Introduction: Build the Best Headphones That Money Can Buy for Under $100 (also Ear Protection)
How do you build one of the best darn headphones possible? It's certainly not signing up musicians and putting big logos on the side. Instead, start with military grade headsets, the type people use on aircraft carriers or screaming through the night sky on black hawk helicopters. Then, upgrade the electronics with 6 Watt's of full range neodymium speakers supported by custom cast mounting brackets. Finally, fill the rest with noise protecting foam and throw on a pair of super comfy gel pads to create arguably the best headphones anywhere. In addition, with the extreme sound dampening qualities you can listen to your tunes while mowing the lawn, working on projects or just generally blocking out the world in a way that was never possible before.*
Not only will you love your new custom headphones but after you realize that you can run a weed eater or leaf blower without having to tuck ear buds under your hearing protection and blowing your hearing in the process you'll want to build sets for all of your family and friends.
This project will require basic soldering knowledge but is simple enough it can be a great first time soldering project.
While the installation is simple the creation of the mounting bracket is not. Since it is infinitely easier to create a second bracket then start from scratch I have created kits with the necessary parts, If there is any interest in making a version that you don't need to solder together please message me or leave a note in the comments.
*Noise reduction is not rated and will be dependent on your build. I make no claims on levels of noise reduction and what is considered safe.
Step 1: Purchase a Military or Aviation Grade Headset
There are lots of headsets out there but I suggest finding a pair of David Clark Headsets from the last 40 years. I know there are other brands that could also work. I have no affiliation with David Clark, but they are easily the de facto brand in this area and all of their headset products I have seen are of the very best quality. The easiest way to find them is to search ebay. You should be able to find a good used pair for about $40-$80. (Click here for ebay search) Although almost any David Clark non active noise canceling headset will work for this project. The way to confirm this is if the speaker assembly is held in by two small screws. The best deals to be found are model H10-76 military headsets, which sell for $800 new but since they will not work for civilian airplanes they can be found cheap. This is what was used for the demonstration of this project.
As you can see from the connector, this is going to take a bit of work before we can plug it into any old MP3 player.
Step 2: Dissassembly
Its fun and easy to take the headsets apart. First, off comes the microphone component, followed by the outer ear pads and the fabric liner. Some headsets have different types of foam insulation but generally it consist of three layers (one 1/4 inch, and two 1/2 inch layers). After the cloth layer is removed, the thin foam layer can be taken out as well as the ring foam layer. The ring foam layer is a bit harder to get out without damaging it as it is pressed in and around the speaker. Eventually you should see the speaker with two mounting screws at roughly the top and bottom. The screws can be a pain to remove because the other headset earpiece will always be in the way. Be careful and make sure they don't get lost, they will be needed. After removing the speaker there is one last piece of foam which may need to come out depending on the wiring situation.
Step 3: Building Speaker Mounts
All the parts you need for this build are shown at the top and are available as a kit over here. If you go this route please feel free to skip to the next Step. However if you are a glutton for punishment, you can build your own speaker mounts similar to what is shown. What you are looking at is about a week's worth of work.
Speakers
If you compare the new speakers with the original you will notice that the new speakers are much thicker and a little bit smaller than the pieces they replace. The new speakers are rated for 3 Watts and 8 Ohms, so they have similar impedance to most headphones on the market. This basically means that they will sound about as loud as another pair of commercial headphones for a specific volume level. The difference is these can go to 11. Well, not really, but they can get much louder before failing compared to almost any other headset. For example, each speaker is rated to generate 85 decibels of sound using only 1 Watt of power from almost 20 inches away. Also keep in mind that each speaker can run at three times that power and up to four in peak situations. Clearly these are not your normal headset speakers. These are usually used in higher end computer speakers and small stereos and not made to put directly on your ear; however when you do, they sound fantastic. A quick word about the old speakers. Even though they serve the same purpose they are not built with a traditional voice coil as your typical dynamic loudspeaker. Instead, they use an electric coil to vibrate an actuator bar that pushes on a rod which vibrates a metal disk. While this is great at making a lot of noise, it is restricted to a fairly small tonal range. That is why it's great for reproducing a voice in an aircraft where quality does not matter, but it is terrible at accurately reproducing music. (An older version can be seen opened up in the last picture).
Mounting Bracket
The mounting bracket holds the speaker as tightly as possible while still matching up with the same mounting screw holes and allows the wires to be easily connected. I tried to make the first one completely out of sculpting clay, however it was impossible to get the impression I wanted from the speaker and keep the shape that I needed. For the next try I used a bracket from a different David Clark headset as a base to sculpt the speaker mounts around. The black and white piece you see is actually built from 6 different plaster sculpting and casting sessions before the final shape was made. This was cast into a silicon mold and after it set was broken up and chipped out. Then the mold was sliced in half to facilitate easier extraction. Rubber bands were used to hold the halves together while the liquid plastic set. Unfortunately, it was still very difficult to get out and quite rough, requiring a lot of sanding to get into decent shape. To improve the looks, I took one of the better casts, sanded and polished it to a nice smooth finish and cast it into a new silicon mold horizontally for easier removal.
Step 4: Installing the Speakers
The speaker casings are designed to be a very tight fit and essentially snap onto the speaker as there are no screw locations or easy points attached to the speaker. To attach the mount, lay the speaker face down on the table and push the plastic mount down gently and firmly over it until both sides snap into place. Although the mounts are rigid, the last thing desired is for something to come loose. I highly recommend gluing the speakers to the plastic mount using a two part epoxy. The best place to glue is the top where both wings contact the notches on the speaker. Take care that none of the glue either drips into the speaker or onto the table and then onto the speaker diaphragm or it will be ruined.
Step 5: Cleaning Up the Appearnce
Besides physically cleaning the device, all the unsightly holes created while removing the mic wire grommet, mic arm mount and volume nob need to be addressed. The plan was to wire the device using the built in volume nob, however when turned it caused crackling through the speakers and it didn't adjust both sides evenly, so It was removed. Cleaning up the appearance (and improving sound dampening) was achieved by using the plastic hole plugs shown previously in the kit. Also notice that the mic arm bar mounting system has put deep scratches near the hole. In this case I drilled it out with a 7/16th drill bit and inserted the appropriate larger plug to cover most of the damage.
Step 6: Wiring It Up
The final wiring is significantly simplified compared to the original setup. Without the mouthpiece and volume adjustment, the wiring is straightforward and outlined in the wiring diagram. Keep in mind the colors you use will probably change depending on the headset version but as long as contact number 3 is the shared common/ground, it should work. The black dots in the figure shows where the connections were made in the left ear piece on this unit. Note that solder connections on the speakers are very susceptible to heat. The lightest touch of the soldering iron is necessary to melt the pre-soldered connections. Any more, and the plastic holding the speaker contacts in place will melt.
The trickiest part is wiring up the 3.5 mm headphone jack. The metal strain relief barely fits over the coiled wire and is difficult to slide around (which is a good thing). As for soldering, the connections are small and it would be easier with a third hand to hold everything in place. Don't forget to slide all three pieces of the cover up on the wire in the right order before you begin or you will have an opportunity to try again.
Step 7: Assembling and Enjoy
Assembling is as easy as taking the unit apart and putting each layer of foam back in with the speakers. From here there is nothing to do but enjoy the finished product. I believe the camera in the video was picking up the vibrations through the table while filming, as it did not seem nearly as loud when the speakers were muted against each other.
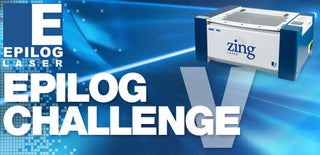
Participated in the
Epilog Challenge V
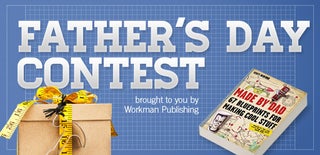
Participated in the
Father's Day Contest