Introduction: Coil Pump V2.0 - Testing Rig
This Instructable is a guide to constructing and operating a simple coil pump.
Sousdey from Cambodia, and welcome to our project!
Following our first Instructable, How to make a very simple hand-operated water pump using components easily found around most properties, we have developed our project to address some of the problems and inefficiencies and we encountered with our first coil pump.
Here are our included improvements for this pump:
1. Include a central axle and bearing to more easily control rotation and rotational speeds
2. Include a swivel joint that allows the pump to rotate while the outlet pipe remains stationary
3. Increase the diameter of the hosepipe used in the pump
4. Increase the length of the hosepipe used in the pump
5. Use a single length of hose for the whole pump assembly
6. Increase the overall diameter and length of the pump to approximately twice their original size
7. Provide a jacket for the pump to protect the hosepipe during operation
The following steps of this Instructable detail how to make and operate our coil pump V2.0, which outperformed our V1.0 pump by 10x - we moved 21.7 liters of water through 3.1 meters of vertical height in 3 minutes... and there's still room for improvement.
Thanks for visiting - we hope you enjoy this build :D
Aziza's Place, Cambodia.
http://www.azizafoundation.org/projects_aziza.html
https://www.facebook.com/pages/Azizas-Place/339342099551
https://www.instructables.com/id/Coil-Pump/
*Edit - Monday 05 September 2011 - The comments section of this Instructable has been handed over to students studying English at Aziza's Place. If you have any questions for the students, please ask them here... we'll get right back to you.(Moderated)
*Edit 2 - Wednesday the 14th of September 2011
The students are currently working on designing a source of motive power for this pump - see step 9.
*Edit 3 - Friday the 30th of September
We've now designed a power source for the pump - a garden swing - see here for 3 videos
For this project, you will need:
Build time
1 full day
Tools
a gas blowtorch or similar heat source
an old 8mm bolt
a sharp knife or strong scissors
a thin, flat spanner
a regular spanner
a metal bar or tube with a slightly larger outside diameter than your hosepipe
Materials
a large bucket
a bicycle wheel
an empty 20 liter water bottle with a screw-on cap (a bottle from a drinking fountain is perfect)
X meters of hosepipe
pvc plumbing fittings
brass plumbing fittings
jubilee clips
a roll of 2" wide scotch tape
an old flip-flop
several large-diameter metal washers
one of the nuts that originally held the wheel onto the bicycle
a tub of automotive grease
a contained source of water for the pump
Step 1: Axle and Bearing
1. Remove the front wheel of a bicycle.
2. Loosen the 4 nuts that hold the axle and bearings in place and slowly thread the axle through all of the nuts until the axle protrudes as far as possible from one side of the wheel and you can still tighten the nuts to it on the other side of the wheel.
3. Re-tighten all of the nuts and lock the axle in its new position.
Before beginning this step, it would be a good idea to check whether you have chosen a good wheel to use.
Flip the bike over to stand on its saddle and spin the front wheel.
Check 2 things:
1. The wheel is straight - look for side-to-side movement of the wheel rim as it rotates
If you know how to straighten a bike wheel, get to it. If you don't know how, here's a link to truing a wheel. Unless it's a really badly bent wheel, it won't affect your pump.
2. The axle is straight - assuming the wheel is straight, remove the nuts holding the wheel in place and then spin the wheel gently while it's still on the bike; look for movement in the ends of the axle.
A bent bike axle cannot easily be fixed, but unless it's really badly bent it won't harm your coil pump - find another axle or another wheel if you want to.
Possible problems:
- The axle nuts have become frozen with age. Find some penetrating oil or WD40, spray the problem areas and leave the wheel overnight for the lubricant to take effect.
- Loosening the nuts around the wheel axle bearings too much may mean that the ball bearings fall out. Be careful and be aware of this when adjusting the axle position, don't move the nuts far from the wheel - just loosening them enough to be able to turn the axle through them is OK.
- The bike wheel won't spin freely now that I've adjusted the axle. The nuts are too tightly closed into the wheel. Loosen the nuts on one side of the wheel until the wheel spins freely and then lock them in that new position - it may only be a tiny adjustment... see here for more details
- The axle wobbles in my hand and the wheel doesn't run in a level circle. The nuts are too loosely closed into the wheel. Bring the nuts on one side closer to the wheel until it runs smoothly and then lock them in that new position - it may only be a tiny adjustment... see here for more details
The bicycle is without doubt the best form of transport in the universe, and a healthy bike should most definitely be kept in one piece and used for its intended purpose as much as humanly possible.
We can assure you that no bikes were permanently harmed in the construction of this pump.
(If you're wondering what you can do with the bike that has no front wheel at the moment, take a look at this...)
*Edit - Monday 05 September 2011 - The comments section of this Instructable has been handed over to students studying English at Aziza's Place. If you have any questions for the students, please ask them here... we'll get right back to you.(Moderated)
Step 2: Begin Construction From the Axle.
You will need:
a large bucket
some large metal washers
the screw cap from the 20 liter water bottle
an old 8mm bolt
an old flip-flop
one of the nuts that originally held the wheel onto the bicycle
1. Turn the large bucket upside down and locate and mark the centre of its base.
2. Locate and mark the centre of the screw cap from the 20 liter water bottle.
3. Heat the old 8mm bolt with your gas torch, then use that bolt to melt a hole directly through each of those centres.
4. Place the wheel bridging a small gap between 2 workbenches so that the axle can spin freely, then put the first metal washer onto the axle. This will be a load-bearing, supporting washer - so it should have a large outside diameter, but it should fit the axle well.
5. Cut a length from the heel of the old flip-flop. This will be a support and cushion for the bucket base and hopefully will help to avoid any cracking of the plastic immediately around the hole. If your bucket base is shaped, (ours had a concentric "cup and ring" design), then whittle or cut the flip-flop to fit the shape of the bottom of the bucket.
Make a hole in the centre of the cushion and drop it onto the axle.
Now cut another length from the flip-flop and shape it to suit the inside surface of the bottom of the bucket - we had 1 concave and 1 convex cushion.
6. Place the bucket onto the axle, then drop the second cushion into place.
7. Over the second cushion, place another large metal washer - ideally of the same size as the 20 liter bottle cap or larger, then drop the bottle cap onto the axle. Later, we will be screwing the 20 liter bottle into its own cap inside the bucket..
8. Put another metal washer onto the axle inside the bottle cap. If possible, find a washer that fits the axle well and also leaves just enough room beyond its outer edge to allow the bottle to screw into place completely to its cap.
9. Tighten everything up together with the nut that originally held the wheel onto the bicycle.
Make any minor adjustments in centering everything at this stage. Keeping the bicycle wheel horizontal, screw the water bottle into its cap and spin the assembly gently to check alignments. If your bucket-bottom is shaped, be careful not to over-tighten anything and crack or break the bottom of the bucket.
Possible problems:
- The bucket doesn't rotate smoothly. Check that your wheel bearings are neither too loose nor too tight.
- The bucket wobbles when it rotates. Check that your flip-flop cushions are positioned centrally - and, if you shaped them, check that they are regularly shaped.Check that the nut holding the assembly together isn't loose. If you used washers that were a loose fit for the axle, check that they are centrally located.
- The 20 liter bottle doesn't spin correctly and unbalances everything. These bottles are often recycled many times; your bottle may be damaged - try using another bottle. The washer inside the bottle cap may be catching the bottle rim and pushing it off-centre.
- The whole assembly wobbles from side to side when it rotates. The bottom cushion may be out of position or not regularly shaped. Your bicycle axle may be bent - replace it or try using another bike wheel. Your bicycle wheel may be bent and causing rocking on your bench - use a different wheel if you like, but this is not necessary for the operation of the pump.
Step 3: Fitting the Pump Outlet Hose
You will need:
the 20 liter water bottle
a gas blowtorch or similar heat source
a metal bar or tube of slightly larger diameter than your hosepipe
1 meter of reinforced-wall hosepipe.
a brass hose-barb to threaded-pipe connector
a jubilee clip
a large metal washer
a pvc threaded connector
Turn the water bottle over and locate and mark the center of its base, then heat the metal bar or tube and melt a hole through the center of the bottom of the bottle. The hose will exit the bottle and the pump here.
Next, lay the bottle on its side and melt another hole at the lowest point of the bottle wall before any curvature to its base begins - make the hole 25% to 50% bigger than the diameter of the hose. The hose will enter the bottle here.
Now take the 1 meter of reinforced hose and attach the brass hose-barb with the jubilee clip. The threaded section of this brass part will pass through a large metal washer and then the bottom of the bottle from the inside, and the pvc threaded connector will screw onto the brass part from the outside of the bottle.
Drop the washer through the neck of the bottle, then pass the "brass fitting end" of the hose through, too. Judicious twiddling with a long stick can align the washer, brass threaded connector, and hole in the bottom of the bucket to allow the pvc threaded connector to be tightened into place. Don't over-tighten the pvc part, you can strip the threads very easily.
Next, push the entire meter of hose into the bottle, then use the same long-stick-twiddling technique to locate and pull the end of the hose through the hole in the side of the bottle. When pulling the hose through, watch through the neck of the bottle and leave a long enough single loop of hose within the bottle to avoid kinking and closing the pipe. Twist the reinforced hose to remove extra loops inside the bottle.
Congratulations! You have just completed the most difficult part of this build.
Possible problems:
- Can't align the washer, brass fitting, and the hole in the bottom of the bucket to fit the pvc part. Put the stick through the hole in the bottom of the bottle. Look through the bottle neck while feeding the parts onto the stick in sequence. Push and twist the stick as far up the hose as possible, then slowly draw them all toward the exit hole. Put the pvc part onto the other end of the stick and screw it all together - don't remove the stick until it's all finished... patience, Jedi; the force is with you.
- The hose kinks at the hole in the side of the bottle when I start to coil it around the bottle. Push the hose back into the bottle. Reheat your metal bar or tube, and then carefully deform the hole horizontally to provide a smoother outlet route for the hose. If that doesn't work, use a stronger hose.
Step 4: Coiling the Inner Pump Hose
You will need:
X meters of regular garden hosepipe (we used 20 meters inside the pump)
a roll of 2" wide scotch tape or similar
Connect the reinforced hose to your regular hose, then, using scotch tape to secure the hose to the bottle every few turns, begin to coil a rising spiral around the bottle from its base. Coil the hose tightly but without deformation and with each successive turn touching the last. Stop coiling and secure all of the coiled hose in place well with scotch tape when curvature towards the bottle neck begins.
Do not cut the hose at this point.
Check both the coiled and reinforced hoses along their full length for kinking or twisting that may restrict water flow.
Step 5: Assembling the Pump and Coiling the Outer Pump Hose
Now it's time to connect the 2 parts of the pump together.
Take the whole of your length of hose and the water bottle over to the large bucket that you mounted on the bicycle wheel axle.
Pass the bottle "neck-first" into the bucket and screw it into its own cap, (hold the bottle still and turn the bucket).
The inner coil of the pump is now in place, and we only need to form the outer coil to finish the pump.
It's important that the outer coil follows a pattern of increasing the coil diameter with each turn as coiling continues from this point on.
Without changing the coil direction, continue the coil of hose from the bottle as closely to the bucket wall as possible. At this stage, be very wary of kinking or twisting the pipe as problems cannot easily be seen at the bottom of the bucket. Use packing materials placed into the bottom of the bucket to help keep the hose in place for the lower coils if needed. Continue coiling the hose to form another rising spiral up the inside wall of the bucket to its rim.
A space will develop between the bottle and the bucket as your coil gets higher - either fill this space with coiled pipe*, (*remember - increasing coil diameter with each turn is required), or pack this gap to keep the hose in place against the side of the bucket.
When your coiled hose reaches the top of the bucket, you've finished the coiling. Pack out any remaining large gaps and make sure that nothing can move inside the bucket.
Fasten the top layers of pipe with wire to keep everything in place when the pump is operating. Don't try to make the top of the bucket watertight - you need water to be able to get into the bucket.
Well done - you have finished building your pump.
Step 6: Rotating Pipe Joint / Swivel Fitting
This part is still a work-in-progress for us.
At the moment, we have a 6" length of pvc pipe that fits snugly into the pvc connector, and - lubricated with automotive grease - this can be held in place by hand and works reasonably well. We also cut off this pvc adapter and used just the plain blue hose fed into the bottle outlet as it was an excellent fit and gave more working room.
The rotating joint is perhaps the most important part of the pump. When we've chosen the best of our designs, we will update this step with the details.
Step 7: Filling and Operating the Pump
Tilt the whole pump assembly at around 30 to 40 degrees in the pump's water supply container while that container is empty, then fill the container with water. To avoid undue strain on the bucket and axle, while filling, try to keep the water levels at roughly the same height both inside and outside the bucket, so spin the bucket slowly and introduce water into the coils of the pump. If the assembly starts to float, let the air out of the bicycle tyre and let water enter the central water bottle through the hole made for the hosepipe to enter it. The idea is to try to let the water in in such a way that it rises to an equal height in all parts of the whole system while filling the supply container.
Attach the rotating joint and hose leading to your collection and measuring bucket, and ensure that the open end of the hosepipe can catch around 50% air and 50% water with each turn, then spin the bucket in the correct direction. Your pump should now be working.
Step 8: Results = 7+ Liters a Minute Flow Rate
Pump V2.0 easily outperformed pump V1.0 and moved 10 times the volume in the same amount of time and to the same height.
We turned the pump by hand at 3 different speeds and for a timed 3 minute period for each test run. Pump revolutions were counted for each test and then divided by 3 to give an average rpm figure.
Test 3 = find the biggest guys around and encourage them to turn the pump as fast as they can. The test was performed twice with different operators and returned almost exactly the same results for each test. The people counting revolutions during test 3 lost count at around 200 on both runs.
All results are for moving the water to a height of 3.1 meters, as that's the height of the first floor a traditional wooden Khmer stilted-house.
Test 1. @ 17rpm, the pump moved 6.9 liters of water.
Test 2. @ 31rpm, the pump moved 12 liters of water.
Test 3. @ over 70rpm, the pump moved 21.7 liters of water.
21.7 liters!
That's over 7 liters a minute...
... or more than 1 liter every 10 seconds.
I'm very happy to say that's a brilliant result, and well done to all there today!
Step 9: Powering the Pump...
*Edit - Wednesday the 14th of September 2011
The students are currently working on designing a source of motive power for this pump.
We settled on using a garden swing after Sengkry's request that it be "hammock powered"... he's ducking out of the first picture on the right, there.
Modeling the swing framework...
The idea is that the swing moves a bicycle front wheel attached to the top swing pivot / axle.
That axle turns through 90 degrees when the swinger swings.
From the bicycle wheel rim, a connecting belt or chain drives the freewheel hub of a bicycle rear wheel, which translates the to-and-fro motion of the first wheel into a single direction and higher rotation at the second wheel - perhaps 2.5 revolutions per swing.
Here's the idea...
Thursday...the finished models...
Bamboo is our choice of construction material for the swing, and we easily found a source in Phnom Penh; it's available all over Cambodia.
The bamboo was assessed for its straightness - none of the pieces we got were entirely straight to their full 6 meter length, but all but 2 stems contained long straight sections. These sections were measured, marked and recorded.
With an eye to the best construction ideas from the modeling session, chopsticks were cut to scaled lengths to match the assessed bamboo and then we figured out the best way to achieve our aims using our available building materials.
We'll update you when we've got it up and running; building starts tomorrow...
Step 10: Swing - Frame Construction
This step of our Instructable is a diary of progress in making a drive system for the pump. We'll make a new Instructable detailing how to make this swing-drive system when we've got it up and running.
Friday the 16th of September
We got the A-frames measured and cut and got the sharp end roughly assembled today.
It's only pinned together for now - we'll tighten and straighten everything up tomorrow when we get the lashing done.
The drive wheel is only wedged in place in these photos - but you can see the idea...
Please bear in mind that between myself and Mr Makara, we have absolutely no experience of building with bamboo. If you can see anything here that's an obvious mistake, please let us know?
Thanks!
Saturday the 17th of September
We finished the A-frames and got all of the structural components cut, pinned, and mostly lashed today.
Making pins
An A-frame drilled. pinned and ready for lashing
Measuring by comparison...
Both A-frames finished
The swing roughly assembled - this set up held 135kg without a single creak... both of us were hanging from it!
A V-belt driven by the upper wheel and connected to a length of bike chain driving the freewheel on a smaller wheel, which will be attached to the bottom of the bucket, will drive the pump directly.
After today's building, I'm absolutely positive that we'll generate more than enough torque to do the job - but will the top bike wheel transmit that power cleanly...?
Sunday the 18th of September
Working on my own today as all of the kids and staff were at the annual Phnom Penh Karate competition - they came back with a whole bunch of medals - WELL DONE!
Finished the swing frame and all of the lashing... the top tie-bars, bottom spreader-bars, bottom cross-brace, and bottom tie-bars are all in place. I tested the frame with 4 volunteers who have a combined weight of 234kg - all hanging from the top tie bars. No problems, not even a creak!
I also found a possible solution to the pump swivel joint problem today - I dug up some brass plumbing fittings and nylon washers in a local store that do the job very well - they will restrict the pipe diameter to around 5/8" for a 1" distance, though... we'll see if and how that affects the pump output when it's up and running again.
Plans for tomorrow afternoon - rebuild the pump with the coils in the opposite direction to match the new drive setup.
Two major hurdles remain:
1. Connect the top bicycle wheel to the swing pivot arm
2. Build in a tensioning system for the drive belt and chain
For connecting the top bicycle wheel to the swing pivot, I'm thinking of setting a 1/2" drive, deep 17mm socket and long extension in either concrete or hard car-body filler within the end culm of the bamboo... if I can get the socket and extension centered correctly and key them to the concrete or filler (maybe with a T-bar), then reinforce the areas around all holes with wide jubilee clips, that should be solid enough to drive the wheel. The extended wheel axle will need 2 sets of locked nuts, a pair at each end of the protruding axle, to stabilise the 17mm socket.
The tensioning system plans for the moment are to place a bamboo tube across the gap between the A-frame crossbar and water pot rim and then use a tensioned/twisted loop from the bottom tie-bar to hold the tube solidly in place.
I'll set another deep 17mm socket and extension in body-filler within a section of pvc pipe, which will turn within the bamboo tube. Putting the belt and chain on first, then tensioning the twisted loop will hopefully hold down the bottom bike wheel axle to the correct height in the water for pump operation and also create enough tension/friction for the V-belt for it all to work.
The best-laid plans of mice and men...
We'll see.
Monday the 19th of September
Rebuilt the pump on a 10" rear bicycle wheel - the bike repair shop threw in a new, longer axle with the old wheel, so the belt and chain tensioning should be very easy.
The students have been given the task of designing an operating system that allows the pump and swing to be in a body of water and the operator on dry land. Very quickly, they came up with the idea of a barrel raft and, when told of it - 4 ways to minimise or stop the rocking motion that the swing would cause:
1. Fill additional barrels with water and place them at the waterline alongside the air barrels at ends of the raft to act as ballast weights
2. Add drogue anchors (they knew and suggested the concept)!
3. Tie guy lines from the raft to the shore
4. Set up 2 swings to act as harmonic pendulums (where that idea came from is beyond me - an excellent suggestion)!!
They'll be designing a system to allow best use of the pump and swing in Cambodia entirely on their own.
The process will have an open time-frame and will include designing, modeling, testing with models, troubleshooting and problem solving, and finally - construction.
Thinking-caps on, guys and gals... you can do it!
Tuesday the 20th of September
Sorted out the anchoring for the top wheel.
An old spark-plug tubular spanner fitted the nuts on the wheel axle nicely - I filled the center of the tube with car body filler ($2.50) to hold the axle beyond the nuts centrally, then found a reasonably fitting length of bamboo to drop over the spanner tube - also held centered with body filler.
This incremental increase of the axle diameter by sleeving makes fitting it into to the large bamboo pivot bar far easier. Next - to drop the expanded wheel axle into the pivot bar and drill 2 holes at 90 degrees through all layers, push bolts through to provide the key for the spanner and sleeves, and then fill any remaining empty space in the end culm of the pivot arm with cement.
Filled the last culm of the "other end" of the pivot bar with cement. This is the section of bamboo that the swing will be turning on, and it was a large void to fill - 1kg of cement ($0.25) and around 1/2 a liter of water.
Found a long V-belt near the market ($2) and set up the tensioner bushing. A deep 17mm socket ($1.50) and a long socket extension (already had) run through a fortuitously sized tube of bamboo. Previously, in the comments section, I've been advised against the use of automotive grease on health grounds, but as this part will not be exposed to the water in the test - I used grease here to help the extension run smoothly in the bamboo tube.
Main problems solved, I think.
Tomorrow - drill the wheel axle sleeves and pivot bar, bolt up and cement all in place, split the V-belt and let in a length of bicycle chain.
Thursday - attach swing arms to the pivot bar, assemble everything, and we're all set to go!
Wednesday the 21st of September
Keyed in
As level as the bamboo will allow, and cemented in place
This belt will be drilled and then the chain ($1.75) bolted to it - when the cement has set and we can set up the drive to gauge height.
Thursday the 22nd of September
Got the drive system connected up and running today. Didn't start to add the swing arms and seat as we ran into a few problems with the rigidity of the output drive and the transfer of torque from the bike axle to wheel rim...
1. The chain kept jumping off as the pump moved slightly out of alignment in the water. Need to add in something more to the framework to keep the pump in a stable position, yet allow it to rotate.
The tensioner was tightened to 2 twisted loops and lashed across the A-frame
2. The axle span in position within the wheel; I need to beef up the joint between axle and wheel. I used a friction connection - will try a directly connected drive... worried about the wheel spokes folding under heavy load, though - do it and see, methinks.
A PVC pipe connector holds the swing pivot bar in place at both ends.
Video download here. Swing powered water pump first assembly run.AVI - 32.8mb file
Pump output was low as the pump was riding high in the water at around 25% immersion to allow clearance for the drive and outlet over the rain barrel rim, and we were turning it very slowly.
Good news -
1. The tensioning system and belt and chain combination worked well. There was slight belt slippage if sudden force was applied to the wheel rim, but overall performance was as good as could be expected on the first day.
V belt drilled and bolted to the chain
Plenty of chain to allow for a high swinging angle
2. The keyed drive shaft worked perfectly.
3. The new outlet swivel valve worked perfectly.
Not much to see, but this is a perfect joint.
Outlet end of the pump lashed across 2 poles to keep it still
4. The pump worked perfectly at the low speeds we turned it at and self primed at every restart; just spin it and it works - no special attention needed.
Overall for the day - Good. She's working - and just needs a debug.
Friday the 23rd of September
1. The chain kept jumping off as the pump moved slightly out of alignment in the water. Need to add in something more to the framework to keep the pump in a stable position, yet allow it to rotate.
Got this one sorted out today. Added an extra strut to the A-frame to support the bamboo bush and filled all empty space on the axle of the small bike wheel with locked nuts. Had to back the chain off the V belt by one link, but that was all it took.
Now that the pump is stable in the water, I can add more water to the barrel, which puts more of the pump underwater - which allowed it to move a higher volume of water than yesterday. The pump's still around 20% too high, though, so output's not what it was when turning the pump in the barrel by hand.
Video download here - apologies for the sound quality, it was raining. Swing powered water pump second assembly run.avi 14.4mb
It's a little harder to turn the top bike wheel now, and the pressure from the tensioner is causing the top bike wheel to come out of alignment when the wheel is turned from its rim... but that's a job for Monday. Perhaps replacing the bamboo bush with a bike wheel-bearing assembly or bottom bracket-bearing to remove some of the friction there will sort that out.
I may develop two swing pivot bars - one using the bamboo pole and one using a length of steel scaffold pipe. The bamboo's strong enough for the job, but it's a natural material and I don't think it's controllable enough in its movement for me to mesh it with the chain drive. Scaffold pipe would give me a straight bar and allow me to support (and possibly drive) the pump at both ends, which would complete the strengthening of this part of the system.
Sunday the 25th of September
Took a day off for thinking space yesterday and decided to move away from the bamboo pivot bar - it's just not suitable for task - it needs to be straight and capable of more than I think bamboo can do without a lot of help.
Found an old scaffold pole in Toul Sanke, the cheapest motorbike front wheel hub, 19" rim and spokes in Toul Tumpong - persuaded the hub to fit the scaffold pole and will lace up the wheel later this afternoon.
This offers a much stronger and more predictable drive - I just don't have the time or skills with bamboo to make the other option work.
We'll lose some rpm with a 2" drop in drive wheel diameter from the bicycle wheel, but the strength of the new pivot bar will allow for a shorter swing arm with a heavier load and a higher swing angle, which will more than make up for the loss. With an increased load capacity, we may even be able to fix 2 pumps in opposite phase to one swing now, which would both improve output volume and make that volume a much more constant flow.
Back to Aziza's tomorrow to fit this to the swing frame and try it out.
Monday 26th September
The motorbike wheel easily transferred the torque from the new pivot bar today.
I attached a short, 12" bamboo swing arm to the pivot bar and and drove the swing from there with little effort.
Problem solved - new problem. The pivot bar moves from side to side and pushes the chain off the pump after a few minutes... collars should fix that.
Time to add in the swing arms and trim out frictional losses in the 3 bushes.
Almost there.
Tuesday the 27th of September
Pivot bar bushes - take several old socks and cut the toes off, pass them onto the bar, then fold them back over themselves, building up a pad of material.
Add in lots of grease... hey presto - greased bushing.
Testing with 40kg on a rope... no problems at all with the swing set - needed weights at the corners, though.
But a rope's no good - we need solid pivot arms - testing with an offcut
Cut a slot for the pivot bar 2/3 of the way through the bamboo, then lash them together
1 swing arm will support at least 80kg - not swinging...
Slots cut into the swing arms to hold a dumbbell bar
Testing the swing with 2 swing arms and 50kg of weights.
This was good until we reached around a 90 degree swing arc, then things got decidedly iffy - the pivot arm bushes wouldn't stay put - the fishmouth in the bamboo strut above didn't hold them in place. Braces or wedges to the A-frame tomorrow - between the bottom-right lashing and the pvc pipe.
When that's done, we'll be all set to connect the pump and see what happens.....
2 more days?
Wednesday the 28th of September
Fixed the pivot bar bushes in place and repacked the bush lubrication, around a 1/4 pint of grease held in layered old rags then taped up for easier placement - the tape burst immediately weight was on the swing and spread grease well.
Got past the BIG one - the water acting as a brake to the pendulum - sorry, that's the part I'm not telling for now...
It works... concept proved !!
Back to Earth... I had trouble with the drive belt slipping today - it was raining hard and the surfaces wouldn't grip - the motorbike wheel needs a rain cover. The V belt wouldn't grip beyond maybe a 30 degree swing angle, so testing was limited to that and gave around 3 liters a minute. The swing will function through around 100 degrees before structural components stop higher swinging.
The markets and shops should re-open tomorrow as Pchum Ben is over now, so I can improve on one or two of the materials used today. Fine-tune for output... I can't see anything that would stop me at the very least doubling today's figure.
Hopefully it will be a dry day for a good test run - and then she's complete.
A garden swing and water pump combination - RESULT!
Friday the 30th of September
Finally got a person onto the swing, today - final proof of concept.
We widened the swinging arm placement and added a "swing seat".
Testing the swing seat
Adding weights to the swing seat for a little boost...
Max Power + 20kg!
The following links are to 4 video downloads. My apologies for the quality - I've compressed the .avi files and the .mp4s are from my cellphone.
First Trial Swing 23mb .avi
Kids Playing 11.5mb .mp4
Kids Playing 2 4.3mb .mp4
Would you like a shower? 3.3mb .avi
I didn't rebuild the pump to suit the swing drive input due to time constraints; we used the same pump configuration as for the last tests - output volume would be higher with a pump rebuild. A larger pipe diameter would give more volume of water pumped, while adding more turns to the coils of the pump would increase the power output / pumping head - but that's for later testing. We're rather limited in our water containment and materials resources at the moment, so I can't build as big as I'd like.
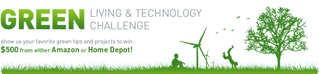
Participated in the
Green Living & Technology Challenge