Introduction: Cedar Paneling for Van Interior
We love skiing. We love mountain life. We love the feel of rustic cabins. We love the smell of cedar. We wanted a real cabin on wheels. This means there was only one material we wanted to use for the walls and ceiling of the van: CEDAR PANELS!
The process of applying cedar panels to the walls of the van took about 4 days with 2 people working in the van. Cedar paneling is not a cheap choice (about 25$ for 14 sq feet), however this is a choice driven by aesthetics and sensual perception. Cedar is also a great wood for a mobile ski cabin since it has a great reaction to humidity (and smells amazing when we boil water in the morning for tea and coffee). For the whole van, it was about 300$ to cover the walls.
This is our third step in the conversion of our Sprinter van. See the two previous steps here: Insulation and Storage platform.
UPDATE: Since then, we have made some progress on the van. Here is the next step: Bed-Table-Benches unit and its cushions!
DISCLAIMER: This is the first van conversion we are doing, so this is certainly a process of trial and error! We tried to describe at every step the reasons why we made the choice materials we made, so hopefully you can see that we used common sense to design this process. I am an industrial designer and design researcher and my boyfriend is a landscape architect with some knowledge in wood working. We see this project as an experiment and as a wonderful place to try out some ideas about design, materials and fabrication.
For an overview of the work we did, take a look at our timelapse videos!
Step 1: Materials
You will need:
- Cedar panels (8 feet long, 4 x 5/16)
- Pine studs (8 feet long, 1 x 2)
- Screws (8 1 1/4)
- Nails (5/8 (gauge 18))
- Wood glue
Step 2: Tools
You will need:
- A mitter saw
- A drill with a metal bit of 1/8
- A screw driver
- A nail gun with 5/8 nails (gauge 18)
- A small table saw
- A measuring tape
- A set square
Again, thanks to the Vancouver Tool Library for most of the tools!
Step 3: Start on the Small Wall - Install Studs
We did not want to attach all the panels directly to the metal walls in the van because it would have been quite difficult and fragile, so we installed vertical studs (1x2 inches) on which we would then be able to nail the cedar panels.
The van has a natural curve and taper towards the ceiling. This meant that we could not use one stud to go directly from floor to ceiling. While looking at the structure of the van, we decided that the easiest would be to separate it into three sections, based on where the metal studs are. We measured the three sections and cut studs accordingly (12 inches for the bottom, 34 for the middle, and 14 for the top). Our goal was to place them as much as possible at equal distances (about 16 inches). However, some details in the van required us to shift some studs around a bit.
- With the mitter saw, cut the studs to dimension.
- With the drill (and a friend holding the studs), make a hole (pre-drill) that goes through the stud and the metal sheet of the van wall. Make sure you are drilling only the metal stud and that nothing is coming out through the exterior wall of the van. We used a metal bit of 1/8 for screws of gauge 8.
- Once the holes are done, change your bit on the drill to screw the screws in the pre-holes.
Step 4: Install Panels
We started at the bottom, placing the first panel just on top of the carpet on the platform. Again, since the van is not straight, we measured the specific length for each panel. We used the nail gun to attach each panel, by placing a nail on each stud. After the first one, we placed the subsequent ones with the help of the tongue and groove form. We used a nail only at the top of the panel, close to the tongue so that the nail would be hidden by the groove of the next one (see photos). We continued until we could not add another one at the top.
Step 5: Leave Some Space for Existing Lights
Once we reached the top of the small wall, we had to cut out some space to let the light shine through. We used a hand saw to cut the details.
Step 6: Now for the Long Wall
On the other side, we used the same strategy. We needed to make sure, however, that when we are starting at the bottom on the floor of the van, that when we would reach the platform, the next panel would also fit. We took our time to place panels without nailing them to measure precisely how much we needed to shave off of the bottom panel to arrive flush at the top. We used a table saw to cut the panel on the length.
Once again, we measured the length needed for each new panel, to make sure it was the proper size. Since the wall was longer than 10 feet, we had to use a full panel, plus a section of an additional one. We made sure the junction point was on a stud, to be able to nail the ends of both panels there. We alternated the long and the short ones, like bricks.
Step 7: Secure the Wires
We wanted to keep the wires running at the top of the walls. They were already bundled together, so we just added c-clamps on the studs to hold them in place.
Step 8: The Ceiling
For the ceiling, we added 1 x 2 pine studs to the existing ribs in the ceiling in the van. This is the same idea as for the walls, we install those ribs so that we can nail the cedar panels right in there. Again, since the ceiling is not perfectly flat, we used 3 sections of 1 x 2 to follow the arc. We used one of 18 inches for the center, then 2 of 17 inches for the sides. This was easy to install by drilling in the ceiling rib and screwing the pine studs in.
The two extremities (just behind the driver's seat and just above the back door) required a bit more attention. It was not possible to add the studs flat to the ends, so we placed them on the vertical profile on the side of the walls. When doing this, we made sure that the bottom of the stud was aligned with the bottom of the other studs so that the cedar panels would follow a nice straight line.
Once the studs are installed, it is time to start adding the panels. We started in the middle, with one panel. There was not really a straight forward way to check if it was straight, so we eye balled it (with a few extra measures taken from each side). We followed the same strategy as for the walls, by adding, panel by panel on each side of the central panel. We did a bit of découpage around the ceiling vent, but nothing fancy. We also did some découpage for the last panel by the door.
Step 9: Top Corners
The final step was to create the junction between the walls and the ceiling, to cover the crack left there. We also wanted this last piece to be removable, if we ever needed to change, add or remove wires. We measured the length of the pieces first and cut them with the miter saw.
We used a small finition table saw to cut 45 degrees angles on each side. The small saw worked really well since it is quite delicate and did not split the cedar panels.
We predrilled the panels and used small screws to attach to the wall.
Step 10: All Done, Ready to Go!
This is it!
We have been using the van for a year with the wall panels now. We were afraid that the nails would become loose after a while, because of the vibration when driving. We are pretty impressed with how sturdy it is and how this is working quite well in the end. We were also curious about how it might crack or squeak when driving (because we are super aware of all the noises in the van, and easily irritated!). The walls themselves are good and do not make any noises. We did notice, however, some squeaking where the panels meet the side of the bottom platform (end to end). It would be best to always leave at least 1/8 between the end of the panels and any grounded furniture piece.
We were also concerned with how the wood would expand and shrink with temperature change (skiing at -15 deg celsius, and visiting interior BC at + 35 deg celsius), but the wood seems to be taking it great! And, a great plus, when you boil water in a cold morning for tea and coffee, the van actually smells like cedar saunas!
Any questions? Comments?
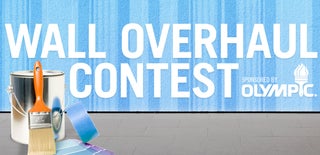
Participated in the
Wall Overhaul
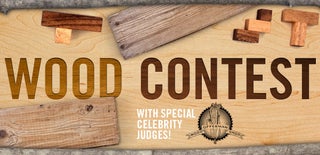
Participated in the
Wood Contest