Introduction: Christmas Changing Color LED Window Candle
Well it is that time of year again and I hauled out the decorations only to find one of my window candles was broken. After not being able to find the exact replacement to match the ones I had, I set out to rebuild them to something completely different. Enter the Changing Color Window Candle! Remember the 1960's when white Christmas trees had a revolving color wheel over a spot light to change it's color? Well, now you can have this same effect on your Christmas Candles! Let's get started!
New AA Battery powered candles $4.00 for a pair
AA Batteries ~$3.00
Led Slow Changing Color type ~$7.00 for 50 on eBay
50 Ohm resistors $1.00 for 5
Silicone caulk $4.00 tube
Start by removing the bulb from the candle and crush the glass using a pliers. Wear eye protection and gloves to protect yourself from injury.
Step 1:
Grid off the bottom of the brass base and drill out the resin base to make a hole through the bottom of the brass base.
Solder the 50 ohm resistor to the positive lead of the LED. The positive is the lead that goes to the smaller half of the junction inside the LED.
Use heat shrink tubing to protect the leads from shorting and to cover the resistor. Follow up with a second cover of tubing to cover the negative lead. This should look like the candle wick when done!
Take a small wire cutter and cut a small slot into the side of the brass base. Do this where the solder was previously soldered for the bulb as it makes for a neater job. Now bend the negative lead at a 90 degree angle to reach the brass side wall of the base.
Insert the LED assembly into the brass passing the positive lead to the bottom and wrap the negative lead to the cut in the wall.
Solder the negative lead to the wall.
Step 2:
Bend a loop on the positive lead and bend over to be 90 degrees to the bottom of the base. Solder a ball on this loop to make a contact point.
Thread the base back into the candle ring and flip over to add a dab of epoxy to hold the positive contact point centered and from shorting out to the base. Be VERY careful not to get epoxy on the sides of the base or it will not allow for continuity to occur.
When the epoxy is dry, file off the epoxy that collected on the positive contact point.
Test the continuity into the candle holder base to ensure the LED lights. If it does not light, check the polarity of the LED and ensure there is no epoxy on the sides of the base.
Now to make the flame...
Step 3:
Save the plastic from the packaging and cut the shape of a flame sized to fit the top of the candle. Cut out a small cut out to fit the plastic flame shape over the led.
Use a small dab of silicone to adhere the plastic flame as it straddles over the top of the LED. The dab of silicone should be enough to hold the flame upright until it sets up.
Follow up with more silicone to coat both sides of the plastic to give the flame a three dimensional look. Let dry.
Now add in the batteries and fit the flame top to the candle and ensure it lights.
My last step (shown on the cover photo) was to melt some white candle wax and fill in the top of the candle brass base to make it look even more real / finished off. But to prevent the wax from running around the base threds and filling the inside of the candle, pack the top with shaved bits of wax first, then when the molten wax is poured over that, it will fuse everything together and not run into the candle, leaving a clean and real looking top,
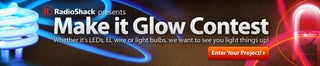
Participated in the
Make It Glow