Introduction: Cross Bladed Axe
The axe is one of the oldest tools known to man, and we still use it heavily today. One of the main uses for the axe is to split fire wood. A traditional axe typically splits wood only into two pieces at a single time. So here is a modification I did to a traditional axe in order to achieve multiple splits of wood in a single swing. I wasn't sure if I should call it a cross bladed axe or a crossed blade axe or somewhere in between.
Step 1: Tools and Materials
Gather your tools and materials:
Materials:
2 x axe heads
1 x Axe handle
Tools:
Angle grinder with cutting discs and flap discs (60, 80 & 120 grit)
Welder
Vice
Bench grinder with stones wheels (40 and 80 grit), buffing wheels and wire wheel.
Sandpaper, various grits 80 to 600 grit
Diamond file
Olive oil
Step 2: Cutting the Axe Head
Using the angle grinder and the cutting disc, cut one of the axe heads in half. I clamped it in the vice and used a really thin cutting disk 0.045". It took me 2 disks to complete the job. Make sure that you wear a particle mask because there tends to be a lot off nasty dust flying around. Of course wear all the other safety gear as well, and depending how you hold the angle grinder the sparks can be really hard on your clothes. Clean up the two pieces of the axe head with the wire wheel on the bench grinder.
Step 3: Grinding
Using the bench grinder with the stone wheels, grind the two side pieces so they are roughly the same shape. I cut a Dayton style axe head in half to create my two side blades so they were not very similar in shape. But the grinding goes quick using the 40 grit stone. Next, align the side blades on the side of the main blade with the cutting edges staggered back. Grind the bottom of the two side blades so they roughly follow the contours of the main axe. They don't have to be perfect because you are going to be filling it in with a heavy weld beads. Next taper the edges of the side blades in preparation for welding and clean up the main blade with the wire wheel.
Step 4: Welding
Align the side blades evenly and symmetrical onto the main blade. I used small welding magnets to hold it in place while I tacked it with the welder. Remove the welding magnets and 'go to town' with the welder. The metal is fairly thick so I used the hottest setting on my little welder and went slowly in order to try and get the maxim penetration that I could. After welding I begin cleaning up the surfaces and grinding down the weld. I also cut of the back corners of the side blades to help reduce the weight of the axe head, I also think it looks a little better.
Step 5: More Grinding
The majority of the grinding was done with the 60 grit flap disk on the angle grinder. This removes a lot of material quickly on the axe head. I found that when the edge of the flap disk began to round off, I could push it into the corner of the side blades and really begin to remove the weld into a smooth contoured shape. After the weld was ground down I went to the finer flap disks and smoothed the entire axe head.
Step 6: Sanding and Polishing
Next is the hand sanding process. I started with 80 grit and moved my way to 600 grit. I didn't use a sanding block and just used my bare hands. This process took me a couple hours, but it doesn't require much thought and you can invent other things in your mind as you sand:) Once I got down to 600 grit paper it was time to buff it using the bench grinder and buffer wheels. I have a 3/4 hp bench grinder and the little extra power really helps with the process. I have a selection of cutting and polishing compounds and worked my way through each of them. I was happy with the outcome of the polishing and the end result was an almost mirror like finish.
Step 7: Finishing
After the polishing, I sharpen all the blades on the axe head with a diamond file. I then mounted the axe head on a new hickory handle and used olive oil to treat the wood of the handle. I have never used olive oil on an axe handle before but it seemed to work out pretty good.
Step 8: Test Run
The final step was to actually try out the axe. I had a bunch of fir rounds left over from the winter and the rounds were between 7 and 12 inches in diameter. The wood was dead standing as of last year so the wood was fairly dry, but the majority of the rounds still had the bark on. The axe did really well on the smaller rounds when the bark was off or partially off, but struggled on the larger ones when the bark was fully intact....but maybe it was me that was struggling and perhaps a stronger man could have split the bigger ones as well. Either way, let me tell you that it is an awesome feeling when you do split an entire round into 4 pieces with a single swing. I also think that this design would be great with a smaller axe or hatchet for making kindling. Here is a clip of me splitting a full round:
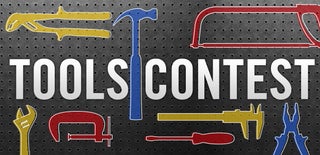
Third Prize in the
Tools Contest