Introduction: Companion Crafting for Beginners
The 'Sewn by Hand' challenge has prompted me to stop lurking and start writing :)
Hopefully by the end of this, you, good reader, will have a reasonable idea of what is required to make your very own, very traditionally styled, teddy bear!
Step 1: Firstly, Gather Your Ingredients...
For a bear the size of the one in the accompanying images, you will need;
Your choice of body fabric (this does not need to be furry, but whatever it is, you will get best results from a non-stretchy material), dimensions 100cm x 70cm.
By the by, this cut is often referred to as a "Fat Half" in crafting circles, due to the fact that fabrics are usually made 140cm wide. A "running" or "linear" metre is cut in half across the shortest dimension to make 2 fat halves. The fat half can be cut, again along the shortest dimension, to make 2 fat quarters. The fat quarter can be cut across the shortest dimension to make 2 fat eighths. Smaller than this is just getting silly...
Suitable fabric for the paws (can be anything the right colour - e.g. Velvet, suede... Again it mustn't be stretchy)
Thread to sew the nose out of (embroidery floss is good, but I have used two-toned 'butcher's twine' to good effect before...)
A pair of eyes (I would suggest in the region of 16mm diameter for a bear this size, but you would be advised to "dry fit" a variety of round things at the appropriate stage to find exactly what looks right for your new friend before committing yourself.
Eyes can be anything suitable with the right look. By suitable, I mean sew-on-able. In this example, I've used glass toy eyes, which have a wire loop on the back to fix them in place. With the right type of bear, you can also get good results using buttons, in fact, the first teds used boot buttons because they were domed, black and cheap...
Stuffing. For a bear this size, I would expect to use in the region of 600g of polyester stuffing. As with many things, Your Mileage May Vary, depending on how "squidgy" or otherwise you want your new friend.
Other stuffing materials are available (Kapok, wood-wool, sponge foam pieces...) but I do not recommend them, as they rarely feel right and tend to break down over a comparatively short time, leaving you with a saggy (or in the case of some foams, leaky) friend.
A set of 5 toy joints, around 38mm in diameter.
These consist of 2 large discs, usually made of fibreboard, 2 washers to protect said fibreboard, and a T-headed split pin at least 1.5" long. I'm sure all you bright sparks out in Makerland can whip up suitable equivalents if you need to, but they can be bought by the set out there on the interwebs, which is how I get mine.
A reel of VERY strong thread in an appropriate colour for your fabric.
I recommend 100% polyester upholstery thread, as it will stand up to the various stages of pulling and tugging that are involved later on...
A pattern
There are many free-to-download patterns for bears out there if you need a pattern. This was exactly how I started out. These days, my patterns start out as a piece of heavy-grade lining wallpaper and a vague idea...
Equipment-wise, in addition to generic sewing gear, you will need an Awl, a pair of Needle-nose Pliers, a Chenile needle for the nose, a Mattress Needle for the eyes and a Chopstick.
Step 2: Marking Out
Work out the pile of your chosen fabric.
In the case of furry material, this is the direction where the fur lies flat when you run a hand over it.
In the case of patterned fabric, it is whichever direction is down
I usually mark a small arrow in the corner as an aide memoir, as I am a master at getting distracted... This arrow must be on the back of the fabric and must point down.
For the same reasons, I routinely mark a small arrow on all pattern pieces to prevent an outbreak of "upside-down leg"
Place your fabric furry / patterned face down (hence we put the arrow on the back) on a large flat surface, with the arrow pointing towards you.
Mark out all of your pieces, except for the paws (they go on the other fabric).
Make sure that everything is pointing in the right direction (hence the arrows on the pattern) and that you have marked enough of everything (2 ears needs 4 "ear shapes")
You also need to remember to reverse most of the pattern pieces for a whole bear - The middle image may help, but don't mark out like I did - It's super wasteful...
Step 3: Cutting Out
In the case of furry fabrics, this step will reward those of you who are verrrrrrry careful...
You need to use a nice big pair of very sharp fabric scissors for this step.
Cut the pieces out without cutting the fur.
This sounds impossible at first but it isn't (after all, I can do it...)
Slide the blades between the hairs
Angle the blades to match the lay of the fur (this is often around 45 degrees) - Remember to change the angle of your scissors as you change direction whilst cutting out.
Make very small "snips" with the scissors, not big meaty slices
It may be hard to believe, but this process is easier using big scissors, as you have more control and it requires less effort.
If you use small scissors (e.g. nail scissors), your "scissor hand" will probably be screaming at you after the first few pieces
Cut out the paws. On the back of the foot pads, make a small mark at the midpoint of the Toe and the Heel.
Look upon the fruits of your labour - a pile of bear bits!
Now quit slacking and get those parts organised...
Step 4: Time to "Get Your Sew On"
Take your neatly organised pile of bits from the previous step and, bit by bit, join them up to their partners...
In yet another outbreak of "Your Mileage May Vary", there is no one "right" or "wrong" way to do this.
I tend to hand-tack using a contrasting coloured cotton thread.
You can alternatively use pins (glass-headed pins are easier to spot, I'd suggest these over small-headed pins)
The main reason behind my choice, is the fact that constantly lightly stabbing myself with pins got real old, real quick.
Don't get me wrong, I still constantly stab myself whilst sewing, just less...
When you get to putting the legs together, it is important that you leave the bottom of the foot open (this is where the paw pads will go). You also need to leave a gap in the "back" of the leg, so that you can turn the finished limb right-side-out at the end - about 2" / 5cm should do the trick.
Step 5: More Sewing!
Now you've put various bits together on a temporary basis, it's time to make things a little more permanent...
Using our nice strong thread, sew along all of the tacked seams using a back stitch. Should you need a primer on what back stitch is, I would recommend this very website - one nifty one I found was "How to Sew." penned by Jessyratfink
You can, of course, also use a sewing machine for this bit ;)
Step 6: More Tacking!
Following on from your first outbreak of sewing, it's now time to do a bunch more tacking...
Make sure that you mark the mid-point on the "nose" of the Head Gusset. This marked point needs to match up to the seam between the head sides, otherwise your bear will be decidedly wonky-looking.
Tack the halves of the arms together.
As before with the legs, make sure you leave a gap to turn the finished limb right-side-out at the end. I prefer to put the gap in where the top / inside of the arm, where the "elbow" would be, but the other side of the arm is fine too.
Have at the head.
This is one of the trickiest bits in the whole process, as the Head Gusset must be properly aligned.
Using the mark to locate the mid-point of the "Nose" at the mid-seam, start tacking / pinning from here and work along one half of the seam to the "neck".
Now, starting back at the nose, repeat along the other half of the seam.
Make with the feets.
In much the same way as you've just done the head, the foot-pads need to be lined up - the mid-point marks should line up with the toe and heel seams.
This stage often requires "fettling". Start at the "toe" and work around the edge.
If you get 3/4 down the first side and find you have a lot of excess paw to fit into the remaining space to the heel, you will need to carefully trim a crescent of material from the "heel" end of the paw pad, until the mid point lines up with the heel seam.
Use the offcut(s) as a template for the other paw pad.
I cannot emphasise enough that this is one of those times where you can always trim a bit more off, but can't put it back on if you've taken too much...
You also need to join the two halves of the body together, but I forgot to photograph this bit...
You need to leave a very small (1/4" at most) gap at the top of the body, where the four seams come together. This will make assembly easier and results on a more durable companion.
You need to leave a larger hole halfway down the back, for turning right-side-out purposes.
If you are of a mind to, this is the stage where labels and tails go in - tack them in place as you work your way along the main seam - I'm sure I don't need to tell you where tails belong...
Step 7: Yet More Sewing...
It's time to get busy with the needle once again.
All those nice freshly tacked bits? Run some proper thread around them as before in Step 5
If you have gone down the sewing machine route - be very careful when tackling the head and foot-pads.
Unlike the other, flat, seams, these seams are bendy and curvy, with bits that get in the way.
It is very easy to sew "too much" or "not enough".
For this reason, I recommend that even you die-hard machinists sew these bits by hand...
Step 8: The Great Turn-through
You have now finished 99% of the sewing needed in this project...
This next bit is where things really start coming together.
You now get to turn all of your lovingly-sewn parts right-side-out.
This is the first point in proceedings where the chopstick probably comes in handy, as it will be useful to reach up into the ends of the limbs and what-not to get those last few creases out.
Take care to use the fatter end of the chopstick, to minimise the risk of you sticking it clear through your fabric.
Yes I have done this.
Yes I cried a bit...
Step 9: Adding the Bendy Bits
We have reached the first stage of fitting the joints to the bear.
For this stage of jointing, you will need 4 of the fibreboard discs, 4 cotter pins and 4 washers.
Locate a board disc centrally at the "shoulder" of the arm, making sure it is on the same side as the paw.
The first of my frankly awful diagrams might help here, the idea is to position the joint so that there is an equal gap around the edge...
Holding the disc in place with one hand, slide a finger of your other hand inside the limb, up behind the disc. Grab a hold of the disc with the rest of your second hand to keep it in place.
Gently push the awl through the hole in the centre of the disc until you can feel it on the tip of the "inside" finger - DO NOT STAB IT IN.
Place your thumb against the tip of the awl and pinch together with your "inside" finger.
Take the disc away and put the awl back in the same place (i.e. against your thumb and touching the same part of your fingertip on the inside.
Using your fingertip as a guard against poking the awl out the other side of the arm, push the awl through the "paw side" of the arm and into the space inside.
Put a half joint together, this is a board disc (textured side up), a washer lain on top of the hole in the disc a and a cotter pin slid down through both, so that the "legs" of the pin protrude from the smooth side of the board disc.
Manoeuvre this half joint into the arm and slide the legs of the cotter pin out through the hole you made with the awl...
Yes, this is as tricky as it sounds the first few times.
To complicate(!) things, it is important that you do not snag any of the backing material of you fabric between the pin legs, as this could lead to structural bear failure at a later date.
Repeat this process for the other arm.
Looking at both legs, decide which one is the right one and which is the left.
Now go through the same jointing steps as for the arms, making sure that the joints are on the "body side" of each leg.
Step 10: Get Stuffed!
Things are really beginning to take shape around here...
The key here is to feed the stuffing in gradually.
Work the stuffing into the far ends of each limb, making sure there are no empty pockets. The fat end of your chopstick will really come into its' own at this point.
There is no "right" or "wrong" amount of stuffing at this point. It really is all about how you want your new companion to feel when you give them a cuddle at the end.
What is important, is that you must be sure to stuff the limbs to the same levels of "Squidge" (at the very least, the arms must match each other and the legs must match each other).
I recommend putting a little extra stuffing in at the joint end of the limbs, as this will help pad them out come cuddling time.
Make sure you do not get any stuffing between the board disc and the fabric of the limb.
Once all four limbs are stuffed to your satisfaction, close the gap in each limb using a "Ladder stitch".
The naff scrawl should help explain this...
I use a doubled length of the strong thread, secured to itself in the seam below the gap, then ladder stitch my way up the hole. In the diagram, dotted lines are "inside" the limb, solid lines are "outside".
Periodically pulling the sewn part closed as you go helps, especially if you've gone down the "lots of stuffing" route.
When the hole is closed, secure the thread and lose the ends inside the limb.
Step 11: How to Get AHead in Toymaking...
Putting the head together is the "Make or Break" step, as almost all of your new companions' personality will be found here.
Stuffing. Lots and lots of stuffing.
For the best results, the head needs to be pretty solidly stuffed..
As before, work the stuffing in steadily. Make sure you get all the corners in the nose/muzzle.
The head should not really have any "give" in it. This is why we are using extra-strong thread, as we don't want exploding seams at this stage.
To close the head up, pull a length of thread approximately long enough to go three times around the neck hole.
Now double it.
Double it again.
Add a little more for luck and then cut it off the reel as one length.
Fold the thread in half, then fold the doubled thread in half again. You will have a 4-stranded thread a little longer than the bit you originally though you needed.
Starting just off-centre of the midline at the back of the head (A in my naff little drawing), using a curved needle, sew this 4-strand thread around the edge of the neck hole in a running stitch, about a 1/4" away from the edge of the fabric.
When you get back to the back of the head (making sure to emerge on the opposite side of the midline [B in said scrawl]),make sure that there is the same length of thread on both sides.
Assemble a final half-joint (1 board disc, 1 washer and 1 cotter pin) and place this in the neck hole, making sure that the board disc is below the line of threads you've just put in.
Tie the first half of a surgeons knot (over-under, over-under again) and pull the neck hole closed like you would a draw-string bag. Be sure to keep the half-joint "inside" of the closure, so that the fabric closes over it.
PULL IT REALLY TIGHT.
A bit tighter than that (this is why we're using a quadrupled extra-strong thread).
Tie the second half of the knot.
Taking the loose ends in their bundles of four, sew them back around the neck hole in opposite directions.
When you get back to the back of the head, repeat the knot-tighten-knot process.
Lose the ends of the threads inside the head.
Close the open side of the ears using a whip-stitch, making sure you have a good length of thread left over to sew the ears onto the head. Put them to one side.
Work out where you want the eyes. There are many ways to do this; sheer guesswork, large headed pins, some kind of proxy (buttons, felt circles...), "dry-fitting" the eyes by resting them in about the right place...
I have a set of "position eyes" for this stage. These are black glass eyes mounted on large pins, which gives me a great deal of flexibility when sorting the eyes out.
Once you have settled on a spot, use the awl to make a hole at both locations. Assuming that you are using them, awl will also help make a bit of space in the stuffing to accommodate the loops on the back of the eyes.
Pull off a length of thread a little over double the distance from the front of the head to the back.
Double it.
Double it again.
Double it AGAIN.
Now cut it off the reel.
Fold the whole thing in half and cut it at the midpoint.
Taking each thread separately, fold them in half, then in half again.
Take the "2 loops" end and secure this to the metal loop on each eye using a Lark's Head knot.
Now it's time to break out the mattress needle. Thread the first "eye bundle" onto this beast and slide the needle into the head.
The point of the needle needs to emerge just off the centreline of the head at the back, on the same side as the eye, down towards the neck.
Do the same thing with the second eye.
It is now time to secure the eyes.
Tie the first half of a trusty surgeon's knot with the eye threads.
Now comes another fiddly bit...
You need to pull on the ends at the same time as gently pressing on the eyes to shape the head.
This is best done by cradling the head in your hands, using your thumbs on the eyes and pulling on the threads by wrapping them around your forefingers.
Finish the surgeon's knot and lose the ends inside the head.
Your companion has eyes to see by, time for the ears next.
Test-fit the ears to find the right position, then sew them on using the curved needle. A ladder stitch works well here.
The nose is the next step.
I recommend choosing a colour that works with the paws. You can pick from a variety of threads for this, but I recommend embroidery cotton.
It will probably help at this point to try a few paper shapes to get an idea of what you want it to look like and what you need to aim for when you get sewing the nose.
Put the needle in from the side of the muzzle and come out at the centre front. Leave an inch or two of a tail at the side.
Using long stitches, "sketch out" the shape of the nose.
Once you are happy with it, go over the whole nose a second time, making sure that there are no gaps.
You may find a pair of needle-nosed pliers useful here, as pushing the needle through can be tricky.
DO NOT CUT THE THREAD OFF.
With the nose now done, it's time to do the mouth.
Looking at the second naff drawing on this page, you can see that the shape you are aiming for is an inverted "Y".
A few large-headed pins will probably help here, so you can trial the shape without committing yourself.
Once you are happy, bring the nose thread out just underneath the nose and sew two long stitches down to "1", forming the "leg" of the inverted Y.
Bring the thread out at the end of one side of the Y ("2"), guide the needle behind the straight threads and then back into the muzzle at the end of the opposite side of the Y ("3").
Bring the thread out at 2 again, back behind the straight threads, back in at 3, then out at the side of the muzzle.
Lose the ends of the nose thread inside the head.
Step 12: The "bear Necessaries" of Assembly
It's construction time!
If you are working with fur that has a pile greater than 10mm, I recommend trimming the fur away from around the joint pins (i.e. over the fibreboard discs) on the limbs and from around the "neck hole" of both the body and the head, to allow you to get tighter joints.
The deeper pile furs will compress over time, meaning that the joint that you thought was nice and tight, won't be any more.
Trimming the fur down to the backing fabric will prevent this and the "bald-spots" are underneath the joints, so are not visible.
Following and necessary haircuts, start with the head.
Push the legs of the cotter pin through the small hole you left in the neck, into the body.
Assemble the second half of the joint inside the body, over the cotter pin from the head.
Use the needle-nose pliers to "roll" the legs of the cotter pin down and onto the joint washer.
The best way to think of this is the same way as opening a sardine tin with the little key - Hopefully the crappy little diagram helps :)
This process is quite physical, as you need to grip the pliers closed and twist them to roll the pin leg at the same time.
There is a specialist tool called a "Cotter Key" for this step, which is basically a large screwdriver with a slot cut in the shaft where the driver head would otherwise be. Whilst it eliminates the holding closed bit, it doesn't help on the turning front. I am hoping to find one made with a "T" handle and then I'll be set for life...
These joints need to be tight. Anything less will give you a floppy friend (unless of course, that's what you want)
Do not rush this bit, especially if you find you end up having to partially reopen the joint in order to get it to sit better. Too much bending, straightening and re-bending will cause the leg of the pin to snap through fatigue. What then follows is a soul destroying process of partially dismantling the bit of bear that contains the rest of the snapped pin to replace it.
Been there, done that, would not recommend it as a fun way to pass time.
Assuming you've survived this stage, go and make yourself a cuppa, because you're on the home straight...
Step 13: Care and Feeding of Your New Friend
Now that you've got the head, legs and arms on, it is time to give your new friend their first proper meal...
The process is pretty much the same as you did for the first round of stuffing, the only real difference is the scale of things. You will probably end up using more stuffing here than you think you will.
As before, steadily feed the stuffing in to avoid it clumping inside the bear.
Start at the top of the cavity. Make sure you get a decent amount of stuffing in around the neck joint and in the hump (traditionally-styled bears like the one in all of these photos have a pronounced hump at the top of their backs)
Take care that you don't end up with a void in front of the neck joint, as this is a particular trouble-spot.
Another issue to watch for at this stage is making sure you get enough stuffing in the "shoulders".
With the top bit mostly done, start feeding the stuffing into the bottom of the cavity. Work from the belly, back towards the tail.
Trouble-spots to watch for here are voids around the "hip joints".
Once you have a reasonable amount of stuffing at both ends, feed more stuffing in until the whole cavity is filled.
This is yet another of those "Your Mileage May Vary" moments, as the finish line is again best defined as "Enough" stuffing...
As when you were stuffing the limbs, there will be a point where your new companion has the right "squidge" for you. This is the point when you stop.
At long last, the (almost) last step...
Close the opening in the back of the body with a ladder stitch in exactly the same way you did on the limbs. Tie off the thread with a surgeons knot and lose the ends inside the body.
Give your companion a hug to welcome them into the World.
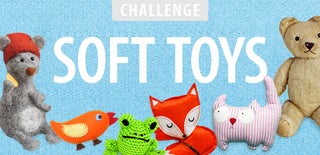
Runner Up in the
Soft Toys Challenge
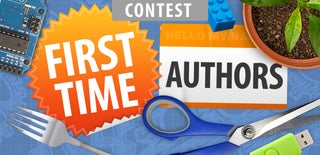
Participated in the
First Time Authors Contest 2016
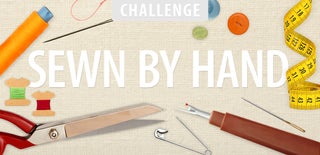
Participated in the
Sewn By Hand Challenge