Introduction: Building a Lugged Bicycle Using a CNC Routed Frame the Jiggernaut
This Instructable is brought to you by Mixed Media Engineering LLC and shows the process of building a lugged bicycle frame using 'The Jiggernaut' a CNC routed, flat pack bicycle frame jig. We will bring you through all of the steps from prepping the lugs, mitering the tubes, silver soldering the joints and finishing everything off to look nice. In the end we produce a single-speed bike with track dropouts capable of shredding the frigid streets of Minneapolis.
To make this project a reality we relied heavily on digital design and prototyping. We used Solidworks to model different bike frame as well as the jig and we used CNC routing to make parts that perfectly matched our drawings. This really helped streamline the process and get us to or goal of a bike frame fast.
Disclaimer:
We are not professional bicycle fabricators. We may or may not have used best practices when fabricating the frame in this instructable. It is the responsibility of the user to ensure that best practices are used. Remember, you're building a bicycle that you or someone else may be riding. You need to be sure that your design and fabrication skills are adequate to produce a bicycle free from mechanical defects. Failure to do so may result in mechanical failure, accident or even death. When constructing a frame you must absolutely keep the safety of you and others in mind. There is a significant risk of fire when using torches and welders for fabrication. You must take the proper safety precautions when using torches and welders. This includes but is not limited to fire extinguishers, ventilation, respirators, protective eye wear, protective clothing and to keep flammable materials away from the area you are working in. You'll be using different fluxes and solvents during this project that can be poisonous. Be sure to wear the proper clothing, gloves, etc... to protect your skin and eyes from these chemicals. Remember, use common sense and when in doubt stop what you are doing and research the proper methods.
There are many resources available that teach proper frame design and fabrication. An especially helpful manual is the Paterek Manual for Bicycle Frame Builders. Copies can be found for sale online.
Step 1:
Step 2: Gather Your Tools and Materials
Bicycle parts:
Tubeset (In our case we're using a standard road tube set)
Lugs (We're using stamped lugs)
Lugged Bottom Bracket Shell
Dropouts (Track Dropouts)
Drawing:
A drawing of your frame showing the lengths of all of the tubes (BikeCAD, pencil drawing, etc...)
Jig:
We are using
'The Jiggernaut' an inexpensive frame jig made from CNC routed MDF
Tools:
Hacksaw
Files (Half round, straight, full round)
Drift
Hammer
Sandpaper (A few different grit values from coarse to fine will be fine)
Dremel Tool with die grinder and sanding drum
7/16" wrench
Bench Vise
Soft jaw vee blocks for holding tubes without marring them
Scribe
Marker
Hand Drill with 1/16" drill bit
Punch
Mapp gas torch or Oxyacetylene torch
1.5 oz 45% silver solder
Flux for silver solder (Stay Silv or equivalent)
Acid brush
Tub for washing flux off of frame
Wire brush
Safety:
Brazing goggles (tinted)
Gloves (rubber and leather)
Respirator and ventilation fan
Fire Extinguisher
Step 3: Overview of What We'll Be Doing
Before we dive in to building, let's talk about some of the things we'll be doing.
Lug Finishing
When the lugs arrive at your door they will be very close to their final shape, but it is often necessary to remove material from the inner diameter so that the lugs are able to slide over the frame tubing. If you have to use excessive force to get the lug to slide over the frame tube then they are too tight.
Tube Mitering
Tube mitering is sometimes called coping or cutting a fish mouth. Basically it is joining two tubes together at different angles and removing material from the end of one tube so that it intersects the other tube and creates a kind of seamless joint. It is important to have copes that have very small gaps because it increases the strength of the joint.
Jig Setup
A jig is used to to accomplish a few things. For one, it aligns the centerline of the tubes that comprise the front triangle so that they're in one plane. In other words it makes sure the frame is built straight and without twist. It also holds all of the frame tubes at the correct angle for soldering.
Silver Soldering
Silver soldering is used join all of the tubes to one another. The tubes are slipped into their corresponding lugs, heated and solder is applied so that it wicks into the gap between the tubes and the lugs forming a strong joint.
Step 4: Finishing the Lugs
Finishing the lugs involves cleaning up the ID with an abrasive to ensure that they will slip over the frame tubing.
First try to test fit the tube into the lug. If it already has a slip fit, then you're done. If not press the two together and then pull them apart. The ID of the lug will have witness marks where they were rubbing together. You can use a Dremel tool with either a die grinder or sanding drum attachment to take of the high spots. Test fit again and repeat the process until you have a nice slip fit.
You can also use this time to finish the outside of the lugs. This can be done using sandpaper and it's up to you to decide when you're done. The more you work on them now, the better they'll look with when the bike is ready for paint.
This is optional, but some people like to carve intricate patterns into lugs. The results can be stunning, but it's all cosmetic and isn't necessary.
Step 5: Tube Mitering
There are many methods to miter tubes, this is one of the simplest methods and can be accomplished with a hacksaw and a file.
The first step is to trace the profile of the cut onto the end of the tube. You can use a scribe or a fine tipped marker for this.
Next clamp the tube in a vise (using soft jaws). Taking your hacksaw, make light, controlled cuts that are tangent to the profile you traced on the tube. It is ok to leave a little room between the saw cut and the traced line. Work your way around the circumference of the tube cutting as deep while still leaving the profile line intact. When you are finished you should have a few rough cuts around the tube. Next cut axially from the end of the tube up to the profile cuts you just made. What we're doing here is creating a few pieces that can be pried loose.
Using a pliers, grasp the ends of the tube and bend back and forth until the piece releases. This will leave behind the rough cut profile.
Now use a half round file to finish off the profile up to the line. Be patient and test fit the mating tube often to ensure the fit is correct. When you are done you should be able to mate the tubes at the correct angle with very small gaps between them.
Step 6: How Setting Up the Frame Jig Works
The jig we're using (The Jiggernaut) can be setup to accommodate any frame geometry. The first step is to bolt the bottom bracket shell down to the backplate of the jig. The centerline of the bottom bracket needs to be in line with the centerline of the frame, so the jig includes shim washers to accommodate different width bottom bracket shells.
The frame tubes also need to be held with their centerlines in line with the centerline of the frame. This is accomplished using a series of vee blocks. The jig includes vee blocks of different heights to accommodate tubes of different diameters.
Setting up the jig involves coping one joint at a time and test fitting the tubes and lugs while adjusting where the vee blocks are positioned.
Here's an example to help clarify. The first joint you'll cope is the seat tube to the bottom bracket. Once this is coped you'll slide the seat tube into the bottom bracket and align the cope to the bottom bracket profile. Next you'll select the vee block that corresponds to the tubing diameter and slide it under the tube to support it. At this point everything will be aligned and the joint can be soldered. The rest of the joints will be very similar to what was described above at least for the front triangle.
Step 7: Silver Soldering the Joints
This is not meant to be a silver soldering tutorial, there are plenty out there and you should get some practice on something that's not a bike frame if it's your first time.
The silver that we used had a 45% silver content and we used about 1.5 troy oz. of it for the frame. We also used Stay Silv flux. I've read to use a flux that can be washed off with water after brazing rather than one that has to be removed mechanically.
One method to practice your soldering is to purchase a few sets of inexpensive lugs. Go through the process of cleaning them up and fitting them to steel tubing of the right diameter. Solder the joints and after they cool hold one tube in a vice and use the other tube to apply a bending moment to the joint. The tube should not break at the joint, but rather along the length of the tubing away from the joint. Also, you can use a hacksaw to cross section the joint and ensure that you have proper silver penetration.
Step 8: Building the Main Triangle
In this section we'll list off the order in which you'll measure, cope and solder the front triangle together. By this point the lugs should be cleaned up and you should have a drawing of your frame that you can check measurements against.
The first joint that we'll tackle is the bottom bracket (BB) to seat tube (ST). Insert the ST into the BB, trace the profile and cope the tube. Set the jig up so the bottom bracket is bolted down and select the correct vee block for the ST diameter. Rough up the end of the tube with sandpaper and then Clean the joint of any contamination (oil, paint, etc...) with a solvent and rag. Flux the BB lug and tube end and re fit the tube into the BB. Place the ST in the vee block and use some safety wire to pin the tube in the vee. Double check everything and then solder the joint.
The next joint we'll do is the downtube (DT) to headtube (HT). Cope the joint and jig up the HT and DT and check that angle. Adjust it until it's close and solder the joint.
The DT to BB is the next joint. Consult your frame drawing and rough cut the DT about 3/4" too long. Insert it into the BB. Re-jig the HT so that it is parallel to the backplate (can be done using a square to measure each end of the HT) and trace the DT. Cope, clean, flux, jig and braze this joint.
On to the top tube (TT) to HT joint. This is done just like the DT to HT joint.
The last joint is the one that requires the most patience. Again, consult your drawing to determine the tube length and rough cut the tube a little long. Slip the TT-ST lug over the tube end being sure to align it with the TT - HT lug. This can be done by placing the assembly on a flat surface and rotating the lugs so that they are clocked correctly to one another. Trace and cope the tube end. At this point you should be able to slide the TT-HT lug, TT-ST lug and TT onto the HT and ST. Measure you angles, measure your lengths ensure the HT is parallel with the backplate and position vee blocks under the TT. Before we solder, there is one new step that we add. We need to drill a 1/16" hole in the HT along the centerline of the TT. This will be hidden under the lug and is used as an air escape hole during soldering. Clean and flux the joints and solder both lugs.
Congratulations, you've completed the front triangle!
Step 9: Chainstays and Dropouts
Now that the main triangle is complete we can move on to the rear triangle. There are a few things we're going to want to get right on the rear triangle. One thing is that the dropouts are spaced for the hub you'll be using. In our case the hub is 130mm. The other aspect to be aware of is to center the dropouts around the center plane of the frame. This ensures that your front and rear wheel will be in the same plane when you're going straight on your bike.
We'll start with the chainstays. Consult your drawing and determine where the dropouts have to be relative to your BB. Be sure the proper sized wheel with tire will fit without rubbing against the seat tube. When you have this length you can rough cut the chainstays (CS) to length.
Now you can move onto bending the chainstays. The bend is needed so that the dropouts will be in plane with the center plane of the bike. There are many ways to bend tubes. Simple jigs can be made in the garage that require little more than a vise and some wood that has been cut to the correct profile, otherwise more elaborate setups can be made, but they all accomplish the same thing. Consult your drawing and determine where the bends need to be so that the dropouts will have the correct spacing.
Next you can attach your dropouts to the end of the chainstays. Depending on what kind of dropouts you have this might vary. In this case we are using a plug style dropout so we are able to silver solder it into our CS. Other types of dropouts may need to be fillet brazed into place, so do your research ahead of time.
At this point the chainstays can be inserted into the BB, traced and mitered. The dropouts are held on a threaded rod and can now be jigged using this threaded rod. Being sure to remeasure everything to ensure that the dropout spacing is correct and that everything is centered. With that set the BB - CS interface can be soldered.
We're almost there!
With the
Step 10: The Rear Triangle - Seat Stays
The last tubes we'll add to the frame are the seat stays. On this frame we're using plugs (sometimes called slugs) on the seat tube side. This should be fit and soldered into place first. With that done, the seat stay can be rough cut to length and final fitted to the dropouts. The Jiggernaut uses a simple post to hold the seat stays in place before soldering. We adjust this post so that the stays take the correct angle and then we can flux and solder the dropout end and the seat tube end.
Step 11: Clean Up, Braze Ons, and Finishing
At this point you'll have something that looks a lot like a bike frame. Depending on how you want the bike to function, you might decide to install your different braze-ons at this time (Water bottle bosses, brake bride, pump pegs, etc...) Then comes the clean up step. First you're going to want to remove all of the flux from the frame. You're going to want to do this anytime that you will be leaving the frame overnight without finishing it. So if you can only do one joint per day, you'll want to clean the flux off after each session. The reason is that it will allow the tubes to surface rust, but this can be avoided by scrubbing the joint off with a stiff brush and hot water. After the flux has been removed you can break out the sandpaper and files so start removing any extra silver or brass that may have accumulated at the joints. Be gentle and take care not to mar the steel tubing underneath. You will be able to remove the excess with patience. Now start sanding everything up so that it's smooth and shiny. If it looks bad without paint it probably isn't going to look much better with paint.
Depending on how long the head tube is, you might have some excess sticking out of the HT-TT joint. This can be rough cut with a hacksaw and finished at a local bike shop, framibuilding shop, or you can order the tool to face the HT. The BB threads should probably be chased with a tap too.
At this point, give yourself a pat on the back, you've just built your own bike frame! Doesn't it feel good?
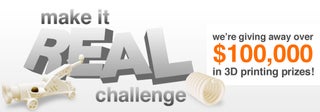
Participated in the
Make It Real Challenge