanding block and 150 grit sandpaper.
Step 7: Cutting Out the Frames
Wood needed for this step:
Frame Blanks made from previous step
Tools needed for this step:
Variable speed scroll saw
Scissors
Rubber cement
Sanding block
Sandpaper
Minwax Wipe on Polyurethane
CAUTION: PLEASE READ THE INSTRUCTIONS THAT CAME WITH ALL OF YOUR POWER TOOLS TO UNDERSTAND THE SAFETY PROCEDURES ASSOCIATED WITH THE USE OF EACH TOOL. USE EXTREME CARE AROUND ALL MACHINERY AND EXERCISE DILIGENCE. MODEL SHIP BUILDING IS A FUN HOBBY BUT SAFETY IN THE WORKSHOP IS RULE NUMBER ONE. BE ESPECIALLY CAREFUL WITH HOBBY KNIVES. REMEMBER, A DULL BLADE IS MORE DANGEROUS THAN A SHARP ONE BECAUSE YOU TEND TO USE MORE FORCE TO MAKE THE BLADE WORK FOR YOU. A SLIP OF THE BLADE CAN CAUSE SERIOUS INJURY. CHANGE BLADES OFTEN, KEEP ALL EQUIPMENT CLEAN AND SHARP, AND BE CAREFUL! KNOW YOUR TOOLS AND HOW TO HANDLE THEM.
You will cut out each frame using a scroll saw. Let's look at the 1st photo in this step.
You see that I have printed my frame drawing with the center line. I have also cut a small rectangular hole in it. The purpose of this hole is to help align the frame drawing on the frame blank's center line. I've used rubber cement to glue the frame drawing to the frame blank.
You may be wondering why the frame drawing is so tall. This is typical for a model that will be built using a "Hahn" style building jig. Years ago a fellow modeler by the name of Harold Hahn developed a series of model ship plans which he sells to other modelers.
Mr. Hahn invented a special jig for holding the framework together until hull planking can be applied. Modelers have adapted his jig for their own model building and given it the name "Hahn jig". The frames have this extended piece on them so that they will fit into the jig and be held in place. Later in these instructions, I will show you how to make the jig, and you'll see its importance and how these extended frame pieces come into play.
They say a picture is worth a thousand words, so the remaining photos and videos should explain step by step, how to take these frame blanks and turn them into actual frames for the model. Enjoy!
In the last 2 videos, I demonstrated how to bevel the frames using a Dremel tool with a drum sanding attachment. At the bow and stern of the model, the hull curves thus causing the frames to be stair stepped initially. To alleviate this stair stepped effect and produce a smooth hull surface, the frames in those areas were beveled. However, since building this model I have built many others and have learned that this beveling process is not necessary.
Once the hull of the model has been framed in the building jig, it will be necessary to sand it until it is faired out. I found that even though the frames had been beveled beforehand, fairing was still needed and in fact, more wood was being removed in the fairing process than was needed. The frames became thinner than they should have been. I recommend that you not bevel the frames but wait instead, to fair the fully framed hull which will put the bevels in automatically as you sand.
The last 3 photos in this step show the finishing of the frame. I've come to prefer to finish my models with Minwax Wipe on Polyurethane. This is a very thin finish that enhances the beauty of the wood without making the model look like it has a heavy finish on it.
After sanding, I apply three coats of the finish to the parts and let each coat dry for 4 to 6 hours. Then I rub the part out with #0000 steel wool. Three coats and three steel wool rubbings produces a very smooth and enhanced finish that really brings out the beauty of the wood. These photos show what I mean.
You will also notice that I installed treenails in my frame. These treenails are made with a special attachment for the Dremel tool. They do not provide any additional strength to the frame and are merely to provide some additional historical accuracy. I won't go into the details on how to make your own treenails. Suffice it to say, it's not fun!
Step 8: Making the Cant Frames
Cant frames are actually half frames. Instead of sitting on top of the keel as the full frames do, cant frames attach to the side of the fore deadwood at the bow and the side of the deadwood at the stern.
Wood needed for this step:
(22) 24" x 1" x .125 boxwood - frame blanks
Tools needed for this step:
Byrnes miniature table saw
Xacto knife handle
#10 or #22 Xacto blade
Rubber cement
Scissors
Office clips
CAUTION: PLEASE READ THE INSTRUCTIONS THAT CAME WITH ALL OF YOUR POWER TOOLS TO UNDERSTAND THE SAFETY PROCEDURES ASSOCIATED WITH THE USE OF EACH TOOL. USE EXTREME CARE AROUND ALL MACHINERY AND EXERCISE DILIGENCE. MODEL SHIP BUILDING IS A FUN HOBBY BUT SAFETY IN THE WORKSHOP IS RULE NUMBER ONE. BE ESPECIALLY CAREFUL WITH HOBBY KNIVES. REMEMBER, A DULL BLADE IS MORE DANGEROUS THAN A SHARP ONE BECAUSE YOU TEND TO USE MORE FORCE TO MAKE THE BLADE WORK FOR YOU. A SLIP OF THE BLADE CAN CAUSE SERIOUS INJURY. CHANGE BLADES OFTEN, KEEP ALL EQUIPMENT CLEAN AND SHARP, AND BE CAREFUL! KNOW YOUR TOOLS AND HOW TO HANDLE THEM.
Making the cant frames is not much different than making the full frames. You start with a frame blank that is two layers thick (.125" each). These layers have two pieces each with staggered joints as shown in the 1st photo. After the parts are cut out, the layers are glued up separately. Then the 2 layers are glued together as shown in the 2nd photo.
And finally, the frame pattern is glued to the frame blank and cut out on the scroll saw. Of course you need a left side and a right side frame as shown in the 3rd and 4th photos. Be sure to number each frame as many of them are similar in shape.
The frames are finished in the same manner as before. You might wonder why I finish the frames now when they have to be sanded later to fair the hull out. I put a finish on my frames before assembly for two reasons. First, it will be more difficult to apply the finish once the frames are in the building jig because there's only a small space between each frame. Second, the finish helps in the fairing process by showing any areas that have not been completely sanded. After fairing (the sanding and smoothing out of the hull surface), the finish on the surface of the frames is gone and must be reapplied. However, applying the finish to the hull surface is much easier than applying it between each frame.
Step 9: Making the Building Jig
We're almost ready to start assembling our model. But before we can do that, we need to construct the building jig. As I mentioned earlier, the jig is needed to hold the framework together and in proper alignment. The jig style is commonly referred to as the "Hahn" style jig.
Wood needed for this step:
(1) 24" x 12" x .187" (3/16") plywood
(1) 24" x 12" x .500" (1/2") plywood
(3) 24" x 2.50" x .500" poplar or pine
(1) 24" x 6" x .500" poplar or pine
Tools needed for this step:
Table saw
Variable speed scroll saw
Rubber cement
Scissors
Clamps
Wood glue
CAUTION: PLEASE READ THE INSTRUCTIONS THAT CAME WITH ALL OF YOUR POWER TOOLS TO UNDERSTAND THE SAFETY PROCEDURES ASSOCIATED WITH THE USE OF EACH TOOL. USE EXTREME CARE AROUND ALL MACHINERY AND EXERCISE DILIGENCE. MODEL SHIP BUILDING IS A FUN HOBBY BUT SAFETY IN THE WORKSHOP IS RULE NUMBER ONE. BE ESPECIALLY CAREFUL WITH HOBBY KNIVES. REMEMBER, A DULL BLADE IS MORE DANGEROUS THAN A SHARP ONE BECAUSE YOU TEND TO USE MORE FORCE TO MAKE THE BLADE WORK FOR YOU. A SLIP OF THE BLADE CAN CAUSE SERIOUS INJURY. CHANGE BLADES OFTEN, KEEP ALL EQUIPMENT CLEAN AND SHARP, AND BE CAREFUL! KNOW YOUR TOOLS AND HOW TO HANDLE THEM.
To make the jig, you will need one sheet of 3/16" aircraft plywood and one sheet of 1/2" plywood. Most hobby shops and craft stores sell this plywood made by Midwest. The ZIP file you downloaded includes a drawing of the jig. The center area must be cut out with a scroll saw. The notches in the center of the jig will hold the frames in alignment until the hull has been faired and planked.
The notches are cut in the thicker piece of plywood first. Use the drawing with the file name "Building Jig". There are 3 parts to this drawing that you will need to print out. They each have an alignment black line for aligning one with the other. It's best to leave about 1/2" of extra paper on the outside edge of this alignment mark on one drawing part so that the other drawing part can be overlaid on the excess paper and taped together.
The 2nd piece, shown in the 1st photo, does not have any notches cut into it, but the center area is still cut and removed. This piece is glued to the underside of the thicker piece and serves as a shelf for the frames to sit on when they are glued into the jig. Use the drawing with the file name "Building Jig Shelf" as a template to cut the center out.
The pine or poplar wood strips are used to build a frame around the jig thus providing a good stiff edge that will help to make the jig rigid. By raising the surface of the jig up off of the work table surface, you won't have to worry about accidentally gluing the jig to the table surface when you start gluing the frames into the notches (in the next step of these instructions).
First cut the 1/2" plywood into two pieces that are 6" x 24". You can use a regular table saw with a finishing blade to cut the plywood in half. The loss of a little bit of wood due to the kerf of the blade will be okay. Just be sure to align the center line of the drawing with one edge of the wood when you cut the center area out on the scroll saw.
The drawing is be rubber cemented to the plywood for cutting on the scroll saw. The drawing is not as wides as the plywood. Cut the drawing down the center line and align the center line with the edge of the plywood. Align the forward end with the forward edge and the aft end with the aft edge. Then you can cut out the center notched area on the scroll saw.
The reason I had you cut the plywood in half was to make it easier to cut the notches. One edge of the plywood is used to align the center line of the jig pattern. After the notches are cut out according to the Jig drawing, the two pieces are butted together and glued. To strengthen this base, pieces of 2-1/2" x 1/2" hobby poplar (found in home improvement stores such as Lowes or Home Depot) are glued around the perimeter of the base as shown in the photos.
The 2nd piece of plywood that is 3/16" thick is used to form the shelf that the frames sit on. I took the notched pattern that I created and using the CAD command to offset, created a parallel line to the notches that was about 1/4" inside the notched lines. Rubber cement the template to these pieces of plywood in the same manner as you did with the notched template/plywood. Then cut the center area out on the scroll saw. Be sure to cut on the inside line, that is, the line inside the center line. The second, parallel line, is merely there for reference. That area outlined by the two lines will form the shelf that the frames will sit on.
By sandwiching the two layers of plywood together, you have the completed jig. You can see how I used small clamps to glue the two layers together as well as the jig base parts. The outside edges of the shelf piece will have to be trimmed to fit inside the pine or poplar boards that form the base of the jig.
There is one additional set of parts I make for my jigs that clamp the stem of the keel and the sternpost in position over the building jig. It's simple to make and the photos show how it's made and how it's used. Theses clamps do not get glued however. By design, they are screwed to the jig base so that they can be removed easily later on. Once the keel has been clamped into the jig, it is being held in alignment on the center line by these clamping pieces.
These clamping pieces are made from poplar. They are 6" x 6". A 1" tab at the bottom enables these pieces to be screwed to the base of the jig surface so that they can be removed later on. You will need the drawings labeled "Keel Clamp Fore.pdf" and "Keel Clamp Aft.pdf" to make these pieces which can be cut out on the scroll saw. Make two each. Pre drill the holes in the tab so that the wood does not split when you screw them to the jig surface. Use 1/2" long wood screws to attach them to the jig surface.
You will notice that the inside vertical edge is notched. When the two piece are put together, this notch is at the precise height to allow the stem at the fore end and the sternpost at the aft end sit on top of the tab. These clamps hold the keel centered over the building jig so that when the frames are inserted into their respective notches in the jig, the notch in the center of the frame will fit into the notch in the keel. This is all by design and will enable you to frame the model with assurance that the framework is perpendicular and square to the keel thus producing a very straight and fair model.
In the next step, you will add the full frames to the building jig.
Step 10: Framing the Model Part 1
Now you're ready to start framing your model. This will be a two step process. First all of the full frames will be installed in the jig and glued to the keel. The second step will be to add the cant frames at the bow and stern and finish the hull by fairing it out with sandpaper. So let's get started!
Wood needed for this step:
23 Full frames previously made
Tools needed for this step:
Mini clamps
5 minute epoxy
Toothpicks to mix the epoxy
CAUTION: PLEASE READ THE INSTRUCTIONS THAT CAME WITH ALL OF YOUR POWER TOOLS TO UNDERSTAND THE SAFETY PROCEDURES ASSOCIATED WITH THE USE OF EACH TOOL. USE EXTREME CARE AROUND ALL MACHINERY AND EXERCISE DILIGENCE. MODEL SHIP BUILDING IS A FUN HOBBY BUT SAFETY IN THE WORKSHOP IS RULE NUMBER ONE. BE ESPECIALLY CAREFUL WITH HOBBY KNIVES. REMEMBER, A DULL BLADE IS MORE DANGEROUS THAN A SHARP ONE BECAUSE YOU TEND TO USE MORE FORCE TO MAKE THE BLADE WORK FOR YOU. A SLIP OF THE BLADE CAN CAUSE SERIOUS INJURY. CHANGE BLADES OFTEN, KEEP ALL EQUIPMENT CLEAN AND SHARP, AND BE CAREFUL! KNOW YOUR TOOLS AND HOW TO HANDLE THEM.
The sequence of photos shows the installation of the frames in the building jig. I like to start by installing the first and last full frames and then fill in the area between them. The reason is that the first and last frame will then provide the support of the keel at both ends while the other frames are being added.
The frames are glued into their corresponding jig notches using 5 minute epoxy. The epoxy is also used to glue the frames to the keel. Now you can see how the bottom of the frames meet the rabbet joint. Imagine how a plank laying across the frames will fit into this joint thus providing a good seal to keep water out. Technically, if you planked the entire hull of this model, it would float in water without leaks, assuming your planks were also sealed with glue on their edges.
I used mini-clamps to clamp the frames in the jig until the epoxy dries. Only mix enough epoxy to glue one or two frames into the jig at a time. It sets up fast so you have to work fast, but once you get the hang of it you will get into a rhythm. Since there are only 23 full frames in this model, it can be fully framed easily in a couple of hours. Don't take those clamps off until the glue has set up though.
In the next step, the cant frames will be added. Have fun!
Step 11: Framing the Model Part 2
As I mentioned earlier, the cant frames are half frames, and they get glued directly to the sides of the fore deadwood at the bow and the deadwood at the stern. They are epoxied into the jig and to the deadwood.
Wood needed for this step:
11 Cant frames previously made
Tools needed for this step:
Xacto knife
#22 Xacto blades
5 minute epoxy
Toothpicks to mix the epoxy
CAUTION: PLEASE READ THE INSTRUCTIONS THAT CAME WITH ALL OF YOUR POWER TOOLS TO UNDERSTAND THE SAFETY PROCEDURES ASSOCIATED WITH THE USE OF EACH TOOL. USE EXTREME CARE AROUND ALL MACHINERY AND EXERCISE DILIGENCE. MODEL SHIP BUILDING IS A FUN HOBBY BUT SAFETY IN THE WORKSHOP IS RULE NUMBER ONE. BE ESPECIALLY CAREFUL WITH HOBBY KNIVES. REMEMBER, A DULL BLADE IS MORE DANGEROUS THAN A SHARP ONE BECAUSE YOU TEND TO USE MORE FORCE TO MAKE THE BLADE WORK FOR YOU. A SLIP OF THE BLADE CAN CAUSE SERIOUS INJURY. CHANGE BLADES OFTEN, KEEP ALL EQUIPMENT CLEAN AND SHARP, AND BE CAREFUL! KNOW YOUR TOOLS AND HOW TO HANDLE THEM.
Starting at the bow, the first photo shows 2 of the cant frames glued to the side of the deadwood. Notice that the frames sit on an angle. That means that the foot of the frame has to be beveled at the proper angle for the frame to sit properly in the jig. Fortunately I included this bevel line on the cant frame drawings.
The bevel is trimmed from the line of the top surface, outward to the edge of the bottom surface. I've included photos of the forward most cant frame that clearly shows what the bevel looks like as well as a few more photos showing the cant frames at the bow. Also,notice that each bow cant frame is butted up against the previous frame installed.
You will need to use a #22 Xacto to cut the bevel. You should also scratch the surface of the deadwood with your Xacto to rough it up some and remove some of the finish on it before you epoxy the frame to the deadwood. The bevel in the forward cant frames gets greater and greater until you reach frame 34 which has the bevel across the entire length of the frame.
Any portion of the frame that extends into the rabbet joint should be trimmed after the epoxy has set so that the frames produce a smooth and continuous line across the top edge of the rabbet line.
The aft cant frames are different than the bow frames in that they do not but up against each other. So a pattern is employed (taken from the Frame Plan drawing) to mark the location of each frame. The aft cant frames do not have as pronounced of a bevel cut into the foot of the frame either. The remaining sequence of photos should explain how these frames are glued.
Once all of the frames are installed, as shown in the last photo, the clamps at the bow and stern are removed by simply removing the screws. This gives you easy access to the entire hull when faring it out. But before the hull can be faired, the stern transom must be framed. We'll cover the process in the next step of these instructions.
Step 12: Framing the Stern Transom
Framing the stern transom might be the most difficult part of the model to build. The stern transom is the aft end of the ship. On ships of a later time period, the transom became more and more complex.
Wood needed for this step:
(1) 5" x .325" x .850" boxwood - Wing transom
(1) 30" x 1.500" x .162" boxwood - Transom frames
(1) 12" x .168" x .500" boxwood - Transoms
(1) 6" x .265" x .287" boxwood - Counter frame
(1) 6" x .217" x .223" boxwood - Deck line frame
(1) 6" x .250" x .160" boxwood - Filling frame cross timber
(1) 12" x .250" x .125" boxwood - Filling frame
Tools needed for this step:
Xacto knife
#22 Xacto blades
Scroll saw
Byrnes miniature table saw
Sanding block and sandpaper (150 grit)
CAUTION: PLEASE READ THE INSTRUCTIONS THAT CAME WITH ALL OF YOUR POWER TOOLS TO UNDERSTAND THE SAFETY PROCEDURES ASSOCIATED WITH THE USE OF EACH TOOL. USE EXTREME CARE AROUND ALL MACHINERY AND EXERCISE DILIGENCE. MODEL SHIP BUILDING IS A FUN HOBBY BUT SAFETY IN THE WORKSHOP IS RULE NUMBER ONE. BE ESPECIALLY CAREFUL WITH HOBBY KNIVES. REMEMBER, A DULL BLADE IS MORE DANGEROUS THAN A SHARP ONE BECAUSE YOU TEND TO USE MORE FORCE TO MAKE THE BLADE WORK FOR YOU. A SLIP OF THE BLADE CAN CAUSE SERIOUS INJURY. CHANGE BLADES OFTEN, KEEP ALL EQUIPMENT CLEAN AND SHARP, AND BE CAREFUL! KNOW YOUR TOOLS AND HOW TO HANDLE THEM.
The 1st photo shows the framed transom. In the 2nd photo you see a piece of wood with some rectangles drawn on it. This is called the "wing transom", and every ship had one. Use the template with the file name "Wing Transom.pdf" as a template to mark the location of these lines and the shape on the 5" piece of boxwood. The template can be rubber cemented to the piece of wood if you like. It's probably easiest to simply cut the piece to shape using your Xacto and a #22 blade.
The rectangles are going to be cut into notches that the transom frames will sit in. The transom frame shape is also on the same template file as the wing transom. You will need to make 6 of these frames so print out 6 copies of the template and rubber cement each one on the piece of transom frame wood. Cut them out on your scroll saw.
The notches in the wing transom are cut using a hobby knife as shown in the next 3 photos. If you look at the template drawing, it shows a view of the wing transom as seen from the fore/aft side. You can see the depth of these notches. By setting your calipers to this depth, you can mark a line across the aft edge of the wing transom, and cut the notches to the line.
The wing transom is installed so that it sits on top of the sternpost. It has a notch cut in the center on the bottom surface. (Keep in mind that the model is upside down, so even though it looks like the wing transom is under the sternpost, technically the wing transom is sitting on top of the sternpost.
When installing the wing transom, use carpenter's glue to attach it to the sternpost and the aft side of the last cant frame. The angled edge should match the angle of that cant frame. The trick is to be sure that it is level and that a measurement of height on both sides is the same. This can be seen in photos 5, 6 and 7.
In photos 7 through 14, you can see how additional timbers are added below the wing transom (based on the ship sitting upright). Those timbers are called transoms also and act as fillers for the planking to lay against. All ships had these filler timbers. They helped to fill in the lower stern area.
Use the transom wood strip to cut these pieces out making them slightly wider than the frame as shown in the photos. They are spaced .168" between them so the same strip of wood can be used as a spacer to set their height. These pieces butt up against the sternpost and are glued to the post and to the aft side of the last frame in the model. Photos 7 through 14 show how these timbers are installed and eventually sanded to finish off the lower stern area of the model.
Photos 15 through 21 show the transom frames installed. These fit into the notches made earlier in the wing transom. They not only give the aft end of the ship a framework but also serve to frame the windows of the great cabin. The great cabin, found on most wooden ships of this size or larger, was the Captain's quarters. In later years, it became a pretty elaborate room with all kinds of amenities.
The spacing of the notches in the top surface of the wing transom is such that the transom frames have the same amount of space between them. The transom frames fit into these notches and sit on top of the surface of the framing jig. They angle inward slightly and a piece of scrap wood acts as a stop pushing against the outside edges of the frames. Glue the frames to the wing transom but do not glue them to the jig surface. You can tack glue the scrap piece of wood to the jig surface.
Stretching across the transom frames is a horizontal timber. This piece is called the lower counter frame and fits across the knuckle of the transom frames. Make it longer than is needed and then cut off the excess wood after it has been installed. A scale drawing of the stern of the model is provided in your ZIP file which may help in taking measurements for locating parts. It is called "Aft Drawing.pdf." Just keep in mind that you are viewing the stern of the ship from a 2D perspective when you use this drawing.
Notches are cut into the counter frame at each transom frame location so that it will fit flush with the outside surface of the transom frames. Corresponding notches were also cut into each transom frame. The area between this timber and the wing transom forms what is called the counter, which is later planked leaving an opening for the rudder.
Photos 28, 29 and 30 show the attachment of a second cross timber I call the deck line frame. This cross timber meets the deck clamp that stretches from one end of the deck to the other (which will be covered in a later step).
Notice that the deck line frame has a slight curvature to it. It was not bent this way but instead cut from the wood strip. The curve is 1/32" deep from the outside ends. You should refer to the drawing with the file name "Aft Drawing.pdf." You can measure the distance from the surface of the jig to the location of this timber using the Aft Drawing. Then transfer that measurement to your model to mark the location of the timber.
To make this timber, first cut the strip of wood to length leaving a slight overhang on each side. Then shape the curvature in two dimensions as shown in the photo. Notches are cut in it to fit over the transom frames. Corresponding notches are cut into the transom frames using a hobby knife so that when installed, the piece will be flush with the outside sufrace of the transom frames. Everything is sanded smooth after installation.
We're almost finished now. In the next series of photos for this step, you see a template used that was taken from the Frame Plan drawing of the profile of the model. This template helps to locate a horizontal timber I call the filling frame cross timber that will help close in the gap between the last frame of the ship and the outer most transom frame. This timber is shown on your Frame Plan drawing in the same color as the frames and may be difficult to distinguish from the deck clamp shown in magenta. As I mentioned earlier, the deck line frame extends across the stern transom at the same location as the deck clamp thus joining the right side clamp with the left side clamp.
The two ends of the timber you need to make has a notch at the fore end so that it fits around the last frame in the ship and a bevel at the aft end that matches the angle of the transom frame. This can be seen in the last photo of the series. It is also glued against the inside edge of the deck line frame that was just installed. A 1/8" x 1/4" piece of wood is used to make that last filling frame. A notch is cut into the cross piece where that filler frame goes. The filler frame timber has a matching notch and sits on top of the building jig base. The lower end of the filling frame meets the inside edge of the last transom frame. The photos show this placement.
One more step to complete the framing of the stern transom is left. Some scrap filler pieces are added on each side of the counter area I mentioned earlier. They are glued to the outside surface of the outer most transom frame. Then everything is sanded and blended to form a smooth transition of the counter as seen in the final photos for this step. This completes the complex construction of the stern transom. If you've made it this far, you are to be congratulated. I promise it gets easier from here!
Step 13: Adding the Outer Planking
As you can see from the 1st photo in this step, the model has been removed from the building jig, which is no longer needed because the planking you are about to install now holds the framework together. But before we can get to this point, we have to fair out the hull.
Wood needed for this step:
(10) .031" x .230" x 24" basswood - Wales under layer
(2) .031" x .230" x 24" ebony - Wales outer layer
(2) .031" x .125" x 24" boxwood - Counter planks
(10) .062" x .181" x 24" boxwood - Planking above the wales
(4) .062" x .093" x 24" swiss pear - Moldings
(1) .031" x .231" x 24" holly - Plank above first molding
(3) .031" x .166" x 24" plum - Planks at the quarterdeck
Tools needed for this step:
Byrnes miniature table saw
Xacto knife
#13 Xacto blade
#22 Xacto blade
Dremel tool with thin cutoff disc
Single edge razor blade
Sanding block
Various grits of sandpaper (80, 100, 150, 220)
Scissors
Rubber cement
Manila folder
CAUTION: PLEASE READ THE INSTRUCTIONS THAT CAME WITH ALL OF YOUR POWER TOOLS TO UNDERSTAND THE SAFETY PROCEDURES ASSOCIATED WITH THE USE OF EACH TOOL. USE EXTREME CARE AROUND ALL MACHINERY AND EXERCISE DILIGENCE. MODEL SHIP BUILDING IS A FUN HOBBY BUT SAFETY IN THE WORKSHOP IS RULE NUMBER ONE. BE ESPECIALLY CAREFUL WITH HOBBY KNIVES. REMEMBER, A DULL BLADE IS MORE DANGEROUS THAN A SHARP ONE BECAUSE YOU TEND TO USE MORE FORCE TO MAKE THE BLADE WORK FOR YOU. A SLIP OF THE BLADE CAN CAUSE SERIOUS INJURY. CHANGE BLADES OFTEN, KEEP ALL EQUIPMENT CLEAN AND SHARP, AND BE CAREFUL! KNOW YOUR TOOLS AND HOW TO HANDLE THEM.
Fairing the hull is the process of sanding the hull smooth so that it no longer has that stair stepped effect. The test for smoothness is by visually sighting down the hull as you hold the model at eye level and by laying a thin strip of wood against the hull at various points to see if it touches each and every frame and lays flat. You cannot lay planking if the hull is not fair.
Various sanding blocks are used to fair the hull. I like to use a plastic sanding block called the "mini-sander" found in most hobby shops and shown in the 2nd photo. It has two pieces of yellow plastic with teeth in them and a rubber pad that wraps around it. Strips of sandpaper can be purchased as belts that wrap around the two plastic pieces. The plastic pieces slide outward catching on their teeth to lock and tighten them against the sandpaper. The nice thing about this sander is the rubber pad which works well on curved surfaces such as the hull of a model ship.
Start with 80 grit sandpaper and aggressively sand the surface of the frames blending each one to the next and so forth. It will take some sanding to get the bow area faired as it has the sharpest curves.
When the hull is close to being faired all over, switch to 100 grit, then 150 and finally 220 grit sandpaper. The next 5 photos show the hull after it has been faired out. Now the planking can be laid.
Typically model ship builders like to leave the planking off of the lower hull of a true plank on frame model so that the intricate details of the frames can be displayed. There is actually some historical models know as Admiralty Models in various museums that are constructed in this manner. When a ship was going to be built, a model was made showing off the framework that would be used for its construction. The model was presented to the Admiralty Board for approval and often times, the plans for the model were also used to build the actual ship.
So, given the historical nature of admiralty models, I'm only going to cover how to plank the upper hull area. Typically modelers will break a ship's hull into two major sections - the area above the wales and the area below them. The "wales" are thick timbers across the center area of the ship going horizontally. The acted like a belt that holds up your trousers. They were thicker than any of the other planks on the hulls. Most modelers like to use a contrasting wood for the wales such as ebony or walnut. I chose ebony for my Hannah model.
In the next photo you can see a template cut from a manila folder. Use a copy of the Frame Plan to make this template. First cut the drawing along the line that is the top surface of the building jig. Then cut on the green line that is the bottom edge of the wale plank. After cutting the drawing, rubber cement it to the manila folder and cut it on the same lines as well.
To mark the line of the wale plank, place the template on the surface of the building jig and align the frames on the drawing with the frames on the model, then mark each frame with a pencil where the wale line intersects the frames.
Once the line has been marked, you're ready to start. Because the wales are thick, .168" on this model, they can be very difficult to bend, so I use a layering technique. Cut strips of wood that are .230" wide and 1/32" (.031") thick. You can use soft basswood for the first 5 layers because the final finished layer will cover them up (color their edges black to match the black ebony). A quick five minute soak in water will soften the basswood so that it bends easily.
Planks on a real ship were typically about 24' in length. Since this model was built in 1/4" scale, it's easy to calculate that length. 24/4 = 6 so the planks should be 6" long. Start at the bow. First mark a line on the stem where the wale will tuck into the rabbet joint. Ahha! Now you see why you cut that rabbet joint into the stem. Using the Frame Plan, the bottom edge of the bottom wale meets the stem at a point exactly 3.290" from the surface of the building jig base.
With that point marked, take your first basswood plank and glue it into the rabbet joint and bend it around the hull keeping the bottom edge aligned with the marks you made earlier. You can use a 24" length of wood for the first 5 layers because they will be covered over with the finishing layer.
It helps to put glue on a few frames at a time. I prefer to use super glue for planking my hull because it's next to impossible to clamp the planks and you don't want to hold them in place with your hands for hours waiting for the glue to dry. Super glue sets up almost instantly, especially if the planks are moist, so make sure you have the planks in the correct position. By gluing a few frames at a time, you can add glue to the surface of the frames, press and hold the plank against the glue for a minute, then repeat the process. Let the aft end of the planking extend slightly beyond the stern transom for now. You can trim it all up and sand it flush later on.
After the first layer is added, go ahead and add the remaining layers, again starting at the bow and working your way aft. Be sure to tuck the end into the rabbet joint.
Add the finished layer but cut those planks to a length of approximately 6". You want to make sure that the ends of these planks end in the middle of a frame. This means that some may be slightly less than 6" and some may be slightly longer than 6". Start at the bow and work your way aft as you did before.
Congratulations, you've begun your hull planking! The next 5 rows of planking is .181" wide and 1/16" (.062") thick. You won't need to layer any more of the rows.
If you look at the 9th photo in this step, you can see that I've added some planks on the counter starting at the wing transom. These are 1/8" (.125") x 1/32" (.031"). They've been sanded, and you can see how the wale ends where these planks begin. If you go forward to the 13th photo you can see that I've planked the entire counter area and sanded it smooth. You should plank the couter before you add the outer hull planks so that the outer hull planks cover the edges of the counter planks.
As the 20th photo shows, 5 rows of planking were added above the wales. That will bring the planking close to the top of the ship's framework at the bow, once it is cut from the jig. The next plank to go on will be a piece of molding. Like molding in a house, the moldings on a ship's hull had a decorative edge. You can make this edge by cutting the profile of the molding into a razor blade using a thin cutoff wheel in your Dremel tool. The 19th photo in this series shows such a scraper made from a single edge razor blade.
Let me also mention that the ends of your 6" planks need to be staggered. You should lay the first row above the wales so that the butt joint ends 2 frames before the butt joints of the wales. You want to repeat this pattern of moving back 2 frames for three rows of planking. On the fourth row, the butt joints should go back to aligning with the butt joints of the wales. This is a common pattern and follows certain rules used in planking the hull of a ship.
You can see in the 20th photo that some of the frames have ben partially cut and removed. Specifically the fore side of 2 frames has been removed. This is part of the design of this ship. Because the upper hull does not have to be as strong as the lower hull, frames were typically thinner to reduce weight. So, from the top edge of each frame going from the aft most frame to the point where the quarterdeck begins, I removed the forward half of the frame.
Exacto makes a small blade with teeth in it like a saw (#13) which can be used to cut the forward half of each frame at the top edge of the last row of planking added. The second cut was made at a point above the area where the last plank will be laid. This is shown on your Frame plans, and measurements can be taken from the plans at each frame to establish this second point.
Use a #22 Xacto blade to then cut and remove this half of the frame. Be careful that you don't damage the frame as you cut away the forward half and don't go beyond the forward end of the quarterdeck which should be shown on your plans as frame 14. Although the forward frames must also have half removed, there are gunports to deal with that will affect the location of the deck, which in turn affects where you need to cut the frames. I'll address that in a later step.
Now we can make our molding. The razor blade is used to scrape the wood strip, a piece of 1/16" (.062") x 3/32" (.093") swiss pear wood. Swiss pear wood is pear wood that has been steamed. Steaming turns the wood pink in color, and it makes a nice contrasting color that works well with the beige boxwood and white holly (used above the molding). By scraping the strip with the razor, the shape cut into the razor will form the shape of the molding. Pretty neat trick, huh? I think some of the mystery behind how these models are made is beginning to emerge.
The molding can be laid as a long, single strip if you wish. It becomes the top most plank at the bow, but at the stern, additional planking is necessary to cover the area where the quarterdeck is located. To give the model more contrast, I added a row of .231" x 1/32" (.031") holly, which is very white and clear.
Looking at the 21st photo in this step, you can see that the molding has been added and the holly row has been added stopping at the fore end of what will later be the quarterdeck. Another row of molding is added, then 3 rows of plum are added and the planking is finished off with another row of molding. Photo 23 shows these final rows of planking added.
Now that all of the planking has been added to both sides (you did remember to add it on the other side too, didn't you?), the model can be removed from the building jig by cutting each frame at a point slightly above the top of the planking. The Xacto blade (#13) can be used to cut the frames. Be careful at the end when you cut the last few frames that you don't drop the freed model on the floor! Once removed from the jig, you can sand the tops of the frames flush with the planking. Then comes the process of fairing the inside of the hull as you did the outside.
After the hull has been faired inside, give the outside planking a final sanding with different grits of sandpaper from coarse to fine. I like to apply a few coats of Minwax Wipe on Polyurethane to the outer planking and frames at this point. Usually 3 coats with a rub down of #0000 steel wool between each coat will give everything nice and smooth but not shiny.
This completes this step of planking the hull. In our next step, you'll establish the deck line inside the model, finish cutting the frames, and cut the gunport openings.
Step 14: Preparations for the Main Deck
In this step we must finish something we started in the previous step, that is, trimming the remaining frame tops. You will recall that in the previous step, before the planking was applied, you trimmed the forward portion of the sistered frames leaving only the aft half. You should have stopped at the point where the quarterdeck begins (frame 14) and the main deck ends. Now we must trim away the aft half of each frame at the main deck area.
Wood needed for this step:
(4) .125" x .250" x 24" boxwood - New upper frame pieces
(2) .062" x .250" x 24" basswood - Deck clamps
(4) .062" x .168" x 24" swiss pear - Cap rail
(2) .031" x .125" x 24" boxwood - Stern transom planking
Tools needed for this step:
Byrnes miniature table saw
Xacto knife
#22 Xacto blade
CAUTION: PLEASE READ THE INSTRUCTIONS THAT CAME WITH ALL OF YOUR POWER TOOLS TO UNDERSTAND THE SAFETY PROCEDURES ASSOCIATED WITH THE USE OF EACH TOOL. USE EXTREME CARE AROUND ALL MACHINERY AND EXERCISE DILIGENCE. MODEL SHIP BUILDING IS A FUN HOBBY BUT SAFETY IN THE WORKSHOP IS RULE NUMBER ONE. BE ESPECIALLY CAREFUL WITH HOBBY KNIVES. REMEMBER, A DULL BLADE IS MORE DANGEROUS THAN A SHARP ONE BECAUSE YOU TEND TO USE MORE FORCE TO MAKE THE BLADE WORK FOR YOU. A SLIP OF THE BLADE CAN CAUSE SERIOUS INJURY. CHANGE BLADES OFTEN, KEEP ALL EQUIPMENT CLEAN AND SHARP, AND BE CAREFUL! KNOW YOUR TOOLS AND HOW TO HANDLE THEM.
Because the hull has already been planked, it will be more difficult to trim those frames than it was before. However, I came up with a way to do it which makes it much easier. In the 1st photo you can see that I have installed the deck clamp. This is a strip of 1/16" (.062") x 1/4" (.250") wood. You may need to soak it in water to make the bend at the bow, or you could layer it with two strips of 1/32" x 1/4" wood. The deck clamp supports the deck beams which will be added in the next step. Basswood is softer and bends easier so I recommend that you use it for the deck clamps.
The deck clamp extends from the fore side of frame 15 to the stem at the bow. The top of the deck clamp is 1.077" from the top of the molding at the main deck. Set your calipers to this measurement and use them to mark the location of the top of the deck clamp.
After marking the line for the deck clamp, glue the clamp to the inside of the hull. Then use a Dremel tool with a cutoff disc to cut through each frame completely. Be careful that you do not cut through the planking though. Make the cut on each frame right at the point where the top of the deck clamp intersects the frame as shown in the 1st photo.
Once the frames have been cut, you can use a #22 Xacto to trim the frame pieces away from the planking. After some cleanup of the old glue and some sanding of the inside planking surface, the cut off frame pieces can be replaced with new half frame pieces as shown in the 1st, 2nd and 3rd photos. Remember, these half pieces are on the forward side of the frame. Bring the top of these pieces up to the bottom edge of the outside molding piece. On the first 2 cant frames, make these frame pieces about 1/4" longer than the others (I'll show you why in a moment). The same goes for the 5th cant frame piece.
Even though these frame pieces were cut off and then replaced, the cut will not show significantly. Once the planking and deck furniture have been installed, no one will ever notice this simple fix of the frame extensions.
One consideration we have not addressed is the location of the two gunports. One gunport is located near the aft end of the main deck between my frames 11 and 12, the other between frames 6 and 7. To frame them, a small piece of 1/8" (.125") square wood is installed above the deck clamp and between the two frames. (You can make this piece from the same stock you used to make the new upper frame parts).
Align the bottom edge of the 1/8" wood piece with the top edge of the deck clamp. Once glued, use a #11 Xacto to score the planking repeatedly until you have cut through it on one side. Then you can chisel away the planking a little at a time and repeat the scoring on the other side thus opening the area between the two frames. DO NOT cut the molding piece. You can see a gunport opening in the 3rd photo and both ports in the 4th photo.
One more detail to add before we begin framing the deck is the cap rail. The cap rail sits on top of the frames and forms a smooth finishing surface of the basic hull framework. If you look at the remaining photos in this step, you can see this rail. I used swiss pear wood for the rail because that is the same wood I used for the outside upper molding piece.
The rail is first cut from strips of wood that are 1/16" (.062") x 3/16" (.168"). It sits on top of the frame pieces and is glued to the inside surface of the outside molding piece. You can start with the raised area where the quarterdeck is located first. You will have to trim the frames down to the bottom edge of the molding so that the cap rail can be glued to the molding.
The transom piece is mitered on each side. You also see that I finished planking the area above the counter using 1/32" x 1/8" strips of boxwood.
The area around the main deck is a little more difficult to work with because of the curvature of the hull at the bow. Clamps can be used to clamp the cap rail until the glue dries.
Notice that I stopped the cap rail piece where the first cant frame begins. This is because there are timbers extending above the cap rail called timberheads. These were used to tie off some of the rigging. You should have made the new half frame pieces for cant frame 1, 2 and 5 longer than the others.
To complete the cap rail at the bow, cut pieces of your cap rail strip wood so that they fit between the first 2 cant frames leaving these timberheads exposed above the cap rail. These pieces are only as wide as the frames are. Cut another strip to fit between cant frames 2 and 5. This piece should sit on top of the 3rd and 4th cant frames. Then cut a small piece to fit between the 5th cant frame and the stem.
To finish off the cap rail, a strip of 1/16" square swiss pear wood is glued to the outside edge of the installed cap rail. (This piece can be made from a piece of the cap rail wood cut down to .062" x .062"). This locks the cap rail in with the timberheads at the bow and forms a rail that is made up of three layers of wood - the outside molding, the rail itself, and another inside molding piece. The remaining photos in this step show the cap rails finished off.
The model is really beginning to come together now. In the next step, the main deck will be framed
Step 15: Framing the Main Deck
In this step, you will frame the main deck as shown in the 1st photo.
Wood needed for this step:
(1) .254" x .250" x 12.606" boxwood - Keelson
(1) .083" x .250" x 24" boxwood - Keelson tabs
(1) 3" x .250" x 24" boxwood - Deck beams
(1) .3" x .186" x 24" boxwood - Deck ledges
(1) .156" x .125" x 24" boxwood - Carlings
(1) .250" x .125" x 24" boxwood - Carlings (large hatch)
Tools needed for this step:
Byrnes miniature table saw
Variable speed scroll saw
Xacto knife
#22 Xacto blade
#11 Xacto blade
Sanding block
Various grits of sandpaper
CAUTION: PLEASE READ THE INSTRUCTIONS THAT CAME WITH ALL OF YOUR POWER TOOLS TO UNDERSTAND THE SAFETY PROCEDURES ASSOCIATED WITH THE USE OF EACH TOOL. USE EXTREME CARE AROUND ALL MACHINERY AND EXERCISE DILIGENCE. MODEL SHIP BUILDING IS A FUN HOBBY BUT SAFETY IN THE WORKSHOP IS RULE NUMBER ONE. BE ESPECIALLY CAREFUL WITH HOBBY KNIVES. REMEMBER, A DULL BLADE IS MORE DANGEROUS THAN A SHARP ONE BECAUSE YOU TEND TO USE MORE FORCE TO MAKE THE BLADE WORK FOR YOU. A SLIP OF THE BLADE CAN CAUSE SERIOUS INJURY. CHANGE BLADES OFTEN, KEEP ALL EQUIPMENT CLEAN AND SHARP, AND BE CAREFUL! KNOW YOUR TOOLS AND HOW TO HANDLE THEM.
Before you can begin though, the keelson must be added. The keelson was a long timber similar to the keel. It sat on top of the frames locking them to the keel. It had notches in it just like the keel did. The 2nd photo shows the keelson ready to be installed. Use the Frame Plan to make a template for the keelson.
Start with a strip of boxwood that is 12.606" long, .250" wide and .254" tall. Test fit this by placing it inside the model on top of the frames. It should fit between the fore deadwood and stern deadwood. Make any adjustments to the length if necessary.
Next, cut pieces of .083" x .250" stock to create the tabs or teeth on the keelson. These fit between the frames in the same manner as the teeth on the keel. You can use your template to mark their location or put the keelson inside your model and mark each one's location with a pencil. They should all be approximately .337" long.
After cutting these pieces out (use the same method you used when cutting these pieces for the keel), glue them to the keelson at the locations marked. Let the glue dry before gluing the keelson into the bottom of the ship. The 3rd photo in this series shows the installed keelson.
With the keelson installed, you are ready to begin framing the deck. The 4th and 5th photos show what a deck beam looks like. It has notches on each end that sit on top of the deck clamps. Therefore, it must be cut to the correct width.
Use the drawing with the file name "Beams and Ledges.pdf" to make your beams and later, the ledges. All of the beams are the same shape and length to start out. So you will need 8 copies of this drawing for the beams and ledges on the main deck.
You will also notice that the deck beam has a curvature or camber in it. This was so that water would run off to the sides. Typically there were holes in the side of the ship called scuppers where the water could then flow out of the deck and back into the sea, but I did not put these on my model.
The first deck beam is installed at the aft end where the deck clamp ends. It is simply glued to the deck clamps as shown. Here is where the deck plan becomes useful. Each deck beam must be placed at the correct location. Start by printing out the drawing with the file name "Deck Plan.pdf" which is actually 2 drawings that must be taped together.
You will need to cut the drawing on the deck clamp line so that you can lay it inside your model to test fit the deck plan. The deck clamp line is the 3rd yellow line from the outside. Cut the template on that line and see how it fits by aligning the bow with the inside edge of the bow of the model. Sit the plan on the deck clamps. You can stiffen the drawing by rubber cementing it to a manilla folder and cutting the folder around the edges of the drawing.
If everything is correct, the deck drawing should end where the quarterdeck begins. This is the area where the planking rises higher. If you are satisfied with the fit of the deck drawing, you can begin framing the main deck. Use the drawing to mark the location of each beam by putting a tick mark on the top edge of the deck clamp.
These beams were cut from a billet of wood that is 1/4" thick. This can be seen in the 6th photo. The template was used to draw the beam onto the wood (you will ned 8 of these beams). The thickness of the billet (1/4") becomes the beam's width. Use your scroll saw to cut the beams out.
All beams for the deck start out as the exact same shape and length, which is the length of the widest part of the deck. A center line is marked on each deck beam. Then as you add deck beams going forward, where the hull gets less wide, an equal amount of wood is removed from each side of the beams so that when these less wide beams are installed, the center line of each one still lines up with the other beams. This method ensures that the camber of each beam is exactly the same.
Each beam has a notch on the bottom outer end that is 1/8" (.125") deep and 1/16" (.062") wide. This allows the end of the beam to slip over the deck clamp. It also lowers the beam by 1/8" which also just happens to be the thickness of the ledges. By lowering the beam 1/8", the ledges will be at the same height making the deck flat if a plank were laid across the beams and ledges.
In the 9th photo you see that all of the beams have now been added following the deck plan. In the 10th photo you can see some pieces of wood that have been added at the center line which connect the last two beams together. These pieces are called carlings. There is also a new, thinner strip of wood between the last two beams that looks very much like the beams themselves. This is the ledge. It is the same shape as the beams but is made from a billet of wood that is 3/16" (.186") thick. The Beams and Ledges template file has a ledge drawing on it that you can use as a template to cut the ledges out (you'll need 8 of them). Cut these out with your scroll saw the same way you cut the beams out.
Fit this first ledge but do not glue it yet, just fit it in place. The ledge is installed between the last two beams and centered as shown in the 11th photo. The 12th photo shows the carling. It is made from .156" (wide) x .125" (thick) wood stock. It is 1/8" longer than it needs to be to fit between the 2 beams. This means that it extends beyond the first beam by 1/16" and beyond the second beam by 1/16" (.062").
You will notice that the ends have been beveled. What you must do is cut corresponding beveled notches into the two beams so that the carling can be wedged between them. This is not as difficult to do as it might sound.
First, make sure you've got your centerline marked on the beams. Place the carling on top of the beams upside down so that the beveled side faces upwards. Center it and mark the outside edges on the beams. Remove it. Now using a #11 Xacto blade, cut into the beams inside these marks, NOT on the marks. Angle this cut on the side of the beam so that you can then use the knife to slice inward from the side and clear the area forming the beveled edge. Do this on both marks, making sure you cut INSIDE the mark until you have cut a small, beveled notch. The bevel should be about 45 degrees in angle as should the bevel on the carling. Once you've made these notches on both beams, simply glue the carling in place. The 13th photo shows the beveled notches cut into the two beams. The 14th photo shows the carling installed between the two beams.
Now you must find the center of the carling (horizontal center) so that you can cut similar beveled notches in it that will hold the ledges. The ledge you fitted earlier is cut in half and trimmed on the center end by cutting a bevel in the end that will fit into the notch in the carling. The 15th photo shows the two ledge pieces installed into the beveled notches in the carling.
Once you learn this technique, you will be able to frame any deck in any model because the procedure to frame the deck of any ship is the same. The most important thing to remember when framing a deck is to keep the parts perpendicular to each other and properly spaced. Careful measurements are important in accomplishing this task. A dimensioned miniature carpenter's square also helps.
Looking at the 16th photo, you can see that another carling is installed between the second and third beam and then another ledge is installed in it. Follow the exact same procedures as you did before.
Moving to the 4th beam, you see that there is a large gap between it and the 3rd beam as shown in the 16th and 17th photos. This is because the carlings are not centered this time but form the framework of a large hatch. Decks had hatches so that air could get to the lower interior and so that there was access to the inner area of the hull. Usually there was a ladder in some hatches that lead to a lower deck.
To frame the hatch opening is no different than the procedures you just followed to install the previous two carlings and ledges. However, the carlings for this hatch are wider, .250". Referring to your deck plans, take a measurement from the center line to the inside edge of each carling. Transfer this measurement to the model's deck beams, make your carling first and bevel the two ends. Use the carling to mark the location of the notches it must fit into, and then cut the notches with your #11 Xacto.
Make the ledges and fit them before the installed hatch carlings. Then glue the carlings in place. Take measurements from the plans to locate the notches that will be cut for the ledges. Cut these notches. Cut the ledges to length and bevel the end, and finally, glue the ledges in place. Simple, right?
Ok, maybe not so simple when it's your first time. But I always say to myself, "It's only wood. If I mess up, no big deal, I'll just cut another piece of wood and try again."
The 18th photo shows me holding the ledges in place for marking and cutting. The 19th photo shows the hatch opening now framed. In the 20th, 21st and 22nd photo you can see that another carling is installed between the 4th and 5th beams and a ledge is installed in that carling. Now we come to the bow framework of the deck.
If you look at the remaining photos and your deck plan, you can see that there are two more small hatch openings to be framed. First a smaller carling is installed between the 7th and 8th deck beams. There is no carling between the 6th and 7th deck beam.
After these carlings are installed, a ledge is installed leaving an opening between the carlings in the center area. Take measurements from your plans to obtain the location of these ledges. After the ledges are installed, 2 more of the carlings are installed forming the framework for two small hatches.
Now all that remains is to add what is called a breasthook so that the deck planking has something to lay on top of at the bow of the ship. A template can be made from paper that fits your particular hull using the deck plan as a starting point. Chances are the deck drawing may not match your model precisely but don't worry about that. Hull shape is a variable because one person may sand more aggressively than another person which will change the shape slightly.
The last photo (and 1st) shows the fully framed deck. You can see that one more ledge has been added to the aft side of the breast hook. This ledge is 1/8" square and can be made from by ripping the ledge on your Byrnes saw to a width of 1/8" after cutting it out on your scroll saw.
Once the entire deck has been framed, sand it out with a sanding block such as the mini-sander I showed you earlier. Do not put a finish on it just yet though. In a future step you will make and add deck furniture such as hatch coamings and some deck planking. A finish would cause trouble with the glue sticking.
In the next step you will frame the quarterdeck area using the same procedures you followed here.
Step 16: Framing the Quarterdeck
Framing the quarterdeck is not much different than framing the main deck.
Wood needed for this step:
(1) .062" x .250" x 24" basswood - Deck clamp
(1) 3" x .250" x 24" boxwood - Deck beams
(1) .3" x .186" x 24" boxwood - Deck ledges
(1) .156" x .125" x 24" boxwood - Carlings
(1) .250" x .125" x 24" boxwood - Carlings (large hatches)
(1) .125" x 3" x 6" boxwood - Mast step, elm tree pump support, chimney support
Tools needed for this step:
Byrnes miniature table saw
Variable speed scroll saw
Xacto knife
#22 Xacto blade
#11 Xacto blade
Pin vise with drill bits
Sanding block
Various grits of sandpaper
CAUTION: PLEASE READ THE INSTRUCTIONS THAT CAME WITH ALL OF YOUR POWER TOOLS TO UNDERSTAND THE SAFETY PROCEDURES ASSOCIATED WITH THE USE OF EACH TOOL. USE EXTREME CARE AROUND ALL MACHINERY AND EXERCISE DILIGENCE. MODEL SHIP BUILDING IS A FUN HOBBY BUT SAFETY IN THE WORKSHOP IS RULE NUMBER ONE. BE ESPECIALLY CAREFUL WITH HOBBY KNIVES. REMEMBER, A DULL BLADE IS MORE DANGEROUS THAN A SHARP ONE BECAUSE YOU TEND TO USE MORE FORCE TO MAKE THE BLADE WORK FOR YOU. A SLIP OF THE BLADE CAN CAUSE SERIOUS INJURY. CHANGE BLADES OFTEN, KEEP ALL EQUIPMENT CLEAN AND SHARP, AND BE CAREFUL! KNOW YOUR TOOLS AND HOW TO HANDLE THEM.
We start by adding the deck clamp on each side. Use 1/16" x 1/4" wood for this. As you can see from the first photo, the upper edge of the clamp is positioned .965" below the top of the frames (NOT below the top of the cap rail). An easier way to locate the deck clamp is to install it 1/8" below the cut frames. The deck beams are 1/4" thick with a 1/8" notch and sit on top of the deck clamps (same as the main deck).
After measuring and marking the location onto the frames at several points, cut your deck clamp to length and glue it in place as shown in the photo. Of course you must repeat this for both sides.
First add the deck beams. Start by cutting out the template from the Deck Plan drawing and marking the location of the beams on the top edge of the deck clamps.
Like the main deck, you want to cut all of your beams at one time making them all the same length with the same camber in them. Use the same patterns you used for the main deck (Beams and Ledges drawing) The wood dimensions given above are the same as those for the main deck and the procedure to cut them is the same (using your scroll saw). There are 7 beams and 7 ledges.
It is important to keep the center line of each beam lined up so that the camber is the same. The 2nd and 3rd photos show the first three beams installed. Here you see something new, the mast step. It is made from a piece of wood that is 1/8" thick. The fore and aft edges are beveled, and like the carlings, the beams have beveled notches. The hole for the mast is .469" in diameter. You can use the deck plan to make a template of this part. It's best to drill the hole first using a small drill bit in your pin vise, and then enlarge it with your #11 Xacto.
The remaining deck beams are made and glued in place using the deck plan. Photo 5 and 6 show the layout of the carlings. In the 7th photo you can see that the ledges have been installed. Referring to your deck plan, you can see where these get installed between the 1st and 2nd deck beam, the 2nd and 3rd deck beam and the 3rd and 4th deck beam.
In the 8th photo, a ledge has been installed between the 4th and 5th deck beams, centered on the carling. In the 9th photo you can see two solid pieces of wood (which are 1/8" thick) installed on each side of the carling and ledge between the 4th and 5th beams. Another piece of solid wood has a square hole in it for the chimney. You can see in the photo how it is installed. Each of these pieces are wedged between the carlings and ledges.
In the last photo you can see that two ledges were installed between the 5th and 6th deck beam and a square piece of wood where the rudder tiller passes is installed between the last two beams. Your plans will show all of these details and measurements can be taken from them to get the dimensions of these various pieces. All of these parts are 1/8" thick.
Sand the deck with sanding blocks but do not put a finish on it just yet.
Step 17: Adding the Main Deck Details
In this step you will make the deck furniture for the main deck (don't ask me why they call it furniture, I don't really know where that term came from!). The first thing to make are the hatch coamings.
Wood needed for this step:
(2) .093" x .310" x 24" swiss pear - Hatch coamings
(1) .062" package of grating strips from Model Expo
(1) 3" x .062" x 24" boxwood - Companionway
(1) 3" x .031" x 24" swiss pear - Companionway trim
(1) .541" x .541" x 6" swiss pear - Windlass
(1) .125" x 1" x 6" swiss pear - Windlass mounts
(8) .186" x .062" x 24" holly - Deck planking
(1) .093" x .093" x 6" boxwood - Windlass leverage posts
Tools needed for this step:
Byrnes miniature table saw
Xacto knife
#22 Xacto blade
#11 Xacto blade
Pin vise with 3/32" drill bit
Sanding block
Various grits of sandpaper
Black artist chalk
CAUTION: PLEASE READ THE INSTRUCTIONS THAT CAME WITH ALL OF YOUR POWER TOOLS TO UNDERSTAND THE SAFETY PROCEDURES ASSOCIATED WITH THE USE OF EACH TOOL. USE EXTREME CARE AROUND ALL MACHINERY AND EXERCISE DILIGENCE. MODEL SHIP BUILDING IS A FUN HOBBY BUT SAFETY IN THE WORKSHOP IS RULE NUMBER ONE. BE ESPECIALLY CAREFUL WITH HOBBY KNIVES. REMEMBER, A DULL BLADE IS MORE DANGEROUS THAN A SHARP ONE BECAUSE YOU TEND TO USE MORE FORCE TO MAKE THE BLADE WORK FOR YOU. A SLIP OF THE BLADE CAN CAUSE SERIOUS INJURY. CHANGE BLADES OFTEN, KEEP ALL EQUIPMENT CLEAN AND SHARP, AND BE CAREFUL! KNOW YOUR TOOLS AND HOW TO HANDLE THEM.
I made my hatch coamings out of swiss pear wood for contrast. First the four sides are cut to length from .093" x .310" strips of wood. Refer to the Top View drawing to get their length and width. These are not mitered. They are butt joined together as shown in the second photo. The sides of the coamings are slanted or beveled slightly
Measure 1/8" down from the top edge and draw a line across the hatch coaming side. Then mark a line 1/32" in from the outside edge. After marking all four sides, use your Xacto knife to shave off the side between the two lines. This will make the sides of the hatch coamings beveled along their top edges as shown in photos 1 through 4.
Several of the hatches have grating in them. Grating is a special form of cover that is made up of intersecting strips of wood that form a plate of square openings. Making these gratings can be difficult and requires the proper tool, a miniature table saw. However, a company called Model Expo (http://www.modelexpo-online.com) sells small strips of wood with teeth in them. These teeth interlock and thus are used to make grating hatch covers. They're very inexpensive and easy to use. The 8th photo shows how the strips are assembled using super glue. The razor blade shown is actually a very fine saw blade I found years ago. It was used to cut the excess wood off to from the completed grating hatch. However, you can use a pair of nippers from Micro Mark to cut the excess off as well or you can cut them after gluing using the Byrnes miniature table saw and as thin a blade as possible (my Preac saw takes blades as thin as .010").
The two small hatches at the bow have these covers as does the large hatch in the middle of the deck. Your Top View plans will show this and you can see these completed hatches in the 6th photo.
In the 9th through the 14th photo you see how I constructed the hatch with the small house like structure in it. This is called a deck house. Use 1/16" thick wood for this structure and the drawings with the file name "Misc Parts.pdf" and as shown on your plans to get the exact width/length shape. I used boxwood for the basic structure but added a 1/32" layer of swiss pear wood as accent pieces. Photos 10 through 14 show the assembly of the deck house.
The final object to make is the windlass. The windlass was used to raise the anchor. It is an octagonal timber that tapered slightly at each end. It has several square holes in it so that long leverage poles could be inserted and used to turn the windlass. The anchor rope was wrapped around the windlass so that when it was turned, it would raise the anchor.
To make the windlass, start with a square piece of wood that is .541" square. You can obtain the length needed from the Top View plans. This piece must be trimmed on each corner for the full length to turn it into an octagonal piece as shown in the 16th and 17th photos.
After first shaping it with an Xacto knife, it is then reduced on all eight sides at each end so as to make it slightly tapered as shown in the 19th photo.
In the 20th and 21st photo, I've marked two lines at one end. The lines are spaced .125" apart. The outer line is .320" from the end. A rabbet joint is cut between these two lines using a #11 Xacto. This forms a recessed cylinder shape at each end as shown in the 21st photo. These cylindrical areas are used to mount the windlass to the windlass mounts shown in the 22nd photo. Another recessed cylindrical area .214" wide is also cut in the center of the windlass. As you can see, it has teeth. These might be difficult to make so if you can't carve the teeth into the cylindrical area I wouldn't worry too much about it. I started by first cutting the cylinder into the wood. Then I used the tip of the #11 Xacto to score and carve each individual tooth. It takes time to do this but the end result looks fantastic.
The plans also show square holes cut into the surface of the 8 sides of the windlass. You can drill these holes using a pin vise and a 3/32" bitt. Then the holes can be squared up with a #11 Xacto. Use your plans to mark the location of these holes on the sides of the windlass.
The mount as shown in the 22nd photo is made of two piece of wood. The first piece is rectangular in shape makde from.125" thick x.358" wide x 1.032" long swiss pear. For contrast, you might want to use boxwood instead. Two timberheads are cut in the upper portion of the part as shown in the photo. A half circle notch is cut in the upper area that will fit around the cylindrical area at the end of the windlass. The drawing with the file name "Side View" shows the shape of both parts and can be used as a template to make these parts.
The second piece is .826" tall and rounded in the upper quadrant as shown in the photo. It too has a half circle to fit the cylindrical part of the windlass. The 23rd photo shows the completed windlass assembly.
In the remaining photos you can see the mounting of these hatches and the windlass. The deck was only planked in the center area using strips of 1/16" x 3/16" holly. Holly is the preferred wood of model ship builders because of its clear, white color. The decks of ships were honed with special stones that acted like sand paper. This honing was done routinely to keep slime from building up on the deck which became slippery. The constant honing and bleaching by the sone made the decks turn white in color, thus the reason for using holly for the deck planking.
The deck planking has blackened edges. I like to use an artist's charcoal to blacken the edges because it does not bleed like a felt tip marker might. This blackening creates the effect of caulking between the rows of planks.
The leverage posts that were used to turn the windlass were made from 3/32" square boxwood cut to a length of 2". These rods were round and slightly tapered but square at the ends where they were inserted into square holes in the windlass. As you can see in the last three photos, the holes in the windlass were staggered - on every other surface of the windlass. They were also on the outside edges. The photo also reveals that the toothed area in the center has beeen painted black. This area was actually made of metal on a real ship. Another strip of metal called the tongue was attached to the aft side of the mast. It worked in a fashion that prevented the windlass from spinning in the opposite direction when the anchor was raised. To lower the anchor, this locking mechanism could be disengaged. Since I'm not going to be adding masts to the model, that detail will be left out.
You will also notice that the deck planking at the bow has a rectangular hole in it. This hole will have a bowsprit bitt installed later on. There is also a round opening in front of the windlass where the mast would go. Earlier when you framed the deck, there were two beams and two carlings very close together that formed a small square opening which is where this mast hole is located. The rectangular hole for the bowsprit bitt is just in front of the forward most deck beam.
This completes the details on the main deck. Our model is just about finished now. If you wanted you could add additional deck planking and purchase cannons from Model Expo to be installed on the deck. I chose not to do this because I wanted to show the framework of the deck and typically an Admiralty model such as this did not have cannons installed. The primary purpose for the Admiralty model was to show the Admiralty Board what the ship's framework would be like, so such details were left off and were often up to the individual captain of the ship to decide.
Step 18: Adding the Quarterdeck Details
Now we will turn our attention to the quarterdeck and its deck furniture.
Wood needed for this step:
(2) .093" x .310" x 24" swiss pear - Hatch coamings
(1) .062" package of grating strips from Model Expo
(8) .186" x .062" x 24" holly - Deck planking
(1) .167" x .167" x 12" boxwood - Bitts
(1) .062" x 3" x 12" boxwood - Companionway, binnacle
(1) .031" x 3" x 12" swiss pear - Trim on companionway and binnacle
(1) .155" x .155" x 12" boxwood - Chimney
(1) .250" x .250" x 6" swiss pear - Elm tree pumps
Tools needed for this step:
Byrnes miniature table saw
Xacto knife
#22 Xacto blade
#11 Xacto blade
Pin vise with 3/32" drill bit
Sanding block
Various grits of sandpaper
Black construction paper
Scissors
CAUTION: PLEASE READ THE INSTRUCTIONS THAT CAME WITH ALL OF YOUR POWER TOOLS TO UNDERSTAND THE SAFETY PROCEDURES ASSOCIATED WITH THE USE OF EACH TOOL. USE EXTREME CARE AROUND ALL MACHINERY AND EXERCISE DILIGENCE. MODEL SHIP BUILDING IS A FUN HOBBY BUT SAFETY IN THE WORKSHOP IS RULE NUMBER ONE. BE ESPECIALLY CAREFUL WITH HOBBY KNIVES. REMEMBER, A DULL BLADE IS MORE DANGEROUS THAN A SHARP ONE BECAUSE YOU TEND TO USE MORE FORCE TO MAKE THE BLADE WORK FOR YOU. A SLIP OF THE BLADE CAN CAUSE SERIOUS INJURY. CHANGE BLADES OFTEN, KEEP ALL EQUIPMENT CLEAN AND SHARP, AND BE CAREFUL! KNOW YOUR TOOLS AND HOW TO HANDLE THEM.
The quarterdeck has two hatches with grating covers that are made in the same manner as the main deck hatches. The first 3 photos show these hatches. You can also see that the holly deck planking has been added in the center area using the same 3/16" x 1/16" strips with blackened edges. There is also a large hatch in the center as shown in the photos.
At the fore end of the deck is a structure called the bitts. This structure consists of two tall posts with a cross beam that has a special shape. The 4th, 5th and 6th photo shows how the upper cross beam is made using a piece of .167" x .167" boxwood. The posts can be made from the same stripwood but should be cut down to .137" x .137". The lower cross piece is also .167" x .167". You can use the Miscellaneous Parts drawing to obtain measurements of these pieces.
The arched shaped upper cross beam is shaped by hand using a #22 Xacto. A bell hangs from the underside which can be purchased from Model Expo also.
As seen in the photo, two square holes are cut in the second plank on each side (from the outside edge of the deck planking) between the first beam and first ledge. You can start by drilling a small hole using a pin vise and a small drill bit. Then the hole can be enlarged using a #11 Xacto knife.
The posts to the bitts fits int the hole being glued to the aft side of the deck beam. The lower cross timber has notches cut into it on each end so that it can be fitted to the two posts as seen in the photo. The posts also have corresponding notches for the cross timber to mate to.
The posts also have a small hole drilled through them at their base. This hole is a simulation of a sheave that would have been installed in the posts for certain rigging lines to pass through, but making and installing such a small detail is extremely difficult.
Behind the bitts is the mast hole which needs to be cut out from the planking. Drill a small hole to begin with and then enlarge it with a #11 Xacto.
Now to finish off that middle hatch which is called a companionway. The four sides are made from 1/16" thick boxwood. Your Miscellaneous Parts plans will show the size of each side. These parts are assembled as shown in the 9th photo and are fitted inside the hatch coaming in the middle of the deck. Notice that the top is slightly slanted aft which is also shown on your plans. (hatch coamings were covered in the previous step and are made from swiss pear wood).
The companionway has some thin .031" x .062" trim pieces made from a billet of swiss pear. These give the companionway some contrast. Small hinges on the simulated doors are made by cutting small strips of black construction paper and gluing them with white glue. A top was made from a piece of .062" boxwood that fits the structure with a slight overhang on all four sides. The top is scored with a #11 Xacto to simulate two separate pieces and simulated hinges are made from black construction paper. The 10th and 11th photo shows the completed companionway.
The next detail to make is the galley chimney. Ships had an oven on the lower deck. Although no below deck details were made for this model, you can still show this chimney on the quarterdeck. It is made from a solid piece of wood measuring .155" x .155" boxwood painted black and can be seen in the 12th photo.
Around the bottom, a small hatch coaming like structure is made using .062" x .155" stock (use the same stock the chimney was made from but cut it down to .062" in thickness). First 2 sides are added around the chimney. Then the other two sides are added. Once these four sides have been added, they are beveled slightly along the upper area. A top for the chimney is made from .031" swiss pear stock painted black as seen in the 15th photo. The upper portion above the coaming is painted black. The chimney is glued into the square opening on the right side of the deck next to the companionway as seen in the 16th and 17th photo.
Ships had pumps that were used to pump water out of the bottom of the ship that might accumulate from rough seas, leaks or rain. These were called elm tree pumps because they were usually made from elm trees due to the tree's hardness and longevity when exposed to water. The 15th through the 18th photos show how these pumps are made.
Make two of these using 1/4" (.250") square swiss pear that is 1" long. First cut the piece to length. Then taper all four sides from one end to the other so that one end is 3/16" (.186") square and the other end is 1/4" (.250") square.
After tapering, bevel each corner from top to bottom to form an octagonal shape as seen in the 19th photo. Drill a small hole in the top surface (the wide end) and then bevel it slightly as shown in the photos. Finally, cut a notch in the top edge of the beveled end and add a tapered strip of .031" wood to serve as a handle. Paint the handle black as seen in the photo. The eighteenth photo shows these installed on the flat wood surface of the pieces added earlier when the deck was framed. Orient the handles on an angle on the forward side as shown in the photos.
The last detail tol make in this step will be the binnacle. The binnacle was a box like structure that housed a compass and a small candle or lantern inside. It was used to aid in knowing the direction the ship was headed in. A man would work the tiller which was attached to the rudder to steer the ship on a certain compass heading.
The binnacle is made in a similar fashion to the companionway using .062" thick boxwood. Use your Miscellaneous Parts plan to get the length and width of each piece. Construction is shown in the 19yh through the 20th photos.
Notice how the bottom edge is cut at an angle. This is because the deck rises fore and aft. The angled bottom makes the binnacle stand straight when mounted to the deck.
Trim the edges with swiss pear as shown in the photos. Mount the binnacle behind the companionway as shown in the 21st photo and top it off with a roof made from .062" boxwood or for contrast, .031" swiss pear as shown in the 21st and 22nd photo.
The last photo shows the completed quarterdeck with all of its deck details. In the next and final step, all remaining details will be made and added to the ship thus completing your construction of a true plank on frame model ship made from scratch. Happy modeling!
Step 19: Final Details
We're closing on on the finished model now! This is the last step in this Instructable. You will finish up the final details on the model in this step.
Wood needed for this step:
(1) .062" x .350" x 24" boxwood - Channels
(1) .062" x .113" x 24" boxwood - Channel outside edge
(1) .250" x .250" x 6" swiss pear - Bowsprit bitts
(2) .219" x .219" x 24" boxwood - Swivel gun mounts
(1) .062" x .262" x 6" boxwood - Steps to quarterdeck
(1) .031" x .262" x 6" boxwood - Steps to quarterdeck
(1) .031" x 3" x 12" boxwood - Deck beam cover at fore end of quarterdeck
(1) .250" x .250" x 12 boxwood - Catheads
(1) .250" x 1" x 12" boxwood - Rudder
(1) .186" x .186" boxwood - Rudder tiller
(10) Swivel cannons (Model Expo)
22 or 24 gauge brass wire (Model Expo)
Flat brass or copper wire (Model Expo)
Package of small brass nails (Model Expo)
(12) Deadeyes (Model Expo)
(2) Anchor kits (Model Expo)
Tools needed for this step:
Byrnes miniature table saw
Xacto knife
#22 Xacto blade
#11 Xacto blade
Pin vise with small drill bits
Wire cutters
Needle nose pliers
Soldering iron
Solder
Jeweler's files
Sanding block
Various grits of sandpaper
Black construction paper or copper tape
Scissors
CAUTION: PLEASE READ THE INSTRUCTIONS THAT CAME WITH ALL OF YOUR POWER TOOLS TO UNDERSTAND THE SAFETY PROCEDURES ASSOCIATED WITH THE USE OF EACH TOOL. USE EXTREME CARE AROUND ALL MACHINERY AND EXERCISE DILIGENCE. MODEL SHIP BUILDING IS A FUN HOBBY BUT SAFETY IN THE WORKSHOP IS RULE NUMBER ONE. BE ESPECIALLY CAREFUL WITH HOBBY KNIVES. REMEMBER, A DULL BLADE IS MORE DANGEROUS THAN A SHARP ONE BECAUSE YOU TEND TO USE MORE FORCE TO MAKE THE BLADE WORK FOR YOU. A SLIP OF THE BLADE CAN CAUSE SERIOUS INJURY. CHANGE BLADES OFTEN, KEEP ALL EQUIPMENT CLEAN AND SHARP, AND BE CAREFUL! KNOW YOUR TOOLS AND HOW TO HANDLE THEM.
The first part to be made will be the channels with chainplates. These structures were part of the ship's rigging. Heavy lines came down from the upper area of the masts to the channels. Special blocks called deadeyes were seized to the end of these heavy ropes. Corresponding deadeyes were attached to the channels using metal strops. These stropped deadeyes were then attached to the side of the ship using chainplates. The two deadeyes were lashed together using the three holes in the deadeyes. This will make more sense to you when you view the photos.
Brass wire purchased at a craft store (I believe 24 or 22 gauge) was used to make the strop. First a piece of wire about 1" long was bent around the deadeye using needle nose pliers (deadeyes can also be purchased from Model Expo - http://www.modelexpo-online.com ). After the wire has been bent around the deadeye, a small loop is formed at the bottom, again being formed and bent using jeweler's needle nose pliers ( also found at most craft stores ). The excess wire is cut off and the strop is soldered in the middle leaving the small loop at the bottom open and exposed. Small jeweler's files are used to file away the excess solder. Finally, the deadeye and strop are painted black. Photos two through five show these steps.
The chainplates are made from flat brass or copper strips. Photo six shows some flat copper wire purchased from Model Expo. These are 1/64" (.015") thick and 1/16" (.062") wide. The wire is first cut to a length of 1/2" (.500"). A small hole is drilled in one end and the other end is bent over at an angle. Small jeweler's files were used to taper the bent end so that it would fit into the hole in the strop. The end where the hole was drilled was rounded on the corners with a jeweler's file and small notches were filed on each side to make this part of the chainplate look more separated. That end was also bent slightly at an angle opposite to the upper end.
Finally these were painted black. Photos 5 through 7 show the chainplates and some flat copper wire but brass wire may also be used, so long as it's flat (otherwise you won't be able to drill the hole in the bottom end).
Now to attach everything to the ship. The channel is made from 1/16" (.062") thick wood. Your plans show the shape and location. The outside edges have small notches cut into them. A deadeye strop fits into each notch as shown in the 8th and 9th photos. A small strip of .113" x .062" wood is glued across the outside edge of the channel thus locking the strop in place. Then the chainplate is hooked onto the strop eye. A small brass nail is used to secure the bottom end to the wale plank. These nails can be purchased from Model Expo as well. Drill a small hole into the wale first, and then insert the nail into the hole using needle nose pliers. The fit should be snug, and a touch of super glue can be used to secure the nail into the hole.
There are two channels on each side of the ship, one for each mast. Your Top View and Side View plans show their location and dimension.
At the front of the ship is a special post called the bowsprit bitt. It is a rectangular post that is beveled at the top on all four sides. Use a piece of 1/4" (.250") square swiss pear wood to make it. A square mortise is cut into the upper end. This mortise was used so that the bowsprit tenon could be mated to secure the bowsprit in place. A bowsprit is a special kind of mast that sat on the stem and protruded out from the front of the ship.
First make the bowsprit bitt. Then cut the rectangular opening in the deck where it is inserted (see the photo which shows it located just in front of the two forward hatches). Temporarily install the bitt into the hole you just cut. Then lay a strip of scrap wood across the stem and mark where it intersects the bitt. Remove the bit, drill a starter hole through the bitt at the mark you made, then use a #11 Xacto to shape the hole into a square mortise. Finally, glue the bitt back into the hole.
In the 10th and 11th photo you can see the timberheads have been shaped. You will recall that when you added the cap rails, these were left sticking above the rail. Shape them with a #11 Xacto by first beveling each edge at the top. Then cut a small "V" shaped groove about 1/8" below the top on all four sides.
In photo 12 you see 10 swivel gun mounts. These were mounted on the side of the hull and had a small swivel cannon inserted into a hole in the top. These small cannons could be tilted up and down. They can also be purchased from Model Expo.
These mounts are made from .219" square boxwood. Your plans will show the length to make them. Bevel the bottom end on one side as shown in the 16th and 18th photos. Drill a small hole in the top.
Your Side View plans will show the location of each mount. You will have to cut the moldings so that the mounts will fit flush against the upper hull planking. Photo 19 shows a cannon mounted. This cannon was bought from Model Expo, and is about 3/4" long not counting the swivel handle.
In photo 20 and 21 you see two more details added. At the bow, a strip of wood 1/16" thick was made where the hawse port is located. This will also be shown on your Side View plans. The hawse port was an opening that the anchor rope passed through.
Drill a hole through the piece of wood as well as the hull planking after it is glued in place. Of course all of these parts go on both sides of the ship.
The second detail is some additional curved and tapered planks that cross the upper hull planking between the wale plank and the upper molding. These planks protected the upper hull when the anchor was raised. Photos 22 through 26 show the anchor construction if you wish to make the anchor from scratch. However, you can purchase anchors from Model Expo that need only minor assembly. The Miscellaneous Parts plan shows the scale anchors
The anchor itself was purchased from Model Expo. Most of their anchors come with the wooden part already cut out, but you can make your own if you want to. Start but cutting two pieces of 1/8" x 1/4" boxwood to a length of 1.709". Shape the pieces as shown in the photo and on your plans by slightly tapering or beveling the outer 1/3rd of each piece on the top surface or widest surface. This can be seen in the 22nd photo.
In the 23rd photo you can see that a small notch was cut in the flat side of each piece so that when glued together, a square hole was formed for the anchor to be inserted. The 24th and 25th photos show that these assembled pieces were now tapered again on their bottom surface so that the outer end becomes square. Copper tape was wrapped around the pieces which simulate the iron bands used to hold them together. Paint the tape black. (You can use black construction paper instead of tape). If you do use copper tape (used by stain glass artists), they don't need to be glued because the tape has a sticky side to it that will stick to the wood.
The 26th and 27th photos show a model of Hannah built by a man named Harold Hahn. I took these pictures when I visited the Navy Museum in Washington, DC where his model sits in a glass case. The photos give a good view of the anchors installed on his model.
The 28th photo shows the pieces used to make the small ladder that goes from the main deck to the quarterdeck. The sides of the ladder are made from 1/16" boxwood, and the steps are made from 1/32" boxwood. Your plans show the basic shape but you will want to measure the height from your main deck to your quarterdeck first.
After cutting the sides, cut two small rabbet joints or grooves in each one so that the steps can be glued in. Make sure you have a left side piece and a right side piece. Don't make the mistake of cutting two pieces alike. These are mirror images of themselves.
Now glue the steps into the notches in one side piece using super glue. After the glue is dry, add the other side with super glue.
Before you glue the ladder in place, make a piece of boxwood from 1/32" stock that will fit across the first deck beam of the quarterdeck. The piece should be flush with the top of the beam and sit on the beam of the man deck below. You'll have to step it over the deck planking but cutting a large notch in the center. The twenty seventh photo shows the piece in place with the ladder installed. Make another ladder for the other side as well. A strip of trim molding was added to the top of the aft part on the main deck where the notch was cut in the filler piece just to give it all a finished look.
In the 30th photo you can see that the cap rail has been cut. This notch is 1/4" forward of the middle timberhead. It is 1/4" wide. The cathead will fit into this notch. The cathead aided in raising the anchor up to the side of the hull when the anchor was raised. It hung out from the bow of the ship and had sheaves in the end where ropes passed through. A double block was suspended under the cathead. The rope passed through one sheave in the end of the cathead, down to a block where it passed through the sheave in the block and then came back up through a second sheave in the cathead. One end of the rope was permanently fixed to an eyebolt either on the cathead or on a frame top. The other end of the rope was used to pull which in turn helped to raise the anchor up to the side of the ship where it could then be lashed to the aft most timberhead protruding from the cap rail. The photos of Hahn's model show all of this.
The cathead is made from 1/4" (.250") square boxwood. There are two pieces to it. The top piece sits in the notch cut into the cap rail. It hangs out over the bow of the ship as shown in the 31st photo. Some holes are drilled in the end to simulate the sheaves.
Another piece of 1/4" square boxwood is cut and mated to the back of the top piece. This second piece goes down to the deck as can be seen in that photo.
We're getting close to the end now. Just a few more details to make. You must be getting excited to see your model finally come together. The next detail to tackle will be the rudder.
The rudder is cut from a piece of 1/4" thick boxwood. Your plans will show the shape of the rudder which can be used as a template. Typically the rudder was tapered from top to bottom. The 32nd photo shows the rudder cut out and shaped. The fore side, that is, the side with the three notches cut into it, is rounded over.
The rudder is attached to the ship with special hinges called gudgeon's and pintles. The 33rd photo shows how these are made. Using flat copper wire, I bent the wire around a drill bit to form the hole that the pin of the opposite piece fits into. Then the copper piece was shaped with needle nose pliers into a "U" shape and soldered in the middle as seen in the photo. The opposite piece, which goes on the rudder has a brass pin soldered in the hole.
The part that goes on the rudder (with the pin) fits into grooves cut into the surface which can be seen in the 35th photo. You can see how the hing works. Make three of these gudgeon and pintle assemblies as shown in the photos and on your plans. Use super glue to glue them to the rudder and the model.
The trick is to get the positioning on the model such that you can insert the top of the rudder into the rudder opening and then set it down onto the gudgeon's that are attached to the ship. By dry fitting the assemblies first, you can mark where the gudgeons go on the sternpost. After marking their location, remove them from the rudder and glue them to the sternpost with super glue.
You will have to open up the hole in the counter that you planked early on so that the rudder top will fit up through the opening. It should come out just above the quarterdeck.
The top end of the rudder has a tiller handle attached using a mortise and tenon joint. The 36th, 37th and 38th photos show how the tiller is made. Your plans have a drawing of the tiller which is made from 3/16" (.186") square boxwood hand shaped with an Xacto knife. After installing the rudder's pintles onto the gudgeons, install the tiller. If you don't glue it, you'll be able to remove it and remove the rudder if needed such as when moving the model.
Photo 39 and 40 show a part called a keevel. It is made from 1/16" x 1/8" x 1" boxwood in the shape shown. It attaches to the two frames opposite the companionway (one on each side). By now you should have plenty of scrap wood to make this part.
There's a decorative piece on the stern transom made from 1/32" boxwood. You can use a copy from your plans as a template to cut the part out. I painted mine black for contrast before gluing it to the stern transom as shown in 42nd, 43rd, 44th and 45th photos.
The last two photos show a simple base using two hard wood barrels as pedestals. You can find these in most any craft store. Slots were cut into the top so that the keel could set in the slots. I glued them to the wooden base also found in a craft store.
The final photo shows the completed model. Congratulations if you made it to the end! You now have a museum quality model ship to display in your home.
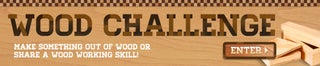
Second Prize in the
Woodworking Challenge
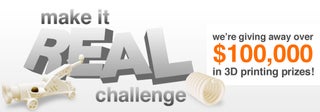
Participated in the
Make It Real Challenge