Introduction: Custom Fitted 3D Print Glasses
This is Instructable will explain how to make fitted 3d printed eyeglasses. I’ve always had trouble finding glasses that fit, so I decided to make them myself. If you want to make something you can wear everyday, please follow along.
Note:
I’m not a 3D printing expert (I’m a student in the healthcare field). The whole process was self taught and uses less than 10 tools.
Step 1: Gather Your Tools
Tools:
- Ruler
- Computer
- 3d modeling software. I will be using Rhinoceros on the Mac. If you own a Mac you’re in luck. Rhino for Mac is an ongoing development project so it’s free!
- Illustrator (optional)
- Plastic frames for the hinges. I bought these at $5 and below for $3.25.
- Soldering iron to remove the hinges
- Epoxy to glue the hinges
- Flexible wire to measure the temple and nose bridge.
Step 2: Start Measuring!
Measure your face to set up boundaries. The lens should not go beyond the red box.
- Highest point: Top of eyebrows
- Lowest point: When the glasses hits your cheeks
- Towards the nose: When it touches your nose (duh)
- Towards temple: Midway through your temple
Step 3: Sketch It on Illustrator (optional But Easier)
Get a pair of frames you like and use that as your template
Open up Illustrator.
Draw your boundaries.
Draw the shape you like.
Save it as .AI and get ready to import it to your 3D software.
Step 4: Making the Frame
Open up your 3D software import your .AI file
Use the curve tool to start tracing over it. This will be your 2D frame.
To make it 3D, draw a cross section of the frame (the blocky looking Pac-Man). The dimensions I made are in the picture.
I used a rail sweep to make the frames 3D.
Step 5: Building the Nose Bridge
Making the temple requires 3 tools:
- Curve Tool
- Extrude Curve
- Extrude Surface
Draw a curve on the Front Plane.
Use the Extrude Curve (ExtrudeCrv) to make the curve a 2D curved sheet.
Use the Extrude Surface (ExtrudeSrf) to make the curved sheet 3D by adding depth.
The temple can be bent into many different shapes such as a keyhole style. This instructable is just to get the job done
Step 6: Build the Side and Hinge Holes
Use the Line Tool to build the sides of the frame.
Extrude the surface (ExtrudeSrf) to make the frames 3D.
Next is to cut a hole in the frame to place your metal hinges:
Draw a cuboid. Depending on the hinge, the dimensions of the cuboid will be different. If you bought similar metal hinges like myself, then follow the dimensions in the image.
Place the cuboid in the frame.
Use a Boolean split to make the a hole in the frame.
We will eventually put the hinges in the hole and epoxy it.
Next is the nose piece.
Step 7: Shape and Build the Nosepiece
Use the flexible wire to make the nose shape (this will be the angle you're trying to draw)
Use the curve tool to draw out the nose piece.
Offset surface (OffsetSrf) to make it 3D.
Rotate the nosepiece to fit your nose shape/angle.
You're frames are done!
Let's make the temple.
Step 8: Sculpt the Temple.
Get the flexible wire and curve it around your ear.
There should be two bends
1. Around the ear
2. Around the head
Step 9: Build the Temple
Now it's time to draw it on the computer.
Here are my measurements but everyone is different.
I extruded my frame by 3mm
I offset my frame by 6mm
Fillet edge to make the edges smoother. (If it's too complicated, you can always sand it down)
Step 10: Curve the Temple Around the Head
Draw the curve (purple) that should mimic the curve of your head.
Extrude the curve into a 2d plane
Draw another plane cutting through the temple.
'Flow along Surface' to make the temple curve along the purple plane
Step 11: Cut Out the Temple Area.
Draw a box to cut out a hole in the temple. The dimensions are listed.
The hole should be place about 1.5 mm from the bottom.
The hinges should fit in the slot.
Step 12: Assembly (Easy)
Remove the hinges from an old pair of glasses. I bought some plastic sunglasses for $3.
To remove it, use a Soldering iron: http://blogs.terrorware.com/geoff/2013/05/27/repla...
Just epoxy the hinges on!
Step 13: My Prototypes
These are my prototypes. I'm currently wearing the bottom one.
Step 14: Done.
Wear it.
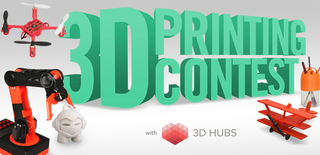
Runner Up in the
3D Printing Contest