Introduction: Build a Laser Cutter Fume Extractor
I built my first laser cutter in 1996 and learned right away that laser cutters "stink". Well, at least the fumes from cutting smell awful and are quite harmful to breath. After trying several fume extraction options, back in 2002 I found the ElectroCorp RSU filter. It was a bit expensive, I think I paid $1500, but it did a great job extracting even the worst fumes from cutting acrylic. Fast forward to 2013, I called up ElectroCorp to buy replacement filters for my unit and found out that the original company was sold and is now being run by another company. This new company claimed to supply the same replacement filters, but after almost three months of going back and forth with them, it turns out that their filters are no longer the same, cost way more and look to be much less robust. Going through this challenging and frustrating process with them got me thinking. After taking a close look at how my old unit worked, it was pretty clear that I could build a similar unit quite easily that would allow me to use off-the-shelf and readily available parts. I figured I would document the process so other people with laser cutters could try their hand at doing the same. Depending on the supplies you have laying around your workshop, you should be able to build one of these for somewhere between $400 and $450. Here's how...
Step 1: Gather Major Components and Supplies
- Qty (1) Fantech Inline Exhaust Fan, 392 CFM, Centrifugal for 6" Duct
- Qty (1) 29500 Honeywell Air Cleaner Replacement Filter
- Qty (2) 3M Filtrete Air Conditioner Filter, 15-Inch by 24-Inc
- Qty (1) Duck Brand 1285234 24-Inch by 15-Inch by 1/4-Inch Foam Air Conditioner Filter
- Qty (1) 55lb bag of activated carbon (I called them and spoke to Karrie Gibbons. Just ask for "4 by 8 coconut shell carbon, for vapor filtration")
- Qty (1) Harbor Freight Router Speed Controlled
- Qty (1) Roll of squishy neoprene shelving liner (It's about 1/8" thick, soft, makes great gaskets)
- Qty (4) 2inch casters
- Qty (1) 3/8" Romex clamp or cord strain relief
- Qty (4) 3/8inch threaded rods
- Qty (8) 3/8inch nuts
- Qty (4) 3/8inch wing nuts
- Qty (8) 3/8inch washers
- Qty (1) 5' roll of window screen
- Qty (1) 5' roll of 1/4" wire cloth
- Qty (1) tube silicon caulking
- Qty (1) 3/8" dowel pin (for the router jig)
- An old extension cord (we only need the male end)
- 4'x4' piece (half a sheet) of 3/4" thick birch plywood smooth on both sides.
- Mat board
- Weather stripping (I had leftovers from other projects, but basically 1/4" thick, foam)
- Qty (1) Roll of post filter material (updated!)
Tools:
- Plunge router with a straight plunge bit
- Electric staple gun
- Drill (with Phillips tip and 3/8" drill bit)
- Jig saw
- Hot glue gun
- Hearing protection
- Face mask
- Dust mask
- Rubber gloves
Step 2: Cutting Disks and Rings
I started out making a jig for my router. If you have a circle cutting jig you can obviously skip this step. We need to cut two inner and two outer rings plus the top and bottom plate (note that the bottom plate doesn't have the 6inch hole in the center). I used the jig saw to cut out the top and bottom plate.
Remember to wear all your safety gear!
Step 3: Install the Casters
Figured it would be easiest to do this now. Just screw them to the base plate (the one without the hole).
Step 4: Staple the Screen and Mesh Into Place
iThe goal is to end up making two cylinders with the sets of inner and outer rings that are just a little taller than the hepa filter, which is 12" tall. I started by cutting strips of the 1/4" wire cloth 12" wide. I stapled this to the outside of the smaller inner rings and the inside of the larger outer rings so that the total height of each cylinder is 12-1/8". Then I lined the wire cloth with the fine window screen. I used a ton of staples since I wanted to be sure it didn't come apart and that there was no gaps between the wood and the mesh.
Step 5: Glue the Mesh Cylinders Down to the Base With Silicone
I drew a circle on the bottom plate so I would know where to position the inner cylinder. Then I ran a bead of caulking around the circle and squished the cylinder into place. I did the same with the outer cylinder.
Step 6: Filler' Up With Carbon
The carbon comes in something like a potato sack. I recommend you leave it in the box it's shipped in as there is fine carbon dust that seeps through the bag. I just used a cup and filled up the space between the two meshes. It is a bit messy so I would do it outside on a surface that you don't mind spilling a little carbon.
Wearing a dust mask and gloves is a great idea for this step.
Step 7: Clean Up and Add Some Weather Stripping
Clean all the carbon dust off of the top edges of the inner and outer rings. Vacuum out the center area. Apply weather stripping to both the inner and outer rings. I also added some weather stripping to the underside of the top plate.
Step 8: Cut the Bottom Gasket
I cut a circle out of the shelving liner that was approximately the same size as the outer diameter of the hepa filter. I then placed it in center area so the hepa filter would sit on top of it and no fumes would leak under it.
Step 9: Build the Pre-filter
To save you from replacing your hepa filter as often, there is a pre-filter that filters the "big" particles. To make it, I cut a 11-3/4" x 25" piece of the 1/4" wire cloth and rolled it into a cylinder overlapping the ends by about 2". Then I used some gaffers tape wrapped around the top and bottom edges to hold it together. I cut the 1/4" Duck Brand foam to fit inside the cylinder and both layers of the 3M Filtrete filters to fit on the outside of the cylinder. A piece of gaffers tape holds the 3M filters together.
Step 10: Build the Mat Board Air Baffle
Having a laser makes cutting cardboard a breeze, but you could probably do the same by hand. Take a look at the attached DXF file.The baffle needs to fit snugly inside the pre-filter. It should be pretty easy to tell how it goes together. I used a fair bit of hot-glue to make sure there were no leaks. You might need to adjust the dimensions a little if your pre-filter cylinder is slightly different dimensions.
Attachments
Step 11: Bolt It All Together
I cut the threaded rods to 15" and bolted everything together. You will want to tighten all the bolts evenly to compress the weather stripping straight down.
Step 12: Wire Up the Fan
I cut the male end off an old extension cord and wired it into the fan's junction box. I used a Romex clamp to provide strain relief. Then I plugged the extension cord into the variable speed router controller (which is just a high current rheostat). You could just add an on/off switch, but I like to be able to turn the fan down when cutting thin material like paper, so that it doesn't get blown around.
Step 13: (Update!) Post Filter
My old unit had this blue fuzzy filter on the outside of the carbon filter (see the picture at the beginning of this Instructible). I never could figure out why it was there since the carbon did such a good job removing the fumes. What could be left to filter out? Fortunately, Soundgod06 posted a comment asking if I saw carbon dust blow out when I turned on the filter. The answer was no, I didn't see any dust, but it got me thinking... Just because I couldn't see it, doesn't mean it wasn't there. Ah ha! THAT'S why the blue fuzzy filter was there. It's there to grab any carbon dust pushed out by the blower. It was simple enough to add, I just ordered a roll from McMaster for $19, cut it to fit in between the top and bottom plates and pressed it into place. I just overlapped the filter material at the end, and tucked the free end behind one of the threaded rods. It holds there quite nicely.
Step 14: Test It Out!
Plug it and flip the switch! It should draw quite nicely when on high. Hard to say what the final CFM rating would be, but it seems to be plenty to evacuate my laser.
There is no guarantee that this filter is filtering out 100% of the bad fumes, so use it at your own risk. So far, it has worked pretty well for me.
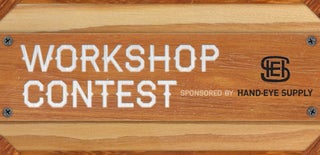
Participated in the
Workshop Contest