Introduction: Cribbage Board Jig for a Drill Press
Cribbage is a great card game (full of weird jargon, like when you get to yell "Muggins his knob!" at your grandpa) with score kept on a classic wooden peg board. There are some good Instructables for making cribbage boards out of plastic with a laser cutter,out of wood with a CNC router, and out of wood by hand. For those of us without CNC/laser abilities and lacking super-steady hands for free hand drilling, how to get neatly aligned cribbage board holes? A cribbage board drill press jig!
I'm working on a hardwood box and cribbage board combo, so I knew I wanted very precise peg holes. The internets is full of suggestions for jigs to allow you to do precise drilling on a drill press. The idea is to brace the work piece against a backstop and use stop blocks to gradually move the piece horizontally for drilling each hole. American Woodworker had a photo of a jig using flip blocks that looked cool, but no Instructions on how to make one. Sounds like a project! Read on to learn how to make your own cribbage board drill press jig.
I made this jig in the woodshop at Tech Shop in San Jose. If you live in the Bay Area or one of Tech Shop's other locations, it's a cool place to check out - lots of tools and interesting classes. And, if you write an Instructable based on your work there, you win a free class. Check out their website: http://www.techshop.ws - maybe I should take the CNC class so I don't have to build a jig next time I need a zillion holes drilled :)
Step 1: Materials and Tools
Materials:
-2 two-foot pieces of poplar stock (or another wood - someone recommended poplar to me, but it was a little too soft. I had some splitting when it came to drilling holes)
-2 four-foot pieces of 1/4" thick poplar hobby board, 1 inch wide
-1 long wooden dowel (needs to be the same length or longer as your wood stock)
-A few screws
-Your cribbage board wood and some test scraps
Tools:
-Drill press and bits
-Hand drill and screwdriver
-Table saw with cross-cut sled
-Measuring tape
-Clamps and stop blocks
Step 2: Jig Design!
Here is a photo of my notes from trying to put together how the the jig in American Woodworker was assembled. My measurements were mostly based on the materials I had on hand - a different sized jig would obviously work. A few considerations that are important to keep in mind:
-Your jig should be square
-You'll need a jig approximately 2X as long as the cribbage boards you hope to make - two feet is a good length
-Make sure that your drill press can clear the various parts of the jig in order to allow you to drill your holes
As I built this jig, I continually dry fit pieces on the drill press itself to make sure that I had the necessary clearance for the both the cribbage board and the drill.
Step 3: Build the Jig Body
The jig body is fairly straight forward and easy to make. The goal is to end up with a U shape that has a sturdy length that serves as a backstop and two arms for attaching your dowel and flip stops (see next step). A set of runners holds the jig in place on the drill press.
Notes for the backstop:
-Make sure your back stop is square! Use a jointer and planer if it isn't.
-Make sure your back stop isn't too high - it may stop the drill from being able to fully lower. Mine was originally an inch or so too tall, so I ripped it on the table saw to cut it down to a better size.
Notes for the arms:
-I used a piece of scrap to test out several drill bits until I found one that made holes that fit my dowel snugly. Then I drilled two holes in each arm (this will allow for raising the dowel to a higher height to accommodate odd shaped cribbage boards.
-I attached the arms to the backstop with wood screws, pre-drilling the holes on the drill press to prevent splitting.
-Make sure they're square!
Notes on the runners:
-Two runners attached to the jig to fit in the grooves on the drill press will allow you to slide the jig back and forth. This is one area where I sort of free-styled it, and maybe could have found a better technique. I cut the runners to size and screwed them in one at a time (again, pre-drilling holes to prevent splitting) but had trouble getting the second one in the right place. I got frustrated trying to get the second runner in the exact right position and eventually just sanded off a few millimeters with a belt sander until it fit in the groove. The jig isn't a perfect fit in the base, but it's pretty good.
Step 4: Build the Flip Stops
The flip stops will eventually sit on the dowel in the jig and act as stop blocks to align your work piece. Each flip stop is 1/4" thick, and so by flipping one up and then re-aligning your work piece, you can advance your work piece an exact 1/4". Flipping two up and then shuffling your piece moves it 1/2", and so on.
Cut the stops
These stops were made from the two four-foot lengths of 1/4" poplar hobby board. I wanted enough to be able to cover the length of a 12" cribbage board, which means roughly 48 stops (four stops per inch X twelve inches). To cut them to size I set up a table saw with a cross-cut sled. I clamped a stop block to the sled so each cut of the hobby board would be two inches long (and thus, with my two 48" hobby boards I should get close to the 48 stops I wanted). See photo for the stop block set-up.
Drill holes in each
I then took the stops to the drill press to drill holes for the dowel to pass through. I used a drill bit that I had tested on scrap wood to fit the dowel with a little wiggle room so the stops could swing freely (not the same bit as used for the arms of the jig in the previous step - this was a size bigger). I clamped a piece of scrap to the press and penciled in the shape of a flip stop to get the hole in the position I wanted, identical for each stop. In a classic example of a novice wood worker not letting the tool do the work, I split the first three stops by drilling too fast. Once I slowed down my drilling and lowered the bit with steady, even pressure, I had no more splits and soon had a stack of flip stops with holes for my dowel.
Step 5: Assembling the Jig and Taking It for a Spin
From here it's pretty simple to finish the job - thread the flip stops onto the dowel and mount it on the jig. I didn't even use any glue since the dowel fit so snug in the jig, and this way I can raise the dowel if I ever need to accommodate a larger work piece. I laid out my holes in two rows, five holes (separated by 1/4", or one flip stop each) with a gap between each set of five holes (separated 1/2" or two flip stops), as well as a pair of holes at the start of the line for holding pegs before the game begins.
Definitely do a test run with a piece of scrap. Watch out for the following:
-Is your jig square? As you run the work piece along it, do your holes end up in a neat row?
-Is your work piece square? If it isn't, you'll have a tough time getting the holes lined up in a perfect row.
-Are there any problems with the jig itself and getting the actual drill past your jig so it can do some drilling?
-Do you like the spacing of the holes?
-Does your work piece slide nicely along the back stop? Mine got snagged on the tops of the runners, so I sanded them down a hair.
Step 6: Use Your Jig to Make Millions of Cribbage Boardsu
That should set you up to make some sweet cribbage boards. Please let me know if you have any questions in the comments, or improvements on my design! These cribbage boards are my second woodshop project, so I'm sure that there are aspects of my process that could have improved. In the mean time, it was good learning experience - worth it if you're starting out in woodworking and need a project. Jig assembly from start to finish probably took me 8 hours. Whoa.

Participated in the
Craft Contest
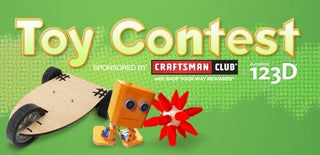
Participated in the
Toy Contest